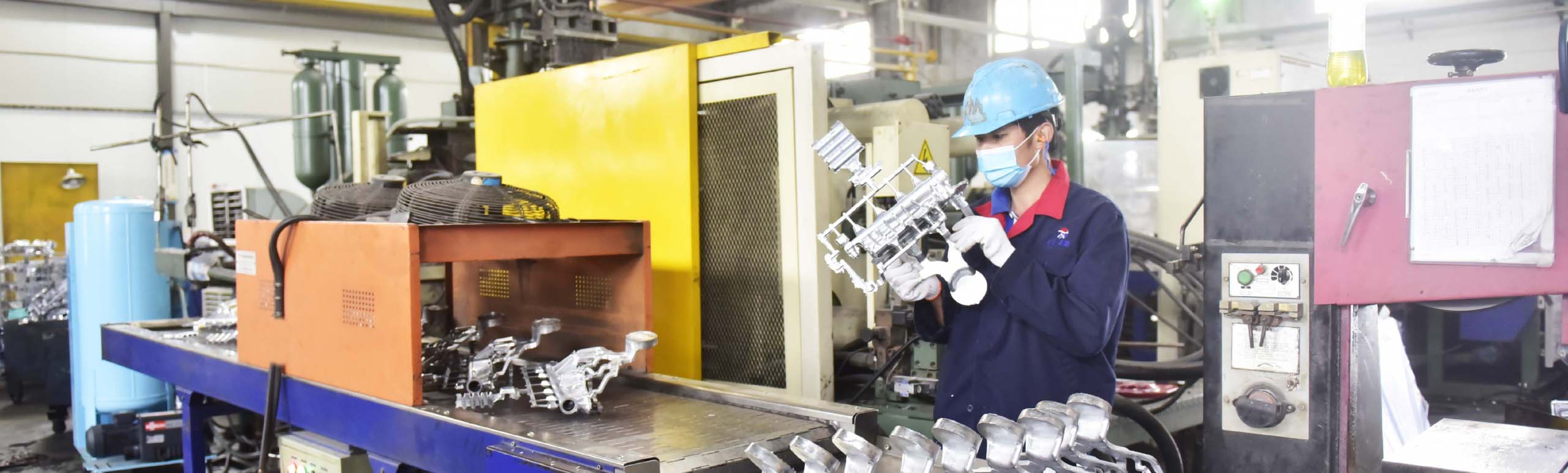
Precision Die Casting Leading Manufacturer in China - Sunrise Metal
Sunrise is a leading supplier of high-quality die casting components manufactured through precision die casting.
This production process has been known to be effective for all engineering machines. And it is one of the manufacturing techniques that Sunrise deals in efficiently. Our expert teams take serious control of every process in order to complete requirements and deliver the most satisfying result.
Quality assurance teams at sunrise check and inspect product development to ensure it meets international compliance standards. For customized requirements, top-rated engineers assist in the planning and designing of your consignment for 100% success.
Precision die casting is supported by our dedicated die casting facility. It is equipped with modern and efficient machinery that fully complies with the quality management system. It can handle diverse operations even in custom parts for exact requirements.
2500+ Die Casting Parts Manufacturing Experience From 500+ Global Clients
How Sunrise Precision Die Casting Manufacturing Capability Help Your Projects
Our long-lasting capability in Precision Die Casting production, enables us to offer service at competitive prices. Whether you need a stated solution for short or long runs, small or large components, simple to complex design and shapes, we have the versatility to quote competitive and competent casting.
Before the precision die casting production starts, our engineers first review the design details. For instance, we would share our insight and ideas allowing you to develop output with optimum performance. They can also design mechanical parts and provide technology support for DFM & PPAP, etc
Sunrise has built a reputation as a trusted one-stop-shop precision die casting solution helping customers under one roof. These include Rapid Prototyping, Tooling, Die Casting, Machining, Assembly in house and various surface treatment, together with value added services.
We do strict inspections of all processes from raw material to final shipping. With our high-level measurement lab, Sunrise ensures all the parts manufactured are up to the standard requirements.
Precision Die Casting Parts Accomplished With Sunrise Advanced Manufacturing Equipment
Precision Die Casting Projects
We offer complex, thin-walled, high precision die casting solutions to be used in industrial applications. We provide a comprehensive component solution to be used in manufacturing units such as pump, valve housing, and more.
- Team Advantage
- Capability Advantage
- Location Advantage
- Order QTY Advantage
Sunrise Metal has skillful organization teams, including experienced engineers, professional customer service specialists, quality control and skilled production workers. Together, they perform at an outstanding pace and impress customers with their abilities.
With 4 dedicated facilities,182 skilled professionals, we provide our customers 1-stop aluminum die casting solution including rapid prototyping, die casting tooling, aluminum die casting, CNC machining, and surface finishing.
Our company is located in angtze River Delta, with 9 Airports, 2 world busiest ports of Shanghai & Ningbo. And the most dense High speed train networks in China / world.
If you have trouble finding the right supplier, Small suppliers cannot ensure the quantity. You need Sunrise Metal where our mission satisfies the demand of your high mix and low to medium volume die casting projects.
Get A Free Consultation
Experts at Sunrise are ready to assist in providing engineering consultation for Precision Die Casting Parts. We will give you suggestions and solutions based on your CAD and Step drawings.
PRECISION DIE CASTING:
THE ULTIMATE FAQ GUIDE
Precision Die Casting is a sophisticated method of metal casting for the production of high precision parts. But it can be quite expensive, and mainly preferred for casting ferrous metals and parts with special geometric features.
High-Pressure die casting is a cost-effective alternative to Precision Die Casting for casting non-ferrous metals. We prepared this guide to give you the basic idea of Precision Die Casting. This should help you choose the right die casting method.
- What is Precision Die Casting?
- What is the process of Precision Die Casting?
- What are the advantages of Precision Die Casting?
- What are the Disadvantages of Precision Die Casting?
- What metals can be cast by Precision Die Casting?
- What are the applications of Precision Die Casting?
- What is the precision level of Precision Die Casting?
- Is Precision Die Casting expensive?
- Is Precision Die Casting suitable for low volume production?
- How does Precision Die Casting differ from Sand Casting?
- Is Precision Die Casting better than High-Pressure Die Casting?
What is Precision Die Casting?
Precision Die Casting is also commonly known as Investment Die Casting. Precision Die Casting was very popular in the manufacturing industry before the arrival of High-Pressure Die Casting.
Precision Die Casting a process based on an old metal casting technique known as lost-wax casting. Castings done this way have the capability to produce parts with some special geometric features.
Such type of geometry is often not possible to produce using other manufacturing methods. Precision Die Casting is also preferred for its ability to produce parts with high precision. This is a reason why Precision Die Casting is still being used by the industries.
But Precision Die Casting has a significant amount of production costs involved. Unless the parts to be manufactured, have a geometry that can’t be manufactured easily using other methods, High-Pressure Die Casting would yield parts much faster and cost-effectively.
That’s Why Sunrise Metal uses High-Pressure Die Casting for manufacturing high precision parts. Because we aim to provide our customers with a fast and cost-effective solution.
What is the process of Precision Die Casting?
Manufacturing parts using Precision Die Casting has a lot of steps involved. We will guide you through the process step by step to give you a better understanding of Precision Die Casting.
Tooling using CNC Machining
In the past Investment Die casting mold was done manually. But after CNC Machines became more available in the market, tooling is done by CNC Machining and the process started to get recognized as Precision Die Casting.
Now, Precision Die Casting tooling is done using CNC Machining for producing parts with higher precision.
Injection of Wax
After the dies are ready, Wax Material is injected into the die cavity. The Wax spreads uniformly inside the cavity obtains the shape of the die cavity. Once the Wax solidification then the wax model is detached from the dies.
Coating with Refractory Material
The wax is then dipped inside a slurry of a suitable refractory material such as Ceramic. It should be dipped several times until a thick layer is formed around the Wax model. Leave the refractory material until it hardens
Melting the Wax
The ceramic shell along with the wax heated under high temperature. The heat must be sufficient for melting the entire wax without leaving any trace.
Pouring of Molten Metal
Molten metal is poured into the ceramic shell until it is completely filled. Leave the melt inside the shell for cooling and solidification.
Retrieve the Casting
Finally, break the ceramic shell once the molten metal is completely solidified to retrieve the casting.
You can also have a look at this video for a visual representation of the Precision Die Casting process.
What are the advantages of Precision Die Casting?
Precision Die Casting can be beneficial for certain types of casting operations. The advantages of Precision Die Casting are as follows.
Ferrous Metal casting
It is one of the major advantages of Precision Die Casting. Other die-casting techniques are limited to non-ferrous casting. That gives Precision Die Casting an upper edge.
Good Mechanical strength
Precision Die Casting can produce parts with really good strength. This a reason industry that need high strength parts prefer Precision Die Casting.
Good Surface Finish
Precision Die-Cast parts yield parts with a really good surface finish. That minimizes the need for additional surface finishes and thus saves some money.
Supports complex geometry
Some geometric features are really difficult and expensive to cast using other methods of die casting. Such complex parts can be cast more easily by Precision Die Casting.
What are the Disadvantages of Precision Die Casting?
Precision Die Casting comes with some disadvantages as well. Let’s have a look at some of the disadvantages of Precision Die Casting.
Expensive
The main drawback of Precision Die Casting is that it is more expensive than other casting methods. There is a high initial tooling cost, and a constant preparation cost associated with it due to other processes that take place later on.
Slow Casting Cycles
Precision Die Casting is much slower than other casting methods. Because every casting cycle requires a lot of preparation.
Labor Intensive
Precision Die Casting also requires more labor as well. There are a lot of things to do and prepare in this process. And increased labor means more cost.
High-Pressure Die Casting can overcome the disadvantages that are associated with Precision Die Casting. So, it is preferable to go for High-Pressure Die Casting for a faster and economical solution.
What metals can be cast by Precision Die Casting?
Both ferrous and non-ferrous metals can be cast using Precision Die Casting. This is one of the main reasons for adopting Precision Die Casting instead of other die casting methods. Because Other die casting methods can’t cast ferrous metal yet.
The common ferrous metals alloys that can be cast using Precision Die Casting are,
- Stainless Steel
- Cast Iron
- Carbon Steel
- Alloy Steel etc.
The common non-ferrous metals alloys that can be cast using Precision Die Casting are,
- Aluminum
- Zinc
- Copper
- Brass
- Magnesium
- Nickel
- Lead
- Tin
- Titanium etc.
Precision Die Casting can cast most of the common metals known to us. That makes it a universal method regardless of the type of metal.
But Precision Die Casting is a costly method and only suitable for casting metals that can’t be cast using other methods. For example, High-Pressure Die Casting can get the job done much more cost-effectively for non-ferrous metals.
What are the applications of Precision Die Casting?
Leading industries that need high strength parts with very good accuracy chooses Precision Die Casting. Some major industries where this process is commonly used are listed below.
- Automotive
- Aerospace
- Electronics
- Defense
- Medical
- Agriculture
- Commercial etc.
Although there has been a significant rise in the usage of the High-Pressure Die Casting process. Before Precision Die Casting was popular due to its ability to cast ferrous metals. But, with the advances of technology Aluminum die casting has become a better and cheaper alternative to Precision Die Casting.
What is the precision level of Precision Die Casting?
Precision Die Casting is popular for its ability to produce parts with high-precision. It can usually achieve a precision close to ± 0.005 inches for most of the common metals. Precision as close as ± 0.002 inches is achievable for some metals.
The reason behind such a high level of precision is due to die tooling using CNC Machining.
CNC Machining can be considered the most precise method of tooling until now.
That’s why Precision Die Casting can produce parts with very complex geometry and sharp details. The repeatability of casting is also great and yields almost identical parts.
Is Precision Die Casting expensive?
Precision Die Casting is one of the most expensive metal casting methods. It is considered to be costlier than most of the common casting methods such as High-Pressure Die Casting and Sand Casting.
Precision Die Casting is costlier because of the varieties of operations required for a complete cycle of casting. The Precision Die Casting tooling is done using CNC Machining and it is the major cost affecting parameter.
The cost of the Precision Die Casting is often inevitable if you are dealing with ferrous metal casting. Because Precision Die Casting is one of the few established methods for casting high precision ferrous metal parts.
But there are alternative casting methods available for non-ferrous other than Precision Die Casting. Low to Medium volume of casting using Precision Die Casting will be rather costlier.
Non-ferrous metal casting can be only cost-effective for a large volume. It is better to go for High-Pressure Die Casting for obtaining similar results.
Is Precision Die Casting suitable for low volume production?
No, Precision Die Casting is only economical for large volume production. In the case of low to medium volume metal casting, Precision Die Casting can be quite costly. So, it is not recommended.
The die tooling required for Precision Die Casting can be very expensive since it is done using CNC Machining. Along with that, additional tasks like wax model preparation, refractory coating, and wax melting adds more cost and time to the process.
The per parts cost would be high in case of low to medium volume projects. But Precision Die Casting can be cost-effective for mass production of high precision parts. The per parts cost keeps going lower as you produce more parts.
A good thing about the dies is that they last for thousands of casting cycle. So, there is only a one-time cost for tooling eventually gets distributed to the number of parts produced.
As a solution for Low to Medium volume projects High-Pressure die casting would be great a cost-effective alternative. The process of casting is also shorter compared to Precision Die Casting.
How does Precision Die Casting differ from Sand Casting?
Sand casting has been a popular metal casting technique for a long time. Sand Casting uses sand as a mold material. Sand is a very common material and available everywhere. That is a major factor affecting the cos of Sand Casting.
Sand molds are very cheap to create, and sand also has good refractory properties. Sand Casting needs very low investment and can be done without any expensive equipment. That’s why many local manufacturers use Sand Casting.
But a cheaper solution won’t necessarily be the best one. Sand Casting is only cheap when done in smaller quantities. Sand casting has very poor casting quality. It is not so accurate and often has defects in the parts.
Sand Casted parts have a rough surface and need additional treatment later on. If you need a smooth surface for your parts, that will ultimately increase the production cost. So, Sand Casting is not a choice for parts that have delicate applications.
That’s why the manufacturers prefer Precision Die Casting when the precision and quality of the parts matter. Precision Die Casting will be for sure costlier than sand casting.
But the quality you get compensates for the extra cost.
Is Precision Die Casting better than High-Pressure Die Casting?
High-Pressure Die Casting is considerably one of the best methods for casting non-ferrous metals. The process of High-Pressure Die Casting is much simpler than Precision Die Casting.
The only major part of the process is the die tooling.
Die tooling requires a 3d CAD model of the part. Using the model data, the dies are machined to perfect dimensions using the model data using CNC Machines. Once the dies are ready, they are placed into the die casting machine and enclosed together.
Molten metal is poured inside the shot cylinder that leads to the die cavity. Then the molten metal inside the shot cylinder is pushed under high pressure, and it spreads uniformly inside the die cavity.
Once the molten metal inside the die cavity cools down and solidifies the dies are taken apart to retrieve the finished casting. There will be some excess metal attached to the parts that are trimmed down using a trim die.
As you can see the whole process High-Pressure Die Casting is less complicated than Precision Die Casting. And the casting cycles take less time compared to Precision Die Casting due to having fewer operations.
Sunrise Metal has advanced CNC Machining and Die casting facilities that can provide you a faster and economical solution. We can reduce the production tooling time by up to fifty percent.
We use High-Pressure Die Casting to provide you high-quality parts while ensuring quality, economy, and on-time delivery.
You can check out this video to find out about our Die casting services.