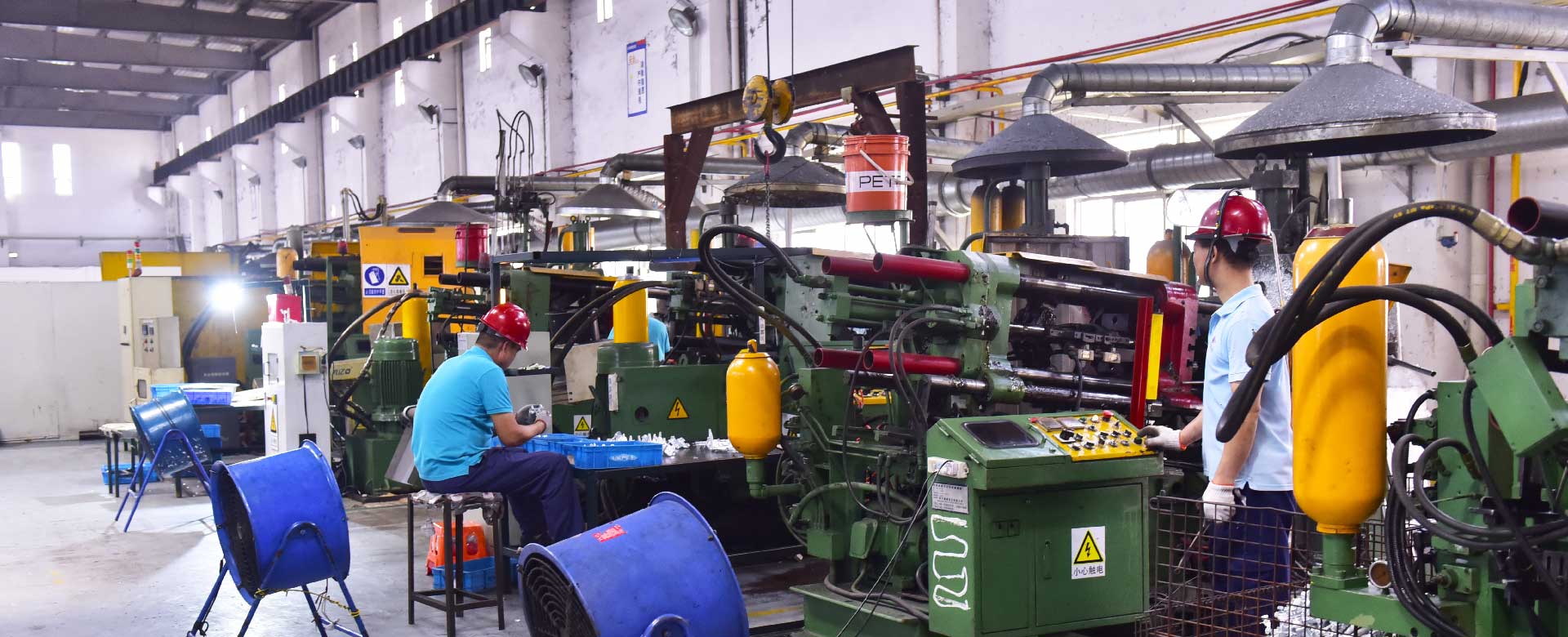
China’s Finest Zinc Die Casting Manufacturer
If you need a one-stop solution for all your industrial needs, then Sunrise Metal is the answer. Be it value addition, quick turnaround time, or reliability, our team will make sure you get exactly what you require.
Zinc die casting manufacturer par excellence in China, Sunrise Metal is a name that is trusted at home and abroad. We provide top-notch 3D printing and prototyping services while also dealing with different raw materials for production.
Our talented personnel will follow your needs to the letter and prepare prototypes that are fully customized to your zinc die casting demands. Moreover, you will receive your order in record time, with the finished product exactly in line with your requirements.
Zinc Die Casting Parts Manufacturing Experience From Various Industries All Over the World
Expertly Taking Care of Your Zinc Die Casting Needs
At Sunrise Metal, there is no compromise on quality. This is why we utilize the most advanced design and manufacturing technologies like low-cost tooling, CNC machining, 3D design, CAD (Computer-Aided Design) and simulation software, etc. They help us produce only the finest quality zinc die casting components.
Our products are high-strength, durable, and last longer than those of any other zinc die casting company in China. The effective tooling process (involving the finest EDM and CNC machining equipment) ensures that the established quality standards are met one hundred percent of the time.
The quality assurance personnel at Sunrise Metal ensure superior design and flawless production so that you can get the best value for your money. As an ISO 9001-certified company, we take our quality standards very seriously.
Zinc Die Casting Production Capabilities At Sunrise Metal Exceed Your Expectations
Get All Your Zinc Die Casting Products At Affordable Cost
Of all alloys, zinc is the most fluid. At Sunrise Metal, we make use of these properties to make lighter and thinner as well as more intricate zinc die casting parts. The result is that no secondary operations are needed and the process requires less material. This leads to significant cost and energy savings.
Zinc die casting company that promises consistency, precision, and excellence, always.
- High Premium Quality Instruments
No. | Name | Brand | Q’ty |
1 | CMM | Carl Zessis | 1 |
2 | CMM | SanYou | 1 |
3 | Spectrometer | China | 1 |
4 | Microscope | China | 1 |
5 | Projector | China | 2 |
6 | X-ray Detector | SANDT | 1 |
7 | Cleanliness Test Equipment | China | 1 |
8 | Leakage Test Equipment | China | 2 |
9 | Salt Spray Testing Equipment | China | 1 |
10 | Pneumatic Measuring Instrument | China | 2 |
11 | Hardness Testing Machine | China | 1 |
12 | Color Meter Machine | China | 1 |
13 | Thickness Testing Machine | China | 1 |
14 | Electronic Balance | China | 1 |
15 | Density Balance | China | 1 |
Book an Information Session with Sunrise Metal TODAY!
Contact us now to get a better idea of what you stand to gain by having Sunrise Metal as your zinc die casting supplier. Get in touch for more information on our tooling systems and strategies, casting technologies in use, cost-cutting methods employed, zinc die-cast parts applications, high-precision designing techniques, fast-track order completion.
We will put your next project on the road to success right away!
ZINC DIE CASTING MANUFACTURER: THE ULTIMATE FAQ GUIDE
The goal of this guide is to provide you with answers to all the questions you have about the zinc die casting manufacturer. It will guide you to make the best decision in choosing a reliable manufacturer for the success of your business.
- What is Zinc Die Casting?
- How is the Zinc Die Casting made?
- What service does Zinc Die Casting Manufacturer offer?
- What are the Characteristics of Zinc Die Casting Alloys?
- What are the Applications of Zinc Die Casting?
- What is the importance of Zinc Die Casting in the Auto Industry?
- What Advantages Zinc Die Casting Offer?
- What are the Surface Finishes for Zinc Die-Casted Parts?
- What are the Zinc Die Casting Services for Customized Industrial Parts?
- What is the difference between Zinc Die Casting vs. Aluminum Die Casting machines?
- What is the difference between Die Cast Zinc vs. Die Cast Aluminum?
- Is Zinc Die Casting better than Magnesium Die Casting?
- What are the Benefits of Die Casting Zinc Alloys?
- Why is Zinc Die Casting suitable for Electroplating Process?
- What are the Process Steps of Zinc Plating?
- How Environmentally Compatible is Zinc Die Casting?
- How to Improve Zinc Die Casting Process Control?
- How Sunrise Metal Monitors Zinc Die Casting Product Quality?
- What are the primary materials used by the Zinc Die Casting Manufacturer?
- Does Sunrise Metal provide one-stop Zinc Die Casting Manufacturing?
- Does Sunrise Metal provide DFM for Zinc Die Casting Product Design?
- How does Sunrise Metal produce Precision Zinc Die Castings?
- What is Special about the Zinc Die-Casted Parts from the Sunrise Metal Production?
What is Zinc Die Casting?
It is a metal casting process described by forcing hot liquid zinc into the mold cavity. The mold cavity is made using a pair of tool steel molds machined to the required parts’ close net shape.
Its process permits items to be made with a severe extent of accuracy and repeatability. This process can output fine details, for example, finished surfaces, without requiring further processing.
This process is very recognized on account of the shapes & molds. These molds can be made just as the volume that can be repeated with excellent outcomes.
It Zinc Die Casting is considered one of the most flexible high-manufacturing techniques. Furthermore, it’s utilized for assembling reliable, precise, and complex-shaped parts.
How is the Zinc Die Casting made?
The process starts with the steel dies. These dies are completely capable of producing and manufacturing many die-castings in the most rapid way possible. That must be done in a pair of sections in-order-to allow the castings to be ejected successfully.
There are “dies” in this process, which works as containers that contain liquid zinc to shape it in parts required. These are shaped exactly as the output part required and commonly consist of two dies.
These dies are precisely inserted in the die casting machine. Furthermore, they are placed so that it’s one part is stationary (fixed), and the other is movable (injector).
In-order-to starts the process; a die-casting machine clamps together the mold halves pair.
Afterward, a hot molten zinc alloy solution is injected into the mold cavity and rapidly solidified. The movable mold half is opened, and the finalized and processed zinc casting is ejected out.
The zinc die-casting molds can be extremely simple or ultra-complex based on the product design requirements and specifications. Furthermore, it depends on moveable slides, cores, or complexity of the required die castings.
What service does Zinc Die Casting Manufacturer offer?
These services include part design, design for manufacturing (DFM), rapid prototyping, manufacturing, production, surface finishing, parts machining, and assembly.
However, having excellent skills that reach out, starting from one phase to the next, facilitate customers with efficient solutions. They are adopted by various industries and continually guaranteeing top-quality material, processes, manufacturing, and durability.
An analysis stage before mold design reduces the production limitations, decreases costs, reduces scraps, and increases overall quality.
What are the Characteristics of Zinc Die Casting Alloys?
Zinc’s high strength and hardness fit make it an ideal option to the machine and manufacture parts.
High strength and hardness. Here are the remarkable characteristics below.
- Exceptional electrical conductivity
- High-level of thermal conductivity
- Low-cost raw zinc
- Excellent dimensional accuracy and stability
- Good thin wall capability
- Ability to cold form, which eases joining
- High-level of surface finishing characteristics
- Exceptional corrosion resistance
- Complete recyclability
What are the Applications of Zinc Die Casting?
Zinc die casting is a surprisingly worthwhile part manufacturing process in modern industrial fields. The auto industry has the most uses of zinc die casting parts. Many applications can be zinc die-cast manufactured, including:
- Interior automotive parts
- Engine parts
- Auto under-the-roof components
- Power steering systems
- Brake parts
- Air-conditioning systems
- Fuel systems
- Complex net-shaped housings
- Electronic devices
Complex zinc parts design, with exact thin walls, offers some best electrical and shielding properties. The exclusive zinc die casting process provides parts for a broad scope of electronic devices.
As said already, the auto industry is the most broadly perceived utilization of Zinc die-casting. However, numerous industrial applications, including:
- Marine Electronics
- Medical & Health Care
- Telecommunication & Networking
- Aerospace Electronics
- Industrial & Commercial
- Smart Metering, LED Lighting
What is the importance of Zinc Die Casting in the Auto Industry?
Zinc is considered one of the most common and necessary die-casting materials in industrial gear and systems.
Using this metal and its alloys, it’s guaranteed to achieve a quality, adaptability, and malleability impossible to adopt with other metals.
Additionally, zinc always has proven an ideal choice to obtain incredible decorated parts., It’s ideal because these decorated parts contain demanding resistances that are hard to obtain and impossible to achieve at the highest point with various die-casting metals. Sometimes these alloys get emblazoning for gear-based and mechanical equipment and parts.
As previously described, the auto industry is the most generally perceived in die casting by using Zinc. Furthermore, its alloys can produce parts fit for showing up at high-level decoration quality, with demanding and meager resistances for shape morphology.
Hereunder you can discover various parts related to the auto industry that are possible to manufacture with zinc die casting:
- Fuel system components
- Weather control components
- Seat belt parts
- Air-conditioning systems
- Brake system parts
- Steering components
- Power systems
- Engine parts
- Mechanical and lighting parts
- Aesthetic parts
What Advantages Zinc Die Casting Offer?
The zinc die-casted part’s brilliant wear and bearing properties permit more superior product design flexibility and save manufacturing costs.
- Surface Finishing: The phase when selecting the most suitable surface finish is performed and applied to these parts. Hence, the coating durability of the finish can be enhanced and achieved with at most precision.
- Less material is required: Zinc’s excellent die-casting smoothness, quality, and solidness ensure thin-wall parts structure for diminished weight and material cost saving.
- Eliminate bearings & bushings: The bearing properties and remarkable wear properties of these alloys allow more important plan adaptability. As well as eliminate bushings and wear inputs for reducing the manufacturing costs
- Faster Production: Zinc die casting production is rapid, a lot quicker than magnesium.
- Reduced assembly operations: Reduce costly manual assembly activities that directly affect the operations and cost without affecting the client’s requirements.
- Choice of production: An array of die-casting processes is accessible to financially produce parts of different sizes, shapes, and functionality required by customers.
- Reduced machining operations: Machining is reduced to a minimum or eliminated because of zinc alloys’ primary net-shape die casting capacity.
- Extended tool life: The smoothness of the process and precision in die casting reduce effort and extend the life-span of tooling.
- Improved Castability: Due to the zinc’s fluidity, the parts can be thinner, more complex, and intricate. It also eliminates the need for secondary operations that are sometimes considered essential for aluminum alloys.
What are the Surface Finishes for Zinc Die-Casted Parts?
When abstract designs are joined with the Zinc die-casting process’s versatility, it extends the parts’ stylish appeal.
Zinc die castings are an unprecedented decision for dozens of functional and decorative parts and applications.
Most of the Zinc die-cast applications are not presented to corrosive environments. The part requirements provide us information about which surface-finish is to be applied, which sometimes means no surface-finish at all.
For applications where the environmental condition is forceful, an unparalleled range and transformation coatings, paint, and sublime electroplated metal finishes can be effectively applied to any chosen part surfaces.
Fantastic substrates help to get great yield finishes. Good mass vibratory finishing can be implemented to improve the ‘as cast’ surfaces. Uncommonly smooth finishes can be acquired preceding finishing by delicately polishing or chemical polishing.
Because of the high ease of zinc alloys, a precisely characterized surface can be added to the part.
Therefore, zinc die-castings can be made to seem as though strong gold, endured metal, treated steel, and even leather. Other outside highlights, for example, lettering and logos, can be ‘cast in.’
For the most significant effect and achievement, the engineers are encouraged to counsel the die caster at the beginning phase. It’s helpful to concede to the ideal method of producing an economical and aesthetically attractive final product.
What are the Zinc Die Casting Services for Customized Industrial Parts?
These services deliver a broad scope of industry-based parts and unique custom products related to different applications. Zinc offers a handful of advantages and services when it comes to custom die casting industrial parts.
The overall precision die-casting customers can achieve with zinc is impossible with any other method, process, or alloy.
The mechanical properties of custom zinc die-casted parts at typical temperatures are better than dim iron castings and Aluminum. Furthermore, it’s better, especially in the sense of durability and quality. They are a lot more grounded, more challenging, and stable as compared to infusion formed plastics. The minimum expense, high-precision, and improved properties have made these parts an ideal swap for Aluminum, magnesium, iron, and copper.
What is the difference between Zinc Die Casting vs. Aluminum Die Casting machines?
Their logical mechanism and machining process is different because both use different machines. Zinc can be processed through Hot-chamber die-casting machines, Aluminum, and zinc alloys with a large composition of Aluminum, magnesium, and copper can be processed through Cold-chamber die-casting machines.
The difference between these two machines is that cold-chamber die casting involves heating the metal alloy in a separate furnace. Afterward, transfer the newly molten metal into the casting machine.
In contrast, hot-chamber die casting heats metal inside the casting machine. Once the molten metal is poured into the cavity of the mold, it’s cooled and hardened. Afterward, it’s removed from the mold, and these processes are the same within these two machining mechanisms.
What is the difference between Die Cast Zinc vs. Die Cast Aluminum?
- One of the main differences between zinc and Aluminum die-casting is zinc’s low melting temperature and its requirement for lower pressure during the die-casting process. Thus, based on the above observations, zinc has proven to be a more castable one.
- Having a low melting temperature benefits zinc die-casted parts because they can last longer because of their low-temperature process. Since dies are costly, utilizing them for a more extended time is a practical way to deal with high-volume production.
- Additionally, zinc alloys are completely castable with high-pressure die casting. Because it has become more affordable than cold chamber die-casting. By utilizing high-pressure die casting, the production and manufacturing process can be enhanced and faster.
- Aluminum alloys are typical to die-cast with cold chamber die casting. However, it is proven to be less beneficial than hot chamber die casting using zinc alloys.
- Zinc is more reasonable for precisely detailed die castings. It’s useful for die-castings next to no computer-aided machining or surface finishing tasks required after a complete part production phase.
- During the die casting process, low weight and low dissolving point lessen the warm stun. Furthermore, these points help to give the die-casted part a smoother surface finish with at most precision.
- The machinability and formability of zinc alloys cost differently depending upon the application’s surface finishes and assembly activities.
- However, zinc is a non-sparking and industrial metal and free from any environmental risks. Zinc is the most suitable alloy for explosive environments and conditions.
- In general, zinc is the metal with the most precision and smaller draft angles with longer cored holes and even longer life-span parts.
- It also offers superior machinability, exceptional tensile strength, extended formability, lower industrial, and die casting costs.
- Zinc offers a fair amount of pressure tightness, more surface finishing options, and choices.
- Zinc alloys are non-sparking metals when compared to other different die casting alloys like Aluminum.
Is Zinc Die Casting better than Magnesium Die Casting?
Unlike magnesium die casting, which requires exceptional resistance against corrosion and surface finishing, zinc has natural resistance against corrosion. Furthermore, it has a fine surface right after its ejection from the die as a finalized zinc die-casted part. However, this finalized part requires a lot fewer secondary processes as compared to what magnesium parts required.
Magnesium has a low-level density, but magnesium and zinc alloys have in common that both can die-casted using high pressure die-casting. However, the mechanical and physical properties of zinc are superior to magnesium in many aspects.
When it comes to the cost, zinc die-casting customers require a minimum budget to die-cast require parts than customers prefer magnesium. Zinc is cheaper because of its lower processing costs and draft angles.
Better precision, stiffness, tensile strength, and resistance against corrosion makes it a superior die casting alloy than magnesium.
What are the Benefits of Die Casting Zinc Alloys?
It’s a unique and suitable die-casting technique in industrial versatility because of its high-precision production with low-tooling costs.
The industrial benefits it offers are the following:
- High-level of shape complexity and thinner walls
- Exceptionally high-level physical and mechanical properties with superior tensile strength and dimensional stability
- Offers the best RFI/EMI shielding properties and capabilities
- Longer life-span and parts that require minimum maintenance
- The vast majority of surface finishing options
However, it’s a crucial solution to high strength manufacturing of die-casted parts with at most precision, durability, and hardness.
Why is Zinc Die Casting suitable for Electroplating Process?
Electroplating is an excellent way to offer excellent defensive and decorative surface finishes to zinc die casting parts.
Furthermore, applying this sort of treatment on die-cast zinc parts have their difficulties. To conquer these issues, an exhaustive morphology and synthesis investigation of zinc die-casted parts as directed.
When dealing with metals inside any industry, the greatest danger is rust and its destructive impacts.
Corrosion cause interruptions and produce transportation, utilities, and framework inside the industry, so what can you do to battle it?
Electroplating allows to coat metals with a physical zinc layer to keep rust from arriving at the metal surface underneath. However, the zinc electroplating process is very complicated.
What are the Process Steps of Zinc Plating?
Cleaning the Substrate
The initial and most crucial step of zinc plating in which the surface of the parts cleaned adequately.
So that no external environmental substance can disturb the surface in-order-to achieve the highest quality plating.
Activation of the Substrate
To complete the pre-processes of the substance, the processed substance experiences a cycle named “activation.”
Activation means lowering the substance into various acid solutions to eliminate oxides and scales with precision.
Because there are chances that oxides and scales can frame on the part surface.
Preparation of the Plating Solution
An electroplating solution is required to perform the zinc electroplating process. This required plating bath comprises the ionic substance solution just as different chemicals help the electroplating process.
Zinc Electroplating
When starting the plating process, the substance can be processed through two different techniques: either barrel or rack plating.
The barrel plating process is most suitable for little parts. Furthermore, these parts are placed into a barrel where they got processed and given a unique and uniform finish.
However, in the case of rack plating, it is for more significant parts. However, the parts are processed by lowering them into a tank containing the electroplating bath.
Rinsing and Drying
After the final plating process, the zinc die casting parts are finished, the rinsing and drying process starts.
In this final step, the parts must be rinsed with water until the surface is entirely purified.
It’s important to purify the part’s surface from any extra coat and afterward dry completely.
How Environmentally Compatible is Zinc Die Casting?
Zinc die-casting at Sunrise Metal is, accordingly, subject to extraordinary natural environmental conditions.
Since operating environment requirements are critical to us, we place great incentive to reuse any deposits that emerge.
The significant strength-weight proportion of the parts and a generally low casting temperature greatly decrease the environment’s strain.
Thin-walled die-casting and life span of the parts can save material and process costs. It’s a cost-effective way to manufactures parts and makes zinc die-casting exceptionally asset effective and maintainable over the long run.
How to Improve Zinc Die Casting Process Control?
The first is decreasing temperature variances to keep up an ideal working temperature. The second is improving hardware maintenance and activity.
Temperature:
Understanding the impact of temperature on die-casting is a significant component in diminishing natural process material and material waste.
With next to zero change, a stable working temperature is expected to produce and manufacture sufficient zinc die-casted parts persistently.
By preheating the components would be required for the die-casting process to arrive at its ideal working temperature.
Furthermore, utilizing a die-warmer, fewer “shots” (when liquid metal is constrained into the die) also help achieve ideal temperature.
This, thus, would decrease the measure of scrap produced. Moreover, adding metal to the heater pot in the correct sums would decrease pot temperature changes, and temperature-initiated casting absconds.
Maintenance:
Appropriately kept up die-casting tools and machinery has less vacation. Furthermore, it permits the die-casting cycle to support its ideal working temperature.
Maintaining this temperature is important for a more drawn out time than when the hardware is closed down for fixes.
Upsetting the framework brings about delivering unacceptable and defective parts. These parts must be disposed of because of defects, for example, porosity, twisted studs, a virus shot, and other deformations.
Understanding the gear maintenance factors that impact part defects can assist administrators. This assistance occurs through changing machine settings and maintenance timetables to decrease defects, hardware downtime, and scrap volume.
How Sunrise Metal Monitors Zinc Die Casting Product Quality?
The product quality and design monitoring programming perform tests to build up production plans that guarantee zinc product quality. These tests comprise following the alloys utilization for a few days and taking examples from the die-casting for composition analysis.
After that, we require to change the die casting pot just with new raw material. Furthermore, we utilize a similar following and testing system to decide its organization.
Our engineers test the zinc alloys’ results to the pot against the outcomes from examining just new material. They test the results with the following data and through a programming plot.
This information ought to uncover the sum and nearly every segment exhausted in the blend to be renewed. We can build up a professional and safe production and manufacturing timing schedule that utilizes raw zinc with this information.
We can track the consistency of the parts produced in the Sunrise Metal die-casting facility by incorporating monitoring systems like a real-time shot monitoring system. Monitoring systems can reduce the scrap and are a much more affordable way to monitor and control your process.
What are the primary materials used by the Zinc Die Casting Manufacturer?
There are two superior and essential zinc die-casting alloy groups.
The first one and most superior is ZAMAK alloys, and afterward came the ZA alloys.
ZAMAK alloys are known for its 4% aluminum solution and give incredible zinc die castability with exceptional quality. The ZA alloys are known for their high aluminum solution and offer predominant strength. The regular or “ZAMAK” alloys are usually called based on their manufacturing and development numbers. Furthermore, these numbers go before the word alloy like Alloy 2, Alloy 3, Alloy 4, Alloy 5.
Alloy 3 and Alloy 5 both offer higher quality and beneficial bearing properties. And they are the most productive and useful alloys of them all. Furthermore, they provide mechanical and physical properties that are superior to their rivals. They are also the most common and cost-effective alloys with exceptional strength. The parts produced through die casting these alloys are accurate and reduce the defect rate among the parts.
Does Sunrise Metal provide one-stop Zinc Die Casting Manufacturing?
A manufacturer that can provide all the Zinc die-casting services is called one-stop Zinc die casting manufacturer. Furthermore, in the field and line of Zinc die casting, this type of manufacturers holds the most respect.
Sunrise Metal is one of them, and its 23+ years of field experience is proof of its high-quality manufacturing. For the past 23 years, we are devoted to the majority of our service years to the production of zinc die-casting.
Over the years, Sunrise Metal has never forgotten his original intentions to learn, adapt, and improve. We as well as deliver our customers top-quality and precise die-casted parts.
Our experience in die-casting production and always put the interests of customers first satisfy our clients. We can accomplish the present accomplishments based on your help, so your help is our main thrust for progress. We accept that we can unquestionably enable our clients to make more noteworthy worth with our joint endeavors.
What advantages and why customers choose one-stop Zinc die casting manufacturer and prefer it over others are the following:
- Zinc die-casting is a one-step forming, so picking this can guarantee the nature of zinc alloy die-casting.
- Sunrise Metal has an ideal management system, carefully controls each production process so that clients can get guaranteed outputs.
- We can help reduce production costs and improve production proficiency while guaranteeing item quality and on-time delivery.
- We can also help from die-casting product design to product delivery independently, without customers worrying about every process.
Does Sunrise Metal provide DFM for Zinc Die Casting Product Design?
Yes! Sunrise Metal is experienced in providing DFM for product design.
Customer and provider trade data to characterize product design and its manufacturing process through DFM: Design For Manufacturability.
The point of DFM is to portray the product and its association with the productive process. Furthermore, it’s required to examine the task’s specialized achievability and recommend arrangements to encourage the manufacturing process.
Experts can state if the design is consistent with the production division’s innovative frameworks through this record.
However, at that point, they can prompt on altering explicit product attributes or production stages.
When choosing die-casting as a production strategy, it’s essential to lead a detailed analysis concerning parting lines and extraction focuses. Furthermore, product design is accordingly inseparably connected to mold design, and thus to the productive cycle.
The use of molds results is profitable because it allows the replaceability of the mold over time. It involves complex studies and tests to obtain the most suitable die-casting mold for the required product. DFM contains all the information required to achieve the target successfully.
How does Sunrise Metal produce Precision Zinc Die Castings?
Born out of the heartland and consistently “Made in China.” Sunrise Metal is the most significant independent devoted Zinc die casting services provider and manufacturer in Jiangsu.
We have kept developing our business by promising greatness and devotion to customers’ achievement for +23 years.
Being in the die casting business for so long speaks volumes of worth we offer to our clients. These include cost investment funds, extraordinary quality, on-time conveyance, agreeable client assistance, advancement, building cooperation, and configuration uphold.
We have the assets and ability to develop with you. Hence, joining forces with Sunrise Metal bear you the security of a believed source. It’ll help you gracefully start your venture with the best exactness designed parts for your existing part pattern.
Sunrise Metal is monetarily solid, and our progressing capital speculations are continually improving. Furthermore, our commitment to mirror our drawn-out point of view to manufacture and produce the best Zinc die-castings.
As we upgrade our cycles, we invite chances to make partnerships with companies similarly dedicated to greatness and excellence.
What is Special about the Zinc Die-Casted Parts from the Sunrise Metal Production?
Sunrise Metal offers customized solutions and die-casting services. We have practical experience in the little, medium, and substantial measured sections at ideal manufacturing and process cost-saving ratio.
Our long understanding and extensive expertise in Zinc die-casting empower us to serve a wide range of enterprises.
Our client portfolio goes from designing to clinical innovation to electronic manufacturers – from sensitive parts to too mathematically complex parts.
Our high quality and economic productivity, just as our quality awareness and precision production, persuade our clients.
Our quality management system is certified. Furthermore, our feeling of quality beginnings with the principal contact and goes right to conveyance. This’s possible through frequently long-term fruitful collaboration on the two sides.
Happy clients are standards for our activities and services. Sunrise Metal sees complex requirements as a challenge, and our objective is finding customized solutions to your specifications and requirements.