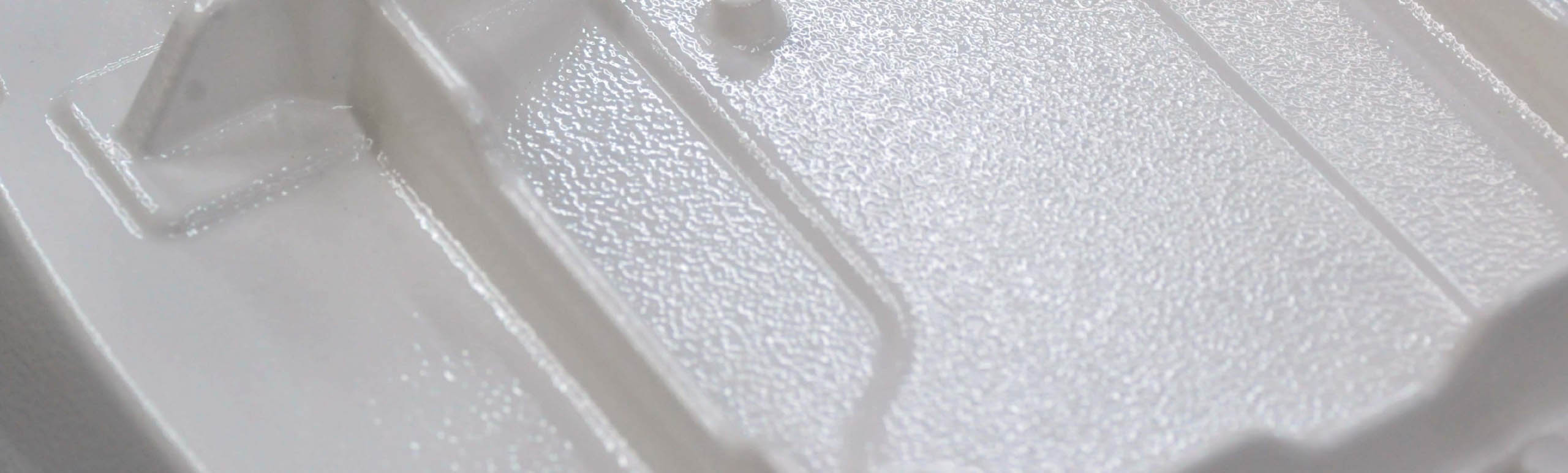
Your Complete Solution To Aluminum Die Casting in China
At Sunrise, you get top-notch solutions all in one place.
After completing all aspects of die casting and machining, we provide support services for the perfect surface finish. We don’t leave your side until the job is done.
We provide technical as well as advisory support in choosing the right surface treatment, along with the right quality control protocols. From functional and protective grade to commercial and decorative coatings, you will be fully equipped to customize your project to perfection.
1000+ Die Casting Parts Surface Treatment Experience From 500+ Global Clients
How Sunrise Aluminum Surface Finishing Capability Ensures Project Success
We have Cleaning, Shot Blasting service in-house, and also specialized partners that allow us to offer various surface treatments in the form of Liquid Painting, Powder Coating, Chromate Conversion Coating, Anodize, Electroless Nickel, Silk Screening, Pad Screening, Laser carving, etc.
We do strict inspections from raw material to finished parts. With our high-level test lab, to meet your requirements
All surface finishing die casting parts we provide are compliant with ROHS & REACH.
Your Wonderful Die Casting coated Parts Coming From Sunrise Rich Capability Manufacturing Equipment
Recent Aluminum Die Casting Coating Projects
Sunrise Metal develops complete solutions for aluminum die casting with surface finishings and manufacturing for 10+ years. For now, the projects we are completing with our customers are as follow:
- Experienced Team
- Advanced Equipment
- Global Clients
- Premium Quality
- Fast Delivery
Sunrise Metal has excellent teams, including experienced engineers, professional customer service persons, strict quality controllers and skilled production workers. They implement best practices in surface finishing and make sure all customers are satisfied.
No. | Name | Stroke | Q’ty |
1 | Mazak 7-axis turning&milling Machine | Ø658*1011MM | 1 |
2 | Mazak /Hass 5axis CNC machine | Ø850/Ø600 | 4 |
3 | 3-axis CNC machine center | 2000*1500MM | 1 |
4 | 4-axis CNC machine center | Ø250*800MM | 8 |
5 | 3-axis CNC machine center | 1000*600*600MM | 20 |
6 | CNC Lathes | Ø320*800/Ø610*1000MM | 2 |
7 | Sodick Wire cutting Machine | 400*400*200MM | 3 |
8 | EDM machine | 500*400*400MM | 2 |
9 | Surface grinder | 600*300*200MM | 1 |
No. | Name | Brand | Q’ty |
1 | CMM | Carl Zessis | 1 |
2 | CMM | SanYou | 1 |
3 | Spectrometer | China | 1 |
4 | Microscope | China | 1 |
5 | Projector | China | 2 |
6 | X-ray Detector | SANDT | 1 |
7 | Cleanliness Test Equipment | China | 1 |
8 | Leakage Test Equipment | China | 2 |
9 | Salt Spray Testing Equipment | China | 1 |
10 | Pneumatic Measuring Instrument | China | 2 |
11 | Hardness Testing Machine | China | 1 |
12 | Color Meter Machine | China | 1 |
13 | Thickness Testing Machine | China | 1 |
14 | Electronic Balance | China | 1 |
15 | Density Balance | China | 1 |
Get A Free Consultation
Receive advice directly from engineering consultants for your Aluminum Die Casting coating parts. Our suggestions and solutions are based on your CAD and Step drawings.
SURFACE FINISHING- THE ULTIMATE FAQ GUIDE
There are metal products surrounding us everywhere. Some are shiny while others are matte. Almost every metallic surface carries a different kind of look and feel. For example, steel is shiny and aesthetically pleasing while aluminum is often sturdy and less shiny. The finished look is dependent on the surface finish.
- What is surface finishing?
- Why is surface finish important in Engineering Applications?
- What are the factors that affect surface finish?
- What should you consider before surface finishing your product?
- What are some of the common surface finishing processes?
- How does surface finishing work?
- What is Chromate-Surtec 650?
- What is Anodization?
- What is the difference between nickel plating and electroless nickel plating?
- What are the different plating services available?
- What are the advantages and applications of Screen Printing and Pad Screening?
- What is the difference between laser carving, etching and engraving?
- What is the difference between shot blasting and sandblasting?
- How does powder coating compare to Liquid Painting?
- What is the relative surface finish roughness of various manufacturing processes?
- What is surface preparation in relation to cleaning metal for surface finishing?
- What is surface finish measurement?
- What are the most common forms of metal finishing?
- How do companies measure and inspect surface finish?
- What surface treatments is Sunrise Metal capable of?
- What are some of the tools that Sunrise Metal uses to test for surface finish quality?
- How does Sunrise Metal assure customers of quality assurance?
What is surface finishing?
Surface finish refers to the process of changing the surface of a material to improve its attractiveness. How the product looks when finished depends on the surface finishing method applied.
In other words, surface finish is the overall texture of a surface defined largely by its waviness, lay, and surface roughness. You will come across these terms in this article. To avoid confusion, surface roughness and surface finish are not synonymous. Here is a diagram to illustrate the three often-confused terms.
Lay is the direction of the pattern on the surface and is typically determined by the method of production used to process the product.
Rough surfaces wear more quickly and have higher friction. These are not desirable aspects. The difference in smoothness between the desired product and the actual surface is surface roughness.
A surface could be warped or have certain unwanted features that exceed mere roughness. Waviness refers to the bigger irregularities and more widely spaced components than just roughness.
Why is surface finish important in Engineering Applications?
The most notable factor is the attractiveness, as the product instantly looks better after the surface finish. This will affect the longevity of the product, which is great for the end-user.
Another big advantage of surface finish is that if one brushes a surface before painting it increases its adhesion that is important if one is to get a quality finish.
There are many advantages of surface finishing but here are the most notable ones:
- Better chemical resistance
- Better resistance to corrosion
- Removal of surface defects
- Aids in the adhesion of paint and similar coatings
- Durability and minimized friction
- Improved conductivity and increased surface electrical conduction
- Enhanced look and feel
What are the factors that affect surface finish?
There are many factors that would influence what type of surface finish and the outcome. The biggest challenge is the manufacturing process, which largely determines the type of surface finishing. For processes that require machining like milling, drilling and turning, factors like the cutting tool, feeds, machine tool condition, speeds, tool-path parameters, cut width, cut depth, tool deflection and vibration are factors that affect surface finish.
Liaise with your surface finish provider before settling on a particular type to get expert advice on the most suitable way to finish your product.
What should you consider before surface finishing your product?
By now we have established that how a part feels, looks and functions is largely dependent on surface finish. While this is not something that you will do personally, you might benefit from the knowledge on what is the best surface finish, what environment is it best suited for, and who will use it. These questions are ideal if you need to know how to choose the right surface finish from the start.
What is your product’s primary role?
We have to look at various products to understand what exactly this means. Let us take the example of a radio. It needs a surface that is firm and durable. A portable radio would benefit from a rubberized surface as it will not fall off and will have a firm grip on tabletops. Knowing what your product’s main use makes it easy to settle on the surface finish best suitable for various environments. Also, consider the raw material used so that the surface finish does not alter the functionality of the product.
Who is the Product For?
If a product will be used in the traffic, then it may benefit from bright deflecting colors. The surface finish on children’s toys is often bright and beautiful to attract children but also has to be nontoxic. Depending on what you think your customer may like, you may use these factors to decide the type of surface finish.
Do you care for durability?
Durability and stability come with a price. The raw material used and type of surface finish must be of superior quality for a product to last long. Surface finish types like painting and anodizing offer the least surface protection followed by powder coating then chrome plating. Ask your service provider what options are available to you for more durability. Choosing a durable finish will not only add value to the finished product but will also increase the manufacturing costs. Weigh what your options are and find the perfect balance for profitability.
Do you want to evoke an emotional response?
The way a product looks and feels can create a perception about it. Gold plating suggests high class and elegance while purple denotes royalty. A good watch would probably cost more if it was gold or silver-plated. For fun projects or children’s items, the objects often have bright colors for outdoor use and socialization. If you have a product that would be improved aesthetically by surface finish, definitely consider it.
What are some of the common surface finishing processes?
There are plenty of surface finishing options available in the market today. Such an exhaustive list cannot be mentioned here so we will discuss the most popular ones that you might have chanced upon;
Plating– a popular surface finishing process, plating is a covering in which a metal is poured onto a conductive surface.
Sanding – This process involves using a type of coated abrasive applied on sheets of paper or cloth to remove surface materials.
Passivation – This non-electrolytic surface finishing process makes the steel resistant to rust by eliminating the free iron on the surface. The process usually uses citric or nitric acid to do this. This results in a layer of inert oxide that does not react with air or cause corrosion.
Polishing – The process smoothens the surface of a work-piece using an abrasive. It utilizes an abrasive glued onto the work wheel. It may seem similar to sanding but not sanding.
Buffing – Quite similar to polishing, buffing utilizes a finer abrasive applied on the work wheel for better results.
Electro-polishing – This is a chemical process applied to stainless steel for better and smoother surfaces.
Sandblasting – The process uses abrasive beads rubbed onto the surface to remove any materials on the surface.
Electroplating – This process utilizes electricity to coat metal surfaces with a layer of thin and bonded layers of another metal.
Anodizing – This coating process adds a layer of iron oxide on a metallic surface to improve its mechanical properties.
Painting – This is one of the lightest applications and can instantly improve the look or feel of a surface.
E-coating – In this process, the work-piece is dipped into a tank that has material to coat.
How does surface finishing work?
Most of the processes enhance the appearance or the properties of the work-piece. However, each process does this through its own unique way. Various surface finishing options can be grouped into 4 broad categories.
·Addition of material
There are additive surface finishing processes that add an extra layer of material to a surface to make it sturdier, more attractive, and more functional. Such processes include powder coating, plasma spraying, galvanizing, and anodizing.
·Altering the material
The chemical and material properties of the product’s surface can be enhanced by mechanical and chemical ways. Such altering processes include pickling, carbonization, and flame polishing.
·Removal of material
This process utilizes abrasive tools or chemicals among other processes to remove unwanted material from the surface of an item. Such processes involve grinding, sanding, polishing, barreling, and etching.
·Reshaping
The surface of the work-piece is deformed to alter its shape. Typically, this is accomplished with the use of mechanical pressure. Great examples of reshaping surface finishing options include peening, burnishing, and knurling.
What is Chromate-Surtec 650?
Chromate-Surtec 650 or simply SurTec 650 is free of chromium (VI) for the passivation of aluminum. The liquid offers great corrosion resistance and is heat resistant without compromising on corrosion-resistance. It is perfect for use with the aerospace industry and the electronics industry.
What is Anodization?
Anodization is a process that uses anodic oxide to coat materials for durable, decorative and corrosion-resistant products. The best metallic material for this is aluminum although other metals like titanium and magnesium are also often anodized.
Anodic oxide further provides better adhesion for glues and paint primers than plain metal. The oxide layer formed on the surface can measure 5 to 30µm in thickness.
What is the difference between nickel plating and electroless nickel plating?
Nickel plating is a process that is often used for engineering, decorative and electroforming purposes. Usually, the base metals used are copper, steel, alloys and zinc alloys. When using copper and steel substrates, the process is done directly on the plate but zinc demands underplating with copper.
Magnesium, aluminum, and stainless steel will also require special treatment before planting. You can expect smooth and matt finishes with engineering nickel plating while the decorative nickel coatings are smooth, lustrous, and bright. The bright coatings can get an additional chromium coating thinly plated to prevent tarnishing. The process can be done on engineering nickel plating for better wear resistance and sturdiness.
Electroless nickel plating is a process that uses external current sources with galvanic electroplating techniques. The process is also known as auto-catalytic or chemical nickel plating. It uses chemical nickel plating baths to create coatings that are corrosion-resistant, wear resistant and boast low friction. Mostly, electroless nickel plating is used on plate kitchen, doorknobs, and bathroom fixtures.
What are the different plating services available?
Plating is a surface finishing process that covers a surface with metal using a conductive surface. This one of the oldest surface finishing methods and has been practiced for hundreds of years. Plating is mainly done for decoration, corrosion resistance, hardening, enhancing wearability, improving paint adhesion, and altering conductivity.
Most jewelry makers utilize this method to add a thin film of silver or gold finish on items. There are plenty of plating techniques in the market today including vapor deposition under vacuum, thin film deposition, electroplating, and sputter deposition.
Here is a list of plating services available;
- Gold plating
- Silver plating
- Zinc plating
- Zinc-nickel plating
- Tin plating
- Composite plating
- Cadmium plating
- Nickel plating
- Alloy plating
- Copper plating
- Rhodium plating
- Chrome plating
- Electroless nickel plating
What are the advantages and applications of Screen Printing and Pad Screening?
You must have come across a branded promotional item. These items are created using either pad screening or screen printing. While it is better to leave it up to the experts, it is good to know how the two processes compare.
Pad Printing
As the name suggests, this process involves the use of silicone pads to transfer ink onto the item you want to print. Pretty much like stamps but a little bit more complicated than that. To put it simply, the pad printing machine will hold the pad and product upright and then press ink into an ink plate which has been designed to the shape of your desired artwork or logo. This pad is pressed on the item and left to dry. Pad printing is more modern compared to screen printing.
Advantages of pad printing include;
- Easy to print 3D objects and uneven surfaces regardless of their shape or size.
- Ideal for delicate items
- If running in-house, pad printing equipment takes limited space and set up costs are low. The process is also easy to learn.
Screen printing
Screen printing differs from pad screening in that this process requires an ink-blocking stencil applied onto a woven mesh. The stencil will them form in the mapped area and ink is transferred onto the work-piece. Today, this is the most widely used method for printing t-shirts and other apparel. The old method dates back to 960 to 1279 AD.
It is perfect for quick printing of t-shirts and similar promotional items butt cannot work for sensitive items. Also, it is expensive to set up and ideal for large productions. While it is great, screen printing iss fairly time consuming and can get quite expensive if you need multiple colors.
What is the difference between laser carving, etching and engraving?
The three laser services offer a permanent marking solution for great labeling and making parts more distinct. While they are quite similar, a few differences set them apart. These differences majorly have to do with what each process does to a surface and how deep the laser goes to alter the outcome. Laser marking just adds color to the surface while etching and engraving actually removes a portion of the surface as it creates the desired mark.
The process is quite similar in all. The laser machine has three major parts; the surface, the controller, and the laser. The laser is the drawing tool that emits a beam allowing the controller to trace the desired logo or artwork onto a surface.
Laser marking is a permanent marking process that utilizes a beam of laser to create a lasting impression on a surface.
Laser engraving is a process where the laser beam actually removes bits from the surface as it is creating the mark to expose a cavity that shows the desired artwork at eye level.
Laser etching is a subset of laser engraving but uses heat from a beam to make the surface of the material melt revealing the desired artwork.
What is the difference between shot blasting and sandblasting?
Shot and sandblasting are two often confused processes and both belong to a form of surface finishing known as Abrasive Blasting. Abrasive blasting is a process that propels a stream of abrasive material onto a surface under very high pressure to smoothen it. It can also be used to shape the surface or remove unwanted material. The two applications are widely used in various industries like blasting floors, walls, and drums.
In both the equipment is the same. The difference is in the materials used to blast. Sandblasting uses silica sand as the media while shot blasting uses metallic shots made from copper, steel, aluminum, or other sturdy metals.
How does powder coating compare to Liquid Painting?
Powder coating is a type of coating used n surfaces as a free-flowing dry powder. Unlike conventional paints, it does not require a solvent to keep the filler parts and binders in liquid suspension form. Wet paint or liquid painting is the traditional process of applying paint on a product. Most of the modern painting techniques are technologized now. An example is sheet metal fabrication shops that use a spray, pressurized vessel, or pump to deliver the wet paint evenly on the surface.
Advantages of powder coating;
- Emit no volatile organic compounds
- Coating over-sprays can be recycled
- Produce thicker coatings than liquid paint with no sagging or running
Advantages of wet paint;
- Can coat items that cannot be heated
- Offers a wide range of colors
- Can provide a thin finish
- More affordable
What is the relative surface finish roughness of various manufacturing processes?
Surface finishes vary largely by what manufacturing process was used to achieve them. A sandblasted surface would vary greatly from a powder-coated one. Choosing a process that works well for your surface is an essential part in making an appealing product, Sometimes process can be overlaid for the best possible end product. Look at the table below to see how various processes compare.
What is surface preparation in relation to cleaning metal for surface finishing?
The first step in surface finishing is prepping the surface to adhere to the preferred method of surface finish. It is essential in preventing corrosion and improve wear resistance in most metals. One good example is how steel is cleaned before surface finishing through abrasive blast cleaning. Surface contaminants on such a surface like oil and grease must be wiped first. Then the steel is blasted for a smooth, shiny surface. There are various cleaning methods available including abrasive sand blasting, hand cleaning, power tool cleaning, and flame cleaning.
What is surface finish measurement?
Surface finish measurement is also referred to as surface texture measurement. This is the measure used to define the quality of a surface from the desired expectations. Mostly this is done by measuring the variations in local height over a distance.
Earlier we mentioned surface roughness and waviness. These terms will be important for you to understand surface finish measurement.
What are the most common forms of metal finishing?
Metal finishing is used to finish the surfaces of metallic products by applying a thin layer to the surface. Most of the processes are additive in nature. There are many metal finishing options that cannot all name here. There general benefits of metal surface finishing include;
- Enhanced durability
- Increased electrical resistance
- Decoration
- Better electrical conductivity
- Better corrosion resistance
Types of Metal Finishing;
Metal Plating – metal plating is the process of depositing a surface covering onto metal using a conductive surface.
Brushed Metal – this is a dull metal finish with a unidirectional satin finish. It is accomplished by polishing the metal with a wheel or belt and softening with a nonwoven abrasive belt. Some of the common brushed metals include nickel, aluminum, and stainless steel.
Buff Polishing – this is a smoother way of finishing metals like stainless steel. It is similar to polishing but finer.
Metal Grinding – This is an abrasive method of finishing metal that uses a grinder.
Sand Blasting – The process uses abrasive beads rubbed onto the surface to remove any materials on the surface.
Powder Coating – Powder coating is a type of coating used n surfaces as a free-flowing dry powder. Unlike conventional paints, it does not require a solvent to keep the filler parts and binders in liquid suspension form.
Hot Blackening – This is the conversion coating used on ferrous materials, copper, stainless steel, zinc and silver solder. It improves appearance, minimizes light reflection and adds corrosion resistance.
How do companies measure and inspect surface finish?
There are two major ways of measuring surface finish. The oldest one is using a stylus profiler, which has been in use for over 100 years. You can also use optical profilers from Sunrise Metal.
Stylus Profilers are contact tools that are dragged on a surface using only the tip. The tool then measures how high or low it is raised from the ideal surface and this is recorded.
Non-contact profilers are tools like the coherence scanning interferometry measure using capacitors like proximity sensors. There are reasons why non-contact surface finish measurements may be preferred;
- If the material is delicate
- If more than one direction is preferred and material lay is a factor
- If it a consumable
What surface treatments is Sunrise Metal capable of?
After a product is manufactured and all the aspects off machining and casting are complete, Sunrise Metal can apply protective, functional, and aesthetic coatings. We are capable of meeting various surface treatment requirements like tumbling, bead blasting, and in-house cleaning.
Some of the surface finish processes we complete include chromating, wet painting, powder coating, anodizing among others.
What are some of the tools that Sunrise Metal uses to test for surface finish quality?
There are many tools at Sunrise Metal’s to die for surface finish quality. Your product will benefit from a worthy assessment from the team. Some of the tools in our stations include salt spray testing, thickness testing and color testing.
How does Sunrise Metal assure customers of quality assurance?
Sunrise metal is ISO 9001 &ISO 13485 & IATF 16949 certified. This means that the quality is assured by the highest standards possible. We are also ROHS and REACH compliant.