Sunrise Telecom Aluminum Die Casting Components
Superior telecom casting products are designed and developed at Sunrise to meet the highest protection standard by international compliance authorities. It is ideal to be used in industrial and commercial applications in the telecommunication sector.
For any housing solution of electrical and electronic components, die casting solutions have features that stand firm in difficult environments. Die cast aluminum components offer additional benefits such as anti-corrosion, ease of installation and detailed designs.
Also, the production process is such that the resultant sturdy and reliable equipment survive even in severe, hazardous, dusty, wet environmental conditions. The waterproof and dustproof design also gets through harsh weather and lasts much longer than other alternatives.
Sunrise Telecom Aluminum Die Casting Manufacturing Capability
Our standard die cast aluminum parts can be configured and specified to customer design requirements. Depending on application, it can be mounted with holes which make it convenient for use. As the structure is made from superior-grade aluminum material, and the casting process involves high exposure, the telecom casting products are immensely strong.
In our modern facilities, we have a range of sophisticated machinery, where these parts are developed. All processes are supervised by professional and skilled engineers, in line with international standards. Any possible deficiencies are identified and corrected during fabrication, and a top-quality product is transported to the client.

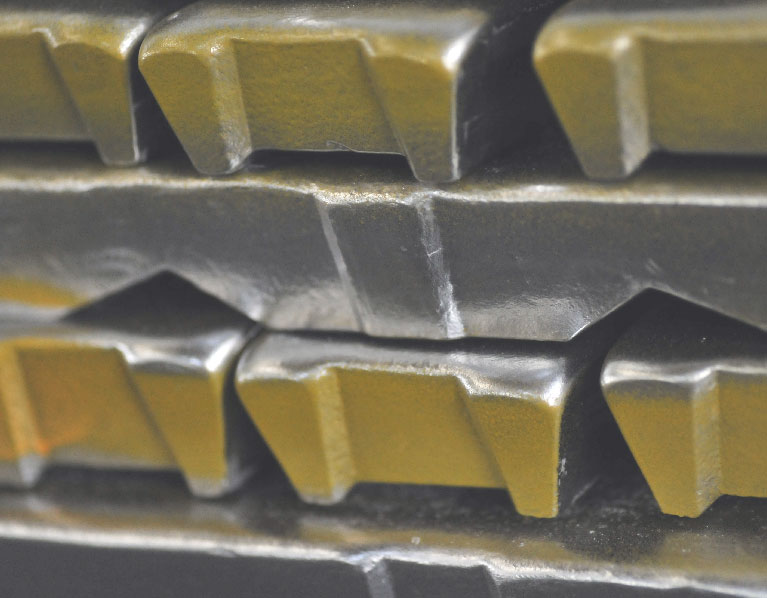
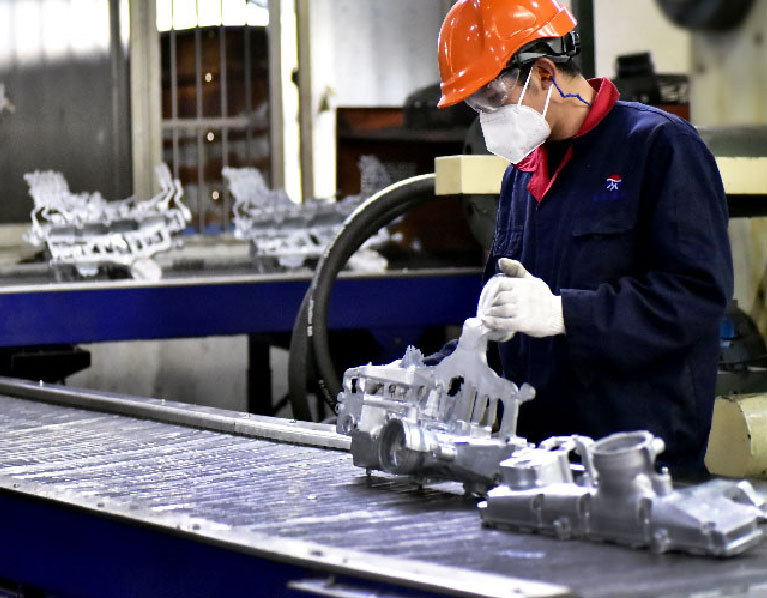
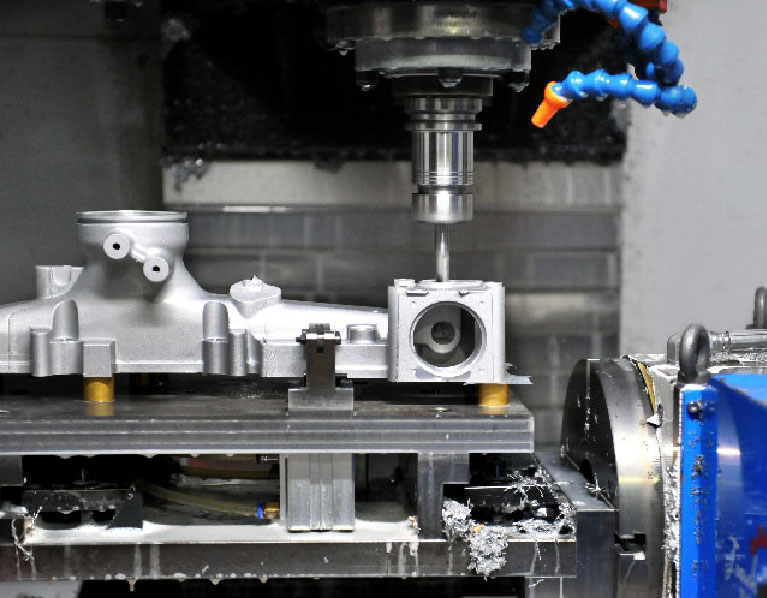
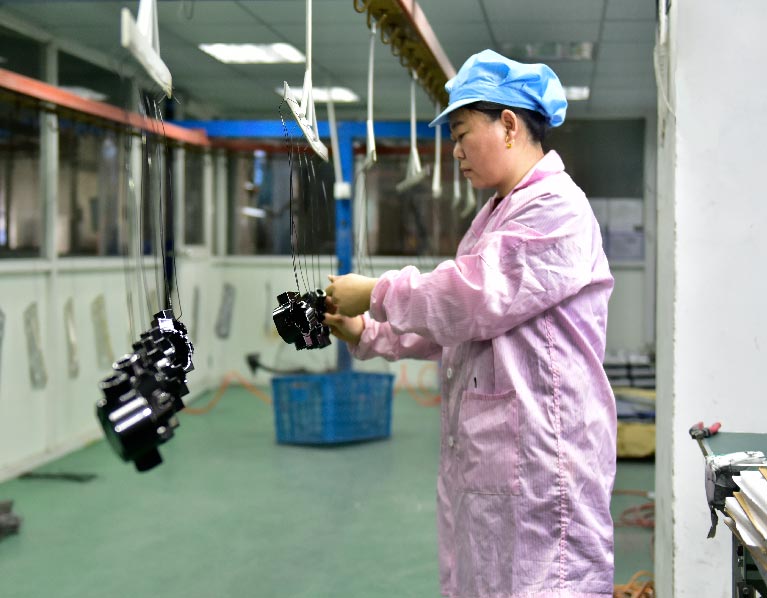
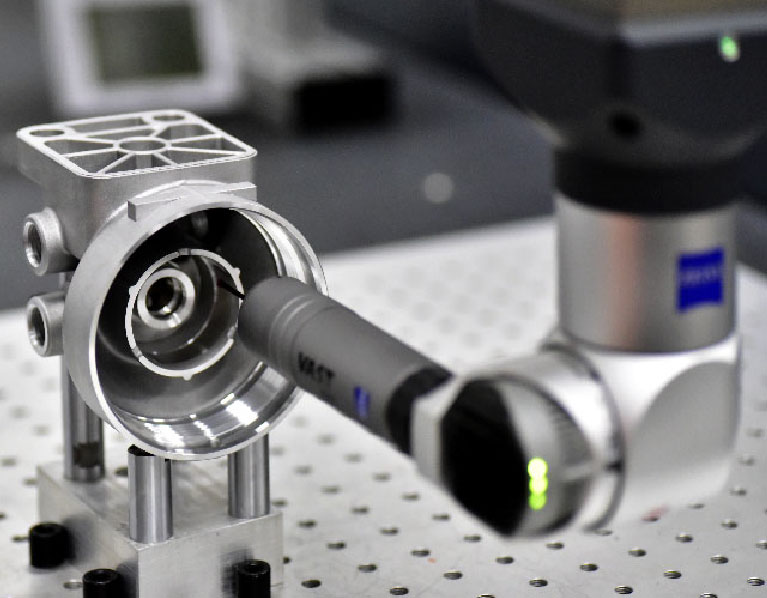
Advanced Equipments For Telecom Aluminum Die Casting
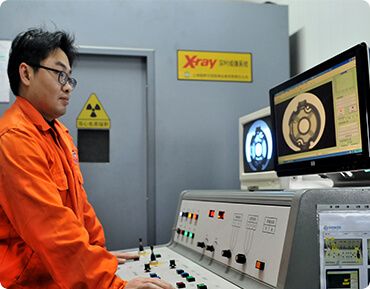
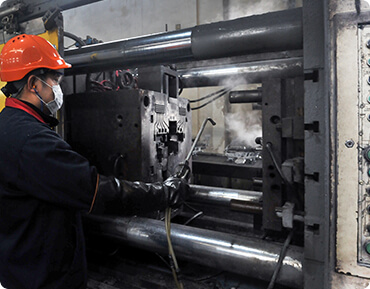
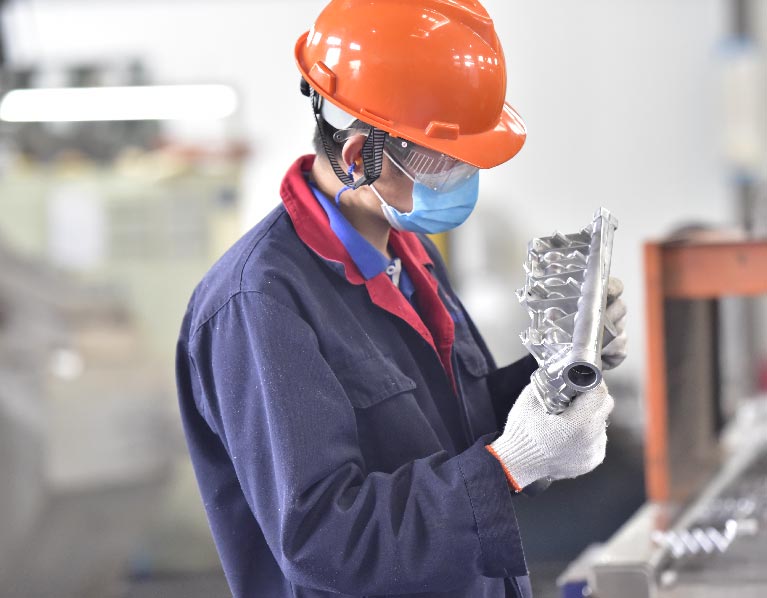
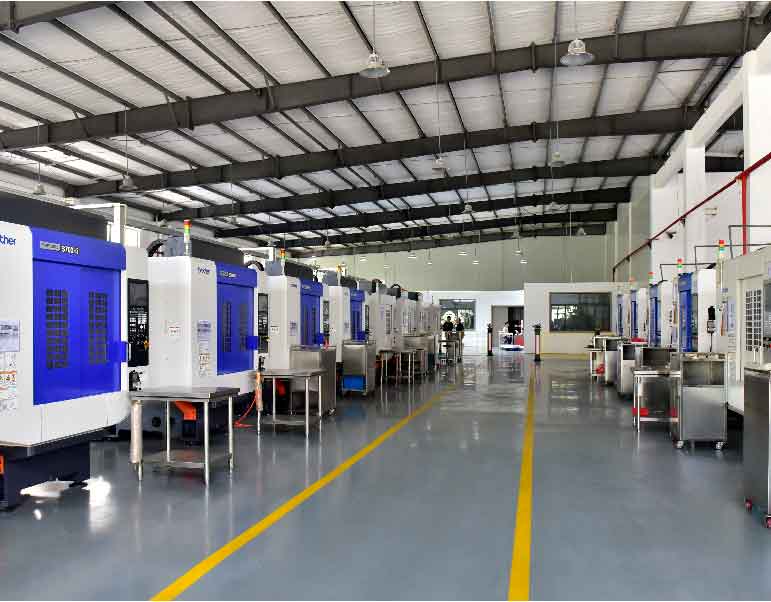
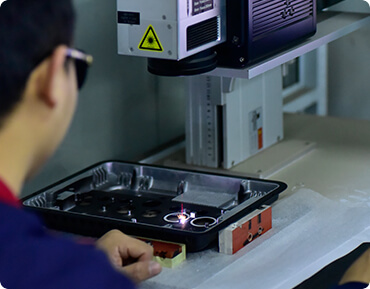
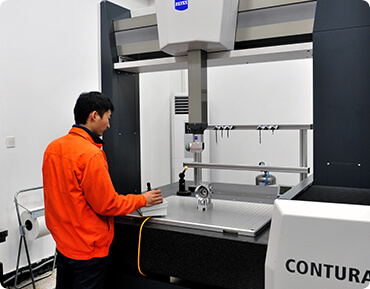
Recent Telecom Aluminum Die Casting Components Projects
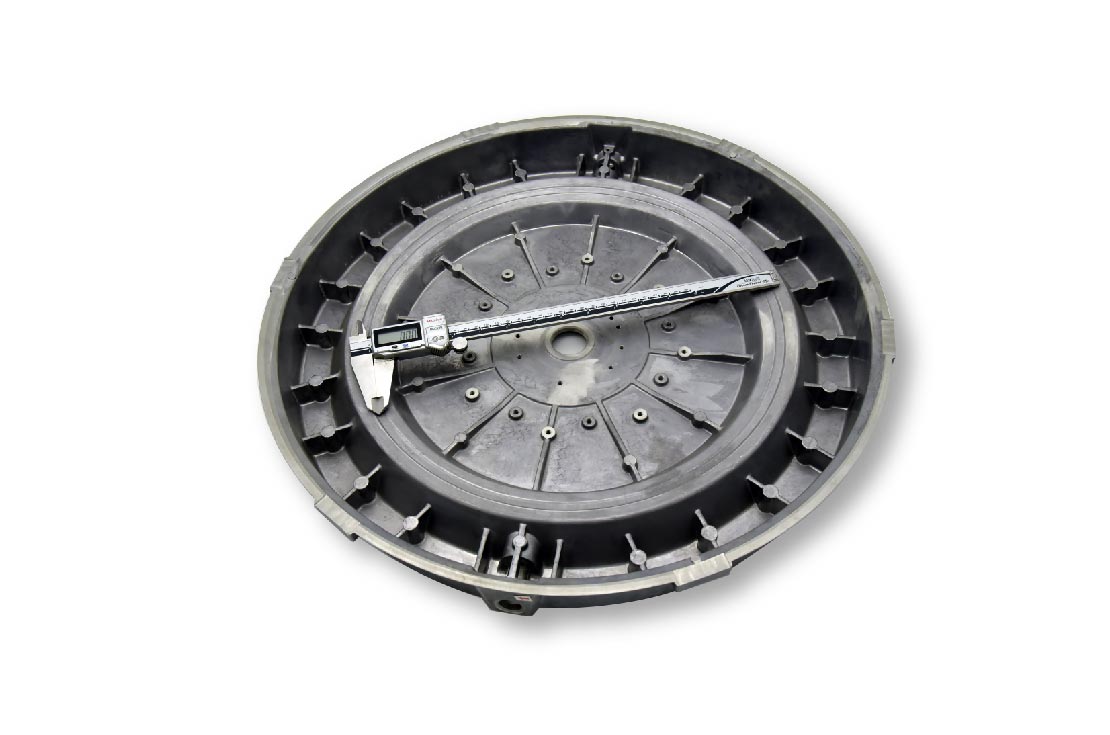
Part Name: RADAR BASE PLATE
Material: AlSi12
Size: 535*520*50mm
Weight: 15000g
Machine Tonnage: 1600T
Surface Finish: Sertec-650
Production Process: Die Casting–Trimming–Deburring
–CNC Machining–Chromating–Screening–Packaging
Applied Industry: TELECOM
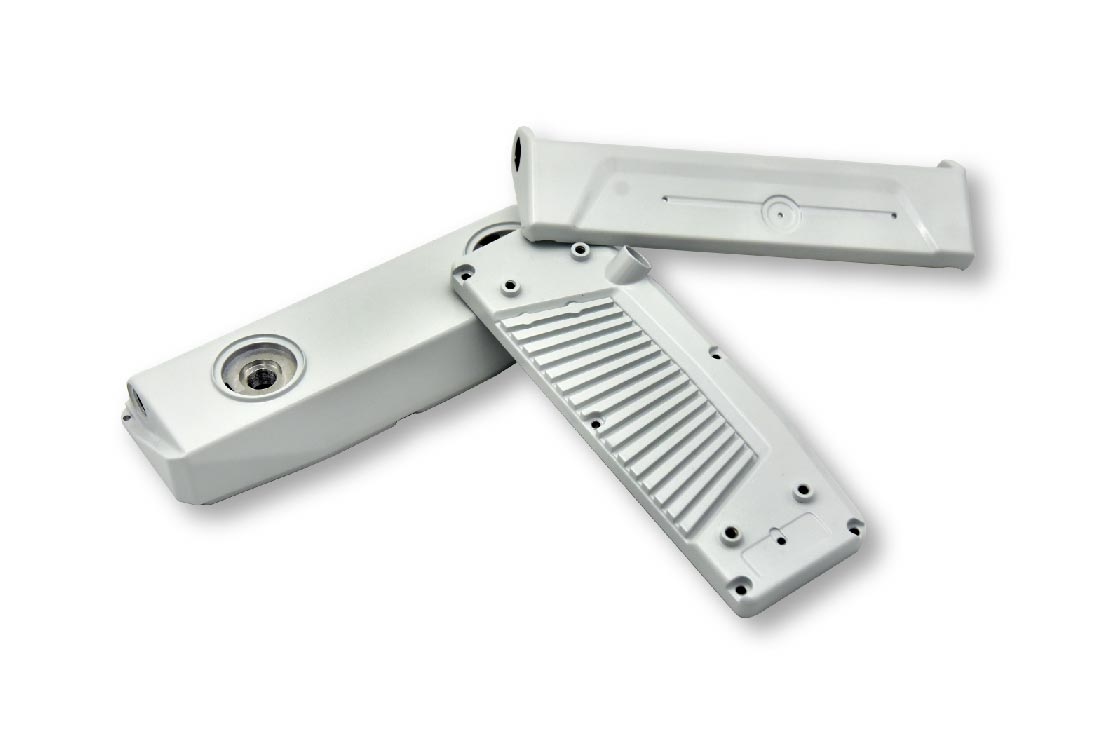
Part Name: HEAT SINK
Material: AlSi12
Size: 182*70*38mm
Weight: 432g
Machine Tonnage: 280T
Surface Finish: Powder Coating
Production Process: Die Casting–Trimming–Deburring
–CNC Machining–Chromating–Powder Coating–Screening–Packaging
Applied Industry: TELECOM
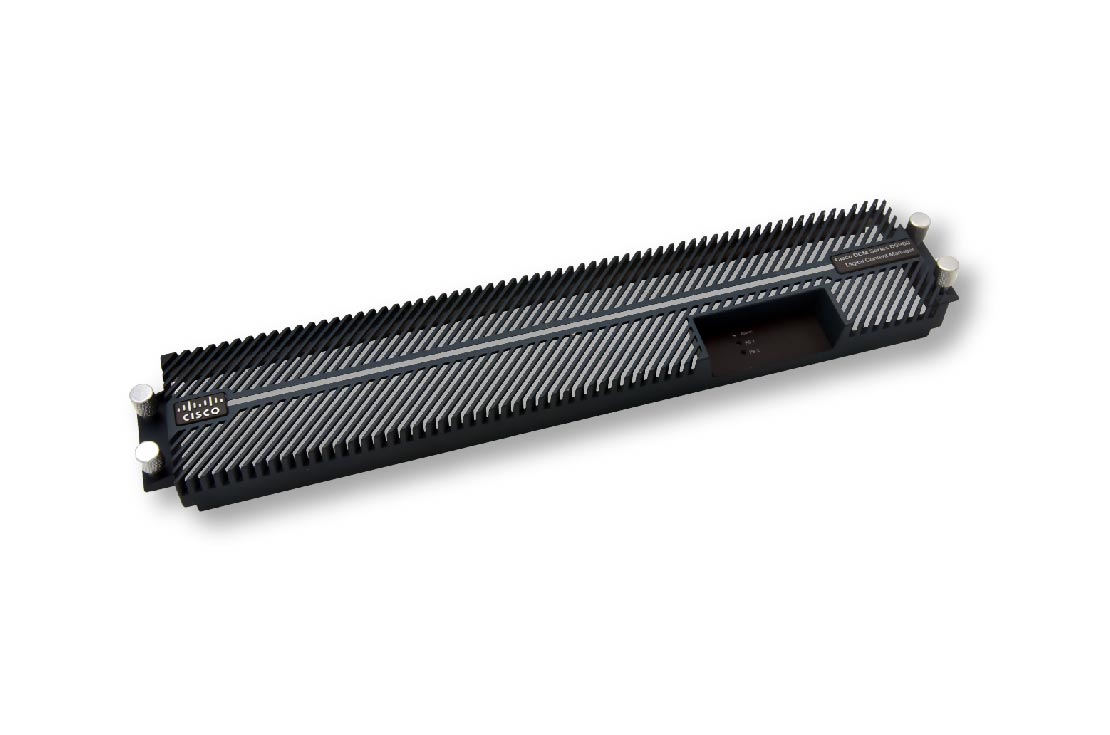
Part Name: Heat Sink
Material: AL6061
Size: 200*71*35 mm
Weight: 276g
Surface Finish: Coating
Production Process: CNC Machining–Sand Blasting–Coating–Screening–Packaging
Applied Industry: TELECOM
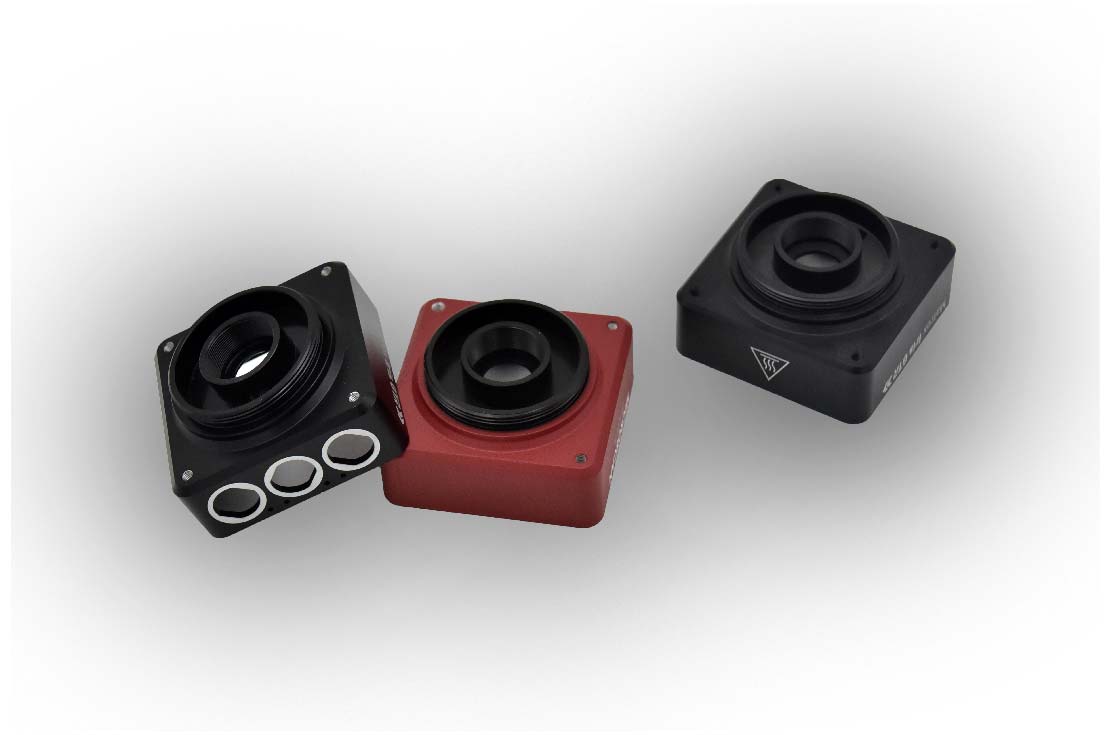
Part Name: Camera Cover
Material: Al6061
Size: 75*75*60mm
Weight: 100g
Surface Finish: Anodizing
Production Process: CNC Machining–Anodizing–Laser Ethcing–Screening–Packaging
Applied Industry: TELECOM
TELECOM CASTING:
THE COMPLETE FAQ GUIDE
The telecommunications industry faces unique challenges when designing products for the highly dynamic tech space. Innovation is constantly changing how we do things and a guaranteed high volume supply of top quality components can be a challenge. Telecommunication casting allows one to make highly accurate parts for various applications in the industry.
- What is Telecommunication casting?
- What are the Benefits for Telecommunication Casting?
- What are the types of die casting ideal for Telecommunications industry?
- What is the difference between Telecommunication casting and injection molding?
- What can be made from Telecommunication casting?
- What surface treatments are available for die cast parts made for Telecommunications?
- What material is used to make telecommunication parts?
- Are there specific dies casting alloys that work best for telecommunications?
- What Telecommunication parts can be made with die-casting?
- What is the process of making die casting parts from drawing to packing?
- What are Sunrise Metal’s capabilities in handling telecommunications die-casting?
- How does Sunrise Metal assure customers of superior quality?
- Why should you choose Sunrise Metal for your die casting needs?
[sc_fs_faq html=”true” headline=”h2″ img=”” question=”What is Telecom casting?” img_alt=”” css_class=””] This is the process of die casting various parts for use in the telecom industry. As a diverse industry, telecom is a highly dynamic space with many innovations released every day from all over the globe. To actualize the ideas is a die casting company that creates a functional piece using various tools. Professional one-stop services supplier like Sunrise Metal provide designing, engineering, tooling, prototyping, and die casting, cnc machining and the final surface finishing. You can expect your telecom casting parts made by an expert like Sunrise Metal will meet your exact specifications. [/sc_fs_faq]
What are the Benefits for Telecommunication Casting?
When creating a component for telecommunications, consider using die casting for the highest benefits. Here are the benefits of telecommunications casting;
- Can make items with complex shapes easily
- The quality remains the same despite high-volume productions
- You can integrate heat sinks with the design
- The cast housings are sturdy and durable
- Requires minimal draft angles on internal features
- A range of surface treatments are available
- Can utilize thin wall aluminum technology on devices
What are the types of die casting ideal for Telecommunications industry?
All the processes used in die casting are made with the same goal in mind – to cast a mold using an injected molten metal. Largely dependent on the kind of molten metal in question, part size and part geometry, some die casting processes offer consistently better results over other methods. You will see that most sources say that there are two types of die casting methods – the hot chamber or cold chamber die casting. There are variations of the two casting types which are;
- Vacuum die casting
- Semi-solid die casting
- Pressure die casting (low and high pressure die casting)
- Squeeze die casting
Let’s learn how the various types of die casting work and what materials they are best suited for.
The Hot-Chamber Die Casting
Also known as hot casting or gooseneck casting, this is the most popular of the two major types. The cylinder chamber is fully immersed in a molten metal bath and a metal feed system then draws out the molten metal into the cavity.
The direct immersion has its benefits as it allows for convenient and quick mold injection and also increases corrosion resistance. It is therefore best suited for metals that have high fluidity and low melting points such as zinc, magnesium, lead and copper.
The Cold-Chamber Die Casting
The cold chamber die casting method focuses on preventing corrosion as opposed to production efficiency. The molten metal is injected automatically or by hand. It is an excellent alternative for materials that are too corrosive and those with high melting temperatures such as aluminum and its alloys.
Vacuum die casting
Vacuum die casting uses a vacuum to get the liquid into the mold. This is utilized is there is air entrapment, undercuts or intricate details or if material or wire or fiber reinforced. It also decreases porosity in the material.
Semi-solid die casting
SSM is a variant of die casting that is preferred with non-ferrous materials like copper, aluminum and magnesium. There are two types of SSM;
- High solid fraction slurries – They are highly viscous with 40 to 50 percent solid particles and used on high quality castings.
- Low solid fraction slurries – These have only about 5 to 20 percent of solid particles for low level porosity items.
Low pressure die casting
Also shortened as LPDC, this process is a bit different from the other. First, a ceramic tube is connected to a steel die above it and goes into a furnace of molten metal below. The furnace has pressure to fill the part, doing this by making thee fluid go up the sprue. Once the casting is solid, thee pressure is reduced so that the remaining molten metal can be returned to the furnace.
This process is best suited for thicker parts up to 2.5 mm, and high volume productions.
High Pressure Die Casting
Unlike LPDC, HPDC forces molten metal into a sealed mould cavity while under pressure. It is held together with powerful compressive power in the mould until it solidified. This phase is called intensification. The pressure releases any gases trapped in the mould. Once solid, the die is released.
Squeezed die casting
This is the hybrid of low pressure casting and high pressure casting and can eliminate thee gas entrapment issue common with high pressure casting.
In this type of casting, the die is filled slowly with metal to maintain laminar flow. Once it has filled up, the pressure is increased and maintained to feed the casting, which compensates foe shrinkage until the casting is solid. The die design for squeeze casting is different from any other. The design often has thick gates and a large shot end biscuit to make sure the gates don’t freeze before the casting does.
What is the difference between Telecommunication casting and injection molding?
There is definitely some variations in both techniques but the major difference between the two is that die casting will mostly use metals while injection molding often uses plastic or polymers as the raw material.
The process of creating a component is fairly thee same whether you are using injection molding or die casting. You start with making a mold or die in the form of the part you want to make. Then you liquefy the material using high temperatures to inject it into the mold. Cooling is the last thing before removing your product.
Benefits of die casting;
- It is an efficient process boasting high accuracy
- You do not need secondary operations
- Complex designs can be cast with ease
- Produces high quality products that are durable
What can be made from Telecommunication casting?
Die casting is a process that has endless possibilities. Any part production that involves high volume metal items will most likely benefit from telecommunication casting. From satellite communications to optic trans receivers, Sunrise Metal is ready to handle all your telecommunications projects.
Fiber Optic Connectors
You can make small precision fiber optic parts with great quality and consistency using telecommunication casting. In the harsh tech environment, you need assurance that the part will not break or wear down.
Networking
Components made from die casting can be used in a range of networking equipment. This includes high precision zinc pins in switching systems and aluminum cast RF filter boxes. You can also make connector housing easily in one of Sunrise Metal’s high capability shops.
Durable & Complex Components
Housings made from die cast are highly durable and can be used with heat sinks within their design. These parts are also used in radar and frequency control systems, antennas and transmitters. Sunrise Metal is able to easily create a draft with parts that has internal features cast into it.
What surface treatments are available for die cast parts made for Telecommunications?
Die casting is often used with metallic products so most of the surface treatments will be those that work for metallic surfaces. They include polishing, plating, painting, anodizing, powder coating, pad printing, water transfer printing, silk screening and e-coating among others.
Sunrise Metal is capable of these surface treatments among others; Chromating, Powder coating, Wet painting, E-coating and Anodizing.
What material is used to make telecommunication parts?
Die casting if often done on metals like copper, aluminum, tin-based alloys, pewter and lead. Sunrise Metal will apply either hot or cold casting depending on the type of metal in question. Here is a summary of the benefits of each alloy in reference to telecommunication casting;
Zinc – one of the easiest metals to cast, zinc has high impact strength, is economical, easily plated, and durable.
Aluminum – a lightweight and highly ductile metal, aluminum is excellent for die casting as it is easy to plate, economical for small components, retains strength at high temperatures, and has good mechanical properties.
Magnesium – The metal is easy to machine, has great strength-to-weight ratio.
Lead and tin – They are both dense, close to dimensional accuracy and corrosion resistant.
Silicon tombac – This is an alloy made of zinc, copper and silicon. It is a great alternative to investment cast steel parts.
Copper – This is a metal with high hardness, mechanical properties, wear resistance and corrosion resistance.
Are there specific dies casting alloys that work best for telecommunications?
Die casting is a fabrication process that is well appreciated for its ability to manufacture parts with great uniformity, quality surface finishing options and close design accuracy. One popular material for use with die casting is aluminum alloys. Castings made from aluminum are able to withstand high temperatures and are lightweight.
Aluminum Alloy Characteristics:
- Lightweight
- Great strength and hardness
- High operating temperatures
- Great corrosion resistance
- Excellent electrical conductivity
- Outstanding RFI ad EMI shielding properties
- Great finishing characteristics
- Fully recyclable
- Commendable stiffness and strength-to-weight issue
Among the most preferred die cast alloys are these aluminum alloys;
- A380 is the most common alloy and preferred because it boasts a wide range of significant benefits that give it the best casting, mechanical and thermal properties,
- 383—also known as ADC12, this alloy is perfect for delicate items and often used as A380’s alternative.
- A413 is an aluminum alloy boasting high pressure tightness.
- B390 is best for metals that require high hardness and great wear resistance.
- A360 boasts great pressure tightness and fluidity.
- K-Alloy is cold chamber die casting ally made to protect parts from extremely tough operating environments.
Other alloys used in telecommunication casting include silicon tombac, ZAMAK, zinc aluminum and AZ91D magnesium.
Sunrise Metal often uses these alloys: ADC12, A380, ADC10.
What Telecommunication parts can be made with die-casting?
The options are endless with telecommunication casting. Die cast telecommunication parts can be made using this method as long they use metal. Some of the components include;
- Bluetooth enabled items
- Parts for wireless devices
- Voice command components
- Satellite communication parts
- Telecommunication components
- Switching devices and equipment in Telecommunications
- Multimedia transmission products
- RF equipment
- GPS Products
What is the process of making die casting parts from drawing to packing?
You have chosen a company and now you are wondering what is the process like. A professional service would be capable of engineering, designing, tooling, prototyping and mass production. You can also expect secondary services like deburring, coatings, vibratory finishing, plating, painting, machining, annealing and assembly.
In creating a die cast product, expect your service provider to go through this steps in their order;
- Design and making the mould/die
- Die casting the product
- Surface treatment
- Inspection and packing
What are Sunrise Metal’s capabilities in handling telecommunications die-casting?
Sunrise Metal has established itself as a leader in the aluminum die casting industry. It is designed to react to market demands. The company has several shops and boasts ISO 9001:2015 Certification. With large volume casting machines, Sunrise has the flexibility to react to quick changes as advised by a client. We also have a wide array of finishing and assembly options to make this a one-stop solution for you.
How does Sunrise Metal assure customers of superior quality?
Sunrise Metal is RoHS, Reach, and ISO9001 compliant. We have a stringent quality assurance team that works efficiently to ensure every product leaving our company shops is up to standard and functioning optimally.
Why should you choose Sunrise Metal for your die casting needs?
Sunrise Metal is a professional aluminum die casting manufacturer located in China. We create telecommunication parts for various facilities globally. With our knowledge and structured project management strategies, we are able to provide the ultimate solution for companies looking for a reliable parts manufacturer. Contact us today to get started on your project.