Sunrise Marine Aluminum Casting Components
As industry leaders, we cater to orders of all types. We accommodate variable order volumes, from low, medium to high requirements. Our commitment to quality sets us apart from competitors, as we provide dependable solutions of aluminum die casting parts.
Our skilled teams are capable of tending to marine casting products that require unique solutions relevant to their industry. We make sure all solutions suit customer demands while still maintaining standards of efficiency and compliance.
At Sunrise, we promise to deliver a one-stop, fast production solution to your business needs. From designing and assembling to surface treatment and delivery, our modern control facilities are capable of doing it all.
Come forward to benefit from our rich experience and knowledge, as we design mechanical parts with features like none other.
Sunrise Marine Aluminum Die Casted Manufacturing Capability
With rich engineering experience and a skillful team of experts, we’re able to manufacture and transport quality products for clients across the globe. Cost-effective aluminum die casting parts have the ability to perform under the most demanding conditions. Such durable components are made possible with advanced production equipment and technology available in our manufacturing facilities. Under the supervision of our hand-picked experts, we are able to offer a high-value range of marine die casting products.

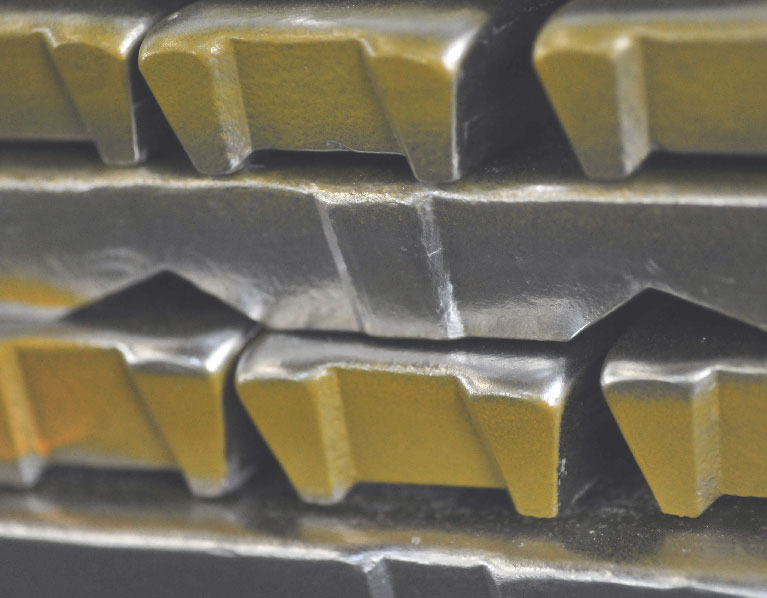
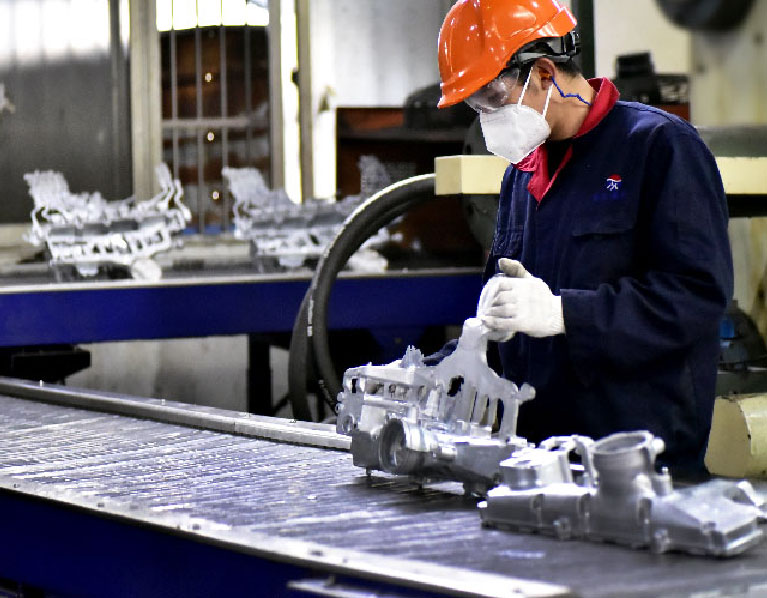
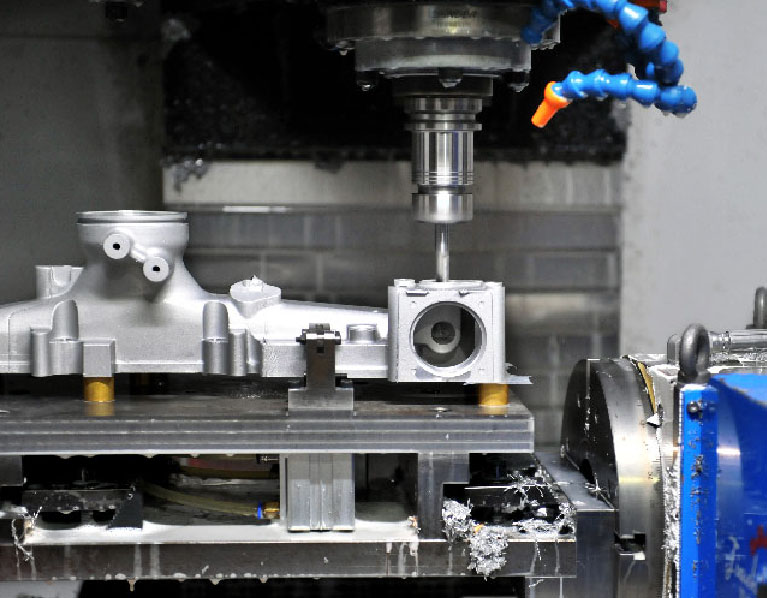
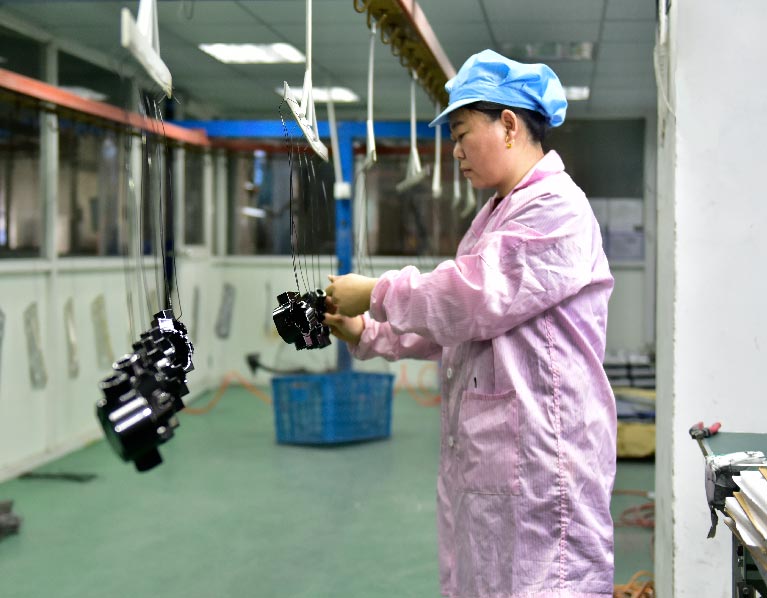
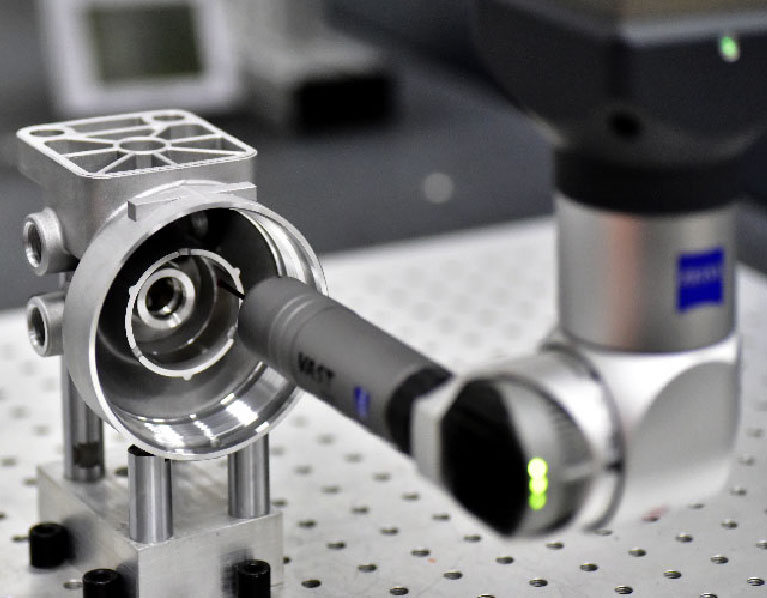
Advanced Equipments For Marine Die Casting
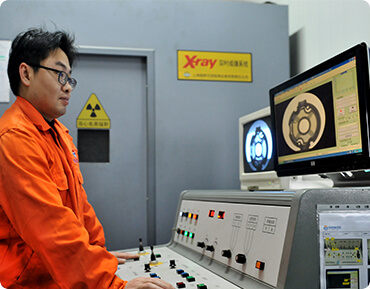
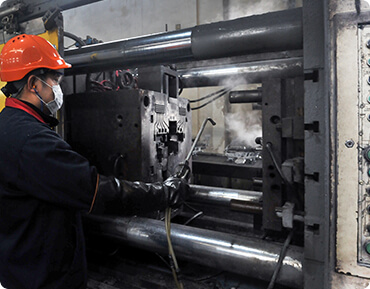
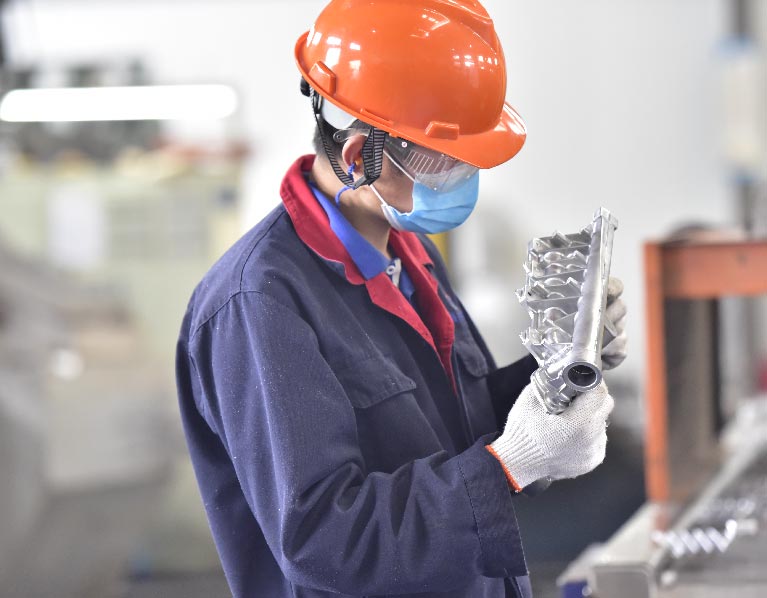
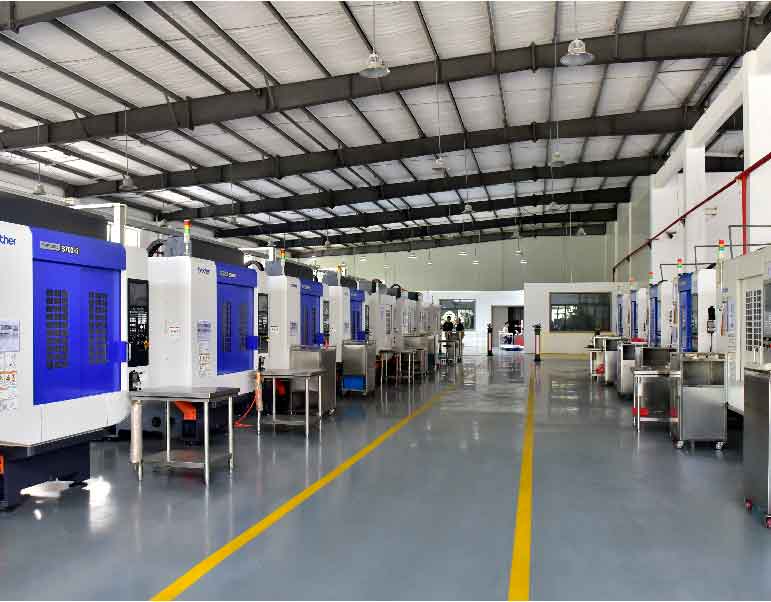
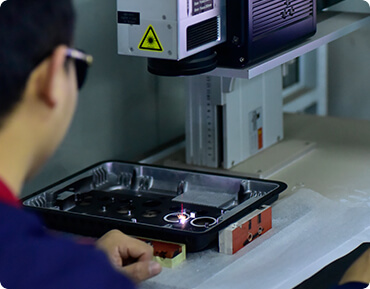
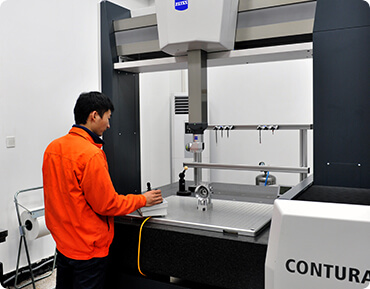
Recent Marine Aluminum Die Casting Projects
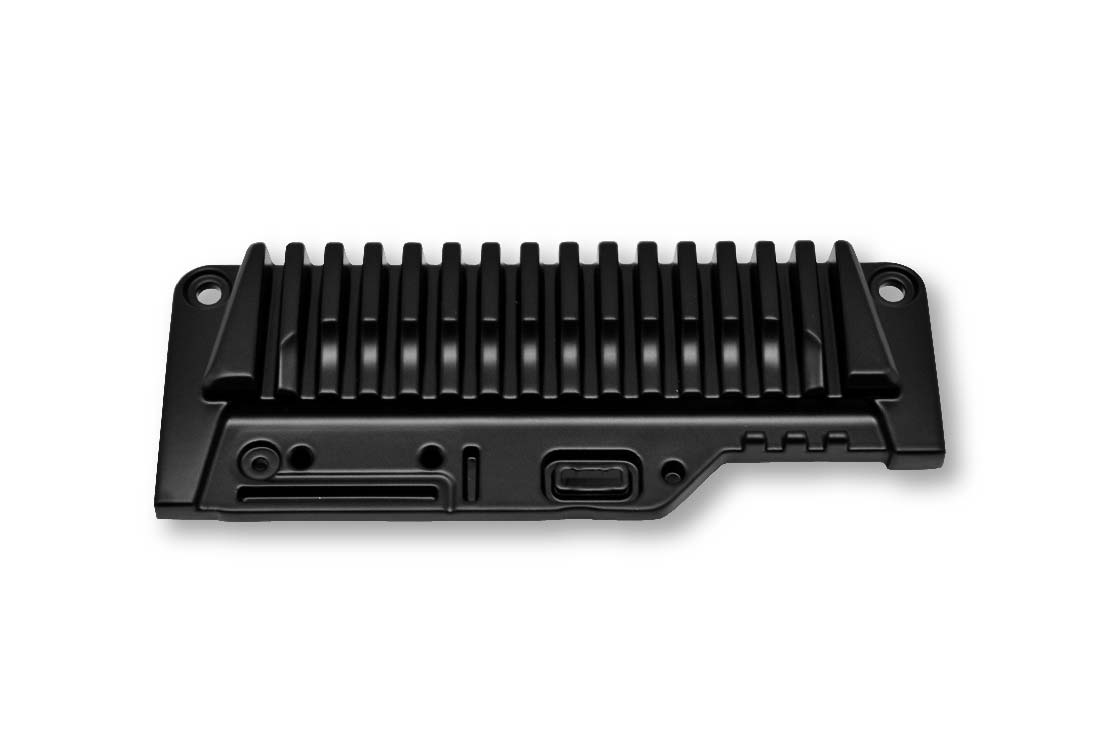
Part Name: HEAT SINK
Material: AlSi12
Size: 182*70*38mm
Weight: 432g
Machine Tonnage: 280T
Surface Finish: Powder Coating
Production Process: Die Casting–Trimming–Deburring
–CNC Machining–Chromating–Powder Coating–Screening–Packaging
Applied Industry: MARITIME
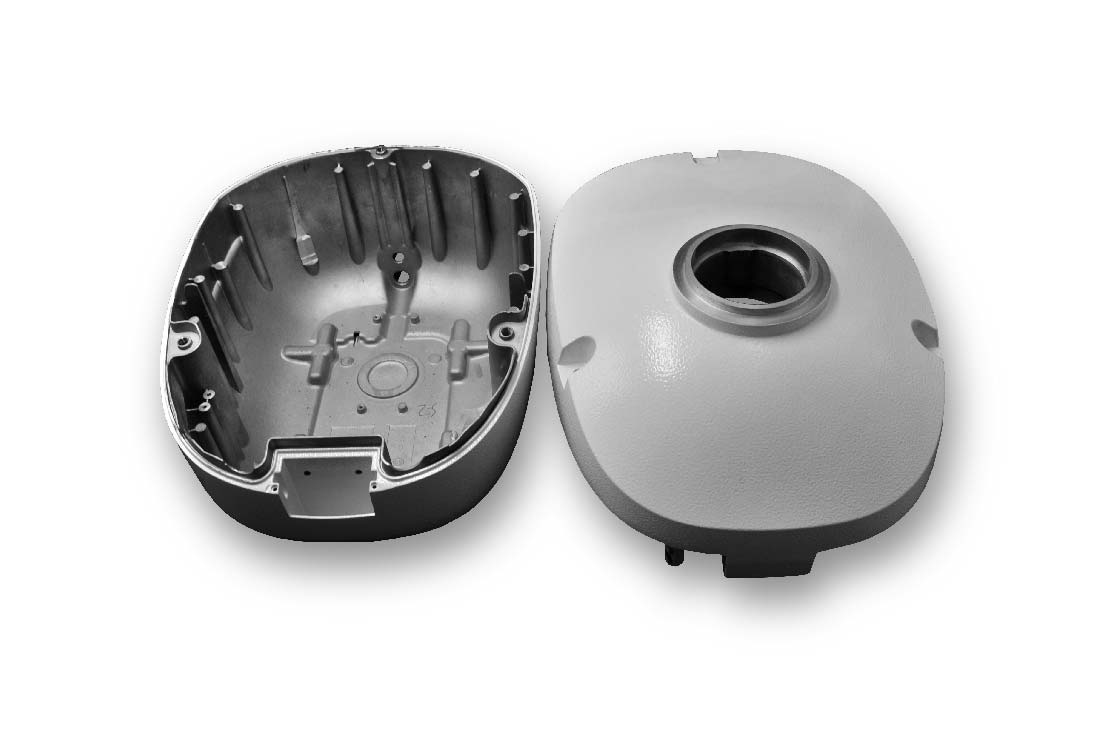
Part Name: RADAR HOUSING
Material: AlSi12
Size: 409*233*314mm
Weight: 5050g
Machine Tonnage: 1600T
Surface Finish: Powder Coating
Production Process: Die Casting–Trimming–Deburring
–CNC Machining–Chromating–Powder Coating–Screening–Packaging
Applied Industry: MARITIME
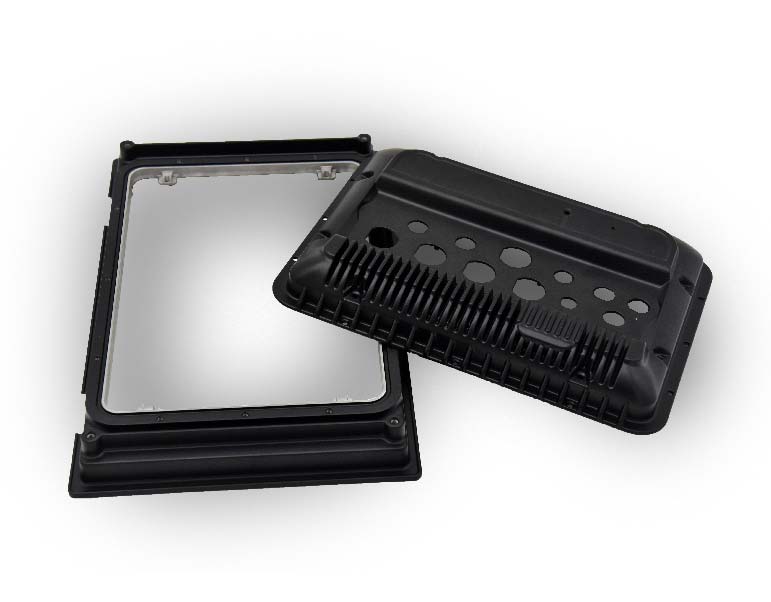
Part Name: DISPLAY FRAME
Material: AlSi12
Size: 317*229*38mm
Weight: 1230g
Machine Tonnage: 800T
Surface Finish: Powder Coating
Production Process: Die Casting–Trimming–Deburring
–CNC Machining–Chromating–Powder Coating–Screening–Packaging
Applied Industry: MARITIME
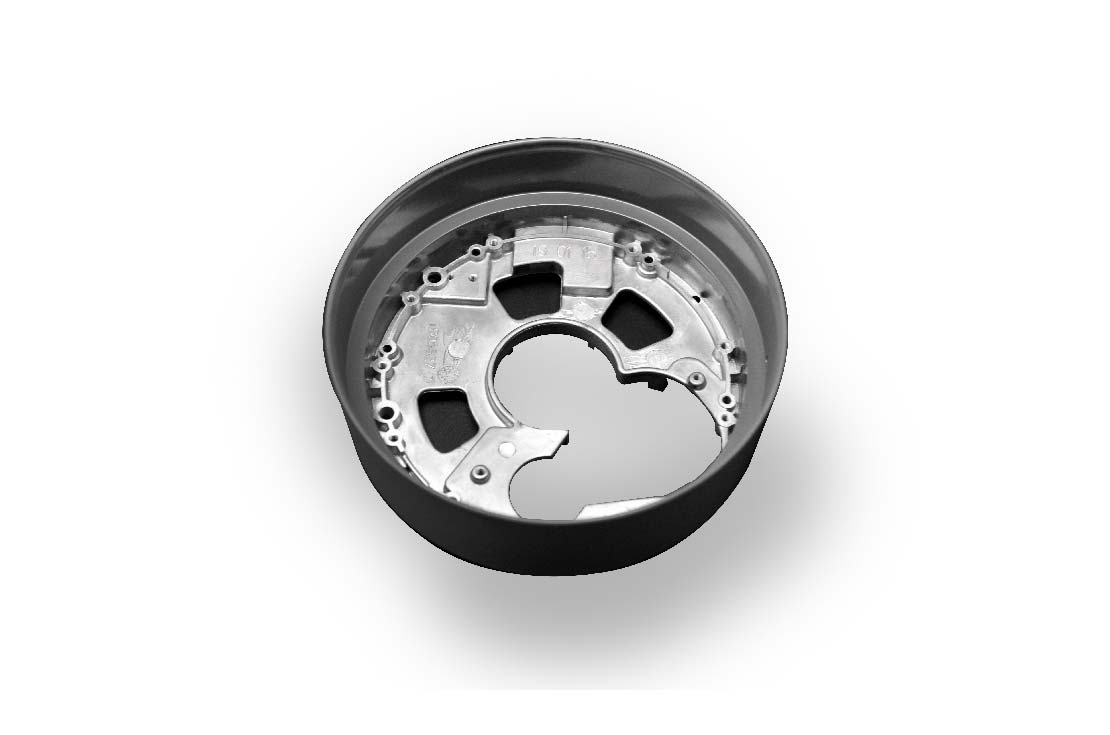
Part Name: CAMERA LAMP COVER
Material: AlSi12
Size: 109x109x48mm
Weight: 103g
Machine Tonnage: 280T
Surface Finish: Powder Coating
Production Process: Die Casting–Trimming–Deburring
–CNC Machining–Chromating–Powder Coating–Screening–Packaging
Applied Industry: MARITIME
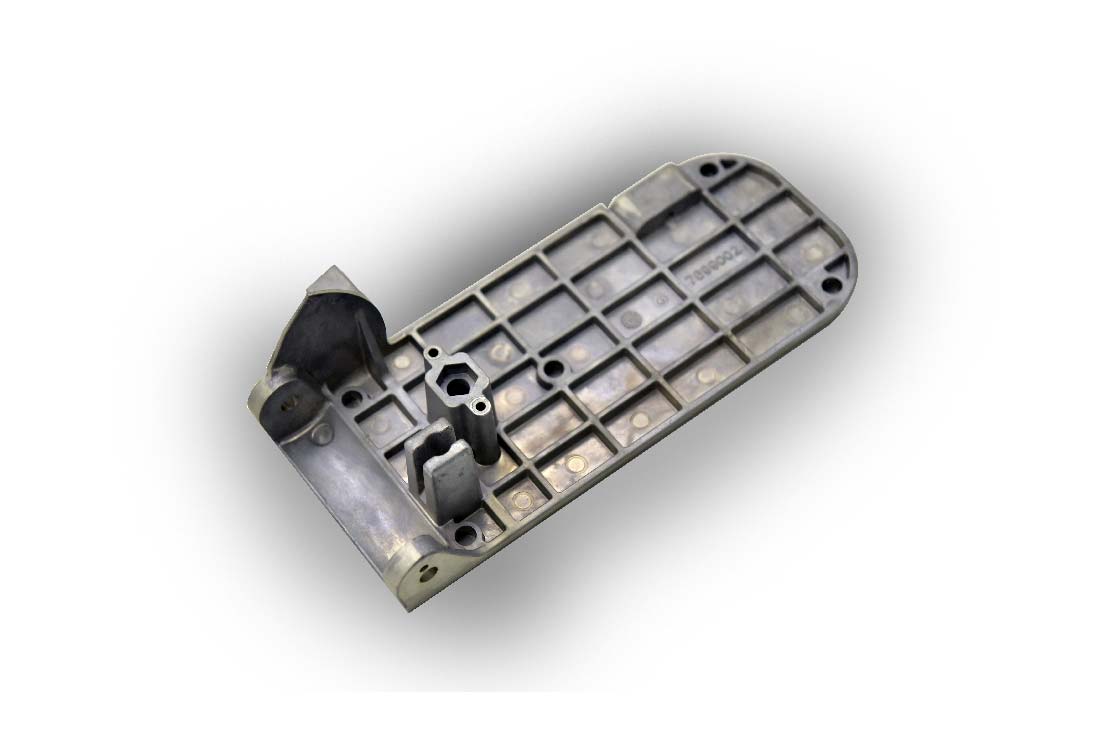
Part Name: PEDAL
Material: AlSi12
Size: mm
Weight: g
Machine Tonnage: T
Surface Finish: Powder Coating
Production Process: Die Casting–Trimming–Deburring
–CNC Machining–Chromating–Powder Coating–Screening–Packaging
Applied Industry: MARITIME
SUNRISE MARINE CASTING:
THE COMPLETE FAQ GUIDE
Marine Casting is a specialized form of casting because of the kind of environmental conditions we are dealing with.
Furthermore, now that sea contains more activity than ever before in history, Marine Casting became one of the essential and essential fields that we must focus on. With thousands of miles of coast and seawater, Marine Casting is a required field in the die-casting industry in China and the whole world.
- What is Marine Casting?
- How does the Marine Casting help protect the environment?
- What are the parts produced by the Marine Casting?
- What is the reason for using Aluminum in Marine Casting?
- Why does Marine Casting consider essential for the highly corrosive environment?
- What is the biggest challenge Marine Casting having to face in marine installations and how to prevent it?
- What is the importance of air/water tight-sealing surfaces near Marine Casting?
- What are the advantages of using Aluminum in Marine Casting?
- Why prefer Aluminum in Marine Casting?
- What are the applications of Aluminum Marine Casting?
- What are the advantages of Aluminum Marine Casting?
- What is the Marine-Grade Aluminum Casting Alloys?
- What are the characteristics of the Marine grade Aluminum Casting?
- What Marine-grade alloys used in Marine Casting?
- Why casting Aluminum for Marine applications?
- What are the reasons for the success of Casting for Marine applications?
- What are the annealing conditions of Aluminum alloys in Marine Casting?
- What are the physical properties of the Marine Casting Alloys?
- What is the engineering suitability of Marine Casting Alloys?
- What are the mechanical properties of the Marine Casting Alloys?
- What are the principles of Thermal Treatments for Marine Casting Alloys?
- What is the importance of pressure testing in Marine Casting?
- What are the steps taken to make Marine Casting leakproof?
- What are the finishing operations available for Marine Casting?
- How to improve the surface of the Marine Casting products?
- What is QC (Quality Control) standards followed during the Marine Casting Process?
- What factors affect the quality of Marine Casting products?
What is Marine Casting?
Specialized type of casting used to die-cast Marine related equipment, parts, and products.
Marine Casting is based on full applications that cannot be limited to ships, tankers, and marine installations but also includes Marine, submarine, bridges, valves, pump components, and sub-sea components/equipment.
Furthermore, deep-sea and installation equipment and tools are also a part of Marine Casting.
How does the Marine Casting help protect the environment?
Marine Casting is a big deal for protecting the environment.
The sea (water-based area) is a significant pathway for transportation goods and heavy machinery or equipment.
This also includes the transportation of different chemicals and oils. There are a vast majority of marine installations – models of transport that are used for the purpose of traffic as oil/liquid platforms, tankers, and ships.
However, these also can prove critical dangers to the environment and sea itself.
Any spill of dangerous and toxic materials or liquids can cause permanent damage.
In protection, we need durable, stable, and reliable materials that can last the course.
With the help of Marine Casting, it enables us to work with the materials that can prove helpful in the creation of a safer environment.
What are the parts produced by the Marine Casting?
The parts produced by our industry for marine applications are divided into three main categories:
- Maritime satellite
- GPS positioning system
- Hunting underwater system
Generally, the following parts are produced:
- Deck hardware
- Pumps
- Pump housing
- Cleats, handles, brackets, covers, and other boat and marine hardware
- Enclosures for the marine electronics
- Bearing housing
- Seal rings
- Seal housings
What is the reason for using Aluminum in Marine Casting?
One of the most important and commonly used metals in Marine Casting is Aluminum, and the reason it is used in Marine application is the following:
- A solid capacity to withstand corrosion and some alloys aluminum shows the best execution when presented to saltwater.
- High-level of resistance to stress-corrosion.
- Very high strength-to-weight- ration, and this makes the Aluminum one of the most durable metals in Marine Casting and nearest to Stainless steel.
Furthermore, it produces strength parts and makes installation easier.
- It’s cost-effective. Easier installation requires less effort and using less metal, which brings down the costs further. It’s a malleable metal and helps to make the stunning structural designs.
- It’s recyclable and which makes the earth and ocean cordial and practical over the long haul.
Other metals like Al-Zi (aluminum-zinc) and Al-Mg (aluminum-magnesium) also can help output sprightful and resistance to corrosion products/parts.
Marine Casting has gotten progressively significant with marine industries and structures currently requiring specific and aluminum castings.
Why does Marine Casting consider essential for the highly corrosive environment?
The seawater is the most corrosive-substance.
Aside from the water itself, the high salt substance can dissolve practically any sort of building material.
This is the explanation for the rusting of all metals when presented to seawater in a brief timeframe.
Moreover, the corrosive impact of the seawater can reach out to beachfront regions when high dampness content (seawater content) has a similar measure of effect on metal structures.
In any case, we should have a horde structure, going from ships for transportation to spans close to the coast.
Marine Casting is a specific part of casting where we use metals like Aluminum that are better ready to withstand such a domain.
What is the biggest challenge Marine Casting having to face in marine installations and how to prevent it?
One of the biggest challenges in marine installations is to develop and prepare something that is entirely durable.
The focus is always on developing something that can last for a long time and still be cost-effective.
It is now essential to resource metals that can last longer despite the corrosive environment and the pressure on specific installations, such as underwater structures and bridges.
Furthermore, the metal structure will start to rust, visible cracks, or start bucking under the high-pressure.
The casting of metals like Aluminum and stainless steel has been instrumental in creating more durable structures, even exceptionally gorgeous structural design and complex shapes.
What is the importance of air/water tight-sealing surfaces near Marine Casting?
Marine Casting requires air/watertight sealing surfaces.
That is likewise motivation to incline toward Aluminum in Marine Casting since Aluminum offers pressure testing and impregnation administrations to guarantee airtight marine-casting/casting/aluminum casting.
Furthermore, Aluminum in marine casting offers finishing options and activities such as powder coating and anodizing to protect further the final Marine cast product from corrosion.
What are the advantages of using Aluminum in Marine Casting?
There are two main reasons behind the use of Aluminum in Marine Casting, and they are the following:
Aluminum (Aluminum alloys) understands delivering exceptional quality, and excellent products consistently are vital to successful outcomes.
Following the ISO 9001:2015 standards in Marine Casting while using Aluminum is considered as the best way to produce high-quality and top-tier die casting casting parts and products.
Our industry is ISO 9001:2015 certified and has built our culture around quality.
For parts and products used in air/watertight, applications require critical sealing surfaces, and there is nothing best than Aluminum in this case.
Aluminum has excellent success with leakproof casting and Marine casting.
Our industry also offers the best testing and impregnation services alongside with the best Marine Casting products.
One-step aluminum casting industries are the best in the Marine Casting and also your best choice for single-source design assistance, tooling, casting, machining, anodizing, coating, and assembly.
Why prefer Aluminum in Marine Casting?
Aluminum is an active metal, which means that Aluminum’s nature is to oxidize rapidly.
Furthermore, soft-spot for most materials and metals; this quality is the center key – its capacity to oppose corrosion resistance.
When the oxygen is present in air, soil, or water, Aluminum instantly and rapidly reacts to form aluminum oxide.
Moreover, this aluminum oxide layer is synthetically attached to the surface and seals the center aluminum from any further harm and response.
This is a by and colossal incredible reaction from oxidation (corrosion) in steel or iron, where rust puffs up and chips off.
In any case, persistently uncovering the new metal to corrosion. Aluminum’s oxide film is tireless, hard, and in a split second self-reestablishing.
So, die to its corrosion resistance, Aluminum (aluminum alloys) is widely used and preferred for Marine Casting.
What are the applications of Aluminum Marine Casting?
Following are some the most crucial application in regards to Aluminum Marine Casting:
- Power steering units and parts
- Cleats
- Handles
-Brackets
-Covers and other boat hardware
-Enclosure for Marine electronics
- Marine engines
- Heat exchangers
What are the advantages of Aluminum Marine Casting?
Following are some of the essential advantages of Aluminum Marine Castings:
- Low-Cost Marine Cast products
- Precision and high-quality products
- Long-life tooling
-Unit cost savings over alternate manufacturing and production methods
-Outputs durable products
-Cleanable product surfaces that can be painted, powder-coated, or anodized
- Lightweight aluminum alloys with superior strength
- It has the ability to cast intricate-features
- Superb and excellent corrosion resistance
What is the Marine-Grade Aluminum Casting Alloys?
Marine-grade metals are extraordinarily treated to withstand use in water or wet environments and conditions.
Be that as it may, this is finished by adding unique alloys to the metal to make it corrosion-resistant.
Aluminum is considered as the metal that has marine grades.
Steel was utilized in shipbuilding enterprises as a result of its amazing mechanical properties and low assembling costs.
However, the increasing demand for large and lightships made the designers and industries search for alternative materials, and Aluminum is an excellent choice because of its high corrosion-resistance and unique mechanical and physical properties.
Aluminum likewise loads less and thought about economical over the long run.
What are the characteristics of the Marine grade Aluminum Casting?
Our industry uses aluminum alloys for Marine Casting because they are lightweight, corrosion-resistant, and have exceptionally excellent mechanical properties.
The following are the characteristics of Marine grade aluminum alloys:
- Exceptionally castable, fluid, and weldable
- Highly Corrosion-resistant
- Moderately strong and excellent
-The best option for the leak- and fatigue-resistant castings
-Used in critical and sophisticated components in marine applications
-Al-Mg alloys are non-heat treatable
- Strain harden-able
- Never lose toughness even at cryogenic temperatures
- Extrudable
Watercrafts made from aluminum alloys have:
- High-speeds
- Longer life-cycle/lifespan
- Lower maintenance costs
- Greater payloads
- High recycle values.
Industries which are proactive about corrosion control and wish to maintain a strategic distance from support and security issues, lean toward utilizing Marine Grade Aluminum Alloys.
What Marine-grade alloys used in Marine Casting?
Aluminum alloys are for the most part liked, and these alloys are commonly ordered by the essential alloying component added to Aluminum and the alloys’ capacity and solidarity to react to thermal and mechanical properties and treatment.
Cast aluminum alloys are formed by pouring molten liquid metal into aluminum die casting molds of shapes and later cooled:
Solid metal is mechanically and physically deformed, forged, or rolled to the required configuration to form wrought aluminum alloys (these alloys usually comprise aluminum-magnesium Al-Mg and aluminum-magnesium-silicon Al-Mg-Si alloys).
These are commonly utilized in auxiliary shipbuilding, vessel lifts, docks, marines, and other offshore basic applications.
Then again, cast aluminum alloys are utilized in immense quantities of marine applications since casting processes can make moderately complex shapes, superstructures, primary segments, inside installations, and different backings.
They usually are aluminum-silicon (Al-Si) or aluminum-magnesium (Al-Mg) alloys.
Why casting Aluminum for Marine applications?
The best casting methods utilized for Marine applications with aluminum is die casting.
For example, Aluminum alloys ADC12 with thin wall thickness is preferred for die casting.
The casting process enjoys lots of advantages, such as forging, welding, stamping, rolling, extruding, etc.
The Marine applications require a long lifespan and excellent mechanical properties and corrosion-resistant metals, and Aluminum is one of the best in regards to this requirement.
What are the reasons for the success of Casting for Marine applications?
The reasons in regards to the success of casting (aluminum casting) for marine applications are the following:
- Owing to physical properties, some metals can be possibly cast since they cannot be re-modeled into bars, rods, plates, or other shapes and complex shapes.
- It is a process that is highly adaptable to the requirements of mass production.
- Large numbers of the given casting can be produced rapidly and quickly.
- Certain lightweight aluminum alloys because of their respective strength and weakness can be produced only as casting.
- Shows excellent and exceptional bearing qualities.
What are the annealing conditions of Aluminum alloys in Marine Casting?
The annealing temperature for aluminum alloys should not exceed 415 degrees Celsius to avoid oxidation and grain growth.
The following conditions are applied to both heat-treatable and non-heat-treatable alloys.
- Recovery Annealing:
- Temperature (degree Celsius): 240 – 280
- Time (hours): 1 – 4
- Recrystallization Annealing:
- Temperature (degree Celsius): 330 – 380
- Time (hours): 0.5 – 2
What are the physical properties of the Marine Casting Alloys?
The following are the unique physical properties required for Marine Casting alloys.
Mostly Aluminum alloys are considered as the best for Marine Casting, and the following are the required conditions (properties):
- Density (kg.m3): 2630 – 2700
- Thermal Conductivity at 20 C (w.m-1 C-1): 125 – 160
- Coefficient of linear expansion between 20 and 100 C: 22 x 10-6
- Solidification Interval degree C: 615 – 690
- Mean Contraction (%): 11 – 14
What is the engineering suitability of Marine Casting Alloys?
The following are calculated and tested values of aluminum alloys engineering suitability for Marine Casting:
- Cracks Sensibility: 2 – 4
- Thin Pieces: 2 – 4
- Dimensional Stability: 3 – 4
- Weldability (TIG and MIG arc): 3 – 4
- Polishing: 2 – 4
- Anodizing for protection: 4
- Anodizing for decoration: 0 – 3
- Resistance to corrosion in the marine environment: 3 – 4
The values are stands for:
. 0 – Unsuitable, 1 – Poor, 2 – Fair, 3 – Good, 4 – Excellent
What are the mechanical properties of the Marine Casting Alloys?
The following are the mechanical properties required for Marine Casting alloys and considered essential.
- Form: Shapes, bar, tube
- Thickness (mm): 2 < t < 51
- Temper: T5, T6, H112, H111, O
- Rm (min): 190 – 310
- Rp (0.2): 95 – 260 MPa
- A % (**) min: 5 – 12
What are the principles of Thermal Treatments for Marine Casting Alloys?
The following are the possible principles of thermal treatments for Marine Casting alloys (mostly aluminum alloys):
- As-Cast, Solution heat treatment
- Quenching
- Natural aging
- Artificially aged to peak strength
- Under-aged
What is the importance of pressure testing in Marine Casting?
Nowadays, pressure testing is considered an essential part of Marine Casting, and it is conducted to assess the safety, reliability, and leak tightness of pressure systems and output products.
A pressure test consistently required for another pressure system before use or a current pressure system after fix or change.
There are two possible ways for pressure tests for Marine Casting:
What are the steps taken to make Marine Casting leakproof?
Water: as it solidifies, it expands.
In the Marine Casting universe, one would tend to believe that shrinkage would cause porosity and porosity would cause a leak and make it unusable for holding pressure in marine applications.
Solution:
To take care of the issues of porosity, current architects utilized comparable strategies.
Efforts typically concentrated on the casting process:
- Improving the molds
- Changing the temperatures
- Controlling the variables where possible
Furthermore, material refinement was the area that marine casting engineers explored for improvements, enhancements, and porosity elimination to make marine applications/products leakproof.
Specialists changed alloys and additives, likewise dismissing those materials that couldn’t be utilized and following the path of those that showed improved outcomes.
Design Changes: For the marine casting items themselves, including mass in specific locales of the casting, changing wall thickness, and moving materials were impeccable alterations.
In the die-casting machine, dies and molds, evolving risers, including cooling/heating, and expanding pressure were a portion of the endeavors that were made.
Besides, there were a few upgrades, however, porosity despite everything remained.
Modern process improvements and enhanced the results but no guarantee of the leakproof product.
Up to this point, marine casting improvement endeavors concentrated on the disposal of porosity to make the item leakproof.
What’s more, the best methodology is to analyze and characterize the sort of porosity and, a short time later, tackle the leakage issue through impregnation with resin sealants.
In any case, more prominent achievement can be accomplished by consolidating marine casting designing endeavors with a wide assortment of post-casting/post-machining impregnation strategies.
Our industry follows these modern improvement techniques and makes the guaranteed leakproof marine products/parts.
What are the finishing operations available for Marine Casting?
Surface finishing and plating are the finishing operations that are followed-up by the parts/components that require a decorative finish and corrosion resistance.
Following are some of the most popular marine casting surface finishes (finishing operations) sometimes required by marine casting products:
- Anodizing
- Chromate
- E-Coat
-Black Oxide
-Powder Coat
-Chrome Plated
- Bright Nickel
-Chem Film
-Copper-nickel-tin
-Cobalt tin
-Electroless nickel
- Gold plating
- Silver
- Nickel-Free Coating
- Polyurethane paint
- Impregnation
- Teflon
How to improve the surface of the Marine Casting products?
There are different types of surface finishing to surface improvement of Marine casted products.
Below is the list of the most common and preferred surface finishes for marine casted products:
- Abrasive Blasting
- Sandblasting
- Burnishing
-Chemical-mechanical planarization (CMP)
-Electropolishing
-Grinding
- Industrial etching
- Linishing
-Tumbling
-Vibratory finishing
- Buffing
- Shot peening
- Magnetic field-assisted finishing
Outside/External surface improvement finishes are applied to the items that necessary enhancing finish or corrosion resistance.
What is QC (Quality Control) standards followed during the Marine Casting Process?
Our industry ensures that the final Marine cast products and procedures/processes are according to two well-known QC standards;
- ISO 9001:2015
- ISO 13485:2016
- IATF 16949:2016
- QC procedures followed by our industry in regards to Marine Casting are the following:
- Delivering products that meet the customers’ requirements
- Opportunities that enable in order to enhance customer-satisfaction
- Addressing Marine risks/opportunities which are associated with its contexts
- Enhancement to achieve an effective process performance
- QC procedures followed by our industry in regards to Marine Casting according to the ISO 9001:2015 & ISO 13485&2016 & IATF 16949:2016;
- Continues Marine Casting products improvement
- Prevention of any physical defects from water (seawater)
- Reducing waste to enable the products environmentally friendly
- Casting the Marine products safety-wise perfect
- Change and warranty management for Marine Casting products
What factors affect the quality of Marine Casting products?
To gather information about the factors that affect the Marine Cast product’s quality, industries perform product analysis in which they identify its main features to understand more about the marine casted products and its uses.
There are three core factors that affect these products quality and they are the following:
Cost: The cost and budget for materials required to manufacture marine products.
The budget/price potential customers are willing to pay for the products.
Ergonomics: The marine casting products can be of different shapes and sizes that also can be complex and understanding it is a significant role and affects quality the most.
Materials: The selection of the right alloys is a critical phase and your outcome will be totally dependent upon this.
The selection of the right material will have an influence on the final design of the marine cast product.