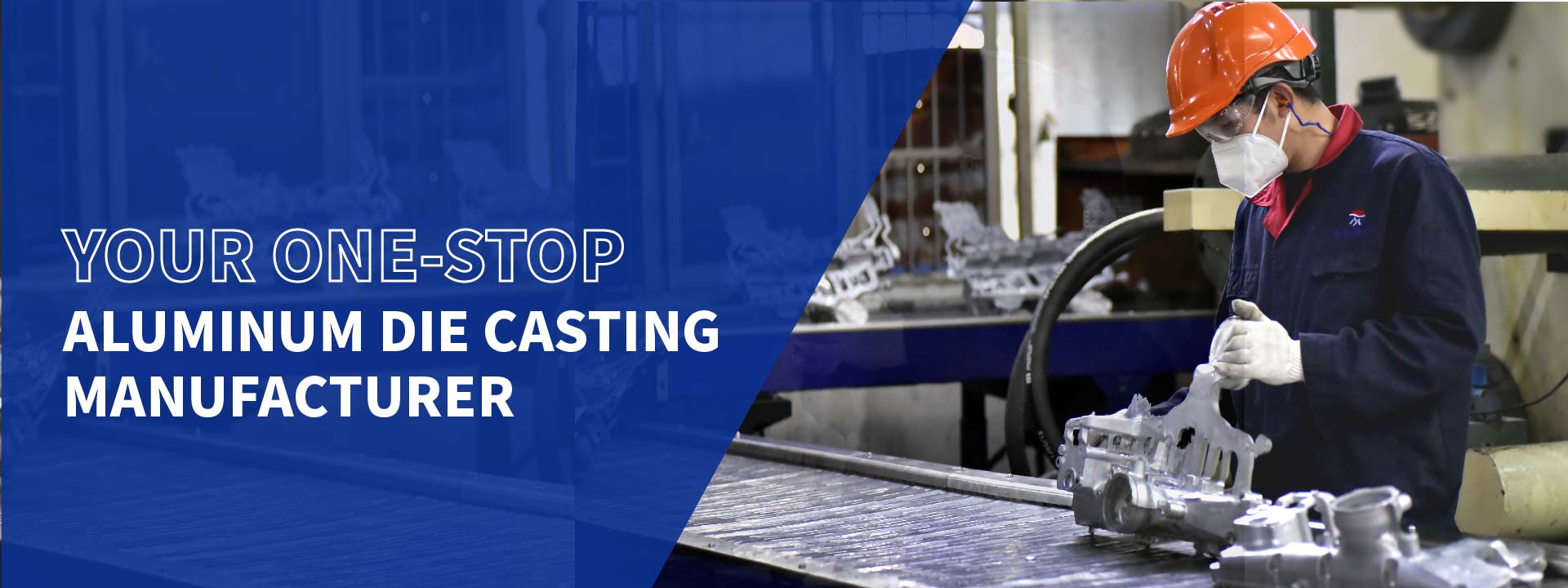
YOUR ONE-STOP DIE CASTING MANUFACTURER IN CHINA
- Rapid Prototyping
We offer rapid prototyping services using CNC Machining, Prototyping tooling, 3D printing, and many more techniques.
- Die Casting Tooling
Our tooling services range from the tooling design to tooling end-management and help build net shape products rapidly.
- Die Casting Production
Sunrise Metal has two die casting facilities. We can meet your various low volume or large volume die casting projects.
- CNC machining
The complement CNC machining service that includes premium milling, lathing, tapping, drilling, and cutting.
- Surface Finishings
Once done with the casting and machining, we offer complimentary finishing services that include anodizing, deburring, shot blasting, powder coating, and much more.
3000+ Die Casting Parts Manufacturing Experience For 500+ Global Clients
Service Your Business Needs With Precise Die Casting Manufacturing Solution
The technology used by Sunrise Metals is among the most progressive die cast companies in China. Our Process automation produces rapid and well-structured parts, and optimize production methods for your projects. Our die casting facilities include:
- CAD and flow simulator software for engineering and design
- Automatic die-cast ancillary equipment
- Automatic electronic melting equipment
- CNC tool changer machining centers
- Auto finishing equipment
- Auto quality measuring machinery
Sunrise Metals is an ISO 9001 & IATF 16949 certified die casting supplier with reliable services including rapid prototyping, die casting tooling, aluminum die casting, CNC machining, and surface finishing. You will be assured of the quality of our process, material, and products using advanced QA tests and quality control methods in advanced laboratories.
Your Fantastic Die Casting Parts Coming From Sunrise High End Manufacturing Equipment
Die Casting Manufacturer Best Suited To Your Business
Sunrise Metal is a leading die casting company in China. We are the one-stop-solution for your die casting needs offering efficient and excellent services. We produce quality die casting parts for your manufacturing needs with state-of-the-art technology. These include automated machinery, CNC precision equipment, and precise measuring instruments.
- Advanced CNC Machining Equipment
- Premium Quality Measuring Instruments
No. | Name | Stroke | Q’ty |
1 | Mazak 7-axis turning&milling Machine | Ø658*1011MM | 1 |
2 | Mazak /Hass 5axis CNC machine | Ø850/Ø600 | 4 |
3 | 3-axis CNC machine center | 2000*1500MM | 1 |
4 | 4-axis CNC machine center | Ø250*800MM | 8 |
5 | 3-axis CNC machine center | 1000*600*600MM | 20 |
6 | CNC Lathes | Ø320*800/Ø610*1000MM | 2 |
7 | Sodick Wire cutting Machine | 400*400*200MM | 3 |
8 | EDM machine | 500*400*400MM | 2 |
9 | Surface grinder | 600*300*200MM | 1 |
No. | Name | Brand | Q’ty |
1 | CMM | Carl Zessis | 1 |
2 | CMM | SanYou | 1 |
3 | Spectrometer | China | 1 |
4 | Microscope | China | 1 |
5 | Projector | China | 2 |
6 | X-ray Detector | SANDT | 1 |
7 | Cleanliness Test Equipment | China | 1 |
8 | Leakage Test Equipment | China | 2 |
9 | Salt Spray Testing Equipment | China | 1 |
10 | Pneumatic Measuring Instrument | China | 2 |
11 | Hardness Testing Machine | China | 1 |
12 | Color Meter Machine | China | 1 |
13 | Thickness Testing Machine | China | 1 |
14 | Electronic Balance | China | 1 |
15 | Density Balance | China | 1 |
Get A Free Consultation
If you are looking for a Chinese die casting manufacturer, contact Sunrise Metal. When you have any hesitation or any design doubt on your aluminum die casting projects, Sunrise Metal Engineering Team can be your free consulter. Sunrise Metal gives suggestions on your die casting parts at 3 aspects:
1. Your design evaluation.
2. Feasibility analysis for mass production.
3. Project time and part’s cost-saving.
DIE CASTING MANUFACTURER: THE ULTIMATE FAQ GUIDE
Die casting is an important manufacturing process. Many engineering industries depend on die casting for their components. This great demand for die-cast products has brought about a large number of die casting manufacturers. But the scope of operation and the quality of services rendered by different manufacturers differ.
Many companies that want to do business with die casting manufacturers will need clarification on some aspects of their operation before making a long term business commitment. Below are the frequently asked questions on die casting manufacturers and their appropriate answers.
- What Is Die-Casting?
- What Do Die-Casting Manufacturers Do?
- Why Are Die-Casting Manufacturers Important?
- How Many Die Casting Manufacturers Are in China
- What Are The Features To Look For In A Good Die Casting Manufacturer?
- How Can I Get the Best Die Casting Manufacturer?
- What Are The Major Raw Materials Used By Die-Casting Manufactures?
- Which Manufacturing Processes Are Die Casting Manufacturing Using?
- What Are The Major Machines In A Die Casting Manufacturing Plant?
- Do Die-Casting Manufacturers Also Do Surface Finishing?
- Do Die-Casting Manufacturers Also Do Machining?
- Do Die-Casting Manufacturers Recycle Scrap Metals?
- What Are The Challenges Faced By The Die-Casting Manufacturer?
- How Do Die-Casting Manufacturers Ensure Environmental Conservation?
- What Are The Safety Precautions Die Casting Manufacturers Must Take?
- How Are Die Casting Products Designed
- Why Do Die Casting Manufacturers Need A 2D Drawing After Providing Them With A 3D Cad?
- Do All Die Casting Manufacturers Offer Prototyping Services?
- Do Die Casting Companies Sign A Non-Disclosure Agreement For Clients’ Special Designs?
- What Is The Minimum Quantity That Can Be Ordered From a Die Casting Factory?
- What Is The Maximum Weight Of Products Produced By Die-Casting Manufacturers?
- What Is The Minimum and Maximum Thickness Of Products Produced By Die-Casting Manufacturers?
- How Do Die-Casting Manufacturers Ensure That Manufactured Parts Are Of Good Quality?
- How to Optimize the porosity for Die Casting Manufacturers?
- How Does Die Casting Manufacturer Do the Leakage Test for Die Casting Parts?
- Why Sunrise Metal is your No. 1 Choice for Die Casting Manufacturer in China
What Is Die-Casting?
Die casting is a manufacturing process used for producing components by forcing metal in a molten state, under high pressure, and at a high speed into a prepared mold so that when the metal solidifies, it takes the shape of the cavity of the mold.
Die casting pressure ranges between 150 to 1200 bar and the speed can be as high as 54km/h
In many die casting manufacturing companies, the process is fully automated.
In this case, a single mold can be used by die casting manufacturers to produce a high number of identical components within a very short time, and at a very low unit cost.
All components produced by die-casting using a mold has the same shape and quality, making the process unique among metal forming processes.
Die casting can be used to produce automobile parts, electrical equipment, medical equipment, machine components, among many others.
Because die casting involves the melting of metals, metals, and alloys with low melting points are most commonly used.
Common metals that are being die-cast by die casting manufacturers are aluminum, zinc, magnesium, copper, lead, tin, and their alloys.
What Do Die-Casting Manufacturers Do?
The major process involved in die-casting is to produce mold, melt the metal, and cast the component, but many die casting manufacturers do a lot more than that,
Standard die-casting manufacturers provide a one-stop solution to the production of die-cast components.
Therefore, die casting manufacturers design parts, produce mold, die-cast the component, offer CNC machining, and surface finishing.
Many die-casting manufacturers will also facilitate the delivery of your die-cast products.
- After the component design has been concluded, the die casting manufacturer will prepare a mold as a once-off part of the project.
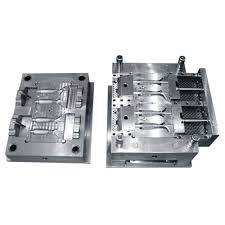
- Mould is a cavity inside which the molten metal is poured. The mold will be used to die-cast the components by pouring the molten metal into it at high pressure, but the job is not ready for delivery even after the part is formed.
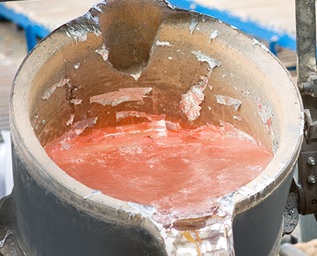
- Some parts may still require machining, but even after that, die casting manufacturers may still need to finish the surface.
- Surface finishing gives the part the desired appearance and may also be used to impact some properties in the die casting. It may include chromate, shot blasting, plating, anodizing, powder coating, and wet painting.
Why Are Die-Casting Manufacturers Important?
- Die casting is the most effective manufacturing process for many engineering components. The process can produce many intricate parts that other manufacturing processes cannot produce. It is also cheaper and faster than other manufacturing processes and requires little machining and surface finishing.
- Die casting can be used to produce a large number of identical components within a short time using a single mold and at a very low unit cost. If not for die-casting, many machines and automobile parts would have been difficult to produce, and the cost would have been very high.
- Once a mold is prepared, it can be used over and over, making the process cost-effective.
- Parts produced by die casting with the same mold looks exactly the same and are of the same quality.
- Die casting produces parts of high quality and great precision, hence when quality and precision are required, die casting is the best choice. Die casting is also able to produce customized design than other metal forming processes.
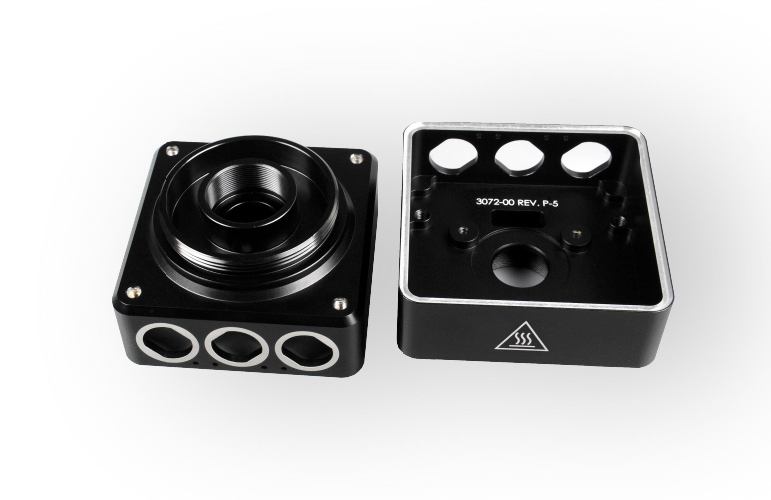
- Many engineering industries like the automobile industry depends a lot on die casting to get their components. And medical pieces of equipment that require accuracy and precision also depend on this forming process to get the exact dimension required.
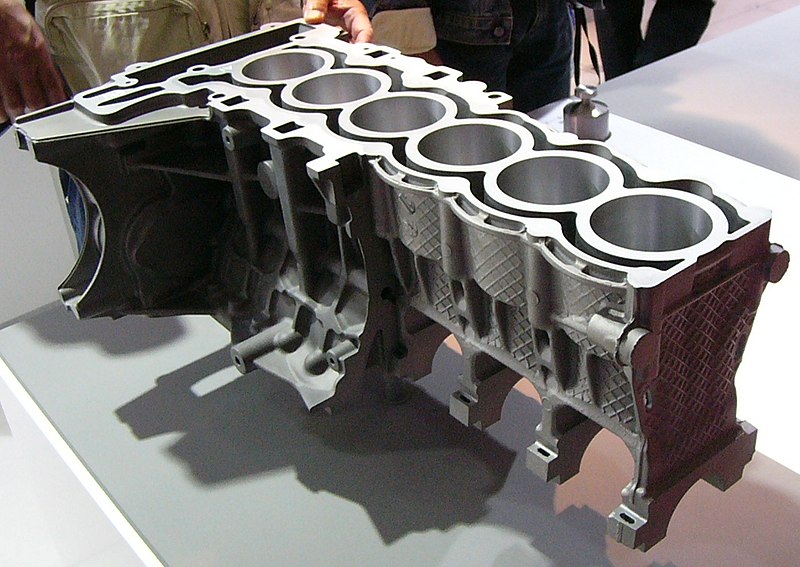
- Die casting is also environmentally friendly.
- Many die casting manufacturers provide a one-stop solution to component parts of automobile companies.
How Many Die Casting Manufacturers Are in China
It is difficult to say the exact number of die casting manufacturers in China as more die casting companies are being continuously registered.
However, China is the leading die casting producer in the world, and the number of die casting manufacturers may be close to ten thousand. About 45% of the total die casting products are produced in China.
Over 4 million tons of die-casting parts are annually produced in China, and the production rate is increasing by as much as 10% per annum.
What Are The Features To Look For In A Good Die Casting Manufacturer?
Features to look for in a good die-casting manufacturer include the following:
Availability of Modern Equipment
Good die casting manufacturers have modern equipment that can deliver quality projects and can produce a large number of components within a short time.
Ability to Deal With Several Raw Materials
A good die casting manufacturer must be able to work with any alloy that fits the functionality of the component most.
Ability to Provide All Services Related to Die Casting
Good die casting manufacturers are also one-stop solution centers for all services related to the production of the die-cast part.
Quality of Job
The quality should be the most important factor to consider. Good die casting manufacturers deliver quality jobs.
Timely Delivery
Speed of production is also very important as die-casting usually involves a large number of components. Good die casting manufacturers deliver a large volume of jobs within a short time.
Good Communication with Clients
The die casting process involves many steps from design to choice of material to production, finishing, and delivery, hence good communication with the client during the process is essential.
Good die casting manufacturers ensure effective communication with their customers.
Honesty and Cost Effectiveness
Good die casting manufacturers will also be open and honest with their pricing system and assist the client in making decisions that will be cost-effective.
Research and Development
As the die casting industry is rapidly evolving, good die casting manufacturers are paying good attention to research and development.
How Can I Get the Best Die Casting Manufacturer?
There are many die casting manufacturers in China, but they are of different scales and expertise.
To get a good die casting manufacturer, you can follow the following steps:
- Look for die casting manufacturer with experience, modern equipment, and skilled workers.
- Talk with top die casting manufactures and decide which one can effectively deliver your task and is ready to assist you on your project.
- Visit die casting factories and see other jobs and the modes of production of different manufacturers.
- Also, compare the prices and quality.
- You can also read recommendations and reviews from customers as well as from reliable online content.
What Are The Major Raw Materials Used By Die-Casting Manufactures?
Die casting uses low melting metal and metallic alloys.
The most commonly cast materials are nonferrous metals, usually aluminum, zinc, copper, tin, magnesium, lead, and alloys.
The choice of material depends on the application of the part being cast.
Aluminum
Aluminum and its alloys are the most commonly cast metal. Aluminum has many advantages as a die-cast raw material, which include the following:
- Lightweight
- Low melting point
- High resistance to corrosion
- High thermal conductivity
- High electrical conductivity.
- The lightweight of aluminum makes it to be efficient to assist in the automobile industry as it contributes to a reduction in fuel consumption.
- Aluminum is also easy to recycle hence protecting the environment and saving cost.
- Aluminum also maintains dimensional stability with thin-walled components.
- Aluminum die-cast products also require less surface finishing.
However, one of the major disadvantages of using aluminum is that it can shrink or crack at high temperatures; therefore, copper or silicon is usually added as an alloy to prevent this defect. Another disadvantage is that Aluminum is more expensive than most other materials used in die-casting
Zinc
Zinc components are easy to form. Zinc also has a low melting point, and it is cheaper than aluminum.
Magnesium
Magnesium is another raw material that is commonly used by die casting manufacturers.
- Lightweight
- High resistance to corrosion
- High conductivity
- Dimensional stability
- High rigidity
- It can be recycled
- It can withstand high temperature and working pressure.
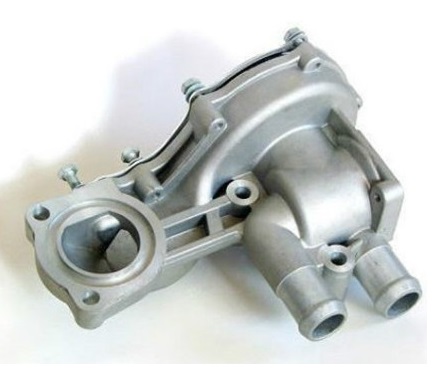
Which Manufacturing Processes Are Die Casting Manufacturing Using?
Die casting involves four major processes. They are:
Die Preparation
Before pouring the metal, the die is prepared. Die preparation involves lubricating the mold cavity. This is usually done by spraying. The lubrication facilitates the easy removal of the casting at the end of the process. The lubricant also helps in regulating the die’s temperature.
Filling
Once the die is prepared, it will be filled with molten metal. The filling is done at high pressure. The mold will be completely filled, and the pressure will be kept constant until the metal solidifies completely taking the shape of the mold cavity. The filling is done at a high speed to ensure that it completes before solidification begins.
Ejection
After solidification, the die will be open, and the solidified metal usually called shots will be ejected with the aid of ejector pins.
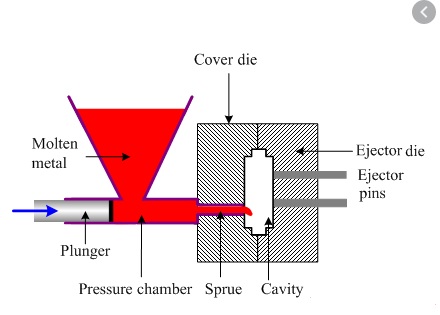
- Shake out
Shake out is the process of separating the shots from other products. The scraps that can be attached to the casting include flash and runners. These scraps can be separated by grinding, sawing, and the use of hydraulic or power press.
After the casting process is complete, the as-cast product will be inspected for defects and necessary correction. The defect can include misrun, cold shuts, shrinkage, porosity, hot tears, and flow marks.
What Are The Major Machines In A Die Casting Manufacturing Plant?
Die casting machines available today can be classified into two – hot chamber machines and cold chamber machines.
Hot chamber machines
Hot chamber machines melt the metal and then transfer the molten metal into the die.
The whole cycle takes a very short time; hence it is fast and convenient, but it is only efficient for low melting metals and non-aluminum alloys.
It is therefore commonly used by die-casting manufacturers for casting products like tin, zinc, and lead-based alloys.
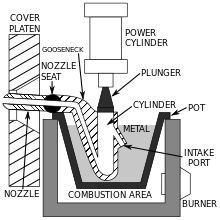
Cold chamber machines
Cold chamber machines are not used for melting metals inside a die casting machine, rather, the metal is melted in a furnace and then transferred into the machine. Here, the molten metal is forced into the mold cavity with a pressurized plunger.
This machine is used for casting aluminum-based alloys as well as copper, magnesium, and some zinc-based alloys.
The major disadvantage of this process is that it takes time, as molten metal still needs to be transferred from the furnace.
Apart from these two major types, there are still some variations of the machines.
Among the variations are semi-solid molding machines which are used to produce semi-solid billets and squeeze casting machines which are used for producing casting with lower porosity.
Casting machines come with different levels of automation.
Modern casting machines are fully automated with every step from die preparation to shaking out.
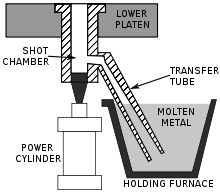
Do Die-Casting Manufacturers Also Do Surface Finishing?
Although modern die-casting machines can produce as-cast parts with great surfaces, yet many parts will still need some finishing before delivery is made.
Die-casting manufacturers always deliver ready to use parts; therefore, after production, surfaces of die-cast parts will be deburred, coated, finally coated, or anodized for beautification, prevention against corrosion, and improved wear resistance.
Deburring
Deburring involves smoothing the edges and removing burs from the cast metal.
Different die-casting manufacturers use different types of machines for this post-production process leading to different qualities, but top die-casting manufacturers ensure their products are completely free of all burs, debris, and flashes, and have smooth round edges.
Deburring can also be used to enhance polishing and coating adhesion.
Conversion Coating
Die-casting manufacturers usually follow deburring with conversion coating.
Conversion coating helps to remove any chemical substance that may be left on the die-cast product and prepare the surface ready for final painting.
In many cases, the conversion coating may serve as the final surface finishing for the product.
Many die-casting manufacturers also combine conversion coating with other functional requirements like decorative appearance, corrosion resistance, and conductivity.
The most commonly used conversion coating method by modern-day die casting manufacturers is chromium conversion coating.
Trivalent clear chromium is environmentally friendly and is recommended by many agencies, hence is the first choice of die-casting manufacturers.
Final Coating
It is not always necessary to coat die-casting, but it might be done for reasons like decorative appearance, corrosion prevention, and insulation.
Die-casting manufacturers use different types of coating depending on the parts and the scale of production of the manufacturer.
The coating could be powder coating, liquid painting, or electroplating.
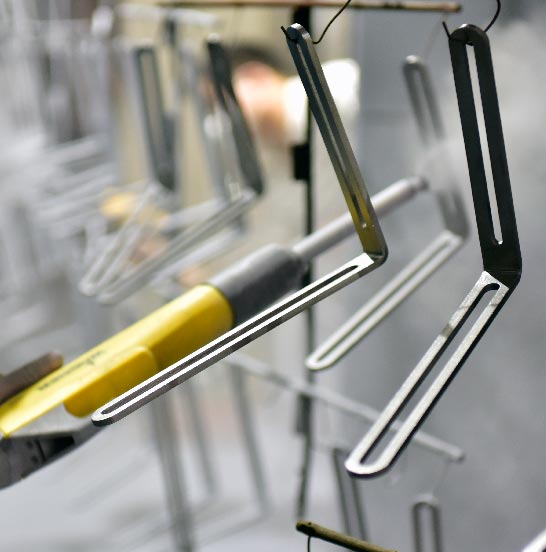
Anodizing
Anodizing is the process of depositing a protective layer on the surface of the die casting
Anodizing can be done to protect the surface against corrosion, to harden the surface or just for beautification
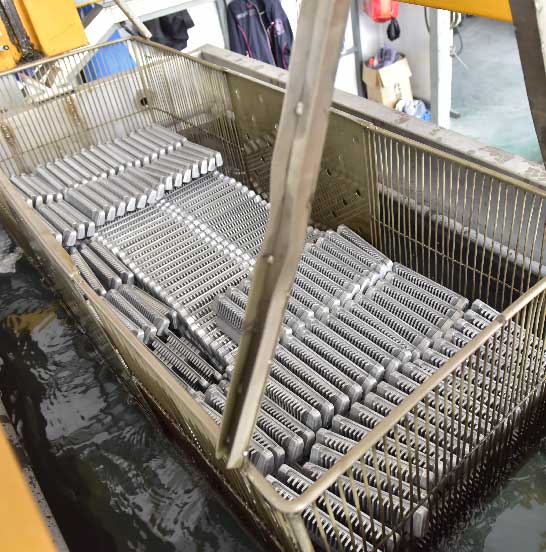
Do Die-Casting Manufacturers Also Do Machining?
While die casting is the process of melting metal to a molten state and pour it into a mold to solidify, forming the shape of the mold cavity, CNC machining involves shaving metal to a desirable shape.
Both are component forming processes, but they are two different things.
However, most die-casting manufacturers offer CNC machining as well.
Also, after die-casting, some components still require machining; hence it is necessary for die-casting manufacturers to include machining in their services.
Machining can be needed after die casting to get tighter tolerances or produce features that die casting cannot produce.
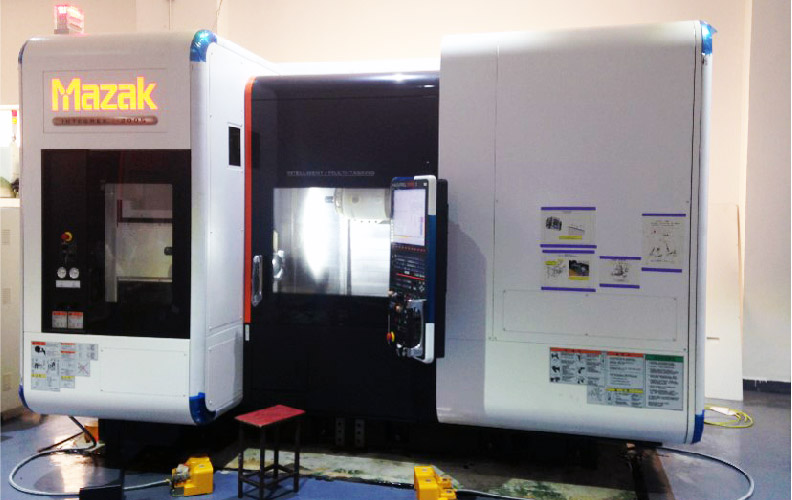
Do Die-Casting Manufacturers Recycle Scrap Metals?
The simple answer is yes.
In fact, the bulk of the metals used in die-casting are from recycled scraps.
Aluminum die-casting is the most common form of die-casting, and aluminum is 100% recyclable.
The same can be said of many other metals and alloys used in die-casting.
By recycling metal, die casting protects the environment from waste, reduces the need for mining, and reduce the cost of production.
What Are The Challenges Faced By The Die-Casting Manufacturer?
Like any other industry, de-casting manufacturers also have their challenges. They are listed below.
- Capital: The capital required to set up a standard die-casting company is high, and not many manufacturers can afford to set up the best equipment, notwithstanding, there are many die-casting manufacturers with high-quality equipment.
- Trade War: The trade war between countries may harm the die-casting manufacturer as the highest concentration of the manufacturers are in Asia.
- Technology: The rapid change in auto-mobile technology may lead to a need for a less complex auto-mobile part and reduced demand for die-casting products.
- Workforce: The workforce is another challenge for many die-casting manufacturers, as the process requires highly skilled labor; however, top die-casting manufacturers have a good policy for training their staff.
- Accidents: Accidents are another challenge that die casting industry is facing. The rate of accidents in die casting factories is higher than that of other engineering fields. Also, the high temperature of melting the metal might create a health hazard to workers. Notwithstanding, top die casting manufacturers have good safety precautions in place to prevent accidents and protect their staff.
How Do Die-Casting Manufacturers Ensure Environmental Conservation?
Die-casting generally is an environmentally friendly process.
- It reduces energy consumption by using a single mold repeatedly, therefore reducing the materials involved in the production.
- Raw materials used in die-casting are also recyclable, hence protecting the environment from scraps and excessive need for mining.
However, the production method and practices adopted by each die-casting manufacturer play an important role in the impact of the process on the environment.
Top die-casting manufacturers are following the standard environmental management system for the metal casting industry to ensure the protection of the environment. The protocol includes:
- Proper disposal of waste
- Efficient use of energy
- Recycling of raw materials
What Are The Safety Precautions Die Casting Manufacturers Must Take?
The rate of accident in the die-casting industry is higher than the rate in many other manufacturing industries; however, top die-casting manufacturers have standard safety policy that ensures their staff and visitors are perfectly safe.
- Die-casting manufacturers always ensure that their staff is properly trained on safety protocols and accident prevention before resuming to duty.
- Top manufacturers pay good attention to the ventilation of their workplace, especially places where metals are being melted. This prevents the build-up of fumes and suffocation
- They also ensure all safety equipment like protective gear, safety glasses, safety shoes, and ear protection are available and used by staff and visitors.
- All machines are always being checked to ensure they are perfectly safe for use.
- Fixed guards are provided to create barriers to moving parts of machines. These prevent workers from accidentally putting their hands in the machine
- To ensure all the safety precaution put in place are functioning properly, top die casting manufacturers are regularly carrying out inspections of safety devices
- Staff are also being constantly monitored to ensure they are complying with the safety protocol
- There is also first aid equipment as well as provision for emergency always on the ground so that any accident can quickly be attended to.
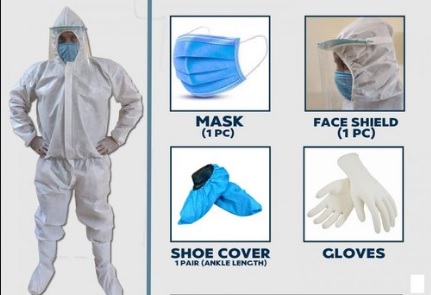
How Are Die Casting Products Designed
There are many factors to consider when designing die casting products; these include:
Wall thickness: Thin-walled parts are usually designed with ribs and bosses to give them extra strength. Uniform wall thickness is usually maintained in the design of die casting. This is to ensure the liquid metal flow properly and consistently.
Fillets and radii: they are used together with ribs and bosses; these are to flatten sharp corners, strengthen the part, allow molten metal to flow seamlessly, and make finishing easier.
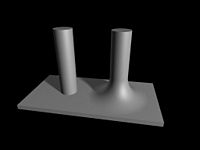
Draft angle: It is added into the design to prevent shrinkage and enhance the easy removal of the die casting. Draft is a slope on the walls of the die casting, adding it to a die casting design will prevents the molten metal from sticking to the mold and therefore increases the surface quality and reduces the cycle time. Drafting is also added to holes and window features to prevent their perimeter from sticking to the die during solidification.
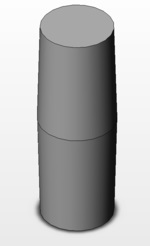
Pockets: they are designed in the solid section for lightweight die casting. This will ensure the weight of the component is reduced and that the cycle time is also reduced.
Parting lines: they are located in areas that do not have an important cosmetic requirement and tolerance control.
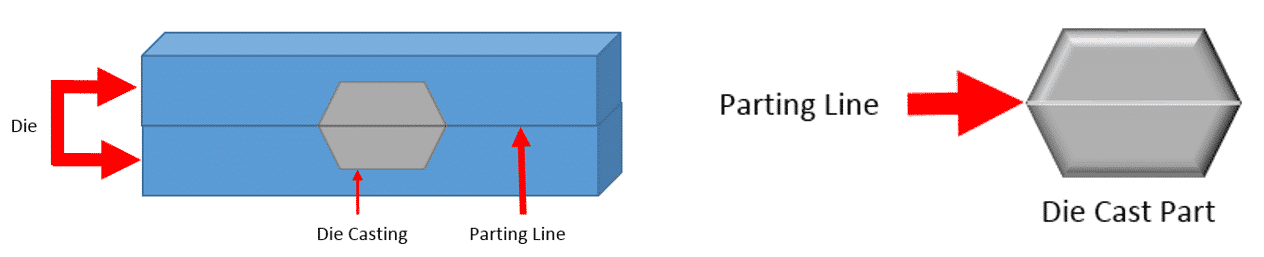
Undercut: The opening direction of the mold is designed not to have any undercut. If undercut must be in the die casting features, then the sliding core will also be added to the tooling.
Bridges: Bridges and cross feeders are added to the design that has an obstruction that can restrict the proper flow of the liquid metal.
Tooling Material: It is also important to critically decide the material for making the dies. If the cycle will be up to 1,000,000, then low carbon steel is preferred, this is because it has a high resistance to cracking. For the cycle between 100,000 to 150,000, high-grade tool steel is usually used.
Surface finishing: this is also important to take into consideration during the design of the die-casting parts. One of the ways of reducing surface finishing is by designing edges such that they are hidden within the product assembly so that edge polishing will no longer be necessary.
Die-casting manufacturers can discuss with clients ways to design parts to minimize surface finishing and reduce cost.
Why Do Die Casting Manufacturers Need A 2D Drawing After Providing Them With A 3D Cad?
One of the most important aspects of die casting design is tolerance, and 3D Cad does not contain tolerance.
Therefore to get all the information needed for die casting, a client must supplier the die casting manufacturer with a drawing that includes tolerance and other design information.
3D Cad contains all the dimensional information and can be viewed from all angles, yet die casting manufacturers need more.
This is the reason every die casting manufacturer will request a 2D drawing.
The 2D drawing usually contains the following information:
- The dimension of the component
- The design tolerance
- Component material
- Component color
- Location of holes
- Sizes of holes
- Type of thread to be used
- Radius of corners
- Surface flatness
- Required surface finishing
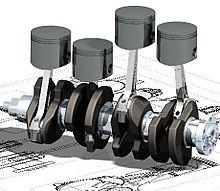
Do All Die Casting Manufacturers Offer Prototyping Services?
Because of the low volume that prototyping involves, the unit cost is way more expensive than the typical die casting. However, prototyping is an essential part of die casting.
Prototyping involves developing ideas and transforming them into a physical product. Therefore, prototyping is among the first step in design.
- Because it requires more than being able to die cast the product, but also to be able to design and develop it, therefore, not all die casting manufacturer has all the required resources for prototyping. However, most top die casting manufacturers in China also offer prototyping services.
- The time spent on prototyping by different manufacturers also differs.
- Some die casting manufacturers will just turn your design drawing into products exactly the way you give it to them without making any input. Some will first review the design, meet with the client, and make suggestion, do all necessary corrections, and modification to the drawing before they finally develop it into a physical product.
- But a good die casting manufacturer will not stop at reviewing and modification before production, but even after the product has been developed, will also do testing and product review and still make further suggestions for perfection.
- Good and experience die casting manufacturers will give you quality prototyping services within a short period.
Do Die Casting Companies Sign A Non-Disclosure Agreement For Clients’ Special Designs?
Yes, die casting manufacturers understand how sensitive some design information could be and will surely keep them secret.
However, it may be necessary to sign a non-disclosure agreement and die casting manufacturers will not object to that.
In most cases, the die casting manufacturers already have a non-disclosure agreement form and enter into the agreement with the client. If a client insists on using his form, manufacturers will surely have no objection.
What Is The Minimum Quantity That Can Be Ordered From a Die Casting Factory?
There might not be a specific number, but die casting is a process that is effective for high volume production.
There is a lot of fixed cost involved in die casting, therefore the higher the quantity, the lower the unit cost.
Components that are not required in large quantities are usually produced using other metal forming processes.
Many die casting manufacturers only over B2B, therefore deals with a high quantity of production.
Each die casting manufacturer will set the minimum quantity of job it will accept.
What Is The Maximum Weight Of Products Produced By Die-Casting Manufacturers?
The maximum weight of a material that can be die-cast depends on the material used for the die casting.
Aluminum is the most common material used in die casting, and it can be used for a component up to a maximum weight of 32 kilograms (70 pounds).
A zinc die-cast components can be up to 34 kg (75 lb), Magnesium can support a maximum of 20 Kg (44 lb), and the maximum allowable weight for a brass die-cast part is 4.5 Kg (10 lb)
However, for the best performance, the die-cast product should not be more than 10 kg (22 lb)
What Is The Minimum and Maximum Thickness Of Products Produced By Die-Casting Manufacturers?
For products manufactured by the Die-casting process, the typical wall thickness can range between 0.040 inches to 0.200 inches.
The wall thickness depends on factors like:
- The alloy used
- The size of the part
- The configuration of the part
- The function of the part.
How Do Die-Casting Manufacturers Ensure That Manufactured Parts Are Of Good Quality?
Die casting manufacturers to ascertain quality products in different ways.
To start with, they always ensure the job is properly designed and the die is correctly produced.
All the equipment is also checked to be sure they are working properly.
Also, spectrometric analysis and density measurement can be performed on the liquid metal to ensure it has the exact composition and properties needed to produce the quality part before the casting begin.
During production, the die-cast products are randomly examined for defects and tested for quality.
In some cases, all products are tested for quality before delivering, so that product with low quality did not leave the factory at all.
Testing of the die-cast part includes a visual examination of the part, measurement with a digital caliper and coordinate measuring machines to ensure it meets up with the dimensional specification and Mechanical testing to ascertain the strength and other important qualities needed from the die casting.
Pressure testing is done to check for leakage. While X-ray radiography is used to check for the sand hole and porosity inside of die casting parts.
Top die casting manufacturers always ensure that the die-cast parts meet up with the quality requirement before delivering to their clients.
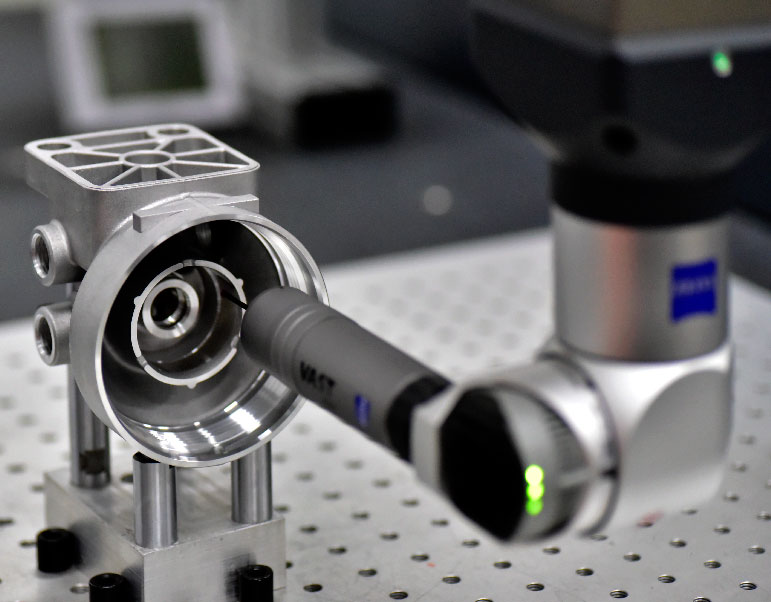
How to Optimize the porosity for Die Casting Manufacturers?
Porosity is usually caused by a defective running system and irregular cooling of the molten metal.
Therefore, porosity can be minimized in die casting by ensuring the running system is specifically up to the requirement.
The problem with the design of mold can allow gas to be trapped in the casting, which may also lead to porosity. Gas porosity can be minimized by a proper mold design.
Adding nitrogen into the molten aluminum before pouring it will also eliminate gas porosity.
HIPing (Hot Isostatic Pressing) is a process of heating die –cast part in a furnace with an atmosphere of inert gas to remove the dissolved gas.
However, many design features can help to minimize the occurrence of porosity.
There is software that can be used to predict part of the die-cast component that is more vulnerable to porosity; this can help in improving the design to prevent it.
Ensuring uniform wall thickness will ensure the liquid metal flows properly and cools uniformly, hence prevent porosity.
Molds should also be designed in such a way to avoid sharp corners and pockets, to facilitate the escape of air.
The addition of silicon to aluminum die casting will lower porosity caused by shrinkage, however, this depends on the composition of the aluminum alloy, so that the silicon addition will not significantly change its properties.
Casting in an inert gas atmosphere will also prevent trapping of air and hence prevent porosity.
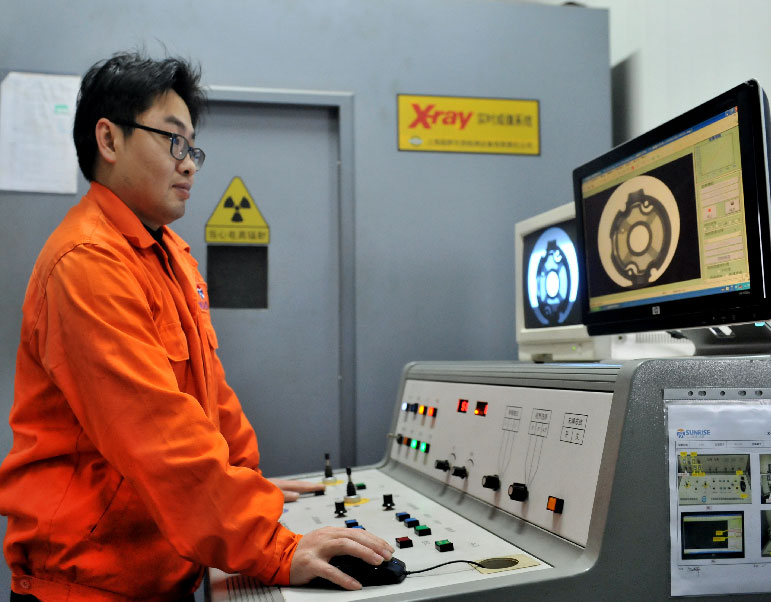
How Does Die Casting Manufacturer Do the Leakage Test for Die Casting Parts?
Different die casting manufacturers use different ways to test for leakage. Among the most common ways are water check and gas inspection.
To check for leakage using a water test, first, seal all the holes in the casting and fill it with red gas. Then put the casting in the water and check for bubbles. If no bubble forms, then the casting is not leaking.
Why Sunrise Metal is your No. 1 Choice for Die Casting Manufacturer in China
Sunrise Metal is a one-stop center for all die casting related work including rapid prototyping, mold design & making, die casting, CNC machine, and surface treatment. We have been in the business of aluminum die casting for over 10 years.
Sunrise metal has four facilities in China; all are well equipped with modern types of equipment and employs 182 full-time workers.
All engineers of Sunrise Metals are professionals with many years of experience in die casting and mechanical engineering.
If you choose Sunrise Metal to do your die casting projects, you can be confident of quality projects, timely delivery, and cost-effectiveness. We will also discuss with you all possible ways to reduce costs and maximize quality through the process from design to delivery and ensure the project meets your standard.
Sunrise Metal Die Casting Factory