Sunrise Automotive Die Casting Components
Automotive casting products at Sunrise are developed to deliver on performance, durability, and efficiency in all types of projects.
We are involved in producing and manufacturing aluminum die casting automotive casting parts delivering optimum strength and enhancing engine power. The material being used in the production is selected carefully and meticulously to expand possible applications.
Aluminum alloy has been a special in-demand option in the market because of its beneficial features and cost-effectiveness. Over the years, the die casting process has led to breakthroughs in the automotive engine parts industry.
Sunrise Automotive Aluminum Die Casting Manufacturing Capability
Automotive aluminum die cast components are produced using high-tech machinery and aluminum die casting tooling, leading to fast production time. At Sunrise, we experienced success in the market and private sector through manufacturing quality automotive aluminum casting parts.
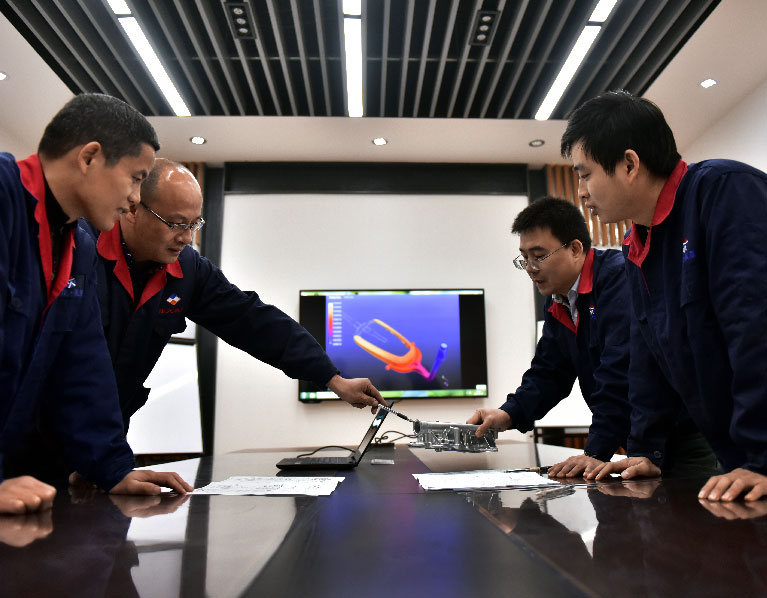
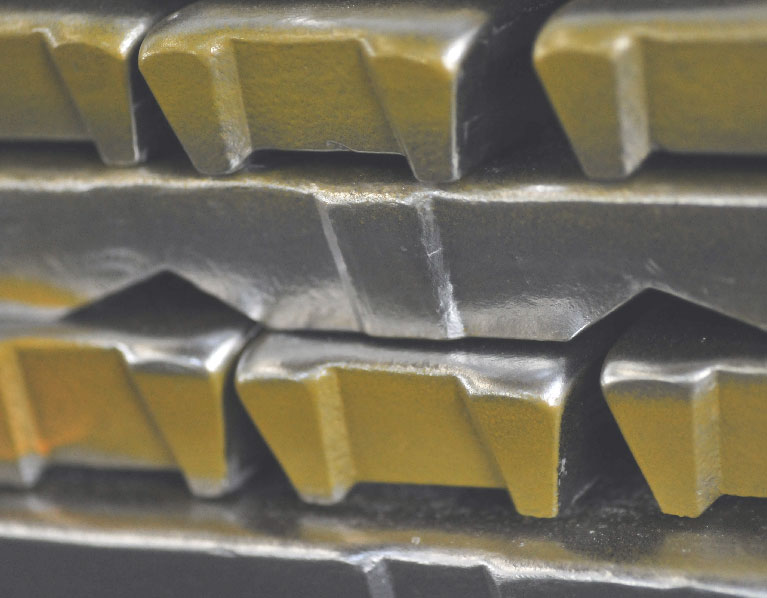
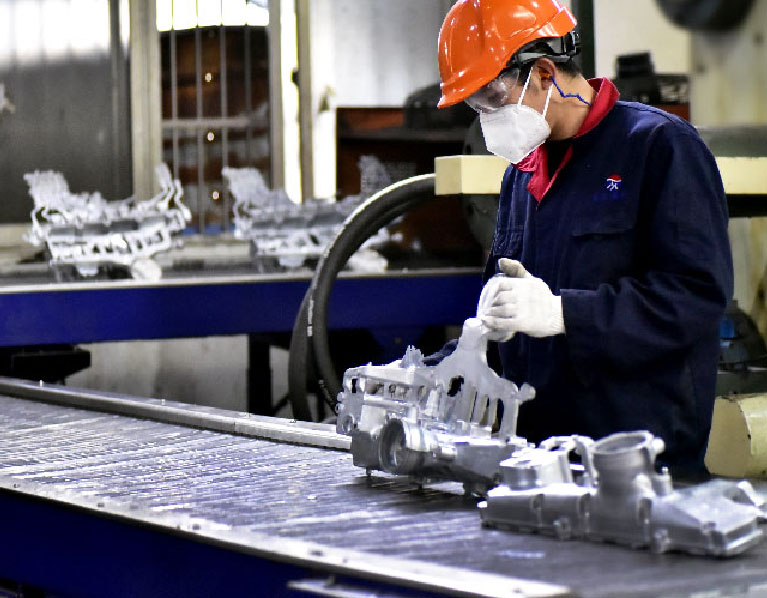
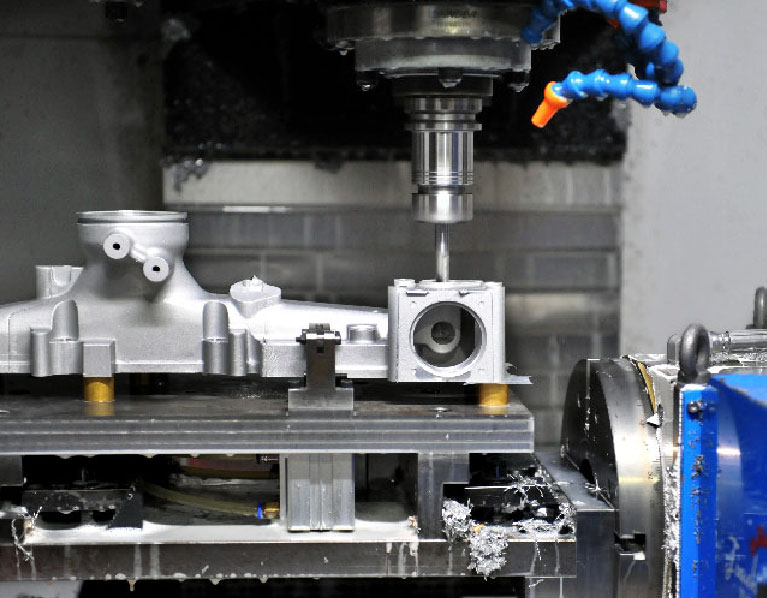
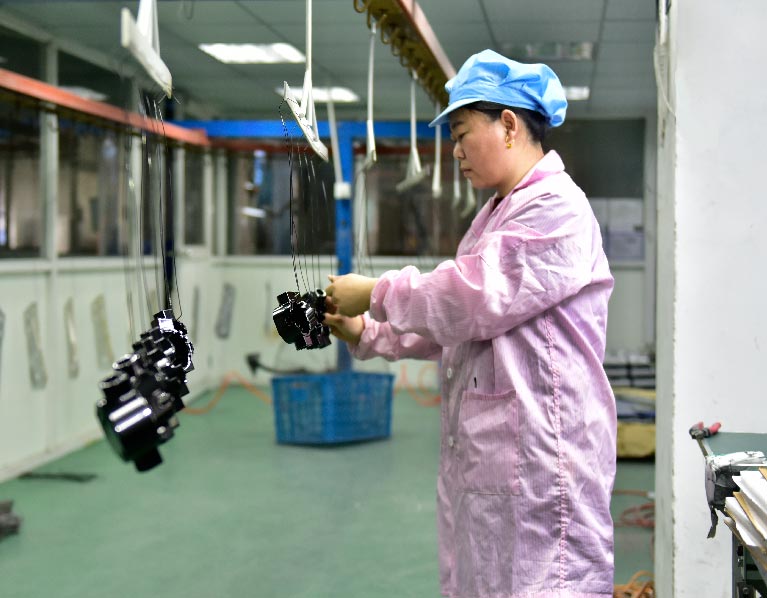
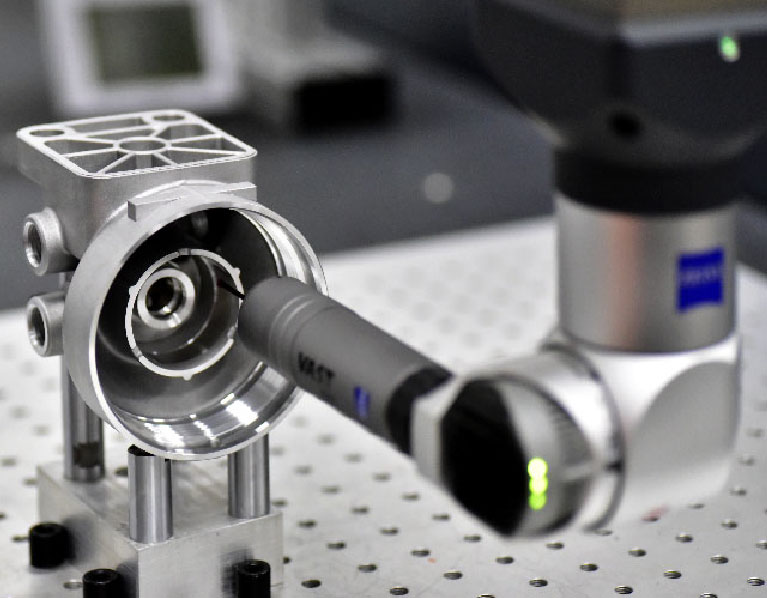
Advanced Equipment For Aluminum Die Casting Products
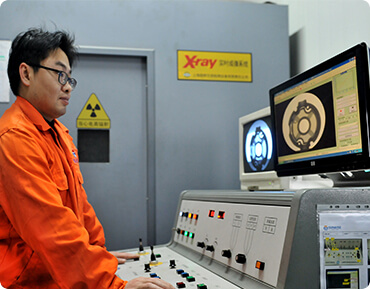
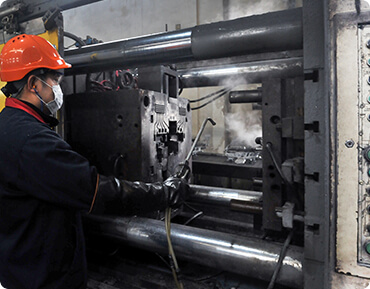
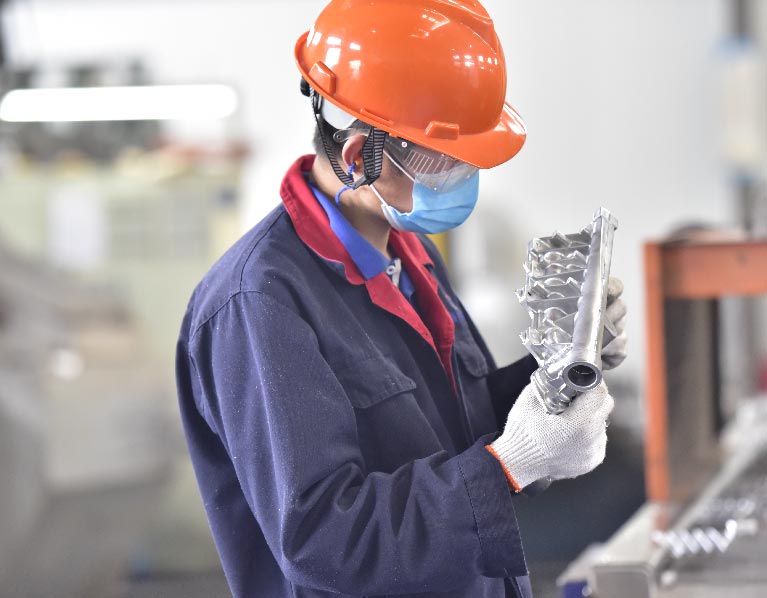
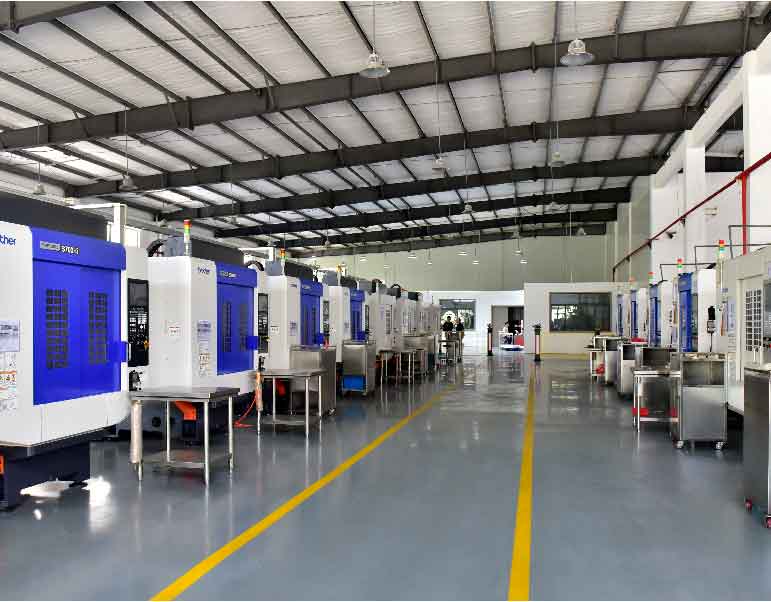
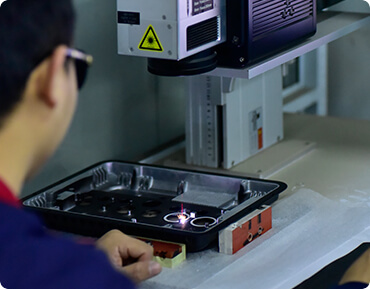
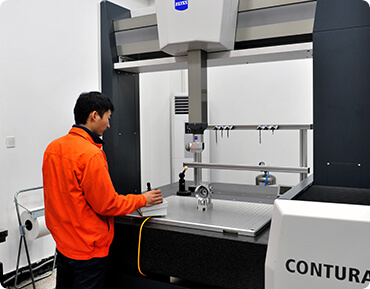
Recent Automotive Aluminum Enclosure Projects
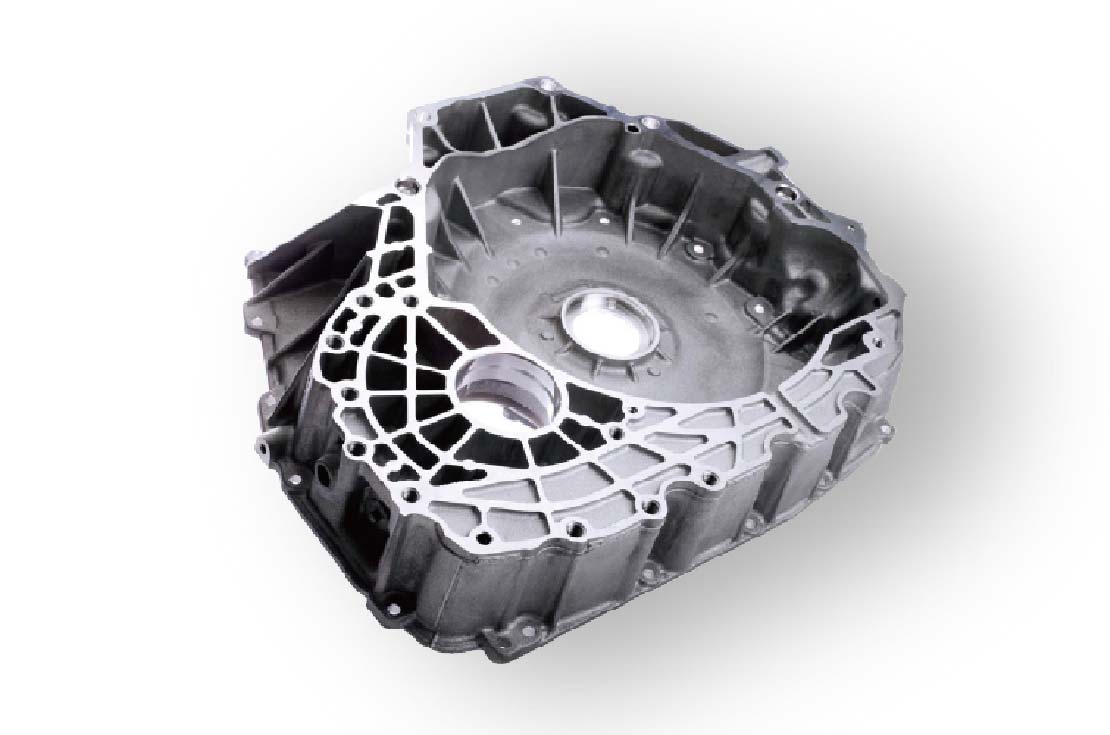
Part Name: Engine Housing
Material: ADC12
Size: 660x480x350mm
Weight: 7300g
Machine Tonnage: 2500T
Surface Finish: Chromating
Production Process: Die Casting–Trimming–Deburring
–Shot Blasting–CNC Machining–Leakage Test–Chromating
Applied Industry: AUTOMOTIVE
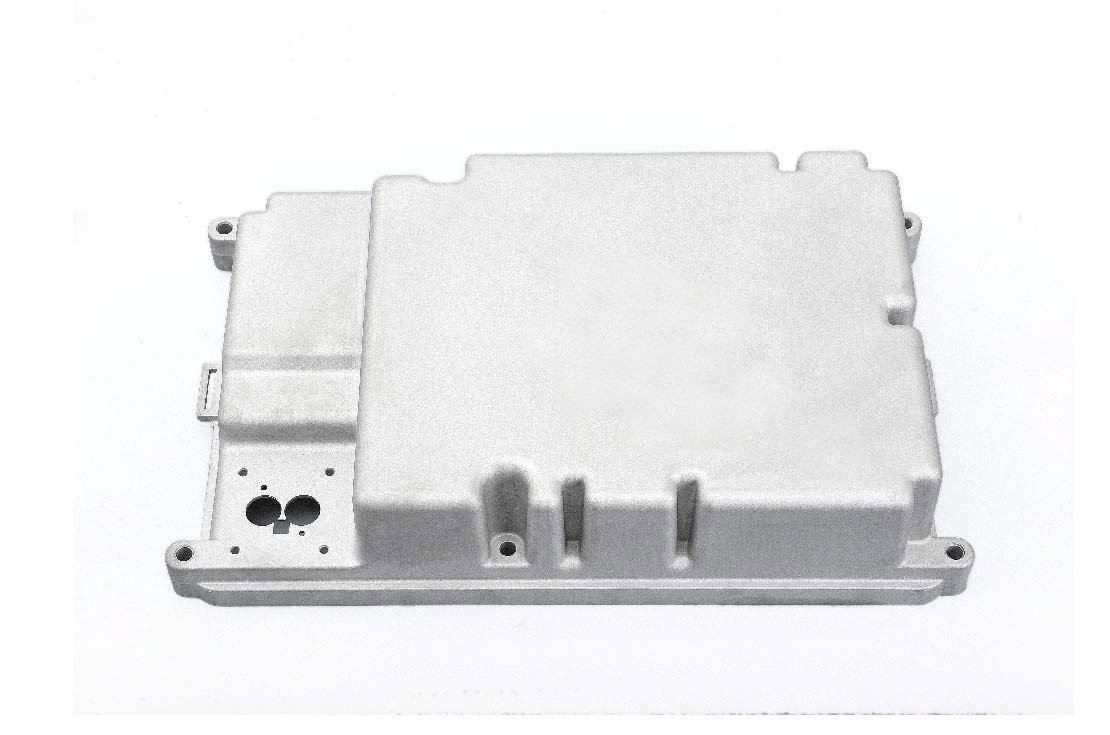
Part Name: Automotive Battery Cover
Material: ADC12
Size:470x284x99 mm
Weight: 2580g
Machine Tonnage: 800T
Surface Finish: Chromating
Production Process: Die Casting–Trimming–Deburring
–Shoot Blasting–CNC Machining–Chromating
Applied Industry: AUTOMOTIVE
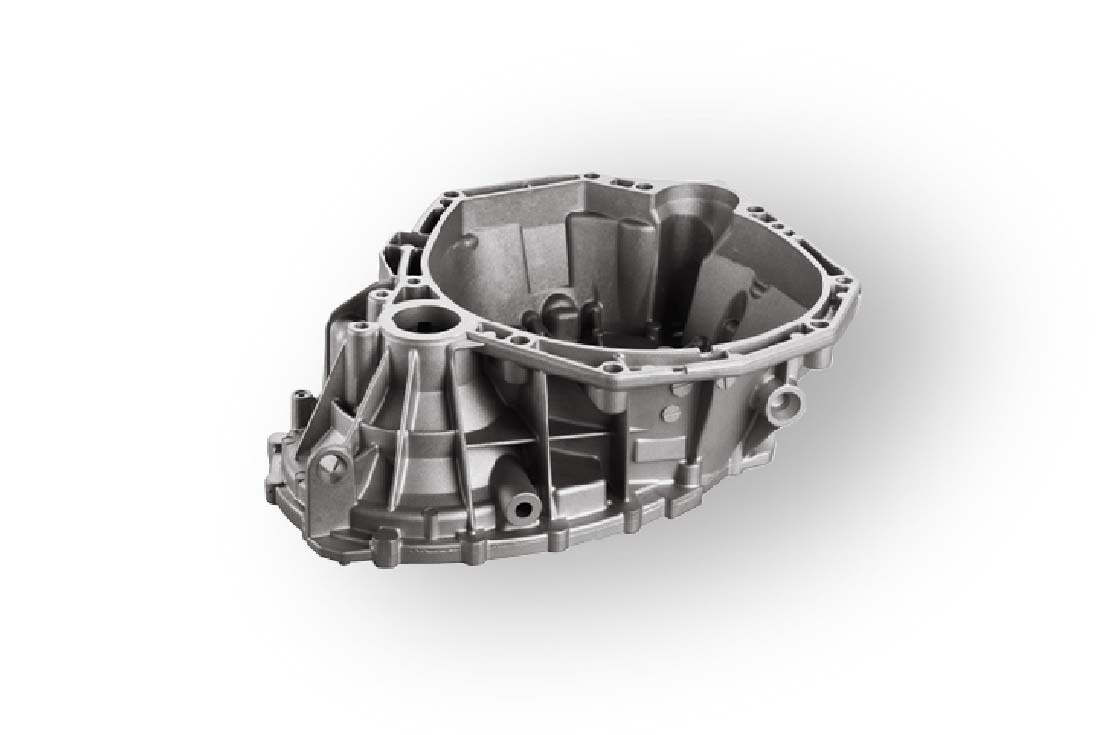
Part Name: Engine Housing
Material: ADC12
Size: 620x500x22mm
Weight: 6000g
Machine Tonnage: 2500T
Surface Finish: Chromating
Production Process: Die Casting–Trimming–Deburring
–Shot Blasting–CNC Machining–Leakage Test–Chromating
Applied Industry: AUTOMOTIVE
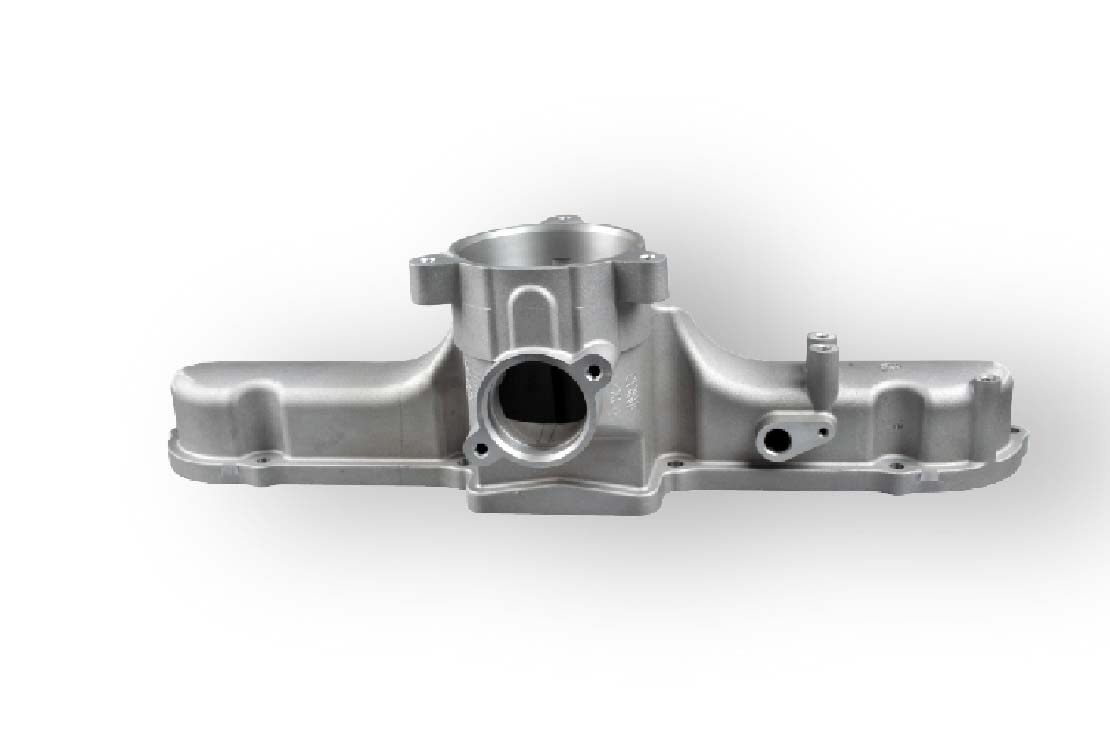
Part Name: Automotive Intake Tube
Material: ADC12
Size:451x138x125 mm
Weight: 1340g
Machine Tonnage: 800T
Surface Finish: Chromating
Production Process: Die Casting–Trimming–Deburring–Shoot Blasting
–Shoot Blasting–CNC Machining–Chromating
Applied Industry: AUTOMOTIVE
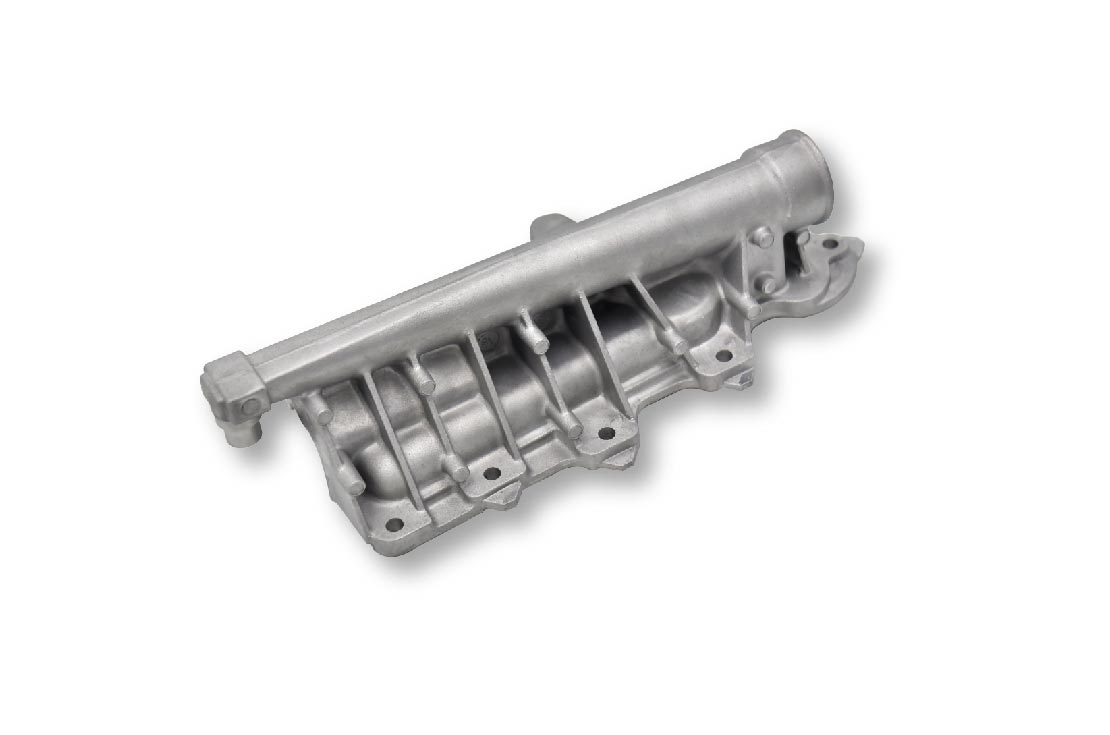
Part Name: Engine Filter Housing
Size: 284x180x84 mm
Weight: 851g
Machine Tonnage: 400T
Surface Finish: Shot Blasting
Production Process: Die Casting–Trimming–Deburring–Shot Blasting
–CNC Machining–Leakage Test–Chromating
Applied Industry: AUTOMOTIVE
AUTOMOTIVE CASTING:
THE ULTIMATE FAQ GUIDE
Automotive castings are becoming popular due to their lightweight, durable and cost-effective properties. For the automotive sector, Sunrise is helping to comply with efficient international standards by supplying only the best quality alloys and advanced machinery.
Our diecast aluminum parts are customized to match customer specifications and deliver the best results worldwide.
- Which die cast products are made for the automotive sector?
- What is the advantage of automotive castings made from aluminum?
- How are automotive casting products manufactured?
- Which materials are used for the manufacture of automotive castings?
- What are the requirements for manufacturing die castings for modern automotive parts?
- What are the different applications of die casting for the automotive sector?
- Do aluminum die cast products help to cut down automobile emissions and increase fuel efficiency?
- What are the costs that need to be considered for automotive die casting components?
- Are there any limitations on the type of die casting parts prepared for the automotive industry?
- Why is Sunrise a reliable manufacturer of castings for automotive application?
- What are the design possibilities offered by Sunrise for automotive casting?
- Which die casting machines are used to provide complex automotive castings?
- Three plate die casting machines with toggle
- Does Sunrise have any special project experience in automotive parts?
- What are the possibilities of aluminum die casting for electric vehicles?
- Which quality standards are followed by Sunrise to produce automotive castings?
Which die cast products are made for the automotive sector?
The automotive industry makes use of automotive die cast parts as they are lighter in structure. This is done for a major reason.
The automotive industry is known for its carbon emissions. New standards ask the industry to produce fuel-efficient structures so the carbon emissions could be reduced. To produce such vehicles, the structure should be lighter so the consumption of the fuel could be reduced. Aluminum provides this feature, allowing manufacturers to meet rising demands.
Different die cast parts are being used for the automotive sector as more and more steel parts are being replaced by aluminum automotive castings. These parts give thin wall thicknesses and high mechanical properties therefore die casted products are of great value to the automotive industry.
At Sunrise, we produce automotive castings that meet highly precise specifications, engineered by expert teams.
Automotive castings are best used in engine blocks. This turns the engine into lighter machinery. The following die casted parts are being used in the industry.
- Engine cylinder heads
- Gas engine parts
- Stator
- Brackets for electric motor
- Stepper motors
- Covers for the gearbox, motor, shades pole.
- Heat sinks
What is the advantage of automotive castings made from aluminum?
Aluminum die-casted parts are very popular in the automotive industry. This is due to the many benefits that they provide.
Lightweight
Cutting down the weight of the automotive by 15% makes them efficient by 25%. Due to the lightweight properties that aluminum die cast parts possess, car engines and wheel structures are manufactured with them at a large scale. Replacing steel parts with aluminum die cast parts have proved to be a revolutionary development in this industry.
Productivity
As the automation in the manufacturing of these parts is increasing at a fast pace, automotive castings are proving to be more productive. A higher number of parts are produced in a shorter time, making this rate beneficial for large-scale production in the automotive industry.
Durability and Stability
Automotive castings produced using diecast aluminum are dimensionally stable and durable. They are dimensionally stable and much stronger than plastic counterparts. Aluminum components can have a high tolerance and are preferred due to their high heat resistance.
How are automotive casting products manufactured?
Automotive parts are manufactured using different techniques. The main processes used in production have to provide efficient and lightweight results. To achieve these results, the following processes are maintained.
High pressure die casting
This process produces products with less porosity and more perfection. High pressure die casting is the most widely used process in the manufacturing of automotive castings. It makes use of pressure techniques to fill the mold with molten metal and the ejection of a set part in the mold. The pressure techniques produce complex parts and reduce the need for more parts in the assembly.
Gravity die casting
Gravity die casting fulfills the needs of industrial components by providing complex parts of automotive. Internal features are produced and polished for the efficient working of automotive. The process uses gravity for its working. Gravity is required to fill molten metal in the mold. This process is cost-effective for automotive castings manufacturers in the long term.
Which die cast materials are used for the manufacture of automotive castings?
Automotive castings are required to use lightweight material. Die casted products are suitable for the purpose. Different materials used for the manufacturing of automotive casting, including zinc and copper, but the most popular and widely-used are aluminum.
Aluminum
Aluminum is prioritized over any other metal in the automotive industry due to its tendency of providing lightweight as well as durable products. Aluminum can be recycled and reused in castings. This makes it cost-efficient too. It meets the weight-saving requirements and provides fuel efficiency through automotive die castings.
Zinc
Zinc is easy to cast and offers many benefits. It is lightweight thus increasing the efficiency of the automobile. It also leads to a low cost during production. Superior quality parts are obtained using zinc die casting. It is corrosion resistant and hence is used to make the exteriors of the automotive. The greater flexibility and greater strength are what make zinc a good candidate for automotive casting.
Magnesium can also be used for die casting. However, at Sunrise, we focus on reaping the maximum benefits of Aluminum and use the best quality alloys for production purposes.
What are the requirements for manufacturing die castings for modern automotive parts?
Modern automotive parts manufacturing requires state-of-the-art solutions for the die casting process to be adopted at a large-scale. Newer solutions are needed to be used in electric vehicles and other modern hybrids automotive.
The die-casted parts in modern automotive need high yield strength and high conductivity. It should support the features of modern vehicles. Contribution to weight-saving requirements will save the energy for these models, making die-cast parts ideal for the purpose.
Excellent electrical performance and shielding properties are major requirements in the modern automotive part manufacturing. Die casting techniques are moving towards flow introduced by modern automotive parts and are producing multi-faceted, complex shapes with a versatile range of physical, mechanical, and finishing characteristics.
What are the different applications of die casting for the automotive sector?
Due to the varied possibilities offered by die cast products, automotive castings have wide-ranging applications in the sector. They play a vital role in manufacturing advanced automotive, while upholding quality and safety standards.
Structural Components
Die casting is applied when manufacturing structural components of a vehicle. They are being used in high-value cars and are proving to be a major factor in boosting the efficient production of automobiles. The industry for the manufacturing of structural parts has multiplied while decreasing the cost of the process.
The die-casted components have reduced the thickness of the walls. This thinning of walls requires greater know-how of the process and expertise proves to be the key factor here. All in all, this results in a product that is classified in a higher category and standard.
Customization
Die casting provides a great deal of customization in the manufacturing process. Different die casting processes are used in order to manufacture custom parts. This has provided new possibilities for the automotive industry to explore. The development of parts that are made to fulfill the requirements of the vehicle is easier. Moreover, customization in automotive castings does not even affect the surface finish or the strength of the automotive part.
Do aluminum die-cast products help to cut down automobile emissions and increase fuel efficiency?
The die-casted parts for the automotive industry are helpful in different aspects. One of those aspects is the increment of fuel efficiency. Reducing emissions is the issue that every manufacturer tries to resolve. To minimize emissions and to increase fuel efficiency, automobiles need to have lighter parts. The automotive castings by Sunrise seek to serve this purpose. They are light in weight and hence cut down the emissions.
Using aluminum die-casted parts is a new trend that the industry is following. Some companies were already using aluminum in the making of the automobile parts and some have started following it just now. Research now shows that reducing the weight of a part by 15% reduces the emissions and increases fuel efficiency by 25%. Following this, every manufacturer is trying to find new ways of making aluminum castings to cater to a growing market.
How are automotive casting parts different from other types of parts?
Automotive parts are being casted using die-casting techniques and different materials. In comparison to parts produced through other techniques, automotive castings produced with aluminum are definitely up a notch.
Some of the advantages can be highlighted to reflect the cross-industry impact that this style of manufacturing has had:
- High production
The industry’s requirement of die cast parts is multiplying every day. Automotive castings are produced at a faster rate serving large industrial clients. Many identical parts are being produced that sometimes require no machining after the manufacturing.
- Stability
The stability of car parts is a major part that can’t be compromised. Close tolerances are maintained using die casting. This is done through die casting. The parts are to be stable as well as durable or else the efficiency of automotive is compromised.
Automotive parts are to be ductile. They are to be changed into different shapes by applying force.
- Dimensional accuracy
Dimensional accuracy is required for the parts manufactured for automotive. The dimensional accuracy is achieved through automotive die castings prepared under expert supervision.
- Strength and weight
The strength of the automotive casting part is required to be greater than other parts while having a lighter weight than other parts. This shows the automotive industry should have lighter parts that are strong to meet the requirements imposed and have to make the machine fuel-efficient. Other parts are not limited by such requirements.
What are the costs that need to be considered for automotive die casting components?
While manufacturing die-casted automotive parts, the cost is estimated depending upon different factors. To estimate the cost these factors are judged.
Material
The type of material being used in the production of automotive parts directly impacts the cost of parts. Different companies use different materials depending upon their requirements and the benefits associated with it.
Wall thickness
The thickness of the parts’ wall also affects the cost of the die cast part. Thicker the wall, more the material required to manufacture it. As the required material increases, so does the cost.
Projected area
The area that the automotive part covers are also a factor that affects the cost of that part. More the area of the die cast part, more will be the cost. This factor is also considered when estimating cost.
Tolerance
Tolerance of the automotive part is also a major factor here. High tolerance is required for the manufactured part or it can cause failures in the automotive while increasing the costs of the manufacturing processes.
Are there any limitations on the type of die casting parts prepared for the automotive industry?
The automotive industry is moving towards the manufacturing of more and more aluminum die caste products in vehicles but there are still parts that cannot be manufactured using aluminum die casting. Limitations that are seen in the industry with this respect are as follows
Stiffness
A rigid design is required for automotive castings to be produced. Stiffness is most importantly required for the nature of the automotive production processes. This cannot be achieved using only die casted parts. Sometimes, the steel structure for such parts can be a better choice.
Cost
The cost involved in die casting is greater than other manufacturing processes used in the automotive industry. Other steel parts are lesser in cost and are easier to manufacture or machine. This factor also limits some of the manufacturers from using die casted parts.
Bent
The die cast parts are easily bendable as compared to other parts that are manufactured from other parts. This limits the manufacturers from using too many die cast parts.
Why is Sunrise a reliable manufacturer of castings for automotive applications?
Sunrise excels in the manufacturing of automotive castings. Guided by a team of expert designers, Sunrise is capable of producing a wide range of cost-effective and high-quality die casted products. These products are superior in nature as they feature the following characteristics:
- Variety: Multiple choices in the terms of material and sizes automotive castings is available. The metal options for your automotive is what makes Sunrise a lucrative option.
- Lightweight: Sunrise is an observer of guidelines provided for the production of automotive parts. These parts are light in weight and will provide fuel-efficient structures.
- Strong: The automotive parts that Sunrise produces are strong as well as durable. This adds value to their production and gives Sunrise an edge over other manufacturers.
- Precise: Sunrise takes pride in manufacturing precision parts for automotives. These parts give high performance. Sunrise manufactures automotive castings that are suitable for heavy-duty vehicles as well as lightweight airplane parts.
What are the design possibilities offered by Sunrise for automotive casting?
Automotive casting has limitless possibilities in the market to produce different parts. Sunrise provides flexible designs and manufactures customized products.
The designs produced at Sunrise are creative as well as scientific. This is so the customer not only has an efficient cast but also an attractive part that adds beauty to the setting of automotive.
Sunrise Metals works over the accuracy and functional futures of the die-casted part. Since the process is customizable, there are endless possibilities of the designs at Sunrise.
A smart combination of design and features is provided by us. The processes offered at Sunrise Metals is providing world-class products and superior precision cast parts.
Which die casting machines are used to provide complex automotive castings?
Different die casting machines are used for the production of simple to complex automotive parts.
Two platens toggle free die casting machine
These machines support a wide range of designs and are suitable for the production of structural components. It offers a force of 1000 tons to 5700 tons. They are reliable, rigid, and flexible.
Automation cells for die casting
These cells offer the automation of different die casting processes. High pressure die casting, low pressure die casting, gravity die casting and many more processes are automated to provide a wide range of automotive parts.
Three plates die casting machines with toggle
The machine with less force achievement as compared to toggle free machine provides solid and reliable automotive parts. Superior quality is achieved using this machinery to provide lightweight automotive castings.
Does Sunrise have any special project experience in automotive parts?
Sunrise Metal has worked for the Cummins project to produce engines that are cost-effective using automotive castings. The idea is to fit manufacturing capacity and expertise to specific consumer needs and drive results.
Cummins is a world leader in diesel engine manufacturing and we have supplied them with top-grade automotive castings. Sunrise Metal has manufactured these using the finest processes and employed the most advanced machinery.
Cummins not only produces high-quality products but ensures that its engines are genuine. This makes it absolutely imperative at automotive castings do not fall short of quality. Sunrise has maintained itself as a trusted manufacturer in this regard.
Our compliance with international standards has won us numerous such accounts and we specialize in contributing to the success to world leaders. Quality standards at Sunrise have never faltered, and Cummins has been assisted in maintaining their own standards and requirements.
What are the possibilities of aluminum die casting for electric vehicles?
It is predicted that electric vehicles will demand more and more lightweight structures and will move towards total die casting solutions in the near future. Electric vehicles might be risky for foundries and die production processes but it is also introducing new possibilities.
Structural applications
Electric vehicles demand very lightweight solutions. These are achieved by providing aluminum automotive castings. Suspension domes, longitudinal carriers, cross-members, doors/gates, and A-B-C pillars all present in electric automotive make use of aluminum casting in their production. Hybrid structures are being produced but predictions say that the percentage of aluminum will grow in electric vehicles in the future as this will reduce carbon engagement.
Aluminum battery cases
For a stiff structure, lightweight thin-walled battery cases are produced. This offers a great deal of flexibility and functionality of the design. High air-tightness is achieved using aluminum battery cases and it integrates different parts inside the casing.
Which quality standards are followed by Sunrise to produce automotive castings?
Over the years, Sunrise has demonstrated the capacity and expertise to build long-term solutions to manufacturing demands. Not only this, but we have built forward-looking systems that engage with suppliers to meet customized demands.
We do this by establishing international standards of quality and measurement in our facilities and inculcate the spirit of professionalism in our teams.
The following two certifications make us a dependable and credit-worthy supplier of automotive castings:
ISO 9001
This is an international quality management system that guides a company through a set of standards to make sure they meet their customer’s expectations. Since the client is of utmost priority at Sunrise, we fulfill all the requirements of the ISO standards related to our products.
We put in place processes and structures in our organization that bring out the best in each link in our chain. Work atmosphere, innovation, and quality are all cornerstones at Sunrise that are never compromised for any reason.
Sunrise follows all kinds of regulatory requirements under this international standard. We implement a quality management system that leads to top-quality automotive castings supplied across the world.
IATF 16949
This certification is a technical specification that fulfills requirements for quality management systems for the automotive sector. As a popular international standard, it brings Sunrise in the spotlight as a reliable manufacturer of automotive castings.
The IATF 16949 perfectly aligns with the vision at Sunrise, which is to provide the best quality product to automotive customers. Along with this, we ensure continued efforts in R&D, defect prevention, and reduction of waste and variation in the supply chain.
As a mandatory standard under ISO 9001, it supplements the efforts for organizational improvements. To ascertain that customers are satisfied, we believe in delivering only the best.