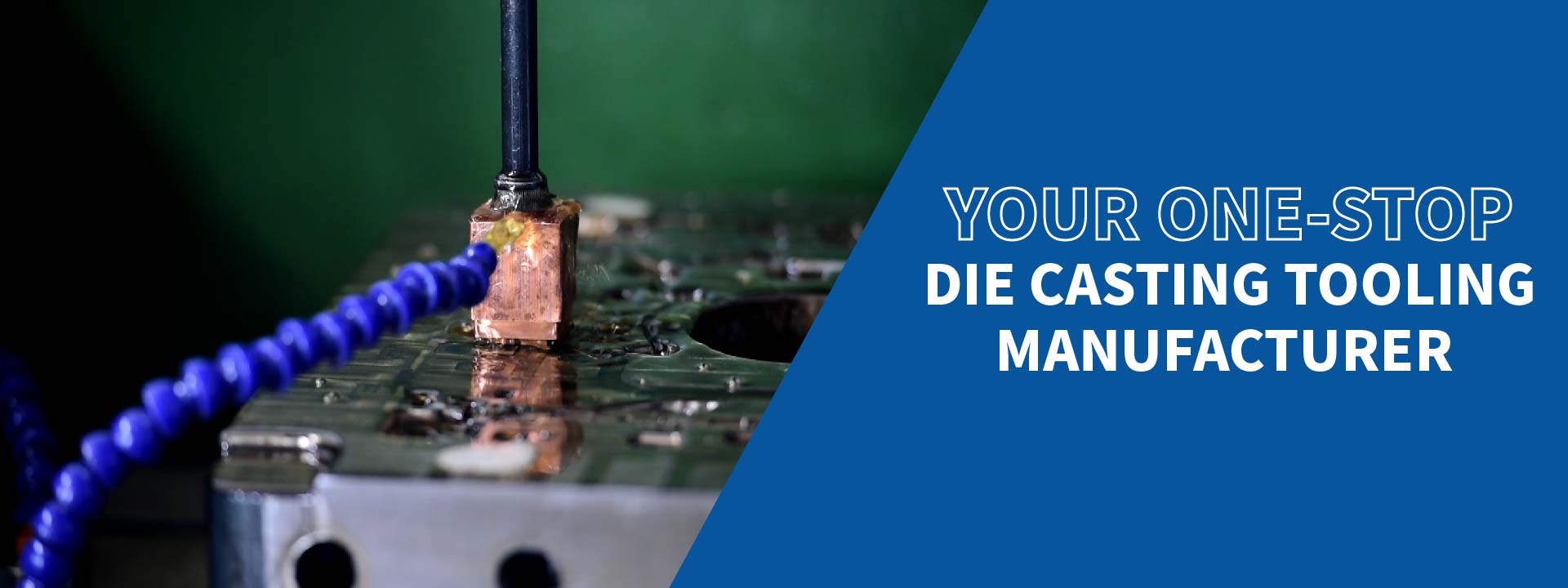
Die Casting Tooling Competent Manufacturer in China
Die Casting Tooling is crucial to the success of aluminum die casting production.
Sunrise Metal is a fully functional and experienced aluminum die casting manufacturer in China. We are dedicated to manufacturing high-quality and reliable die casting toolings and aluminum die casting.
As a professional China aluminum die casting manufacturer, our strength lies in delivering quality cost-effective die cast tooling and die cast components to suit customer’s requirements.
1000+ Die Casting Tooling Manufacturing Experience From 500+ Global Clients
Competent Die Casting Tooling Capability To Fulfill Your Aluminum Die Casting Projects
Our mold designers utilize the latest technology in engineering and mold flow analysis, including flow simulation technology & other engineering software, such as Anycasting/Pro-Engineer/CREO & AutoCAD, etc. This is very important in die casting mold fabrication and die casting manufacturing. This will assure your success.
A team of experienced tooling engineers can help you with your concept visualization, functional analysis, mold flow analysis, and complete mold design. This will help to prevent the most possible problems during the dies manufacturing and aluminum die casting productions.
As a professional China die casting tooling manufacturer, Sunrise Metal has Tooling design & Mold construction & Tool validation & Repair and Maintenance All In House. We can always respond quickly to your die casting tooling fabrication and aluminum die casting production.
High Quality Die Casting Tooling Supported By High-Tech Process Machines At Sunrise Metal
Recent Die Casting Tooling Projects
Ultrasmooth die casting tooling designs and manufacturing processes are at the centre of Sunrise Metal’s commitment. Currently, we are engaged in various projects with long-standing clients:
- Experienced Team
- Advanced Equipment
- Global Clients
- Premium Quality Equipment
- Fast Delivery
Sunrise Metal has skillful organization teams, including experienced engineers, professional customer service specialists, quality control, and skilled production workers. Together, they perform an outstanding result for our worldwide customers who demand high-quality die casting tooling and aluminum die casting products.
No. | Name | Stroke | Q’ty |
1 | Mazak 7-axis turning&milling Machine | Ø658*1011MM | 1 |
2 | Mazak /Hass 5axis CNC machine | Ø850/Ø600 | 4 |
3 | 3-axis CNC machine center | 2000*1500MM | 1 |
4 | 4-axis CNC machine center | Ø250*800MM | 8 |
5 | 3-axis CNC machine center | 1000*600*600MM | 20 |
6 | CNC Lathes | Ø320*800/Ø610*1000MM | 2 |
7 | Sodick Wire cutting Machine | 400*400*200MM | 3 |
8 | EDM machine | 500*400*400MM | 2 |
9 | Surface grinder | 600*300*200MM | 1 |
No. | Name | Brand | Q’ty |
1 | CMM | Carl Zessis | 1 |
2 | CMM | SanYou | 1 |
3 | Spectrometer | China | 1 |
4 | Microscope | China | 1 |
5 | Projector | China | 2 |
6 | X-ray Detector | SANDT | 1 |
7 | Cleanliness Test Equipment | China | 1 |
8 | Leakage Test Equipment | China | 2 |
9 | Salt Spray Testing Equipment | China | 1 |
10 | Pneumatic Measuring Instrument | China | 2 |
11 | Hardness Testing Machine | China | 1 |
12 | Color Meter Machine | China | 1 |
13 | Thickness Testing Machine | China | 1 |
14 | Electronic Balance | China | 1 |
15 | Density Balance | China | 1 |
Get A Free Consultation
If you have any questions on your die casting tooling projects or you are looking for a China aluminum die casting manufacturer, you are welcome to contact Sunrise Metal. Our experienced engineering team consults for your die casting mold projects with skillful suggestions and solutions based on your CAD and Step drawings.
DIE CASTING TOOLING:
THE ULTIMATE FAQ GUIDE
Die casting tooling helps to produce aluminum die casting components to the desired shape and form. Sunrise Metal is a leading aluminum die casting manufacturer in China, We produce high-quality aluminum die casting tooling with long life spans.
Abiding by strict international standards, we pay special attention to the structural design and finishing of die casting toolings so that they are durable. Our die casting tooling department also helps to optimize key aluminum die casting manufacturing process and we provide reliable aluminum die casting components for a large range of industries worldwide
- What is an aluminum die casting tooling?
- What are the key steps involved in preparing an aluminum die casting Tooling?
- How is the cast part removed from the aluminum die casting tooling?
- What is the service life of a typical aluminum die casting tooling?
- Which factors determine the lifespan of aluminum die casting tooling?
- What kinds of aluminum die casting toolings can last longer and optimize production processes?
- What is the use of moving die and fixed die in aluminum die casting tooling?
- What is heat treatment for aluminum die casting toolings?
- What are the benefits of using heat treatment for the production of aluminum die casting toolings?
- How to do heat treatment for aluminum die casting tooling?
- What is the aluminum die casting tooling base?
- How is an aluminum die casting tooling repaired and maintained?
- What are the components of aluminum die casting tooling?
- Is aluminum die cast tooling-making a complex and expensive procedure? Why?
- What are some of the best materials to use when making die casting tooling?
- What are some of the metal casting processes that make use of die casting tooling?
- Which factors need to be considered when choosing a material for aluminum die casting toolings?
- Do aluminum die cast toolings impact the quality of aluminum die casting parts being produced?
- How to produce high-quality aluminum die casting tooling design?
- Why is it important to get the draft angle right during the aluminum die cast tooling-making process?
- How is a prototype tooling designed?
- What is the mold flow analysis for aluminum die casting tooling and why is it important?
- Can the best aluminum die casting tooling designs be achieved using flow analysis and computer simulations?
- How to ensure production of high precision aluminum die casting tooling? Do CNC machines help?
- Why should poorly manufactured aluminum die casting toolings be discarded before use?
- What kinds of top aluminum die casting tooling design techniques and machining are employed by Sunrise Metals?
- DMU monoBLOCK 5-axis CNC Machine
- Coordinate Measuring Machine
- High Precision CNC machine
- How does Sunrise Metal implement cost-optimized tooling manufacturing?
- Which new systems and technologies can be used to optimize cost and efficiency in the aluminum die casting tooling process?
What is an aluminum die casting Tooling?
Aluminum die casting tooling is a tool that helps shape the aluminum die casting part in the required form. It is a hollow block that creates dimensionally accurate parts and offers faster production.
Aluminum Die cast toolings consist of two halves, a feeding half and the ejector side. The mold is sprayed by a release agent which ensures the easy removal of the casted part.
The feeding half is mounted on a fixed plate whereas the ejection half is found on a moving plate. The moving plate is used to eject the part inside the molds.
Different types of toolings are used in die casting. These can be permanent as well as temporary. The permanent toolings are used again and again while temporary toolings are discarded after use.
Many different techniques are used to manufacture the molds. Molds are manufactured according to the process they’re going to be used in, the type of metal to be casted in the mold and the dies being used in the process.
What are the key steps involved in preparing an aluminum die casting Tooling?
Different techniques and materials are used in the preparation of aluminum die cast toolings. It is created using the template of the final object. The material used in the construction of molds is reflected in the die casted piece.
The following steps outline the die casting dies making process:
Designing
The mold to be manufactured is designed in this step. The positioning of each bend is defined during the designing process. The specs and other data required for the manufacturing are laid out. Dimensions and tolerances are also measured in this step.
Construction
Whichever technique is to be used for construction is applied on the design in this step. It is carried out under detailed supervision due to the high precision required for final products.
Secondary Processing
The part then goes through the process of machining and is finished through processes like heat treatment and grinding.
Assembly
All the parts required in the mold are assembled in this step. Mold used in die casting is not a one piece set up. It joins different parts to make a mold.
How is the cast part removed from the aluminum die casting tooling?
Once the molten metal is set in the mold, it is allowed to cool down. After the part is casted, it is ejected from the ejection part of the mold. Ejector pins are found in the ejection half that push the casting out of it. The ejector part is placed on the moving plate.
As the plate moves, it drives the ejector pins to move all at once and eject the casting. All of the pins are driven at the same time with the same force. This keeps the casting intact. Once the casted part is removed, the pins come back to their position and are set for the next casting.
The force of the pins is kept as low so that they might not affect the casted part which is still hot. The ejector pins can leave a mark on the casting as well, so they’re managed and placed in positions that can’t hurt the final product.
What is the service life of a typical aluminum die casting tooling?
The service life of aluminum die cast mold ranges between 50,000 shots and 150,000 shots. The life of the mold depends upon its usage, the temperatures it stands, and the amount of machining required. Many processes and techniques are carried out to increase the life of mold.
Different aluminum die casting processes have different molds and hence have varying service lives. To maintain the functionality of the die cast mold, it is important to increase its service life. It can be done during the production of the mold and sometimes regulations are required during its service life to maintain its efficiency. If the maintenance is not carried out, it might affect the uniformity of the die casted parts.
Which factors determine the lifespan of aluminum die casting tooling?
The lifespan of aluminum die casting tooling does not remain constant. It is affected by different factors such as:
Stress Concentration
The mold has to have stress endurance in order to stand the pressure. The die cast product can form sharp corners or cross-section changes which can affect the structure of the mold. A deformation or cracking of the mold due to successive heat treatment can occur. The mold is to be designed to stand all of that.
Machining
If the mold is not machined properly, it can affect the lifespan. The finishing of the mold is to be done properly so as to endure the stress concentration. The failure to do so can cause early failure of the mold.
Grinding and EDM
In the production of mold, grinding time tends to be an important factor. If not carried out properly, it can cause high surface residual stress and tissue changes and hence can produce grinding cracks. Electric Discharge Machining (EDM) helps with the corrections of the surface.
Heat Treatment
The deformation of the mold occurs if the heat treatment and the stress exceed its yield limit. The thermal stress can cause the early failure of the mold. It can also cause the quenching of part.
Production Operation
The production of the casting part can affect life of the mold. The processes being carried out are done with extreme care so as not to affect the mold. The speed of the injection of molten metal and the ejection of the casted parts is carried out to remain beneficial for both casted part and the mold.
What kinds of aluminum die casting toolings can last longer and optimize production processes?
The aluminum die casting toolings have a lifespan that is affected by many factors and is shortened by many of these. In order to make them last longer and optimize the production process, certain processes are carried out. These techniques are either applied during manufacturing of the toolings or by their maintenance.
Structural Design
The molds with the structural design that prevent sharp corners and cross sections can last longer. A reasonable structural design deformation and cracking, along with a uniform shape and symmetry standard should increase the lifespan of the mold.
Finishing
The finishing of the mold can impact its production efficiency and life. The thickness of the mold is ensured. The two-sided processing maintains concentricity. The machining is carried out properly in order to improve the quality of the mold.
Preheating of the mold
The mold is preheated when the hot molten is to be inserted. This can prevent the formation of cracks as preheating prepares the mold for the high temperatures.
Injection speed
The injection of molten metal in the mold is a huge factor that affects the life and the production efficiency. If the speed is too high, the mold corrodes and if the speed is too low, the part formed is defective. The average speed kept is 43m/s in order to form a perfect balance.
What is the use of moving die and fixed die in aluminum die casting tooling?
Aluminum die casting tooling structure makes use of two hardened steel dies. The two dies are created in order to achieve a better casted product.
Moving die
This die has the ejection part of the mold attached to it. It contains ejector pins that work to eject the casted part and a runner. It drives the pins uniformly to efficiently eject the molded part without affecting any of its properties.
Fixed die
This die part is fixed and allows the moving of molten metal inside. It takes up the metal and sets it inside. When the metal is shaped, it floats off to the moving die. The fixed die is secured to the stationary platen of the mold.
What is heat treatment for aluminum die casting toolings?
The heat treatment of aluminum die casting toolings is a process that alters the properties of molds. It involves the method of heating and chilling in order to achieve desired results like softening or hardening of the mold.
Many different processes such as annealing, tempering, carburizing, normalizing quenching and case hardening are carried out for the heat treatment of molds. The overheating of the mold can however cause over burning. This deteriorates the properties to the extent that they can’t be remedied. Heat treatment is thus carried with extreme care.
What are the benefits of using heat treatment for the production of aluminum die casting toolings?
As heat treatment changes the physical, chemical, and mechanical properties of mold material, it gives beneficial results. Some of them are as follows:
- The durability of the molds becomes higher as it provides case hardening. This will cause lesser fracturing and will leave it working for a longer time.
- Internal stresses of the mold material are relieved due to alternate heating and cooling.
- The machinability of the mold increases and it becomes easier to work with.
- The mold softens while leaving the outer surface hard. This makes it flexible.
- The electric and magnetic properties of the material are improved.
- The resistance of the mold to wearing, heat, and corrosion increases.
- Minimal surface decarburization is achieved.
- As the mold becomes more flexible, the operational cost also decreases.
- The surface oxidation decreases and causes less deformation.
The following video shows how heat treatment affects the mold blocks:
How to do heat treatment for aluminum die casting tooling?
There are different heat treatments for die cast molds. Some of the techniques used in heat treatment include:
Quenching
In this process, mold is heated at a rapid rate and then cooled down. It is heated above the upper critical temperature and then cooled down using gases or sometimes liquid since liquid has more thermal conductivity. The rapid cooling will cause a hard and brittle structure in the mold.
Annealing
Annealing is carried out by heating the mold to a specific temperature and then cooling it down with a rate that creates a microstructure that separates the constituents. Annealing is carried out using these two techniques for molds. These are:
- Normalizing: This is carried out by heating the mold above critical temperature and keeping it there for some time. The mold is then cooled down in air. This causes a uniform structure in the mold.
- Stress relieving: This is carried out by heating the mold above critical temperature and then cooling it uniformly. The mold obtained will have reduced internal stresses.
Tempering
Tempering is carried out to reduce brittleness of the mold. The mold is quenched and the temperature to which it is to be heated, is kept for some time until the stresses are relieved.
What is an aluminum die casting tooling base?
Aluminum die casting tooling base consists of the outer periphery of the mold. It contains all the cavities that are included in the mold. The following parts of the mold are held in the base:
- Fixed half retainer plate
- Fixed half mold plate
- Moving half mold plate
- Spacer blocks
- Ejector plate (top)
- Ejector plate (bottom)
- Moving half retainer plate
- Runner stripper plates when 3-plate structure is utilized
The structure is alternated depending on the process being followed and the material being used. There are two types of mold base structures:
- 2-plate structure
- 3-plate structure
The gate is used for the casting process also determines the type of mold used. Keeping the gate inside the mold is an important task and must be kept at a specific place. If not placed carefully, the thickness of the walls deviates from the requirements. A mold base helps to keep the gate in place.
What is a die casting tooling cavity and how is it created?
The mold consists of a core and a cavity. A cavity is the structure of the resultant product. It is the concave plate. It sometimes has the same shape as the part to be produced and sometimes a part is inserted in order to obtain the finished part. It actually creates a space or cavity that is filled with molten metal in order to achieve the metal product.
These cavities can be replaced to create different shapes of products. The cavity is created by using different processes like CNC machining and printing. An impression of final product is utilized in the process.
How is an aluminum die casting tooling repaired and maintained?
The repairing and maintenance of molds is absolutely necessary for them to work efficiently and to last long. The molds are passed through different stages in order to achieve the finest results.
History
The history of any faults in the design of the mold is necessary. It is important to know any prior defects that are seen in the mold. This helps in a deeper examination and achieves better results.
Disassembly
The mold is then disassembled in order to find newer defects. This is done with extreme care and a specific part is kept in mind before the disassembly. Disassembly is usually done in 3 levels as an industry standard.
Troubleshooting
The technician analyzes each part and finds the trouble in the mold. This is done by reading past issues, as well as gathering new readings using different tools. Each defect is then repaired and corrected one at a time.
Correction
The correction and troubleshooting are done side by side in order to achieve better results.
Cleaning
The disassembled parts are then cleaned in order to get the best results. The cleaned tools do not let any impurities get stuck in the end result.
Assembly
The pieces are then assembled accurately. This is a critical stage in the process as a small mistake can cause sizeable losses. Every piece is to be put in its place correctly.
What are the components of aluminum die casting tooling?
The aluminum die casting tooling components are the parts that make the mold work. These parts are assembled to create a complete mold and produce efficient results. The key components of the die casting mold are:
Mold bases
The mold base is a structure of the mold. It contains all the components that are assembled together to work. It helps to hold the gates inside the mold and produce better end results.
Pins
The pins are found inside the mold that are used to eject the casted part out of the mold.
Ejectors
The ejector part of the mold is placed on the moving plate. After the complete formation, it ejects the casted part.
Lifters
This moves on an angle to let the ejector remove the casted part. The release of the mold is eased up with the use of lifters.
Bushings
Bushing is placed between the molten metal and the cavity in order to provide reduced friction and easy ejection of the metal part.
Guides
The guides are used to guide the needles when ejecting the casting.
Alignment devices
These devices are used to align all the parts of the mold. The mold is kept consistent with use of alignment locks and other devices.
Is aluminum die casting tooling -making a complex and expensive procedure? Why?
The use of aluminum die casting toolings makes the process of casting very easy. Duplicate products can be manufactured in a matter of hours. This has made the process a versatile procedure but, at the same time, it’s not as simple to implement in all cases. Mold making is a complex manufacturing process and must be done with extreme care. Every single stage directly affects the end result.
However, if done properly with the right temperatures, right treatments and best procedures, it leads to excellent molds and great castings. But, the more the process deviates from ideal conditions, the higher the chances of ending up with defects in the casting parts.
Die casting dies making is cost-efficient in the long term but a high initial cost is required for the process. Therefore, it is ideal for large production volumes of die casting parts.
What are some of the best materials to use when making a aluminum die casting tooling?
Aluminum die casting toolings make use of different materials depending on their specifications. The most widely used material in the making of die casting dies is tooling steel. It is used in different forms as different forms provide different properties to the mold. The commonly used forms are H11 and H13. Tooling steel is used for its following properties in the industry for mold making.
Machinability
Tool steel can be machined and produce high quality finished products. However, this machinability reduces with addition of impurities in the tool steel products. Nonmetallic impurities are reduced using various techniques and a uniform distribution of carbides is achieved. The tooling steel can then be drilled, milled and turned easily.
Heat Treatment
The heat treatments are done in order to achieve better mold life. Tooling steel allows heat treatments at high temperatures. It has a tendency to turn hard after certain temperatures. The hardness of the tool steel increases its toughness and ductility. The steel can withstand higher temperatures ranging to 1050°C.
Dimensional Stability
The mold created goes through different stresses such as machining stress, thermal stress and transformation stress. Tooling steel is machined and heat treated to get rid of such stresses.
What are some of the metal casting processes that make use of die casting tooling?
Die casting toolings are used in the manufacturing of large-scale die cast machine parts using aluminum and its alloys. Applications are wide-ranged, namely in the medical casting, telecom casting , automotive casting and marine casting , aerospace casting, and general industries die casting.
Molds play a vital role in determining the final net shape and quality of the metal components. Since these molds are used repeatedly to produce parts on a massive scale, it is important to ensure top-quality and precision. They are used in:
- Aluminum, zinc and magnesium die casting process
- Sand or permanent mold process
Which factors need to be considered when choosing a material for aluminum die casting toolings?
Choosing a material for aluminum die casting toolings depends on a number of factors. These include but are not limited to:
Cost
The affordability of the material is an important factor while making the choice of mold material. The ability of the material to create the mold and deliver the results with greater ROI is considered in the process of choosing mold material.
Material specifications
The specifications of the material are kept in mind for tooling making. The malleability, ductility, resistance to wear and hardness are some of these specifications. The materials with more of these properties are considered an ideal choice.
The complexity of product design
The product to be designed through the mold is kept in mind for the mold. The complexity of the product can alter the decisions. The product to be created has to be ideal theoretically and hence the choice of the material.
All of these and many more standards like endurance of the pressure of molten material and specifications altogether are to be considered in making the choice.
What are the benefits of using aluminum die casting tooling designs?
- Aluminum is a priority choice for many designers because it provides many benefits.
- Aluminum is malleable and hence can easily be transformed into any shape with less energy spent. This makes aluminum molds less costly.
- The low production runs are handled with aluminum molds. They are very effective in providing short term mold usage.
- The aluminum molds can create simple shapes in a very near to perfect manner. The molds created to deliver great results.
- The low strength level of aluminum causes lesser use of techniques like machining and treatments. The mold is created easily due to this property.
- Prototype manufacturing also makes use of aluminum molds as they align with the needs.
- When considering all of the properties of aluminum, it is the choice of many manufacturers. It provides all of the properties while keeping it affordable.
Can die casting die to develop some defects? How to prevent them?
Die Casting dies makes it easier to replicate metallic components and parts.
However, molds can sometimes develop defects that can be managed by using the right technology and implementing efficient manufacturing standards. The following factors must be kept in mind:
- A large production volume is required in the process. Lesser volume will make it costly and is not preferred by small-scale manufacturers.
- The tooling and the setting up of the molds are costly if used for a small batch.
- Drafting is required on the mold core and hence the casting. They are affected by different factors of the casting material.
- Fillets are also required at times. These include the process of smoothing angled surfaces in the mold. It reduces the risk of production errors but increases the cost.
- Porosity can rise in the mold due to many factors which can, in turn, affect the efficiency of the produced part. This can be managed by using efficient technology and quality standards.
Does aluminum die casting toolings impact the quality of metal parts being produced?
Aluminum die casting toolings are an important factor that affects the quality of the part produced. It directly impacts the end result of the product.
Gas porosity
Gas porosity is the entrapment of gases in the metal formed after die casting. It can occur due to defects in the mold such as:
- Poor venting of mold
- Moisture in the mold
- Gas permeability in the mold
Cuts and washes
Cuts appear on the metal when the molten metal erodes the mold. This can occur due to the following reasons:
- Lower mold strength
- Faulty design of the gates in mold
- Low endurance of the mold
Fusion
Fusion occurs when the particles of mold get mixed with the molten metal. This happens due to defects in the mold. The mold has lower refractoriness that causes it to melt with the molten metal and get mixed in it.
Run out
The molten metal runs out of the mold. This happens because of a faulty mold. A faulty metal part is formed due to this.
How to produce high-quality aluminum die casting tooling design?
To produce a high-quality aluminum die casting tooling design, a number of specifications are kept in mind. While designing the mold, a number of factors are considered.
Improving the design of the mold can improve the end results.
Draft
Draft is required to perform precise ejecting of casting from the mold. It is the degree to which the gap between the mold wall and casted part can be reduced. A good draft gives quality mold design.
Fillets
Fillets reduce the sharp edges of the casting part. The sharp edges directly affect the quality of the product hence fillets are placed in the mold to increase the quality.
Parting line
Parting line keeps the molten metal from running to spaces it is not supposed to run to. A precise parting line is what makes the mold design better.
Bosses
These are the knobs in the process of die casting. They help with the mounting of molten metal in the mold. Wall thickness is improved using bosses.
Ribs
This improves the material strength of the casted part if it doesn’t have the thickness required in the product.
Why is it important to get the draft angle right during the aluminum die casting tooling-making process?
Draft angle is the angle at which the ejector ejects the casted part. The accuracy of draft angle is what makes it feasible for the ejector. The draft angle depends on the metal being used for the casting and the thickness of the created part walls.
If the draft is not designed carefully, problems like vacuum and friction can arise. This can affect the casted part or sometimes the mold itself. The surface of the part is dragged with the walls of the mold causing major flaws in the surface of the part. Scratches and gouges appear on the part. The texture of the part is ruined due to this. Draft angle ensures the smooth ejection of casted part.
This is how draft angle works:
How is a prototype mold designed?
A prototype mold or rapid tooling is designed to produce a small series of casted parts. It can be created using additive and subtractive methods. Some of the techniques used in the process are:
3D printing
It is an additive process which creates a 3-dimensional object using Computer Aided Design (CAD) techniques. Material is added layer by layer in order to form one object that is 3 dimensional. The whole process is first examined in the computers and then carried out. It has a very little to no room for error.
Selective Laser Sintering (SLS)
This process uses a laser beam to produce a compact product out of powdered material. The laser targets a design in the space and keeps adding the particles. The material is bound together and a compact product is formed.
What is the mold flow analysis for aluminum die casting tooling and why is it important?
Mold flow analysis is done by creating a simulation of the molten metal flowing into the mold. This is done using various software. The complete process of molten metal is built to check for any limitations that the process might have.
The flow of the metal into the mold can affect the properties of casted metal. Therefore, to avoid any inconvenience during the process, a mold flow analysis is quite helpful.
Color mapping shows the properties that would reflect in the metal casting to be produced. The process is a graph of the object to show that the product will have optimal properties after production. The defects are found beforehand. This process is beneficial for the following reasons:
- Discover defects in design geometry
- Prevent expensive tooling errors and rework
- Enhance manufacturability
- Reduce time to market
- Boost efficiency and quality
Can the best tooling designs be achieved using flow analysis and computer simulations?
The flow analysis is used in order to achieve best tooling designs. It predicts the filling of molten metal in the mold. The mold analysis is helpful in achieve the following:
Product Geometry
If the geometry of the casting to be achieved is complex, computer simulation causes better predictions. For a simple geometry, computer simulation might not be needed for the prediction but when it comes to complex geometries, the product to be formed is easily predicted through this.
Tolerance requirements
Tolerance requirements are to be kept in mind when producing a casting. The computer simulation is an answer before the production. It predicts the properties of the casting and hence if the requirements are not getting fulfilled, changes are made.
Unusual materials
If any unusual materials are found in the mold or the path, it is captured before production.
If all of the afore-mentioned observations are made before the production, a high-quality product is bound to be achieved.
How to ensure the production of high precision aluminum die casting toolings ? Do CNC machines help?
Aluminum die casting toolings have been created with conventional methods. CNC machining is an advanced and feasible method to produce molds with high precision. Different techniques and CNC machinery are used for the production of die casting toolings.
The cycle times of the CNC machining are faster than the conventional methods. This results in the rapid production of the molds. The process even tests and fits the molding parts and no mold tooling is required later. CNC machining produces high-quality parts without any delays.
CNC machining even eliminates the limitations on the sizes. Since the inspection is carried out by itself in CNC machining, the part produced is ready to use. No finishing or tooling is further required.
Why should poorly manufactured aluminum die casting toolings be discarded before use?
The poorly manufactured aluminum die casting toolings need to be discarded due to the following reasons:
- Variations in cooling of the mold
- Entrapment of air while manufacturing
- Excessive temperature of the material
- Pressure applied on the mold
- Mold cooling down quickly
- Non uniform temperatures
- Collisions of the mold material
All of these reasons make up for a faulty piece. The fault is tried to be machined and treated in order to get a working piece. But if the fault is not diminished, the mold is to be discarded. If the defective piece is still used, it can cause defects in the casted parts.
The casted part is seriously affected by the mold. Almost all of the properties of the casted part are because of the mold. It defines the casting. The faulty pieces would have to be discarded if the mold is not checked in the first place. This can cause larger damages than simply discarding one defective mold piece before beginning large-scale production.
What kinds of top tooling design techniques and machining are employed by Sunrise Metals?
As a professional aluminum die casting tooling manufacturer in China, Sunrise metals makes use of the best machines for the production of tools. The latest techniques are employed for large-scale, high-precision manufacturing to ensure that international quality standards are met.
DMU monoBLOCK 5-axis CNC Machine
The DMU monoBLOCK 5-axis CNC Machine creates tools with efficiency. It is unique for its following properties
- The machine has large doors that gives the work area unique access
- Extensive cooling measures and multi-sensor compensation
- Several table solutions up to milling and turning
The process is automated with the use of this machine. It can work with project specific automation processes.
Coordinate Measuring Machine
This machine measures any object with sensing parts of the object. Sunrise Metal uses this machine to achieve precision in the measurements of the tools. It can measure the parts that are unreachable. A 3-axis system is employed in the machine. The machine moves in all directions for the measurement.
High Precision CNC machine
The High precision CNC machines are deployed in order to move towards complete automation of the manufacturing process. The tools are achieved with greater quality at Sunrise Metals.
How does Sunrise Metal implement cost-optimized tool manufacturing?
Sunrise Metals tooling provide the manufacturing tools as per the client’s requirement. The tools are cost-optimized and are easy to use. The features of the product are modified and the final product is improved. This also ensures top-quality of the mold. An early evaluation of the tooling saves time and the high-quality decreases cost for our customers.
At Sunrise Metals, the customer is not going to get trapped into paying for something he doesn’t want to pay for. Over-dimensional molds or the extra detailed molds that make up for higher costs are not what the customer is going to pay for. The customer only has to buy what he needs.
Which new systems and technologies can be used to optimize cost and efficiency in the tooling making process?
Many new technologies and techniques have optimized the process of mold making. They are employed to produce efficient molds that are cost effective.
CAD center, CNC machining centers, lathes and milling machines and spark erosion machines are used in order to achieve all of that. These processes have produced advancement in the industry and are the new ways of getting high quality results.
High-tech equipment is now being introduced to carry out these processes and can currently be seen in use by advanced manufacturers.