Sunrise General Aluminum Casting Components
As a distinguished manufacturer in the aluminum die casting field, Sunrise offers a premium-quality range of aluminum die casting parts for various industries.
We are engaged in developing components to be used in both small and large scale industries. It can be used in Power Tools, Consumer Electronics, Flow Control System, Ultrasonic Scanner,Textile, as well as many other general applications.
General die casting products have extremely lightweight design, while at the same time the ability to withstand high pressures, temperatures, and extreme weather conditions.
Sunrise General Aluminum Die Casting Manufacturing Capability
At Sunrise, we ensure high-speed production of a wide variety of die cast aluminum enclosures available in different sizes, shapes, and configurations. We offer visually appealing designs and parts with a long serving life to suit each industry’s needs. The production process of die casting enclosures is executed utilizing cutting-edge technology and high-grade aluminum material. The procedure is strictly monitored by vigilant and expert quality controllers to ensure that all products’s dimensions are accurate and stable. We manufacture enclosures with full compliance in the set international standards.
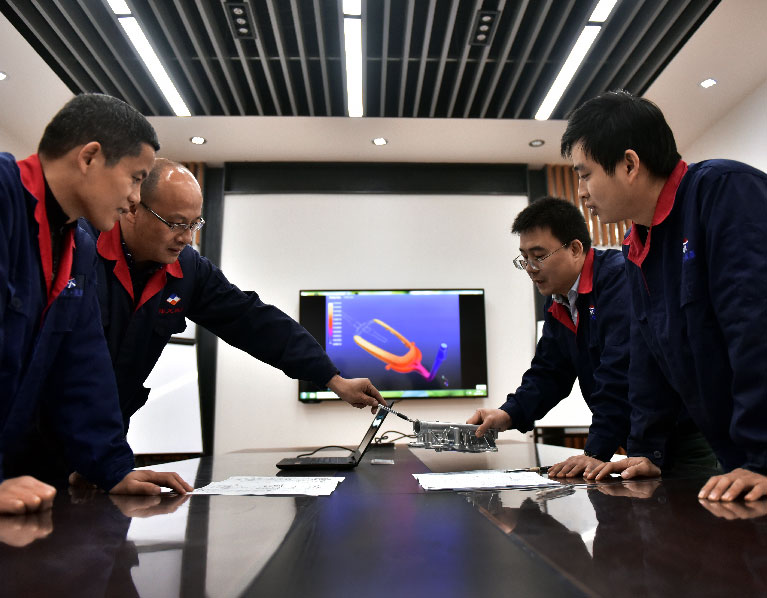
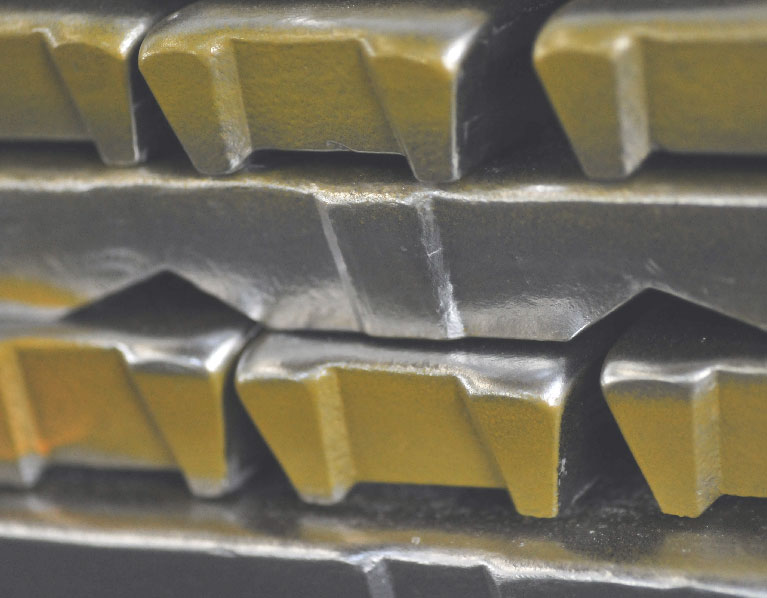
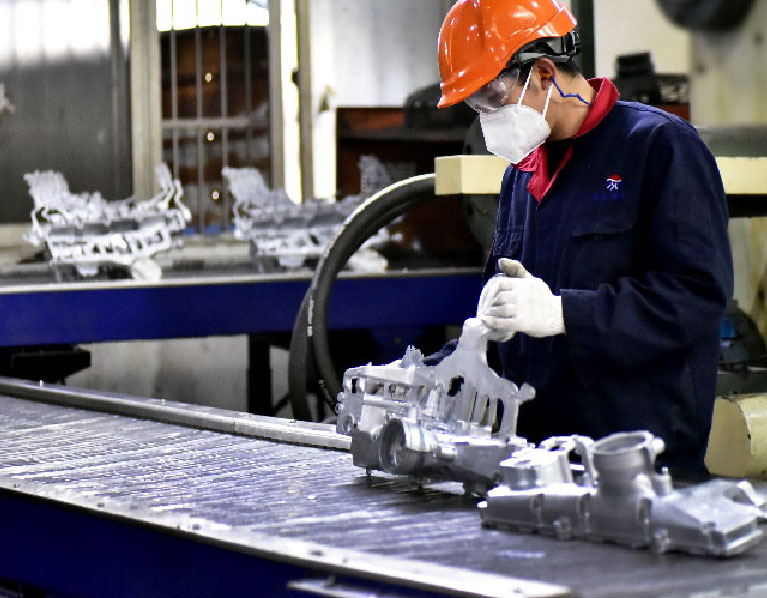
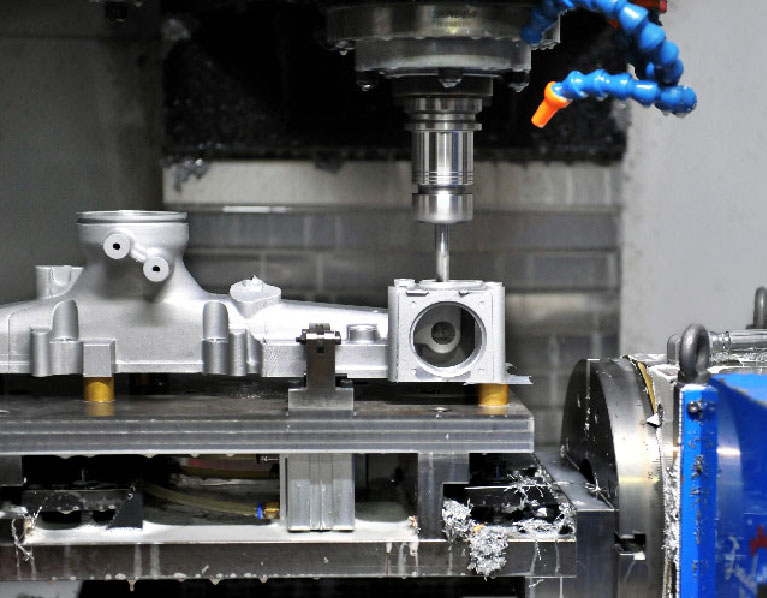
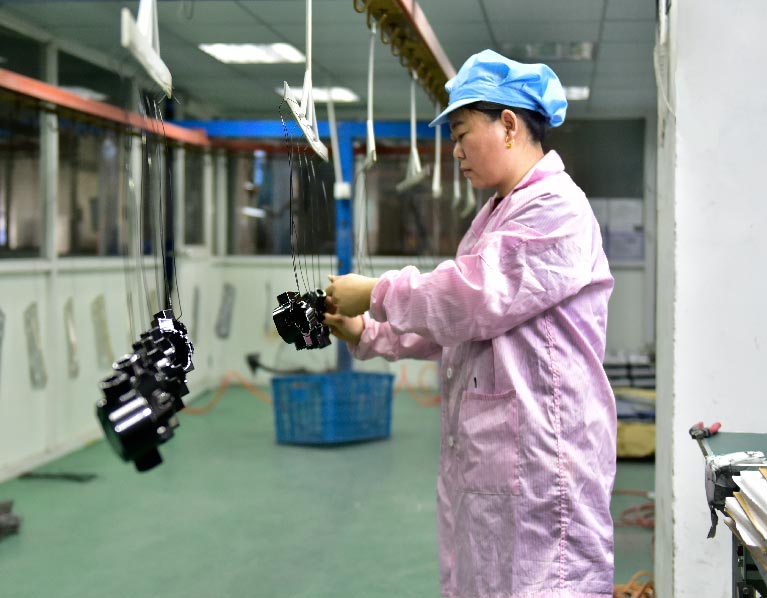
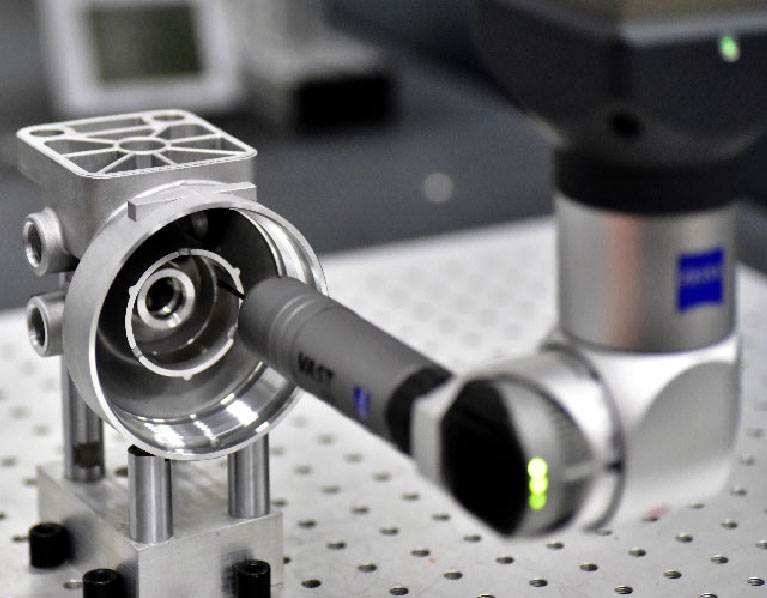
Advanced Equipment For Aluminum Casting Components
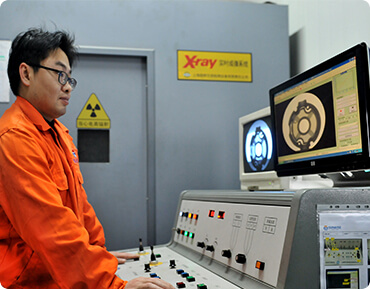
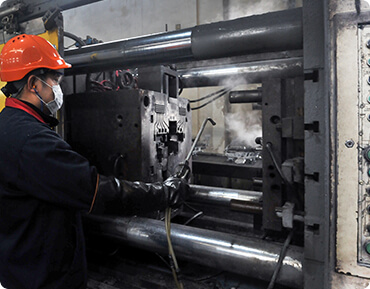
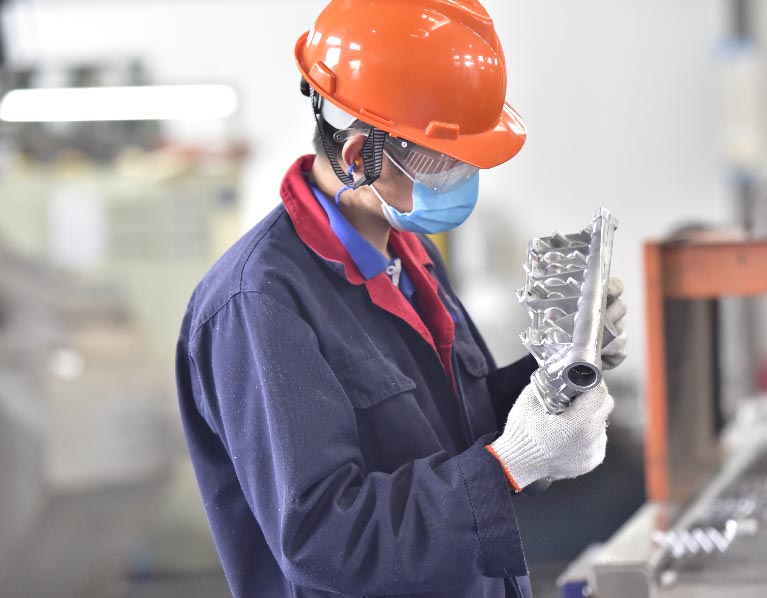
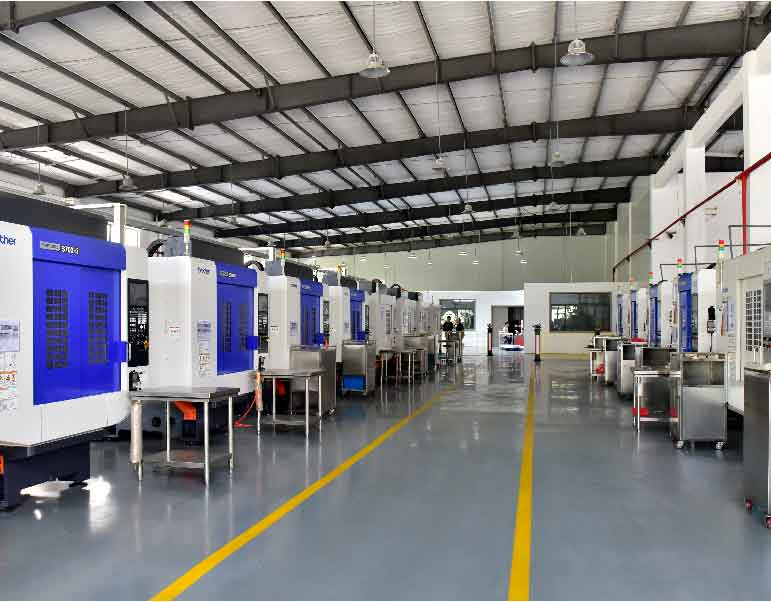
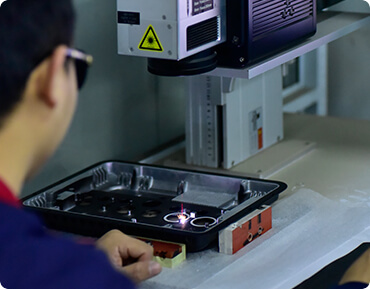
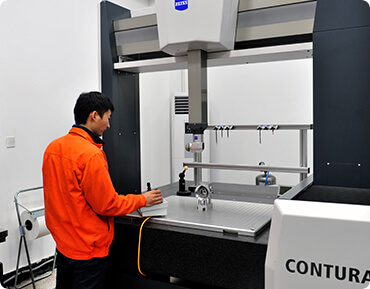
Recent General Die Casting Projects
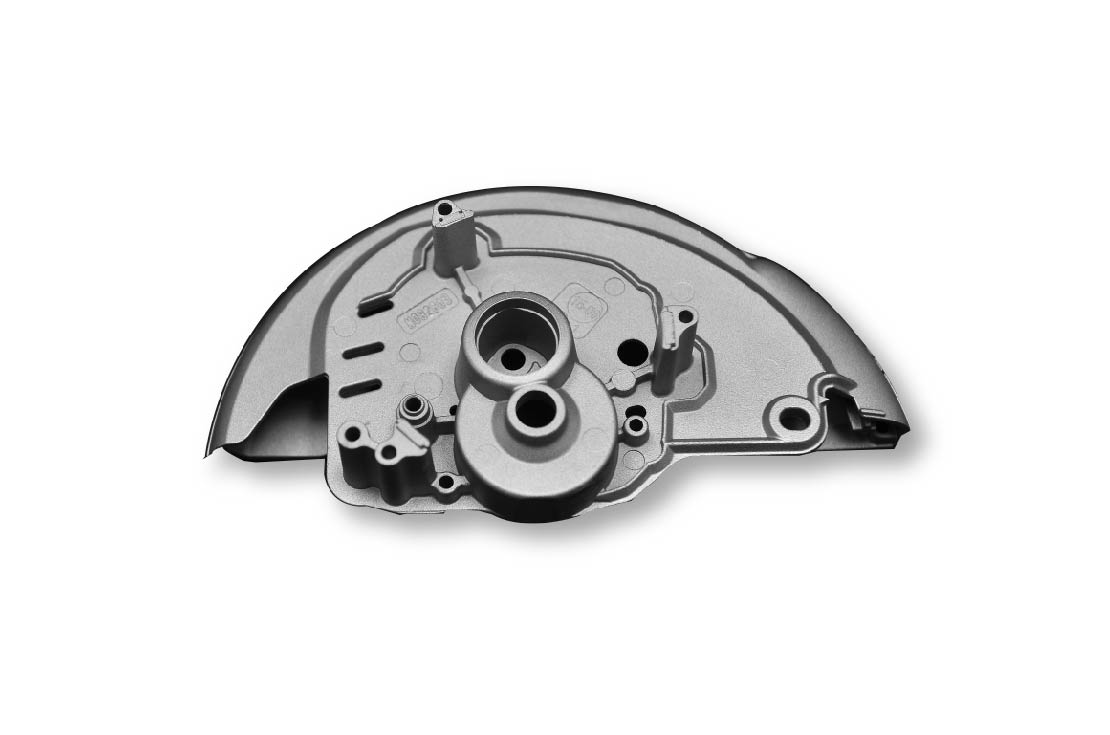
Part Name: POWER TOOL HOUSTING
Material: ADC12
Size: 300x150x80mm
Weight: 450g
Machine Tonnage: 400T
Surface Finish: Powder Coating
Production Process: Die Casting–Trimming–Deburring–Shot Blasting
–CNC Machining–Chromating–Coating–Printing–Screening–Packaging
Applied Industry: POWER TOOL
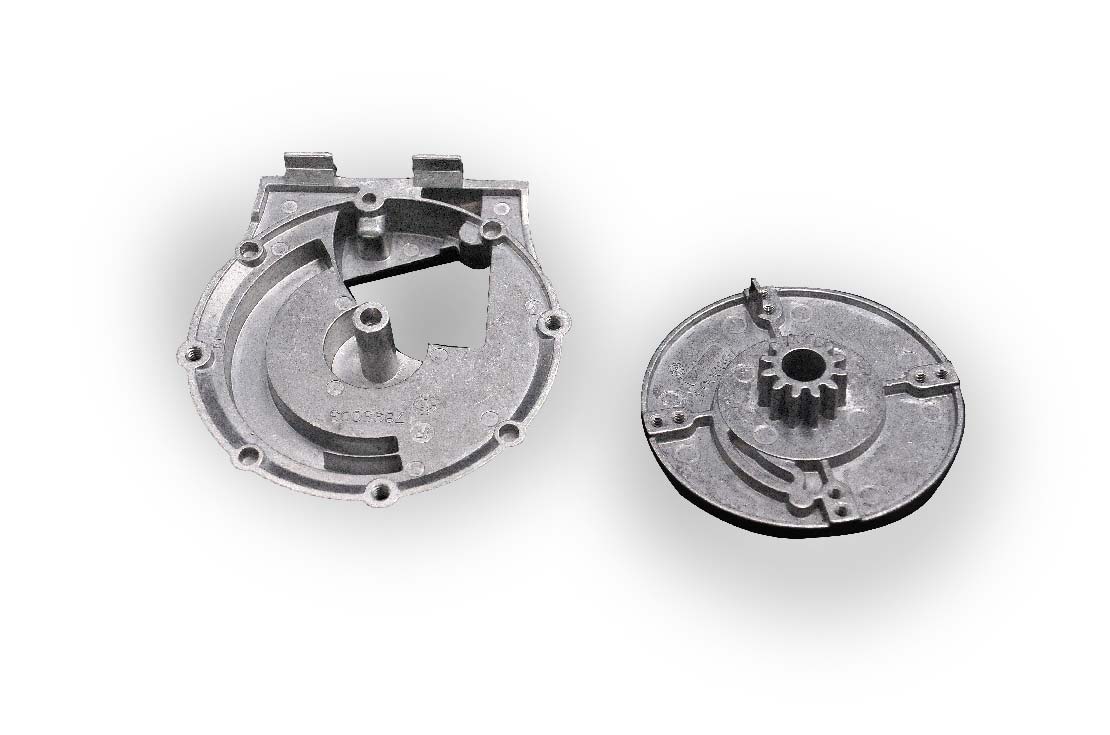
Part Name: GEAR VALVE
Material: ADC12
Size: 140x133x45mm
Weight: 230g
Machine Tonnage: 160T
Surface Finish: Powder Coating
Production Process: Die Casting–Trimming–Deburring–Shot Blasting
–CNC Machining–Chromating–Coating–Printing–Screening–Packaging
Applied Industry: CRUISE
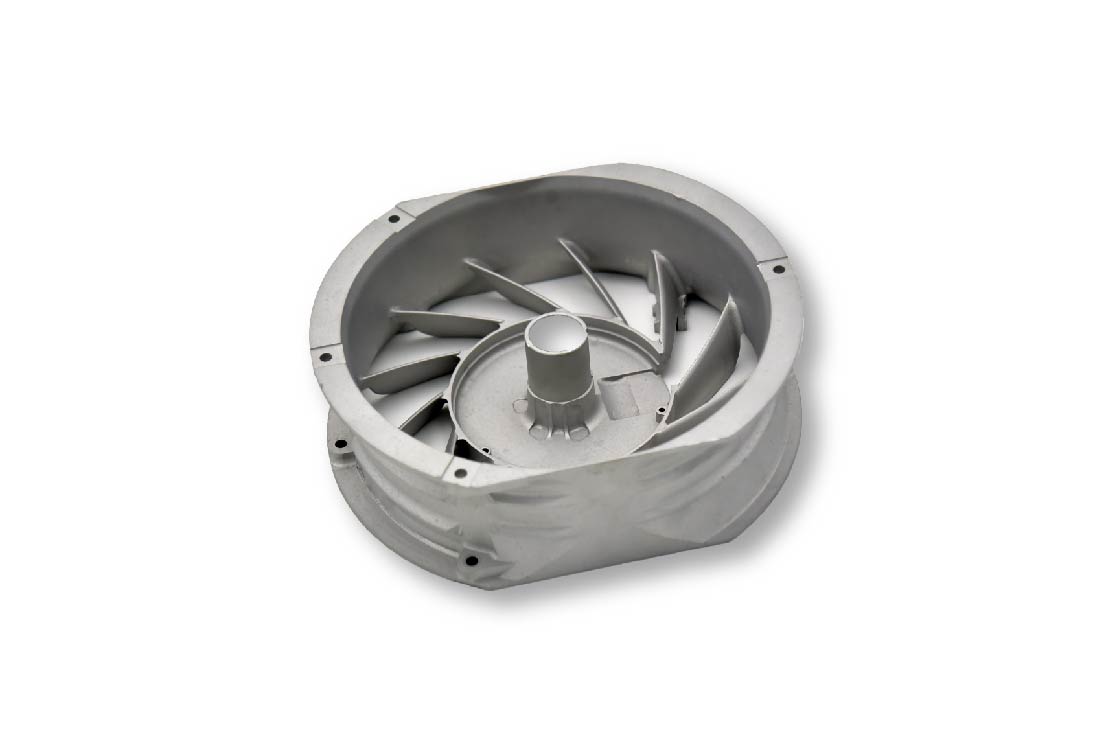
Part Name: INDUSTRIAL FAN
Material: ADC12
Size: 100x95x40mm
Weight: 220g
Machine Tonnage: 160T
Surface Finish: Chromating
Production Process: Die Casting–Trimming–Deburring
–CNC Machining–Chromating–Screening–Packaging
Applied Industry: GENERAL INDUSTRY
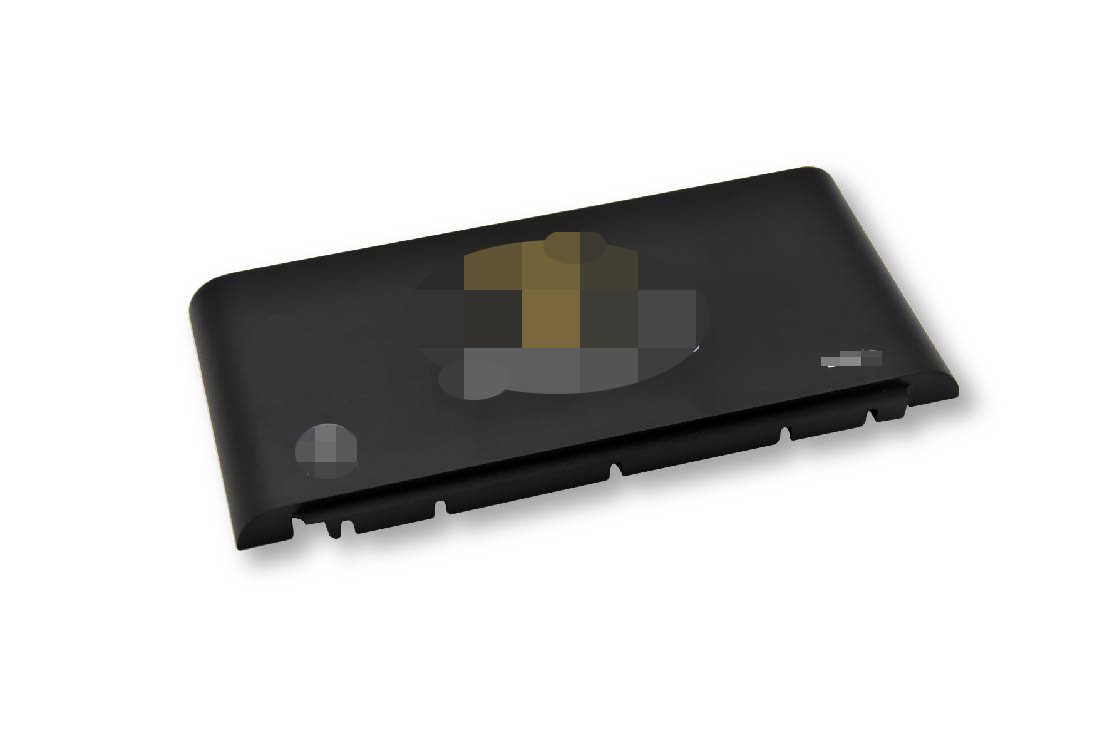
Part Name: COFFEE SIDE PLATE
Material: ADC12
Size: 270*134*18mm
Weight:660g
Machine Tonnage: 280T
Surface Finish: Coating
Production Process: Die Casting–Trimming–Deburring
–CNC Machining–Chromating–Coating–Printing–Screening–Packaging
Applied Industry: COFFEE MACHINE
GENERAL DIE CASTING:
THE COMPLETE FAQ GUIDE
A die casting part for general use can include a wide range of castings for use by top industries, such as Flow Control System, Ultrasonic Scanner,Textile, etc. These have excellent mechanical properties and good structure to suit all kinds of needs.
Sunrise employs manufacturing systems that are streamlined according to international quality standards to produce general die casting components at a large scale.
- What is a general die casting part?
- What are the main general die casting alloys?
- How are general die casting products made?
- What are the advantages of using general die casting parts?
- What are the main characteristics of a general die casting product?
- How to ensure the best design for general die casting parts?
- How durable and reliable are general die casting components?
- Which materials are used for making molds for general die casting parts?
- What kind of surface treatments are available for general die casting parts at Sunrise?
- What costs need to be considered when producing general die casting products?
- What products does Sunrise make with general die casting techniques?
- How does Sunrise ensure quality and precision in its supply of general die casting products?
- What are the rules for creating good designs for general die castings?
What is a general die casting part?
For general use, aluminum die casting parts are in demand for large series production. As a non-ferrous material, aluminum offers a wide range of options for general die casting components. These are produced using high pressure techniques, achieving high quality castings.
These castings are strong and durable, and produce accurate and stable general die casting parts. This process is more suitable for small parts with low thickness and intricate design.
Streamlined manufacturing systems and high-tech machinery allow the supply of the immensely popular aluminum general die cast parts.
What are the main general die casting alloys?
General die casting parts make use of different alloys of aluminum in their production. Following are the most widely and commonly used materials in the production of die cast alloys.
A380
A 380 is a widely used aluminum alloy due to its flexibility. It provides significant benefits in terms of mechanical and thermal properties. A380 shows resistance to cracking at higher temperatures and retains dimensional stability. This alloy is used in almost every industry that employs die cast products.
ADC12
ADC 12 or A383 is an aluminum alloy used in die casted products. It provides improved properties for filling of the mold and is resistant to cracking at high temperatures. Due to its conductivity, it is mostly used in the production of general die casting parts.
How are general die casting products made?
General die casting products are made using general die casting techniques like high pressure die casting. Molten metal is poured into the mold and is allowed to set in the mold. The set part is then ejected using ejectors in the die. Finishing of the part is done to achieve better properties.
Cold chamber and hot chamber methods are the two most popular techniques used for the production of general die casted components.
Hot-chamber die casting processes heat up metal inside the casting machine. On the other hand, cold-chamber casting involves the use of a separate furnace to heat up the metal.
Since aluminum has a high melting point, the most preferred method for producing versatile industry products is the cold-chamber die casting process.
Zinc and aluminum are the main materials used for general die casting parts. Their alloys are used in the production depending on their properties and the product required. The properties required in the manufactured part decide which metal alloy is to be used in the manufacturing of general die casting parts.
Other than zinc and aluminum, metals like magnesium are also used for the same parts. Copper, lead and tin based alloys are used in the production of general die cast parts. However, aluminum is the best choice in making high-strength and economical designs for large scale manufacturing.
What are the advantages of using general die casting parts?
General die casting parts are necessary components in big setups and are present in our daily life. They are present in our homes from our doorknobs to industrial level products such as automotive casting engine parts.
General die casting parts have the following features:
- Durable as compared to other types of parts.
- Adding stability to the setting.
- Efficient dimensional properties.
- High precision for complex industrial components.
- Good mechanical properties.
- Economical when produced at large-scale.
- Fine structure to give precision to the setting they are employed in.
- High accuracy attained due to the lightweight properties of aluminum.
What are the main characteristics of a general die casting product?
Die casting products are being used in home appliances, automotives, telecommunication and other industrial components. This is because of the properties that die casting parts provide and the benefits of the die casting process. In comparison, other casting techniques are not as cost-effective or quick.
Die casting products have the following unique characteristics:
Intricate design
The products show intricate designs that make them easy to use. Great creative designs make the object unique and remarkable.
Treatment friendly
The general die casting objects used by manufacturers are treatment friendly. Different treatments are applied on these products to create an optimal result. For example, the finishing of these products is achieved through machining.
Strength and durability
General die cast parts are corrosion resistant and highly conductive, along with having a good strength-to-weight ratio.
How to ensure the best design for general die casting parts?
To ensure the best design for general die casting parts, different factors are considered.
Undercut
The mold ejects the casted part through moving die. To ensure best design, we make sure there are no undercuts in the opening area of the dies. Undercuts affect the design of the product severely and change the properties of the casted product as well. To avoid these undercuts, slide cores are introduced to the opening of dies. This ensures smooth ejection of the part and design is not hurt.
Draft angle
The angle at which the casted part is ejected from the mold also affects the design of the general die cast part. Proper drafts are added to the die cast part in order to ensure smooth ejection of the part and hence improving cycle time.
How durable and reliable are general die casting components?
Manufactured through die casting, general die casting components are durable and reliable. They show this durability and reliability because of the alloy they are manufactured from. The measure of this strength depends on following factors:
- The structural properties of die cast parts dictate the properties of final industrial product. If the material they’re casted from is durable, the manufactured product will be durable and reliable.
- The flowing of molten metal into the mold and then its setting into the mold also define the properties of general die cast products. The solidification of the metal is also an important factor in preparing high-quality industrial parts.
- Aluminum general die cast parts can within high temperatures in comparison to other non-ferrous materials like zinc and magnesium.
- They have high conductivity, with a good stiffness and strength-to-weight ratio.
- General diecast components are resistant to corrosion and are therefore reliable for use in outdoor settings as well as rough conditions. They can even be used under water.
In short, if the process of die casting is carried out with great observation and consideration, the product is highly reliable and durable.
Which materials are used for making molds for general die casting parts?
The components used in the making of mold depend on the metal being casted. In general, the following materials are used in the process:
- Aluminum is used to create molds for the production of general die cast parts. This is because they’re malleable and ductile.
- Silicone rubber molds are also used to produce general die cast parts. They can withstand higher temperatures and are used to cast zinc alloys.
- Hardened steel molds are sometimes used in production of these parts. These molds are durable and provide efficient die cast products.
What kind of surface treatments are available for general die casting parts at Sunrise?
General die casting parts are treated at Sunrise using chromating, anodizing, tumbling, powder coating, liquid painting, and platin.
The following treatments are also done at Sunrise:
Bead Blasting
Beads are applied at the surface of the general die cast part. This removes any deposits against the die cast part without damaging its surface. This method provides a smooth finish to the casted part.
Powder Coating
Sunrise powder coats the general die cast part to increase its life. Powder is sprayed on the casted part and then melted in an oven or under ultraviolet rays contact to fuse the particles into the product leaving a coating on it. This provides security to the product.
Anodizing
This is an electrochemical process that provides an anodic oxide finish to a metal and converts it into a corrosion-resistant and visually appealing one. It also makes the final product more durable. It is done by immersing the aluminum part into a bath of acid electrolyte. Electric current passes through the medium to provide this surface finish.
What costs need to be considered when producing general die casting products?
Cost efficiency is a major requirement in any industrial product in combination with other requirements. The factors that are considered for the estimation of die cast parts are as follows:
Material
The material being used for the production of general die cast parts is a major influence on the cost of the process. Good quality and cost-efficient metal alloys are used for these products.
Production quantity
The general die cast part is cost efficient if it is being produced in large quantities. Production of small quantity products is a set back as it is a waste of resources over very little income. The quantity of production is also a factor that changes the cost of production.
Finishing
If the general die cast part needs finishing or surface treatments after production, it also increases the cost of production.
What products does Sunrise make with general die casting techniques?
Products like die casted top covers, valves, brackets, plates and few others are created at Sunrise Metals using general die casting techniques. These parts are created in a large quantity at Sunrise Metals with expert supervision.
We use updated die casting methods for the production of such parts. Our automated machineries work to produce efficient general die casting products.
How does Sunrise ensure quality and precision in its supply of general die casting products?
Sunrise Metals uses the up to dated techniques to ensure quality and precision in the production of general die casting products.
Flow Control System
The molten metal that flows to the mold is poured using a flow control system. This facilitates the entire process using sensors to meet the temperatures required and control the flow rate of the molten metal. Using this technique, the production of the metal parts is made accurate.
Mold Flow Analysis
Sunrise Metals uses simulation software to know the precise flow of molten metal before the starting of the procedure. It shows the elevation of material to provide smooth processing of die casting procedure.
What are the rules for creating good designs for general die castings?
Techniques that ensure good designs for general die casting parts to abide by strict standards, including but not limited to the following rules:
- There should be no undercuts.
- The walls of the die casted part should have a uniform thickness.
- Parts should have curved surfaces in order to avoid any faults due to sudden changes in direction of flow.
- Bosses should be added to the general die parts in order to avoid additional machining.
- Adequate draft angles and fillets should be added.
- There should be openings for any additions post-production.
- Proper identification of the general die cast part should be observed.