What Do You Know About Die Casting?
· Definition:
As per die casting definition, it is an advanced metal casting process in which molten metal is transformed into precise shapes. Die casting molds are used to shape the molten metal as per the specified requirements. Due to this high-pressure casting method, parts of high-quality finishing and dimensionally accurate precision are obtained. Non-ferrous metals like magnesium, aluminum, copper, tin, zinc, lead, and pewter are usually used to make different types of die-casting components.
· Significance:
Die casting is all about manufacturing efficient, economical, precise, and strong metal molds and components. There are numerous industries like automobile, medical, and even aerospace which use die casting products. It aids in mass production of high-precision components while providing consistent results and very low-level material wastage. The manufacturing speed, high tolerances, and seamless finishes are some of the key factors which add up great value to its significance.
What is the Die Casting Process?
There are several stages involved in the die casting process. Some of the most important die casting methods are as follows.
· Metal Melting:
In this first step, the molten metal alloy is developed by melting down a chosen metal like aluminum, zinc, or magnesium. In order to get optimal casting, the alloy is brought to the exact temperature which is required as per the design requirements.
· Filling:
After the metal melting process, filling is performed. It is a process in which molten metal is injected or filled within the mold cavity. The filling method is applied at high pressure to ensure that metal flows flawlessly and every detail of the mold has been filled up completely.
· Solidification:
Lastly, the metal that was poured into the mold is set to be cooled. So that when it is solidified, it takes on the exact shape of the mold cavity. It is considered to be an important step because the speed of solidification largely impacts upon final properties of the mold.
What are Different Types of Die Casting?
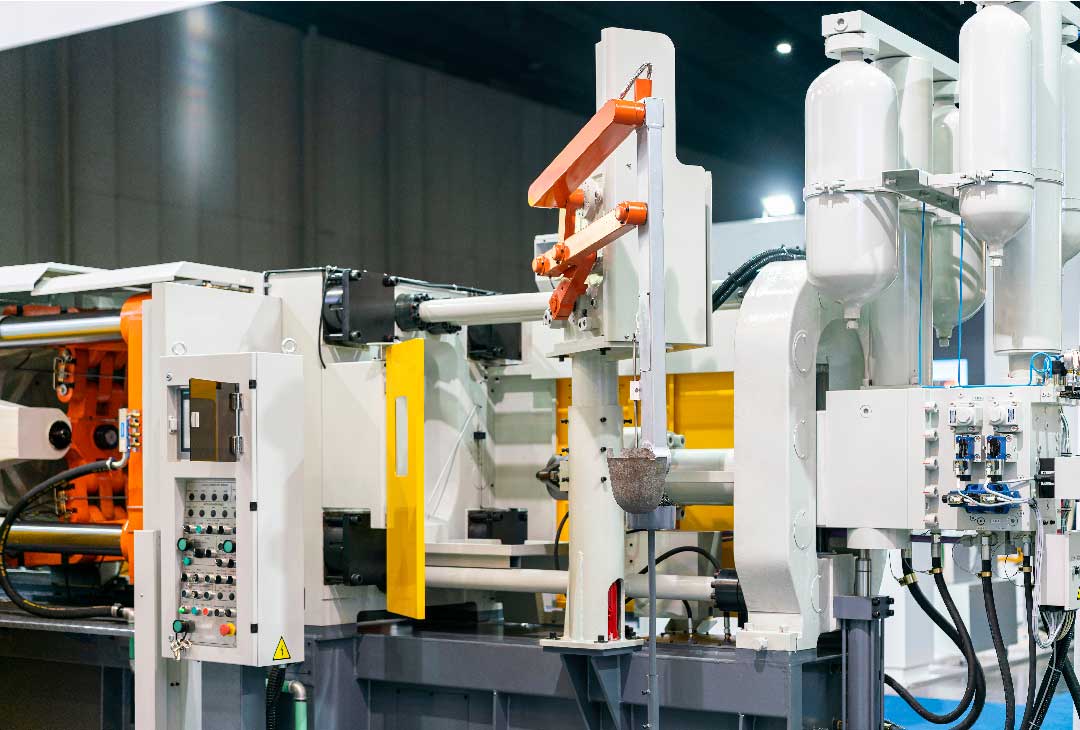
Gravity die casting relies on gravity when filling the mold with molten metal. As the metal cools and solidifies, it assumes the desired shape. This type of die casting produces stronger parts with fewer imperfections due to its reliance on gravity. It is typically used where excellent accuracy, higher density, and greater strength in molds are required. It’s best suited for medium to large-sized parts.
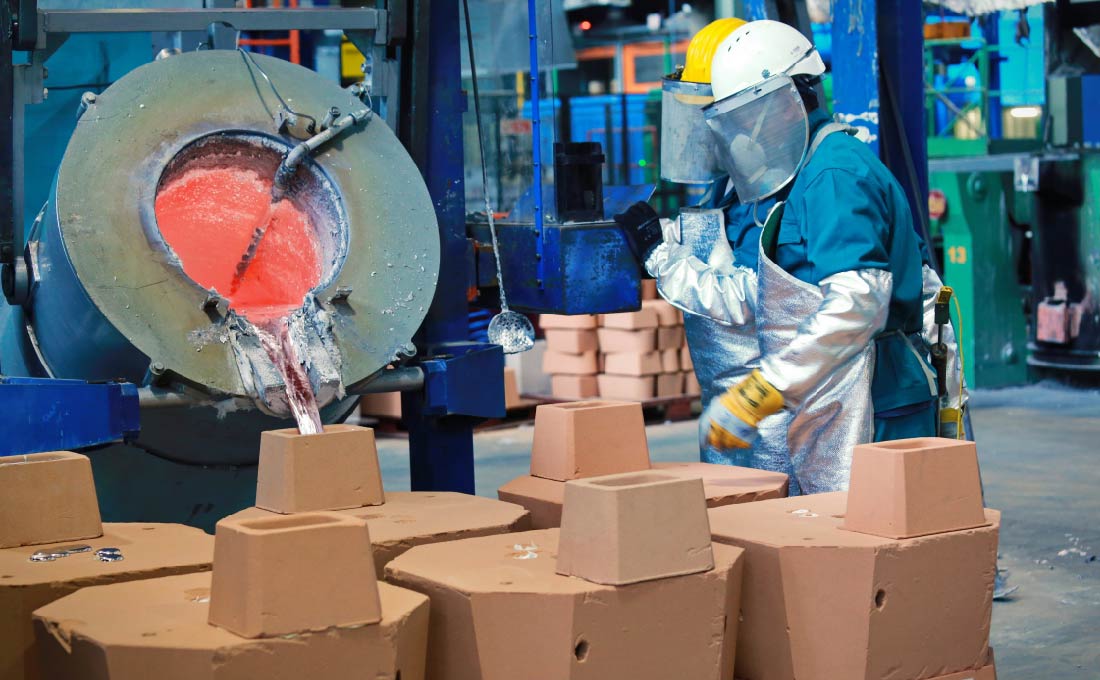
Mold is developed through sand and binder in this method. It is ensured that all the parts of the mold is filled with substances of sand and binder properly. Sand casting method is mostly suitable for comparatively large and complex components.
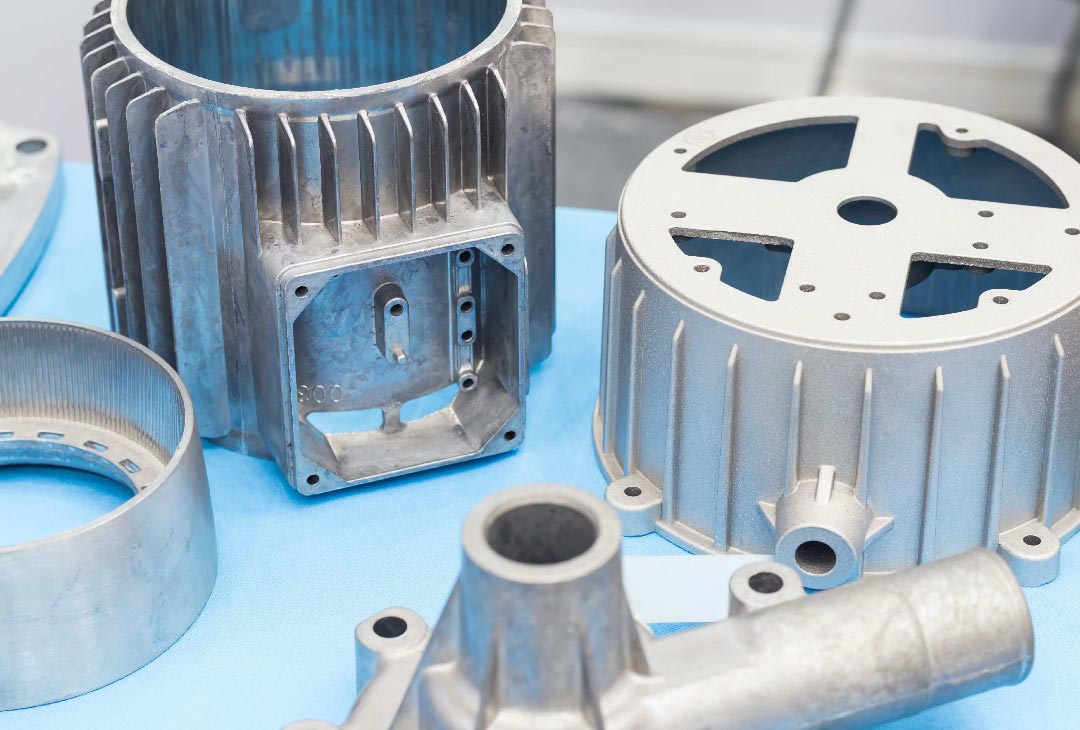
As the name suggests, an amount of medium pressure is applied over the molten metal while pouring it into the mold. It offers a good balance between speed and precision. It is suitable for most of the industries ranging from automotive engines up to complex electronics. Another important feature of medium pressure die casting is reduced porosity.
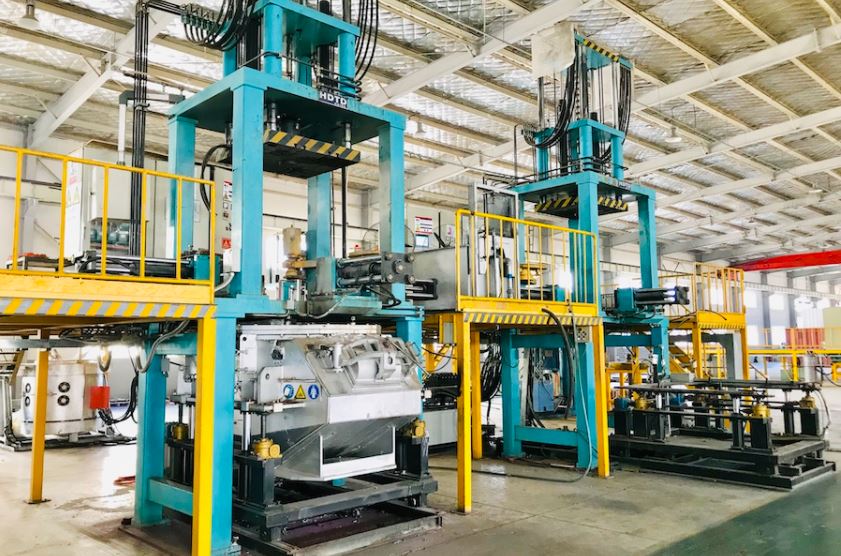
It is a method renowned for its compatibility in developing large and structurally well shaped components. Lower injection pressures are applied over the metal or alloy during the die casting process. Manufacturing critical parts is supported through low pressure die casting like automotive engine blocks and even aircraft components.
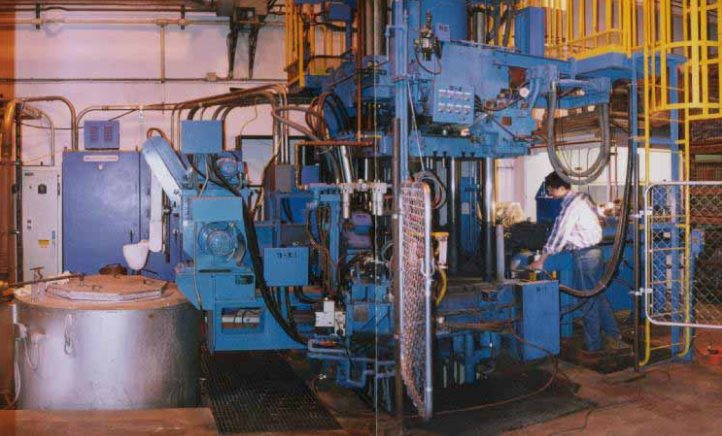
Squeeze casting provides exceptional mechanical properties. In this method, intense pressure is applied during the process even after solidification. Ultimately, it enhances material density and also minimizes porosity. Superior strength, wear resistance and dimensional precision are some of the notable features of Squeeze casting.
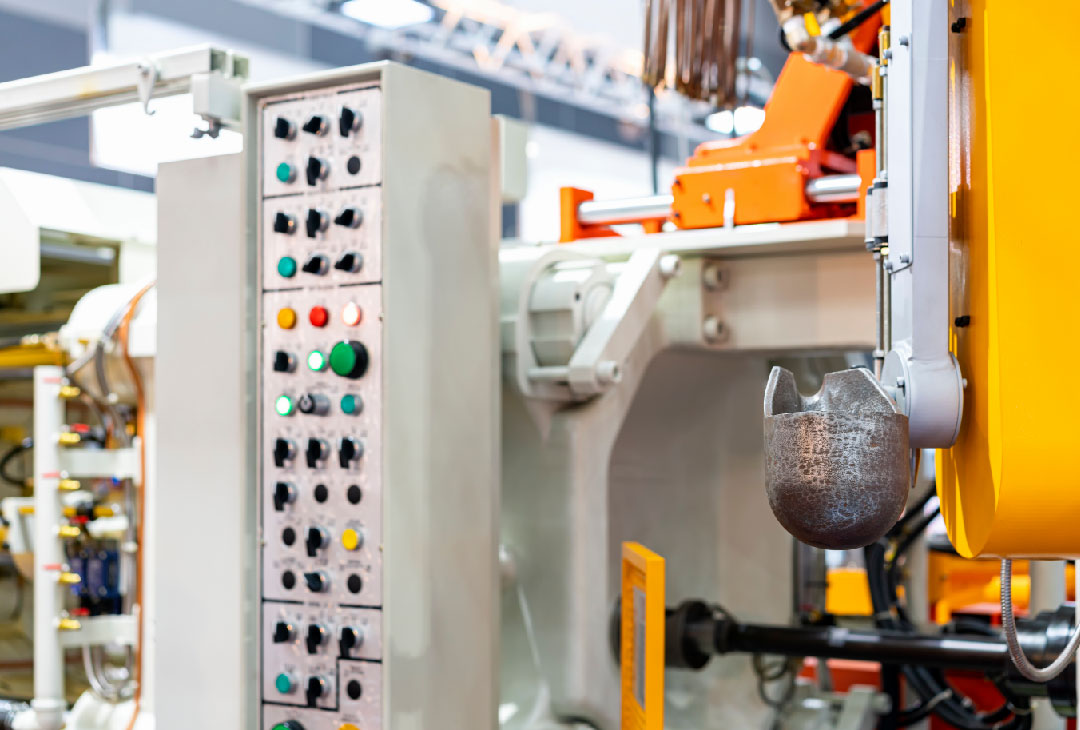
High pressure die casting involves applying immensely high amount of pressure throughout the die casting process. It provides rapid filling and considerable solidification. Components where tight tolerances and outstanding surface finishing is required like in aerospace industry or electronics use high pressure die casting.
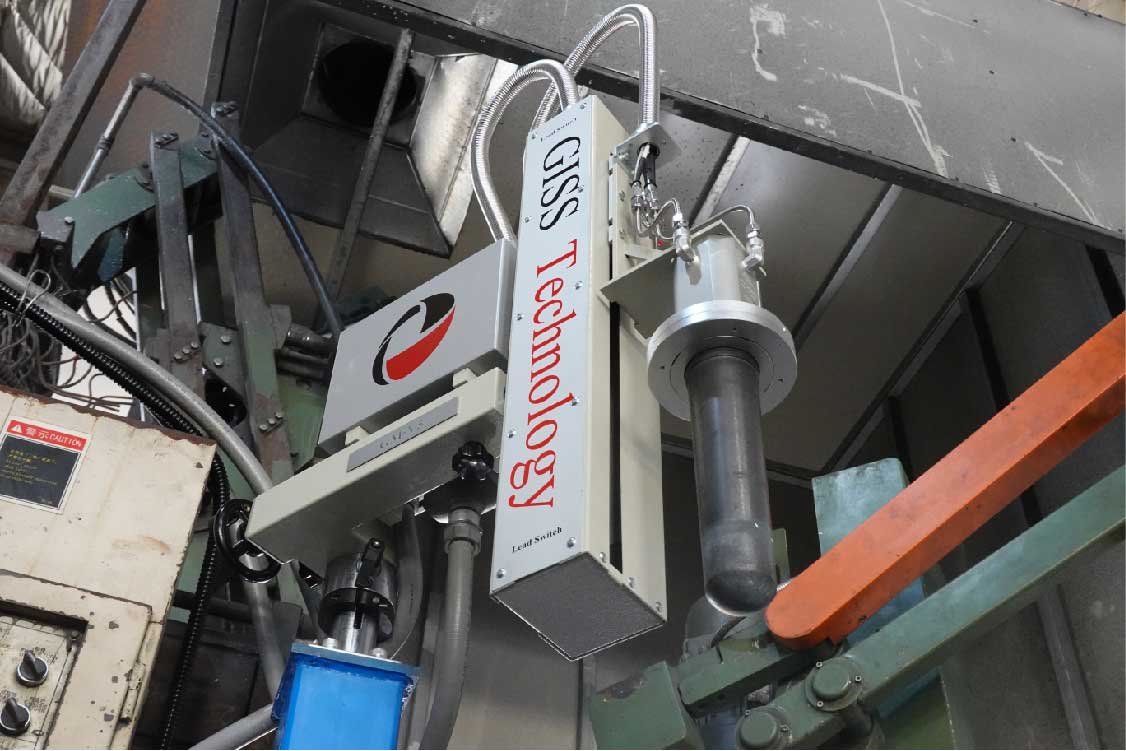
Partially solidified metal is used to manufacture components throughout the die casting process. In this way, the mechanical properties are enhanced whereas the porosity of the components is decreased. Automotive engine components as well as other intricate industrial parts are manufactured through semi solid die casting.
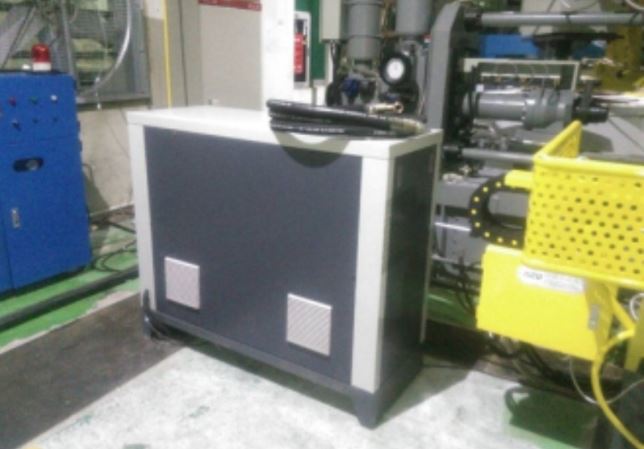
In this advanced method, any type of air and gases are removed from the mold cavity. In return, it provides minimal defects during manufacturing and ultimate surface quality. Medical equipment is usually developed through vacuum die casting.