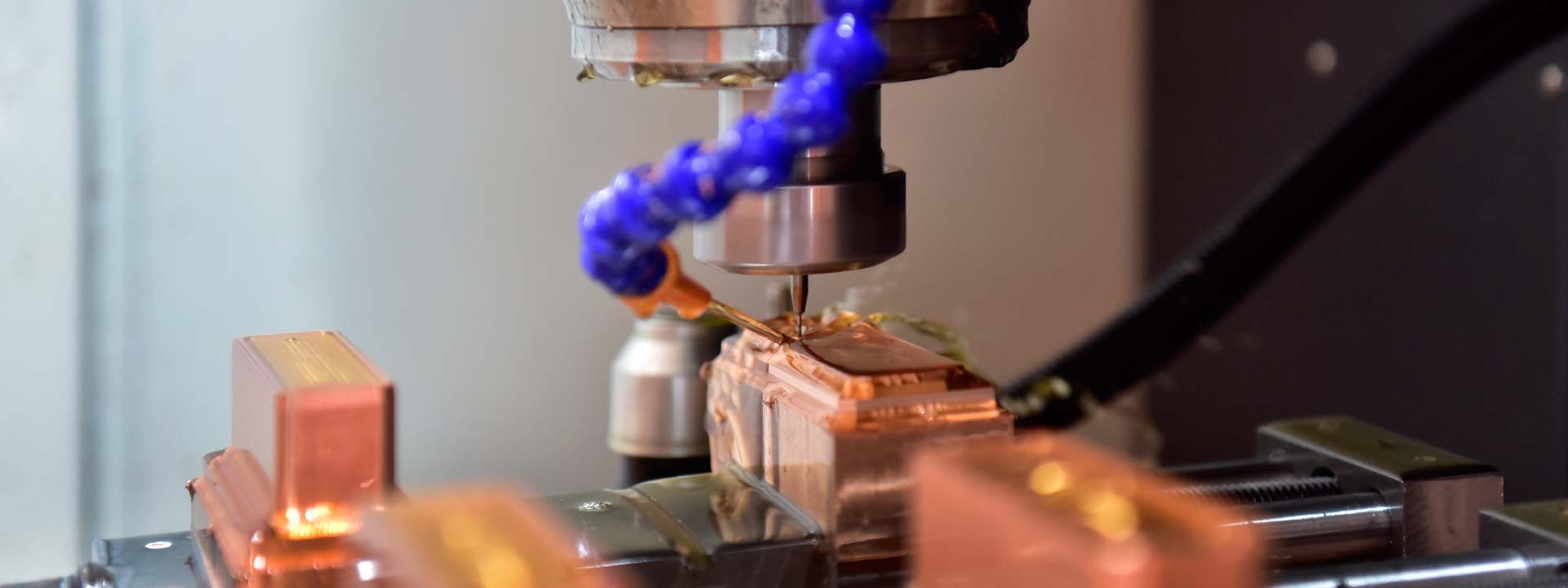
Die Cast Mold Professional Manufacturers in China - Sunrise Metal
Smart mold designer and die cast manufacturers providing high-quality tooling services
Sunrise Metals is devoted to the supply of high-quality die-cast molds in China. We offer a one-stop tooling solution from tooling design to end-management. You will find us to be one of the most experienced aluminum die cast manufacturers that support a variety of wholesale tools.
From design to production, we promptly consider your requirements and appreciate your input at every step. You can receive better performing products with our innovative designs that meet global standards. Sunrise is the die-cast mold manufacturer that delivers unmatched tooling services at an affordable price. We offer low-cost fixtures of your die cast molds regardless of the tool type.
Your Aluminum Die Casting Toolings Coming From Sunrise High-end Mold Machining Equipment
Rapid Die Casting Tooling Capability To Fulfill Your Projects
Get Rapid Services for the Production, Repairing, and Machining of Robust Molds
Sunrise has not only grown to become the leading aluminum die cast manufacturer of China but also an efficient aluminum die cast mold manufacturer. We produce, repair, and machine each part on time. Remarkable expertise of over 10 years helps us achieve premium results in the least time possible. We have made it our mission to deliver each part on time.
Our fast solution enables you to market your product rapidly by providing rapid tooling, rapid delivery services. We take 2-4 weeks in the design and production of your mold, giving you an absolute edge over your competitor.
Sunrise Metals engineers bringing innovation with over 10 years of experience in the industry.
As a leading die cast tooling manufacturer, we are proud of our team of managers always working to bring something new to the mold making industry. Every employee meets the requirements of ISO19001 and promotes quality management. Our experts enhance the quality of production with each batch. Skilled mold manufacturers, designers, and engineers work together to help you obtain production-ready parts with guaranteed quality.
Contact our experienced engineers for a quote today and learn more about our tooling services.
Productive Die Casting Tooling Supported By High-Tech Process Machines At Sunrise
Get Customized Die Cast Molds using Advanced Technologies
Die-Cast Tooling Manufacturer of Complex Molds Using Mold Flow Analysis
Advanced Technology: Sunrise manufactures superior products using its advanced mold flow analysis techniques. We offer our professional customization services that help you get your unique product and market it.
Essential Tooling: We specialize in manufacturing the required tools using a variety of materials. Sunrise is the premium die-cast mold manufacturer that creates a virtual simulation depicting the metal flow during the production phase.
Smart Analysis: All necessary results are analyzed before the design goes into the production phase. The end product you receive is one for which risk has been mitigated before production, which helps us give you flawless service.
- High Class Die Casting Tooling Equipment List
- Premium Quality Measuring Equipment List
Tooling Shop (Nantong) | Brand | Type | Stroke | Unit |
Grinder | TATUNG-OKUMA | KGS-615AHD | From 380mm to 1600mm | 4 |
Drilling | Shenyang Machine | Z3050*16/1 | 1600mm | 1 |
Sawer | Juli | MJ034W | NA | 1 |
Lather | Shanghai 2nd Machine | C6250A | 1000mm | 1 |
EDM | EDM Korea YIHAWJET Taiwan | NA | From 438mm to 1100mm | 8 |
CNC | Local Brand | SONYU-SL850 | From 850mm to 3015mm | 5 |
Wire Cutting | Local Brand | DK7763 | 800*630mm/1000*800mm | 2 |
Milling Machine | Local Brand | QJM-S2 | NA | 4 |
High-speed Cutting Machine | Local Brand | 906148 | 750mm | 1 |
Deep Hole Drilling | Local Brand | DHD-1513 | 1513mm | 1 |
Die Spotting Machine | Nice Dongguan | NC150-1511 | 1400mm | 1 |
EDM/wire cutting Combined Machine | Local Brand | DK7755 | 550*630mm | 1 |
EDM for a very small hole | Local Brand | DD703 | 300*400mm | 1 |
3D Laser Scanner | Si kan Hangzhou | HSCAN771 | NA | 1 |
No. | Name | Brand | Q’ty |
1 | CMM | Carl Zessis | 1 |
2 | CMM | SanYou | 1 |
3 | Spectrometer | China | 1 |
4 | Microscope | China | 1 |
5 | Projector | China | 2 |
6 | X-ray Detector | SANDT | 1 |
7 | Cleanliness Test Equipment | China | 1 |
8 | Leakage Test Equipment | China | 2 |
9 | Salt Spray Testing Equipment | China | 1 |
10 | Pneumatic Measuring Instrument | China | 2 |
11 | Hardness Testing Machine | China | 1 |
12 | Color Meter Machine | China | 1 |
13 | Thickness Testing Machine | China | 1 |
14 | Electronic Balance | China | 1 |
15 | Density Balance | China | 1 |
Die Cast Tooling Manufacturer of Tested Quality Mold
Modifying and Enhancing Quality of Molds with our Advanced Testing Equipment.
Sunrise Metals uses state-of-the-art technology including our Coordinate Measuring Machines, DMU monoBLOCK 5-axis CNC Machines, CNC precision machines to test the manufactured molds. Our automated machinery makes us one of the precision die cast mold manufacturers.
You are assured of the quality of our products using quality systems that keep us aligned with global standards. We acquire tryout services for large orders to maintain the quality of your product. Sunrise is the die cast tooling supplier of complex and detailed molds. Whatever part you require, our automated processes can produce these parts in no time.
DIE CASTING MOLD MANUFACTURER: THE COMPLETE FAQ GUIDE
A qualified Die Casting Mold Manufacturer can significantly increase the production capacity and quality of metal parts. So, make sure you have partnered with the right Die Casting Mold Manufacturer for maximum economy and quality.
In this guide, we shall briefly discuss various parameters related to die casting molds and services provided by the manufacturers in China. It should clear your confusion about what you are looking for and help you find the right supplier for your project.
- What is a Die Casting Mold?
- How Can Companies Benefit From Die Casting Mold?
- How Do Manufacturers Make Die Casting Mold?
- What are the Types of Die Casting Molds Typically Manufactured?
- What are the Common Issues Faced by Die Casting Mold Manufacturers Due to Improper Design?
- What are the Typical Components of a Die Casting Mold?
- Why Do the Die Casting Factories Apply Lubricants In Molds?
- What are Die Casting Molds Made of?
- What Type of Materials Can be Cast in Die Casting Mold?
- What Causes Shrinkage of Die Castings inside Mold and How Do Manufacturers Counter It?
- How Can Companies Ensure Higher Lifetime for Die Casting Mold?
- What accuracy can manufacturer reach for Die Casting Mold in Normal Industry?
- What are the Crucial Factors During Die Casting Mold Design?
- How Do the Die Casting Foundries Deal With Entrapped Air in Mold?
- How Can I Find a Good Die Casting Mold Manufacturer in China?
- Does Sunrise Metal Make Die Casting Mold For Companies Outside of China?
- Can I Use My Existing Die Casting Mold for Production?
- How to Control the Quality During Die Casting Mold Manufacturing?
- What is Your Standard Lead Time for Making Die Casting Mold?
- Why Should I Consider Partnering With Sunrise Metal For Die Casting Mold Manufacturing?
- Can Sunrise Metal offer vacuum die casting mold manufacturing?
- What Service can Sunrise Metal provide for Die Casting Mold?
What is a Die Casting Mold?
Mold is a prerequisite for any metalworking process, and that applies for die casting as well. The terms die, and tool is often interchangeably used to denote mold. Die Casting Mold is used for making metal parts by injecting fluid metal inside it.
It makes manufacturing a large number of parts much more efficient. Although, it can be pretty expensive as computer numerical controlled (CNC) machines are used for manufacturing die casting mold. CNC machines are costly and require skilled human resources to operate.
But, an experienced die casting company can guide you to optimize your design and considerably reduce your mold tooling cost. So, your choice of die casting supplier can prominently affect your experience with die casting.
Sunrise Metal is an expert aluminum die casting mold manufacturer located in China. Our first-class aluminum mold tooling services can ensure the best quality and economy for your project. If you are in search of a qualified Chinese toolmaker, we welcome you to learn about our die tooling services.
How Can Companies Benefit From Die Casting Mold?
Die Casting is one of the most efficient ways of manufacturing metal parts. And a big credit goes to the advanced molds used by die casting foundries. Below are some common advantages of die casting mold that can benefit a company’s production.
Higher Rate of Production
The most important advantage of the die casting mold is its huge production capacity. Die casting is one of the fastest means of production. And the molds makes it possible. Now a large volume of parts can be manufactured within a very short time frame.
Cost-Effective in the Long-Run
Die Casting mold can effectively function for a long period. So, per part cost for die casting is significantly reduced in the long run. And you can get the cheapest manufacturing solution from a high-pressure aluminum die casting mold factory.
Great Dimensional Stability
Die casting mold can create parts with excellent dimensional stability. Designers can implement tight tolerances and thin walls into the design. So, manufacturing parts with intricate details are very easy and much faster.
Exceptional Durability
Die casting molds are usually used for casting non-ferrous metals with a relatively low melting point. The mold is made with materials that have a higher melting point than the ones used for die casting. The molds can withstand very high pressure too.
How Do Manufacturers Make Die Casting Mold?
Die casting mold is made by CNC machining large solid metal block. CNC machining is an automated process. But there are many preparations needed before a die casting mold maker can initiate machining the operation.
The process of die casting mold tooling is described below.
Drawing CAD Model
To get started with mold making, you need a 3d model of your desired part. There are many CAD software available for this task. But, the designer must be familiar with some crucial design factors that can simplify the tooling process.
Preparing DFM
The actual design of a part needs to be adjusted a bit to comply with the machining process. This is known as Design for Manufacturing (DFM). Suitable mold design is created according to the part model. Some special features are included to make it easier to machine.
Mold Flow Analysis
Die casting mold tooling is very costly and time-consuming. So, it is highly undesirable to find any fault in the mold design after completing the mold. So, simulations are carried out beforehand to find out any inconsistency of metal flow inside the mold cavity.
Generating Codes
CNC machines can’t directly execute a model file. CAM software is a numerical control programming software that converts the CAD model into suitable codes for the CNC machine. The code provides instruction for the machining tools to follow specific coordinates and rotational speed.
CNC Machining
A metal block of suitable size is placed into the CNC Machine. Then the machine is programmed to start machining according to the given codes. The rest of the process is automated. The CNC machine can change tools automatically to implement different types of features in the parts.
What are the Types of Die Casting Molds Typically Manufactured?
You will see various types of die casting molds in a foundry. They can be classified based on their structure or the purpose they serve. Die casting mold makers usually classify them into the following categories based on their pattern.
- Single Cavity Mold
- Multiple Cavity Mold
- Combination Mold/Family Mold
Single Cavity Mold: Such a cavity can only create parts with individual designs. Single cavity molds are mostly used for casting relatively large parts.
Multi Cavity Mold: These have multiple cavities in the mold. Usually, smaller parts are cast in a pattern instead of a single one. The cavities are interconnected to allow the flow of metal among all the cavities.
Combination Mold: Combination mold is technically a multiple cavity mold. But instead of making a pattern of a single part, the cavities are made for different parts.
Now die casting molds can be further classified based on the purpose they serve. They are,
- Production Mold
- Prototyping Mold
- Trimming Mold
- Unit Mold
Production Mold: Production mold is machined with a higher degree of accuracy and designed to last longer. So, the tooling cost is significantly high. Production mold is only made after completing all tests and prototyping of a product.
Prototyping Mold: Prototyping molds usually have simpler details compared to the production mold. They aim to produce parts with the required mechanical properties rather than physical properties. So, unnecessary details are avoided in prototyping mold to cut the tooling cost.
Trimming Mold: A trimming mold is used alongside with a prototype or production mold. It is more like a cutting tool that is pressed against a die casting to separate parts from a pattern or remove residual metal attached to it.
Unit Mold: Unit mold is more like a portable mold. They are also known as die or mold inserts. They are smaller in size and designed to fit inside a base mold of a die casting machine. It is great for saving material when you need a large variety of molds.
What are the Common Issues Faced by Die Casting Mold Manufacturers Due to Improper Design?
Die Casting Mold designing is a sophisticated process. Even the slightest inconsistencies in the design can cause defects in the casting. Here are some of the common type of defects that many tool and die shop in China often faces during production.
Gas Porosity
It is a prevalent and undesirable casting defect that can arise due to multiple reasons. Gas pores are void spaces in the casting that hampers the rigidity and appearance of castings. In the case of mold design, it is caused due to bad ventilation in the mold.
The mold must have enough vents, risers, etc. to help the entrapped air inside escape. Creating a vacuum inside the mold cavity can also help to minimize porosity issues.
Cold Shuts
Cold shuts are formed when the fluid metal entering through two different gates becomes relatively cold before they merge. Due to the relatively cold temperature, the streams fail to merge properly, and cracks are formed.
Cold shuts can be avoided beforehand by conducting proper mold flow analysis. It allows the mold maker to determine the proper gating system for the mold.
Metal Flow Traces
Shallow runner and gates can cause the molten metal to splatter inside the mold. Narrow inlets increase the injection velocity of the metal. It causes the metal to splatter, and unwanted traces are left along the casting surface. Broadening the runners and gates can solve this issue.
Misruns
Misruns occurs when the fluid metal freezes too early and solidifies before reaching some deeper portion of the mold cavity. It is quite similar to cold shuts. But in this case, the molten metal solidifies before it can connect with another stream. A bad gating system is a primary cause of it.
Casting Stuck to the Mold
This type of problem can occur due to a lack of lubrication or an inadequate draft angle. The lubrication issue is not permanent. But the draft angle is a crucial design parameter for the die casting mold. Without a proper draft, removal of casting is difficult and often damaged.
What are the Typical Components of a Die Casting Mold?
A die casting mold is not just a simple shell for the casting. A die casting mold consists of many components. Each of those serves a specific purpose to compliment the casting process. Some of the important components are discussed below.
Cover Die: The die casting mold is mainly divided into two parts. The cover die is the stationary part of the mold. It is remains attached to the platen of the die casting machine during the whole process.
Ejector Die: The ejector die is attached to a movable platen of the die casting machine. It can clamp to the cover die to form a cavity. When the molten metal has been injected and solidified, it is reopened to retrieve the casting.
Shot Cylinder: It is actually a component of the die casting machine as a whole that extends into the mold. The fluid metal is poured inside the chamber, which is pushed inside using a plunger.
Runner: It is the path of entry of the fluid metal from the shot cylinder to the gates.
Gates: It is the connector between the runner and the mold cavity. The cross-section of the gate is smaller than the runners. There can be multiple gates in a single mold.
Ejector Pins: The ejector plate is equipped with some holes. The ejector pins can move through these holes to push a solidified casting. It makes retrieving the casting easier.
Ejector Plate: The ejector plate is like a housing surface for the ejector pins. When the ejector plate is pushed forward, the pins altogether punches into the ejector die.
Overflows: Sometimes, molds need to be provided with overflow channels. Because when the molten metal is solidifying, it undergoes shrinkage. Then the deficit of metal is then filled from the overflow channels.
Vents: These are small channels that allow entrapped air to escape the die casting mold. These are also used for accelerating the cooling of the parts.
Why Do the Die Casting Factories Apply Lubricants In Molds?
Lubricant or mold release agents are essential for any die casting operation. So, die casters in China and many other countries rely on these chemicals to achieve some added benefits. Some of the key reasons for using lubricants in the mold are discussed below.
- The solidified die casting tends to adhere to the mold. Forcefully trying to remove the castings often damages it. Applying lubricants make the casting ejection much easier. That’s why the mold is sprayed with lubricants after each casting cycle.
- The lubricants can improve the heat transfer characteristics of the liquid metal and reduces the chances of cold shuts.
- The lubricants create a wet surface over the casting at high temperatures. It keeps the surface of the parts clean and deters gas generation. So, it effectively reduces some common surface defects.
- Some lubricants can also form a protective coating over the die cast parts. It can increase the corrosion resistance of the parts as well.
- Water-based lubricants are used after casting is ejected. It effectively cleans and cools the mold surface.
So, manufacturers should use quality lubricants to obtain better results in die casting.
What are Die Casting Molds Made of?
Die casting mold must have higher temperature resistance than the metal it is supposed to cast. Ferrous metals are ideal for making molds due to their higher melting point and excellent machinability. In the case of aluminum die casting, most of the metal mold company uses H11 and H13 steel.
But, die casting molds created by CNC machining causes internal stresses to build up inside the mold. A convenient feature of ferrous metal such as Iron or Steel is that they can be heat treatment, which can relieve any internal stress within the mold.
What Type of Materials Can be Cast in Die Casting Mold?
The mold material must be able to withstand the high temperature of the molten metal. That’s why die casting utilizes non-ferrous metals because of their relatively low melting temperature. It is not impossible to die cast ferrous metals, but it is impractical and less commonly used for production.
Some suitable materials for die casting are,
- Aluminum
- Zinc
- Magnesium
- Brass
- Copper etc.
It is rare for any Chinese toolmaker to use a pure variant of any metal. All of the metals mentioned above are usually alloyed with other elements. There is numerous alloy composition available for each type of metal, and each of them has varying characteristics.
What Causes Shrinkage of Die Castings inside Mold and How Do Manufacturers Counter It?
Shrinkage is a common phenomenon in die casting. Normally any metal has less density in its liquid state. So, when the metal is cooling down and solidifies, it becomes denser. Thus the casting undergoes shrinkage due to solidification.
If a manufacturer doesn’t leave any allowance for shrinkage in the Die casting mold, the shrinkage could result in surface deformation. Shrinkage defect in a casting can be classified into two categories depending on its location within the casting.
- Open Shrinkage Defect
- Closed Shrinkage Defect
Open Shrinkage Defect
Sometimes a casting undergoes shrinkage, but there isn’t enough extra fluid metal left to fill up the void. In such cases, entrapped air within the mold fills up the void. Such a defect is open to the atmosphere and thus called Open Shrinkage Defect. Unlike defects caused by gas pores, open shrinkage defects tend to cone inside the casting surface.
Closed Shrinkage Defect
This type of shrinkage defect takes place within a casting. So, unlike an open shrinkage defect, it can’t be seen with a naked eye. The closed shrinkage defects are identified as microcracks inside the casting. Such type of defect is critical because it can’t be detected without testing with an X-ray detector.
It is difficult to eliminate the shrinkage of metal during casting completely. So, it is a major concern for many die casting mold suppliers in China. But, an experienced supplier can avoid shrinkage by proper mold design.
Shrinkage defect can be solved by following some design guidelines and keeping allowance for shrinkage defect in the mold. Improving the runner and gate design can also help in reducing the chances of shrinkage defects.
How Can Companies Ensure Higher Lifetime for Die Casting Mold?
Die casting molds are very costly to manufacture. So, customers want to keep their mold alive for as long as possible. Here are some tips that many China tooling shops use to increase the lifetime of the die casting mold.
- Preheat the die casting mold before injecting the liquid metal. Because when the molten metal with high temperature comes in contact with the mold, the sudden rise in temperature can cause the mold to develop cracks.
- Air vents or cooling channels can increase the rate of cooling of the casting. Keeping the temperature in check can keep the mold functional for longer without developing cracks.
- Giving heat treatment to the die casting mold can significantly increase strength and durability.
- Sometimes machining can induce internal stress in a mold. The mold should be machined carefully to avoid inducing any internal stress to avoid premature failure.
- Your precision requirement also plays a role in the life expectancy of the mold. Higher precision needs greater clamping force, and the injection is done at higher pressure. So, the mold is subjected to a greater extent of pressure.
There are many more minor factors involved that contribute to tool life. But, do keep a fact in mind that the die casting mold life is heavily dependent on the material you are casting.
Zinc alloy die casting mold offers the highest lifetime out of all, followed by aluminum die casting and magnesium die casting mold. Brass alloy casting offers the lowest mold life.
What accuracy can manufacturer reach for Die Casting Mold in Normal Industry?
CNC Machining is one of the most accurate processes of metalworking. Since the die casting mold is made by machining, the casting precision is also very high. The precision achievable by die casting molds can slightly differ depending on the casting material.
Typically most of the casting has a precision of up to 0.004 inches for the first inch. As the mold is machined deeper, the precision is 0.002 inches for each additional inch.
What are the Crucial Factors During Die Casting Mold Design?
There are multiple factors in mold design that can greatly enhance your die casting mold’s functionality. Some of the important design parameters are discussed in detail.
Draft Angle
The surface of die casting mold along the parting line is given an inclination for easier removal of the casting. This inclination is known as the draft angle. Providing an adequate draft is mandatory for any mold design. Otherwise, it can be difficult or impossible to eject a casting without damaging it.
Wall Thickness
Avoid thicker walls in design. They negatively affect the cooling of the molten metal. So, that increases the time required to complete a casting cycle. Also, maintain a uniform wall thickness throughout the design. Doing so can minimize the chances of heat pooling into a specific zone.
Fillets
It is desirable to replace any sharp edges with fillets because sharp edges take significantly longer time to machine. When it comes to CNC machining, the cost is directly proportional to the machining time. So, It is best to reduce the time as much as possible.
Undercuts
Having undercuts in your parts can complicate the mold design because undercuts can get your casting stuck with the mold. Carefully placing undercuts along the parting line can fix this issue. But it won’t be easy if there are multiple undercuts.
Deep Pockets
Try to avoid using deep pockets in the mold design. Deep pockets are time-consuming and need costly tools to machine. So, designers prefer to keep the depth of pockets limited.
Parting Lines
The parting line is an important parameter for the die casting mold. The orientation of a part should be chosen carefully considering the location of the parting lines. Proper orientation can greatly simplify the casting of some complex parts.
How Do the Die Casting Foundries Deal With Entrapped Air in Mold?
Porosity is a type of die casting defect that is caused due to entrapped air within the mold and the metal itself. Many China die casting foundries are doing extensive research to find an effective way to deal with porosity.
Gases infused within the metal can be removed by using some chemicals in it. But entrapped air inside the mold needs some special design considerations. Normally keeping proper ventilation channels can minimize porosity in the casting.
But in order to obtain almost pore-free casting, creating a vacuum inside the mold cavity can help. Traditional die casting machines can be paired with a vacuum-pump system to remove air from the cavity during casting.
The negative pressure induced due to the vacuum helps the liquid metal to travel through all recesses. So, the casting of intricate details and thin walls are easier. The parts are also free from porosity defects.
How Can I Find a Good Die Casting Mold Manufacturer in China?
Chinese manufacturers hold a significant share of the global die casting market. Numerous manufacturing businesses throughout China are offering mold making services. With so many choices at your hand, it isn’t easy to find the right supplier for your company.
Working with a qualified supplier will be a vastly different experience for you. Even with the same set of equipment, there are so many things that can go wrong during production. An experienced die casting manufacturer company can provide you the most effective solution for your project.
Here are some tips that can help you choose the right die casting mold manufacturer.
- Sort out your requirements. Keep a clear idea of what services you will need for your project. Aim for vendors that can provide a one-stop solution.
- Die casting mold manufacturing is heavily based on CNC Machining. So, Companies with a vast CNC machining capability is what you are looking for.
- Search the popular online business directories like Alibaba for finding China mold making companies.
- Keep in touch with international trade shows. They are a great way to find out about the leading B2B manufacturer companies.
- Check out whether the company you are interested in has proper quality assurance certifications.
- You can discuss it with your business contacts as well.
Following these tips can be helpful for you to find a good die casting supplier in China.
Does Sunrise Metal Make Die Casting Mold For Companies Outside of China?
Sunrise metal is a B2B China die casting supplier. Our continuous success in the manufacturing business has earned us a widespread reputation in China. We have successfully served many international clients from many regions of the world as well.
Our customers are mostly from European, North American, and Asian regions. We have served more than five hundred customers worldwide until now. Our fast solutions can significantly reduce the lead-time for mold-making.
So, we are able to keep our commitment towards foreign customers and provide on-time delivery. We also maintain a strong command of English to give our international clients a welcoming feeling and ensure better communication with them.
Can I Use My Existing Die Casting Mold for Production?
Yes, you are welcome to use your resources from previous projects. We provide both mold making and die casting services. If you already have a mold ready, then we shall focus on the die casting of your parts.
The die casting mold has to be compatible with our machines. But don’t worry because our mold making facilities can deal with any minor changes or adjustments if required. We try our best to ensure the satisfaction of our customers.
How to Control the Quality During Die Casting Mold Manufacturing?
Die casting mold requires strict quality control measures. Even the slightest defect in the mold can cause damage to your die cast parts. Quality control of the mold making process should be maintained from start to finish of a project.
Here are some quality control measures followed by the mold suppliers in China for creating high-quality molds.
Proper Communication with the Client
It is a common issue with many China manufacturing companies. Often there is a gap in communication with foreign clients. It is crucial to communicate with the client regularly. Manufacturers must have an exact idea of what the client really wants.
Thoroughly Check the Model and Coding
The die casting tooling process by CNC Machining is an automated process. So, there is no chance of human errors. But there still remains the possibility of making mistakes in the design or programming. So, designers and programmers better recheck their work to ensure that it is free from errors.
Keeping Track of Progress When Machining
It is crucial to keep monitoring the die tooling process. Even if it’s an automated process, sometimes issues may become apparent during machining the mold. Identifying any problems in the early stage can save a lot of work and hassle.
Inspection of Precision with CMM
The ability to produce precision parts is the charm of die casting. The supplier must ensure the precision of the mold. Inspect the die casting mold with a Coordinate Measuring Machine for verifying all the geometric parameters.
Check for Internal Defects with X-Ray Detector
Sometimes the machining stress can cause internal cracks to develop. It can result in reducing the integrity of the mold. So, the mold should be checked with an X-ray detector to find out traces of any internal cracks.
Following these guidelines can help improve the quality management system of any die casting mold manufacturer in China.
What is Your Standard Lead Time for Making Die Casting Mold?
With our advanced rapid tooling facilities, we can make die casting mold within the course of 2-4 weeks only. It is about half the standard lead time required by most of the die casting mold manufacturers in China.
If you need the fastest mold-making services available out there, we can help! You may be eager to enter the production phase sooner or have a tough to meet schedule. With our enriched tooling facility and experienced employees, we shall provide you with on-time delivery.
Why Should I Consider Partnering With Sunrise Metal For Die Casting Mold Manufacturing?
There are a ton of die casting mold manufacturer in China. So, why choose us? We welcome you to check out our services and facilities and find out for yourself whether we have the capability to live up to your expectations.
Our Fast Solutions Ensure Half the Standard Lead Time
We have talented engineers who can design and optimize your parts within a relatively short period. Our rapid tooling facility can significantly reduce the tooling time as well. So we can reduce the production tooling time by up to fifty percent.
We Have a Dedicated Tooling Facility for Mold Manufacturing
We have a tooling shop dedicated entirely to deal with any mold manufacturing projects. Our in-house tooling solutions aim to provide you with a one-stop solution. We can create, repair, and carry out maintenance operations for your mold.
Our Engineering Team Has Rich Experience with Molds
Our engineering team consists of professionals dealing with mold manufacturing projects for a long time. They can design molds for you and run a mold flow analysis to ensure the perfection of your project. You can get cost-saving suggestions and tips from them to make the mold more efficient.
We Have the Latest Technology Equipment
Our mold making capabilities are apparent from our advanced set of die casting tooling equipment. We have more than 23 machine centers in our tooling shop. We also have the latest 5 and 7-axis CNC machines that are capable of handling very complex jobs with ease.
Implemented Strict Quality Management System
We pride in our superior quality control for our mold making services. We have a dedicated quality control team for assessing the quality of your projects. The molds are checked with advanced QA Test devices such as the CMM and X-ray detector. We also earned international certifications for our quality management system.
Can Sunrise Metal offer vacuum die casting mold manufacturing?
Yes, we manufacture vacuum die casting mold. Vacuum die casting is an effective solution for reducing porosity in casting. We aim to manufacture mold with top-notch quality. So, we focus on making vacuum-assisted mold to ensure optimum quality.
We can modify your existing die casting molds to make them suitable for vacuum die casting as well. The molds can be redesigned to link it with a vacuum pump. It can remove entrapped air from the mold during casting, thus improve the casting quality.
What Service can Sunrise Metal provide for Die Casting Mold?
Sunrise Metal has varied services available for aluminum die casting mold. Some of our important services are discussed below.
Provide DFM of Mold
Our technical mold design team can provide effective design for manufacturing for your mold. They can optimize your models to make them easier to machine and allow better workflow during casting. It also helps to reduce tooling costs as well.
Validation of Mold by Flow Analysis
Our engineers are capable of handling advanced mold simulation software. We can validate the numerical modeling from the flow analysis data. It helps us minimize the chances of any possible errors while making the mold or die casting parts.
Repair and Maintenance
Sunrise Metal can confidently provide a lifetime guarantee of your mold. Our die casting mold repair and maintenance facilities make it possible for us. We can repair any used molds at our tooling shop. We regularly run maintenance on the existing molds to keep them functional for a longer period.