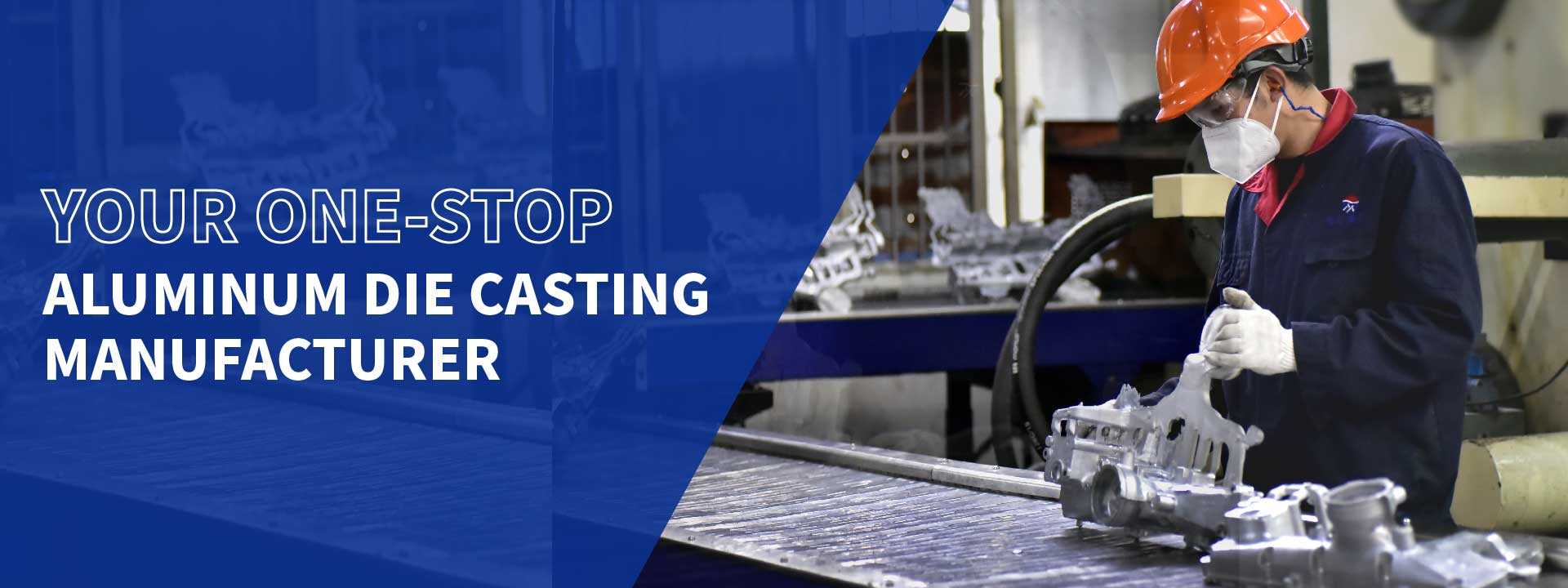
Aluminum Die Casting Trustworthy Supplier-Sunrise Metal
- Sunrise Metal is an ISO9001 and IATF16949 certified aluminum die casting supplier, located in Shanghai, China.
- With 4 dedicated facilities and 182 full-time employees, we focus on one-stop Die casting aluminum manufacturing for over 10 years. Sunrise metal welcomes your high-mix, low volume projects.
- Sunrise Metal’s rapid tooling technology and fast production system can save your ½ lead time. This helps us to achieve 100% on-time delivery goal for you.
2500+ Aluminum Die Casting Parts Manufacturing Experience For 500+ Global Clients
Outstanding Sunrise Aluminum Die Casting Manufacturing Capability to Reach New Possibilities
Our strong engineering team possesses professional die-casting aluminum & mechanical background. Most of our engineers have over 10 years of experience. They can design mechanical parts and provide technical support with DFM & PPAP and etc.
Sunrise Metal offers a 1-stop solution for Aluminum Die-casting projects, including DFM, Rapid prototyping, molding, Die casting, CNC machining and various surface treatments, etc.
With our high-level measurement lab, We execute strict inspections to our aluminum die casting parts, from raw material to out-going parts. Sunrise Metal guarantees all parts are up to your requirements.
Aluminum Die Casting Parts Made With Sunrise Metal High-Precision Manufacturing Equipment
On-Going Die Casting Aluminum Projects
Sunrise Metal has been delivering comprehensive aluminum die casting manufacturing solutions for many years. These projects are on-going in our production.
- Experienced Team
- Advanced Machining Equipment
- Global Clients
- Premium Quality
- Fast Delivery
Our experienced and passionate team is ready to make your design vision into reality.
No. | Name | Stroke | Q’ty |
1 | Mazak 7-axis turning&milling Machine | Ø658*1011MM | 1 |
2 | Mazak /Hass 5axis CNC machine | Ø850/Ø600 | 4 |
3 | 3-axis CNC machine center | 2000*1500MM | 1 |
4 | 4-axis CNC machine center | Ø250*800MM | 8 |
5 | 3-axis CNC machine center | 1000*600*600MM | 20 |
6 | CNC Lathes | Ø320*800/Ø610*1000MM | 2 |
7 | Sodick Wire cutting Machine | 400*400*200MM | 3 |
8 | EDM machine | 500*400*400MM | 2 |
9 | Surface grinder | 600*300*200MM | 1 |
No. | Name | Brand | Q’ty |
1 | CMM | Carl Zessis | 1 |
2 | CMM | SanYou | 1 |
3 | Spectrometer | China | 1 |
4 | Microscope | China | 1 |
5 | Projector | China | 2 |
6 | X-ray Detector | SANDT | 1 |
7 | Cleanliness Test Equipment | China | 1 |
8 | Leakage Test Equipment | China | 2 |
9 | Salt Spray Testing Equipment | China | 1 |
10 | Pneumatic Measuring Instrument | China | 2 |
11 | Hardness Testing Machine | China | 1 |
12 | Color Meter Machine | China | 1 |
13 | Thickness Testing Machine | China | 1 |
14 | Electronic Balance | China | 1 |
15 | Density Balance | China | 1 |
We are committed to ensuring the right quality & on-time delivery. We always work on customer satisfaction and establish a superior business with our global customers.
Get Our Team Technical Support
If you are looking for a China aluminum die casting manufacturer, contact Sunrise Metal. When you have any hesitation or any design doubt on your die casting aluminum projects, Sunrise Metal Engineering Team can be your free consulter. Sunrise Metal gives suggestions at 3 aspects:
1. Your design evaluation.
2. Feasibility analysis for mass production.
3. Project time and part’s cost-saving.
Contact us now, to see how we can help you with your Aluminum Die-casting projects.
ALUMINUM DIE CASTING- THE ULTIMATE FAQ GUIDE
Aluminum die casting is a manufacturing process that produces highly defined and durable metal parts using high-pressure systems. At Sunrise Metal, we ensure the best die casting experience, with state-of-the-art facilities and professional workforce.
The best aluminum die cast tooling and production methods are employed to serve a vast array of industries. These span from automobiles to medical equipment, and make use of efficient high-volume die cast production.
- What is die casting?
- What are the different types of die casting?
- What is die cast aluminum?
- Why is the die casting process used?
- When did die cast manufacturing start?
- What is the difference between cast aluminum and die cast aluminum?
- What kind of products are made from die casting?
- What are the advantages of aluminum die casting?
- What are aluminum die casting parts?
- Are there any concerns of die casting that must be taken into consideration?
- What are casting defects?
- Why is aluminum used in die casting instead of other cast alloys (e.g. Zinc and magnesium)?
- Which aluminum die cast alloys are majorly used by manufacturers?
- Is die cast aluminum strong?
- Can die cast aluminum be anodized?
- What are the highest operating temperatures that aluminum can withstand?
- Which other materials can be used for casting?
- How to choose the right die casting alloy?
- How does aluminum die casting work?
- What are the main steps in the casting process?
- What types of dies can be used in the casting process?
- What is the difference between gravity die casting and pressure die casting?
- How does aluminum die casting compare with sand casting?
- How does aluminum die casting compare with investment casting?
- What is the difference between die casting and injection molding?
- Which materials are most suitable to be used as molds for the die casting process?
- Are there any precautions that need to be taken while using aluminum die casting molds?
- What is the best way to design a premium die casting part?
- What kind of mechanical equipment is used for producing die casting parts?
- What are the key structural parts design points to be taken care of during the die casting process?
- How can you weigh out the pros and cons of screw machining vs die casting?
- What kind of product segmentation is associated with aluminum die casting parts?
- What are the different die casting applications that make it a lucrative option for industries?
- Which aluminum die casting components can be used in electric vehicles?
- How does the use of aluminum casting improve fuel efficiency for the transportation and automobile sector?
- In order to optimize manufacturing, how does a company choose between conventional die casting and multi-slide die casting?
- a firm achieve significant cost savings and high production speeds as a result of choosing the right die cast method?
- What are main cost drivers for the casting method?
- How is the material cost optimized during the process?
- What are the advantages of a fully automated aluminum die casting process?
- What are the best methods of building casting prototypes and why?
- What are the differences between die casting and CNC machining?
- What is the best way to design a die cast component without compromising on ROI and scalability?
- How does the use of aluminum in the die casting process help achieve high returns?
- Why should I opt for aluminum die casting services by Sunrise Metal?
- What kind of engineering techniques are employed by Sunrise Metal to ensure efficient and cost-effective mass production?
- Which machines are used in high pressure die casting production processes?
- How can small and medium sized companies in the automotive/aerospace/industrial/ communication/medical/marine sector benefit from Sunrise Aluminum Die Casting services?
- What are some of the die cast tooling capabilities offered by your die casting company?
- Does die cast aluminum rust?
- What are the advantages of non-destructive inspection for die casted metals?
- Why is destructive inspection for die casted aluminum preferred over non-destructive inspection?
- How is scrap reduced in aluminum die casting?
- Why is there a limitation in the height and weight of components prepared through die casting methods?
- How can the automotive industry benefit from aluminum die cast products?
- What are the advantages of using aluminum die cast products in the telecommunication industry?
- What variations of the basic die casting process can be applied?
- What quality systems are followed by Sunrise Metal to ensure products are in-line with international standards?
- What are some of the applications of pressure die casting?
What is die casting?
Die casting is a process that is used to cast metals by forcing molten metal into a die or mold cavity. This is done under high pressure and at a high filling speed. It is suitable for atomized and high-efficiency production in the industrial sector.
The process mostly uses non-ferrous metals such as aluminum, copper, magnesium, and zinc. It involves a furnace, metal alloy, die casting machine, and die. These dies are created with hardened steel machined to the net shape of the die-cast parts.
With this method, thousands of castings can be produced using only one mold. Products are made to a high degree of accuracy, making it highly efficient for industrial use.
Die casting parts are used by a wide range of industries including automobile, household appliances, aerospace, communication, and medicine, among others.
What are the different types of die casting?
There are several types of die casting that can be adopted to suit different purposes.
Hot chamber die casting
This type uses metals with low melting points and high fluidity such as zinc and magnesium alloys, along with copper and lead.
The hot chamber casting option is best for alloys that prevent metal pots and cylinders from eroding. It immerses the cylinder chamber of the injection mechanism in molten metal.
This direct immersion facilitates a quick mold injection but results in high rates of corrosion as well. A gooseneck metal feed mechanism then delivers the molten metal into the die cavity.
Cold-chamber die casting
Die casting method using a cold chamber is best suited for alloys like magnesium and aluminum with a high melting point, as well as corrosive properties.
In this process, the molten metal is poured into a cold chamber and pushed into the die using a hydraulic plunger.
This is done as a single shot operation and reduces the time of contact between the molten metal and injector parts. Machine corrosion is also kept at a minimum due to this production design.
Sunrise metal offers high-level manufacturing capability during the aluminum die casting production process, with high precision. It is especially suitable for industrial customers with low levels of demand. If you are looking for a China aluminum die casting supplier, Sunrise Metal is your right choice.
What is die cast aluminum?
Die cast aluminum is produced by melting metals under high pressure in mold cavities. This can be done using the cold chamber die casting method.
Metals are hardened to obtain desired shapes and can be prepared in several different sizes, shapes, and thicknesses with a high level of accuracy.
For aluminum die casting, Sunrise Metal uses aluminum alloys including ADC12, A380, ALSi12 among others, and merges quality with optimum pricing to provide the best options to consumers worldwide.
Aluminum die casting is now a popular industrial process that assists in mass level production of aluminum for sale as a metal, as well as machine parts. Using modern technology and efficient die cast tooling and production methods, high quality results can be achieved.
Why is the die casting process used?
Die casting is used due to its superiority over other manufacturing processes.
Manufacturing of gears with high degree of accuracy and repeatability is achieved through die casting. It can produce complex net shapes with even complex internal structures.
This minimizes the assembly operations as it can also provide a combination of multiple parts into a single part. Labor cost is also reduced through die casting.
A fully automatic, high productivity, high volume production is the major role of die casting. Some of its major benefits include, but are not limited to:
- Scrap reduction
- Shorter production time
- Better product life
- High Dimensional Stability of tools
Many manufacturing companies employ die casting methods for mass production. As a one-stop aluminum die casting china manufacturer, Sunrise Metal has perfected the art of die casting manufacturing and has become capable of producing high-quality aluminum die casting products.
When did die cast manufacturing start?
Die cast manufacturing has been progressing since the 19th century. The origin of the process goes back to the Soss company which used it for the first time to cast print type. Madison Kipp corporation first introduced automatic die casting machines in the market in 1928 with cold parts attachments in 1932.
A vertical die casting machine was developed in the 1960s which was less widely used. It reduced the chances of air entrapment in the metal feed system. The figure below shows the vertical setting of the die casting machine.
By this time, the printing machine was not the only machine that was being developed by die casting methods. Due to its wide applications, appliances and other consumer goods were being produced in the loop too. This era gave pace to the modernization of die casting machines and gave us the die casting machines that we use today.
What is the difference between cast aluminum and die cast aluminum?
Cast aluminum and die cast aluminum are two different processes of manufacturing aluminum products.
Cast aluminum is a process where aluminum is melted and is poured into a mold to rest. The aluminum cools down on its own and takes the shape of the mold. Aluminum and aluminum alloys are used in the process for their strength and stability. No other mechanical or industrial procedure is used in the process.
Die cast aluminum is an industrial process. It is carried out on a larger scale than cast aluminum and is best suited for high-volume, precision die casting production.
Die cast aluminum uses the high-pressure technique to melt the metals into the cavities. Aluminum is injected rather than being poured into the molds. This gives finished products stronger than those made through aluminum casting.
What kind of products are made from die casting?
Die casting is found in many products today. From household items to large-scale manufacturing industries, die casting is everywhere. The strong tools made from die casting are used in machinery and engines. Aeronautical gears also make use of die cast products.
Some of the die cast products used in homes are locks, toys, hooks, utensils, door handles, pumps, washroom necessities, and much more.
When it comes to our industries, big machinery, tools, gears, controls, and other numerous metallic products make use of die casting for high-speed manufacturing.
Medical instruments being used in hospitals are also manufactured through die casting. Surgical tools, ultrasound equipment, and other parts of medical supplies make use of die cast products due to their durability, strength, and design.
Automotive is one of the biggest industries where die casting is found. The engines, tools, machinery and even the structure of automotive vehicles find die casting in their manufacturing.
Sunrise Metal uses the aluminum die casting process to manufacture a list of products ranging from die cast brackets, plates, holders, enclosures, tubes, and engines. When you want to find a reliable aluminum die casting parts manufacturer, you should contact Sunrise Metal. As a professional aluminum die casting company in China, Sunrise Metal will provide excellent aluminum die casting service to you and bring satisfaction to you.
What are the advantages of aluminum die casting?
Aluminum die casting provides numerous benefits to industrial companies and manufacturers. Not only does it allow for efficient production of key metal components, but it also offers significant advantages to designers of such parts.
Some of the more prominent advantages that have rendered aluminum die casting as the most favored process by metal casting manufacturers:
- Aluminum die casting produces lightweight products that are still superior in strength.
- The method can produce aesthetic end results and provides a good surface finishing for industrial components. This makes the product attractive.
- It facilitates the customization of specific manufacturing processes with complex designs.
- A large number of products are obtained in a comparatively smaller amount of time. This makes it a cost-efficient means of production and gives companies a competitive edge.
- The near net shape is achieved even before the finishing of the product. Extra work on the product is avoided through aluminum die casting. Mechanical properties, if required, can be improved through treatments.
- The fast rate of production also makes the process cheaper and favorable for a larger production.
- The dies in the molds last longer as compared to the other alloy die castings.
- High-level of solidity is found in the aluminum die-casted parts. This also achieves lower porosity as opposed to other processes.
What are aluminum die casting parts?
Aluminum die casting parts are made to ease up the processes in industries and are said to even open the doors towards lightweight construction in the future. For instance, commercial and industrial equipment such as pistons, connecting rods, housings are all die casting parts.
Many industrial parts are made using aluminum die casting because of the durability, strength, and consistency it provides. As aluminum castings are resistant to corrosion no wastage is observed in the case.
Heat sinks and other components in light products are also prepared using this die cast method, along with meters for parking, gas, and other utilities.
Aluminum die-casted parts resist rusting and are used in automotive industries for molding products. They provide dimensionally accurate products that play a vital role in producing long-lasting supporting parts.
These parts are measured against efficient quality systems to achieve seamless customer experiences. The aluminum used in our parts can resist pressures and cracking, and depict strength. Equipment such as lawn tractors and recreational vehicles benefit from these properties and make use of premium die casting parts
Are there any concerns about die casting that must be taken into consideration?
While there may be a number of upsides to the use of die cast, there are certainly some limitations that must be accounted for before making a choice:
Size: Die casting does not produce castings larger than 600mm or 2 feet.
Weight: When it comes to heavier parts’ manufacturing, die casting goes ineffective. It only works if the part under manufacturing ranges from 30 grams to 10kg in weight.
Cost: There is a high initial cost for the manufacturing of the products. It might save costs in the long-term but is cost-effective only if to be used for the long-term. If a small number of productions is required, die casting stands very expensive. Smaller production makes it high-priced and is not so economical.
Raw Material: There are only a limited number of metals and their alloys that can be used in the die casting. Due to this, manufacturers choose sand casting over die casting. Ferrous alloys often don’t work with die casting.
Porosity: This is a common occurrence in die casting. It mostly happens due to the pressure with which molten metal is inserted in the mold.
What are casting defects?
Casting is mainly ineffective for many manufacturers for the following reasons:
Gas defects
When the mold has a lower tendency of letting gas pass through, it causes gas defects. If the mold has moisture left in the core, it can produce cavities called blow holes. The gas if not passed through can even become part of the casting and can weaken it. Once the product is formed, the gas will get expelled and will cause a cavity.
https://youtu.be/IGNDMLyx_uE
Shrinkage
If the molten metal is not properly fed into the mold, it can cause shrinking of the liquid while it solidifies.
Defect in the mold
If the material of the mold is not strong enough, the excessive flow of the molten metal will cause spots on the mold resulting in an uneven product. If the metal is not poured properly into the mold, the spots can appear even if the mold is strong enough.
A weak mold might also let the fluid run out of. The gap between the sand grains of the mold can also result in the rough surface of the cast or sometimes sand particles get fused with the metal resulting in the same thing.
Why is aluminum used in die casting instead of other cast alloys (e.g. Zinc and magnesium)?
Aluminum stands out among other non-ferrous alloys used for die casting for many reasons.
A. Liquidity
Aluminum and its alloys have high liquidity when we compare them to other non-ferrous alloys. This makes it easier to die and therefore easily manageable.
B. Appearance
Aluminum and its alloys have a smooth appearance which makes the products more attractive and gives a smooth finish.
C. Resistance
Aluminum is highly corrosion-resistant, hence produces more durable products. Along with this, the metal and its alloys also provide high resistance towards abrasion and wear.
D. Weight
Aluminum and its alloys are lightweight along with other superior properties of strength and durability. To produce a lightweight end result, aluminum is the prioritized choice.
E. Structural properties
Since aluminum is most elastic among other competitive metals, it is a popular choice for mid-range to large die castings. It does not change its structural properties when exposed to heat and remains stable at a higher range of temperatures. This stability also makes it a better choice.
Other metals and their alloys are sometimes better choices than aluminum while comparing individual properties. But by and large, aluminum is almost always chosen over others due to long term benefits.
Which aluminum die cast alloys are majorly used by manufacturers?
There are 3 aluminum die cast alloys that are majorly used by the manufacturers.
A380
A380 is the most widely used alloy of aluminum in die casting. It is favored by many manufacturers as it provides a combination of many physical and mechanical properties. While it is lightweight, it is also strong enough to stand by and resist high temperatures.
It has a higher thermal and electrical conductivity and is highly stable. A380 is being used in the manufacturing of communications equipment, automotive components, gear cases, furniture components, hand and power tools.
A383 (ADC12)
As the most popular choice of alloys for die casting, this aluminum alloy is used in order to reduce manufacturing costs and improve manufacturing efficiency.
A383 is often used as a replacement of A380 with almost the same physical and mechanical properties. When inserting A383 in the mold, some specific die filling instructions are to be followed since this can impact the end result. It might not be A380 but it does have the same strength and shows improved resistance to cracking at elevated temperatures.
A360
A360 is not prioritized by manufacturers due to the difficulties faced while casting it. But if the casting abilities are just right, A360 can provide the best pressure tightness, high-temperature strength, and corrosion resistance
Is die cast aluminum strong?
Die cast aluminum method is used in the industry because of the strength it provides. The following properties lend aluminum the strength that helps it stand out as a popular alloy:
- Tensile strength: The maximum stress that aluminum can endure ranges from 40MPa to 700 MPa. It can even be increased by applying mechanical processes.
- Shear strength: Shear strength of 50MPa to 305MPa is withstood by aluminum and its alloys. This makes it withstand any sort of frictional forces.
- Yield strength: Aluminum shows a yield strength range of 3.5MPa to 70MPa. This means that it can resist this much pressure before deformation.
- Fatigue strength: The fatigue strength shown by aluminum is between 50MPa and 300MPa. Aluminum can hold itself to this point of pressure and doesn’t break.
All these properties depicted by aluminum, and combined with the industrial process of die casting, add up to the success of aluminum die casting.
Can die cast aluminum be anodized?
The metal aluminum can be anodized and gives beautiful results when done.
It is a non-spontaneous electrochemical process that forms a layer on the surface and keeps the metal from corrosion. An actual surface transformation is witnessed in the process. The metal reacts with the oxygen and forms aluminum oxide or alumina.
However, it can be harder to anodize die cast aluminum because of the additional materials it includes. When done, it usually leaves black spots or grayish smut that be speckled. The surface is not as smooth and the resultant color isn’t as the intended outcome.
Anodization also increases the service life of die cast aluminum and provides a good net shape, along with forming a protective oxide layer on the surface. These properties of anodized die cast aluminum make the entire process more economical for the manufacturer as well as the industrial user.
What are the highest operating temperatures that aluminum can withstand?
Aluminum has a low melting temperature which makes it suitable for molding and bending. It is a good thermal and electrical conductor. Aluminum melts at a temperature of 655 ° C and boils at 2425 ° C (4400 ° F). It changes its physical and mechanical properties as the temperature rises.
Physical properties
The thermal conductivity increases with the increase in temperature. This distributes the heat in all of the metal and reduces hot spots. The rate of increase in temperature reduces with more heat. The heat capacity of aluminum becomes higher and will become slower to heat as the temperature rises.
Mechanical Properties
Even before the metal reaches its melting point, the mechanical properties start altering. The strength of aluminum decreases with the rise in temperature or standing at an elevated temperature for a longer time. The resistance and stability of aluminum also get compromised in the said situations.
Which other materials can be used for casting?
Some reliable materials that are used for casting are:
Gray iron
Gray iron is a strong versatile substance used in casting. It is easily tested and meets specific casting requirements for precision parts. It is highly cost-effective when produced at large volumes.
Ductile iron
Ductile iron can be used as an alternative to gray iron and shows many of the same advantages. As the name suggests, it shows greater ductility than gray iron, and hence lesser strength is required when casting ductile iron. Due to the superiority of gray iron, industrial processes are carried out to convert ductile iron into gray iron.
Steel
If the product is to be exposed to shock, exceptional loads, or even corrosive environments, steel is the most well-suited material for casting. The steel casted products are used in aqueous environments.
Copper and zinc are also suitable for the casting process in the industries.
How to choose the right die casting alloy?
There are a lot of factors that go into choosing the right die-cast alloy:
- The composition of the alloy
- The mechanical and physical properties
- The chemical composition
- Cost of alloy
The right alloy also depends on the requirements of your projects. For instance, if you are making parts for an automobile, your die casting requirements would differ when compared to a die-cast alloy for the electrical field.
The Cost of the alloy is also an important factor when it comes to the overall price of the product. Cost per inch cubic gives an approximation of the total cost of the alloy required in the process. The volume of alloys being used in the process almost remains constant.
Aluminum die casting is an integral part of the automobile, lighting, and computing fields to name a few.
How does aluminum die casting work?
The typical aluminum die casting involves a reusable steel mold, which in turn produces hundreds of thousands of castings or parts with remarkable efficiency.
Various industries require complex shapes and parts that must be manufactured with extremely high precision. This is where aluminum die casting comes in.
The die casting process begins when the two parts of the ‘die’ are firmly secured by the die casting press. The locking mechanism may make use of either hydraulic cylinders or hydraulic pressure. Molten aluminum is then poured into the die cavity in order to solidify and take the shape of the die.
From faucets to complex medical machinery, die casting is an integral process in the manufacturing industry – directly contributing to millions of tons’ worth of mass-produced items that can be found commonplace.
What are the main steps in the casting process?
The following steps are involved in a die casting process:
Preparing the Mold
The preliminary step involved in a die casting process is the preparation of the mold. Typically, a lubricant is applied to the mold’s interior walls. This is crucial to maintain the mold’s temperature – creating a thin barrier when the molten aluminum is poured in the cast.
This thin veil of lubricant enables easier removal of the cast once it has finalized.
Injecting Molten Aluminum
Once the die mold is ready, the next step involves pouring the molten metal in the mold. It is imperative for a successful cast that the die mold must be completely locked during this step.
Only a secure mold is able to accept the high-pressure molten aluminum, which may be injected with a pressure rating of around 1,500 to 25,000 pressure per inch (PSI).
Cast Removal
Once the molten metal has cooled down and solidified, the next step is to remove the newly-made cast from the mold. Usually, enterprise-level molds are made with designated removal pins that allow a seamless removal process.
Cleaning the Mold
Once the newly-made cast is removed, the final step before manufacturing another cast is to clean the mold from any excess metal. Metal scraps are not uncommon in the die-casting process, and the mold must be clean before it can produce another cast.
What types of dies can be used in the casting process?
Die casting processes make use of various dies, depending on the project requirements.
Single Cavity Die
A single-cavity die is only able to produce one cast (cavity) per process. These dies are typically used for highly complex parts that require center gating or multiple-side cores.
However, they are not as effective when the production requirement is high.
Multiple Cavity Die
These dies are able to manufacture multiple casts per process, with each mold designed to make identical parts. They provide great ROI when there is an increased manufacturing load.
Combination Die
Like multiple cast dies, these dies are able to produce more than one cast per process. What makes them unique is their ability to produce different components.
However, combination dies are designed to make parts that contribute to the same end-product.
Unit Die
Unit dies are smaller-than-usual dies that are used to make varying components. Unit dies work in conjunction with a master die, and come equipped with ejectors and cover die halves.
What is the difference between aluminum gravity die casting and aluminum pressure die casting?
Generally, the term die casting is used to refer to high-pressure die casting, especially in North America. However, there are three distinct sub-processes under the heading of die casting:
- Permanent mold casting or gravity casting
- Low-pressure die casting
- High-pressure die casting
Pressure die casting and gravity die casting (also known as permanent mold casting) are two different forms of die casting. Both processes involve a metal mold into which molten non-ferrous metal is introduced.
These metals are aluminum, magnesium, copper, lead, zinc or tin, etc. The most fundamental difference between the two processes is the way the molten metal is shifted or poured into the mold.
In gravity die casting, the metal is shifted into the mold from a height or a vertical position filling the bottom up. This part affords the name ‘gravity’ to the method. This melted mold is filled up purely with gravitational force and is used for less complex cavities.
On the other hand, in pressure die casting, the molten metal is injected with pressure into the mold. The pressure is the real part of the die casting process. The pressure normally ranges between 1500-25,400 psi and is maintained until the casting becomes solid.
The high pressure is usually adopted due to the intricate design of the mold requiring complex machinery. A minimum wall thickness of 2mm can be prepared with an excellent surface finish. However, the cost of choosing
such a method is also considerably higher than in comparison to the use of plain gravity.
How does aluminum die casting compare with sand casting?
In aluminum die casting, the castings may be produced from non-ferrous metals like aluminum itself. These can also include other metals like zinc, magnesium, copper, tin, lead, etc. However, in sand casting, castings are produced from different metals like grey iron, steel, aluminum, magnesium, and steel.
Another difference between the two is the use of molds. For sand casting, as the name suggests, mold can be made using green sand. However, for die casting, only a metal mold is suitable.
Die casting also produces thinner walls and much finer surface finishing, along with discrete dimensional limits. It’s also more cost-effective and faster to use a die-cast than a sand-cast, making it a better long-term choice for most manufacturers.
How does aluminum die casting compare with investment casting?
A comparison of aluminum die casting with investment casting reveals a contrast in the amount of time and type of materials used.
In aluminum die casting, the process involves forcing the molten metal with high pressure into the mold crater or cavity.
Whereas investment casting, also known as the ‘lost wax’ involves injecting a wax in the aluminum crater or cavity. A wax prototype of a particular part is made and immersed in liquid ceramic. As the ceramic hardens, it turns into a mold, letting melted wax drain out.
Next, the ceramic mold is broken to reveal the metal casting after the metal has solidified. This process does not use a ceramic mold twice, as opposed to a die cast that can be used multiple times.
Investment casting is used when companies are looking for stainless steel or copper alloys. It is a high-precision method which requires minimum additional machinery to achieve minute details and features. The process is suitable for small scale projects and low volume manufacturing, as well as for creating large-sized parts.
What is the difference between die casting and injection molding?
Die casting and molding both involve pouring the molten metal inside a mold or die, so that the molten metal takes the shape of the die upon solidification.
The main difference between the two methods lies in the type of material used; metal or alloy in die casting, and plastic or polymers in injection molding. While both processes may present benefits, it is best to know which type of material best suits your manufacturing needs.
Plastic injection molding benefits:
- More flexible molding process that speeds up production
- Cost-effective method due to low labor and material cost
- Ability to employ varied types of plastics and polymers
- Strengthening through the use of fillers
- High accuracy and efficient production
At the same time, aluminum die casting also offers high accuracy and cost-efficiency. However, an additional advantage is its ability to cast more complex designs easily and accurately.
Metal end-products have superior strength and resistance properties, making them a clear winner in the race for the best large-scale industrial process.
Which materials are most suitable to be used as molds for the die casting process?
Depending on the type of industrial component being produced, a number of different molds can be used in the aluminum die casting process.
Some can be used for temporary periods, while some are permanent and of great value and can be used more than once. These permanent molds can be used for many different types of metals besides aluminum.
Different types of molds are:
- Permanent
- Ceramic
- Sand casting
- Shell
- Plaster
- Ceramic
- Graphite casting
Are there any precautions that need to be taken while using aluminum die casting molds?
Safety measures are taken at Sunrise Metal to avoid any casualties. The die casting mold, especially, has to be handled with care when the melted aluminum is inserted or ejected.
The following precautions need to be taken while handling molds:
- Wear protective gear or personal protective equipment (PPE) to keep yourself safe from the contact of heat. Mold can leave steam burns on the skin even if one doesn’t touch the mold directly.
- The temperature of the furnaces goes up to 800°C and the utmost care is required when handling molds. Take proper training on how to do so in order to keep safe.
- Keep the proper distance from the molds and the furnaces while working.
- Avoid moisture on the molds as it can cause highly energetic reactions when in contact with the metals.
- Follow all established protocols and ensure all machines are in working order.
What is the best way to design a premium die casting part?
To design a premium die casting part, some factors are to be kept in mind:
Parting lines
Parting lines decide the split between the manufacturing of the two parts. These lines are according to the size and geometry required for the product.
Customer specifications
Customer specifications are always the priority because, in the end, the customer is the judge of produced part precision.
Die Costs
As the parting line is decided, the die is selected accordingly. Different die toolings have different cost effects. It depends on the kind of parting line design.
Machining
Machining of the parts is required to produce a perfect finished product. Removing the material from the cast and the removal of scrap require machining.
Metal Flow
The flow of metal ensures the proper letting of the molten metal and hence the formation of a premium product.
Cores
The location of the core, as well as the size of the diameter and length of each core for each hole needed in the casting is considered with proper calculation in order to achieve great results.
Ejector or knockout pins
The degree of force required to eject the casted part also takes part in the precision of the product.
What kind of mechanical equipment is used for producing die casting parts?
The die casting process increases ease in producing metal casting components. The mechanical equipment used in the process increases the efficiency and the rate of production. The more automated a process, the more efficient it gets. The following machinery is used in the process that increases productivity:
Melting
Melting of the metal is the defining step in die casting of how the product will turn out. Different types and sizes of furnaces are used in order to carry out the process. Electrical and heat treat furnaces and temperature control machinery is utilized. Gas-fired melting machinery is also used as a replacement of furnaces.
Insertion
The automated insertion of melted metal increases productivity. Robots and shot blasts are two of such machinery. The insertion of melted metal does not stop.
Chambers
The chambers that hold the melted metal when allowed to solidify also make use of the advanced technologies. Hot chamber, cold chamber, low-pressure chamber, high-pressure chamber, and many more are used for the purpose as required by the process chosen.
What are the key structural parts design points to be taken care of during the die casting process?
Structural components are being widely manufactured using die casting. Since they’re the backbone of any system, there’s no room for error.
The following points are kept in mind when manufacturing the structural components:
Elongation to withstand impacts
The components should have high elongation so they could withstand any external or internal impact. This also measures the strength of the system.
Yield Strength and/or ultimate Strength
The components should not deform when exposed to stress. The higher the yield strength of the part, the better part will work.
Heat Treatability
When the structural part is treated with heat, it should show a change in its physical and chemical composition. This will make it easier to treat the damaged part.
Weldability
The components should be easier to weld as more parts are to be attached to the structural component.
How can you weigh out the pros and cons of screw machining vs die casting?
Screw machining and die casting produce the same results when it comes to precision metal parts. The differences lie inefficiency, feasibility and price.
Screw machining even manufactures steel alloys that are not possible with die casting. As zinc and aluminum, widely used die casting alloys, have lower melting points than steel, steel, and these metals don’t fuse together. Screw machining even holds tolerance and produces more precise parts.
Die casting makes use of multiple cavities and produces more complex parts in less time. The hard to produce parts with the complex structure are produced through die casting. Bar or tubular stock are unable to do so and the expense is also higher with them. Die cast provides the feasibility of having precise tools, in less time with a lower price than screw machining.
Screw machining may produce products with high tolerance but the rate of production and the cost difference between the two methods lets die casting overcome screw machining.
What kind of product segmentation is associated with aluminum die casting parts?
Aluminum die casting produces lightweight metal parts that are used in many aspects. The product line ranges from household to aerospace and even defense equipment.
Due to the tendency of producing lightweight parts, die casting is mainly known for the production in the automotive industry. The demand for di- casted parts is rising day by day in this segment.
Several end-use industries producing automotive parts are being developed in North America, Europe, Asia Pacific, South America, and Middle East & Africa.
This segment is also anticipated to gain a visible higher share in the market globally. It is moderately fragmenting in recent years and is expected to grow exponentially.
Sunrise metals is a leading producer of the automotive parts produced through die casting.
What are the different die casting applications that make it a lucrative option for industries?
Die casting has many benefits that make it lucrative. Productivity, better finish, smooth surface, lower cost, and efficiency makes die cast stand among other manufacturing processes.
Due to these benefits, die casting is prioritized and applied in many fields. Majorly die casting is chosen for these applications in order to profit in the industry.
Die casted parts are light in weight and are applied in automotive. This makes them fuel-efficient and hence cost-efficient increasing the profitability for the companies.
Die casted parts in medical equipment are lightweight and durable. This makes them easy to handle and more reliable thus cutting off the costs.
Die casted parts in the telecommunication industry are more durable. The fiber optics are long-lasting and are profitable.
Which aluminum die casting components can be used in electric vehicles?
As die cast aluminum has its applications in the automotive industry, electric vehicles make use of the technique in most of its parts. A high-yield strength and conductivity is shown by aluminum and its alloys that are the main concerns for the industry.
An electric vehicle needs to be lightweight and die cast aluminum serves the purpose. Electric motors can be manufactured using structural components made of die-cast aluminum. The efficiency does not get compromised with the use of such tools.
Battery and power electronic housings are made through die cast aluminum and are utilized as powertrains of the vehicles.
The inverter, converter and charger of electrical vehicles makes use of die cast aluminum. All these applications are said to shed the weight of 35-40 kg as compared to the regular vehicles.
How does the use of aluminum casting improve fuel efficiency for the transportation and automobile sector?
Ever since the production of automotive started, the need to improve fuel efficiency has always been talked about. Aluminum casting is said to do exactly that.
Research says that reducing the weight of the automotive by 15 % can increase the fuel economy by 25%. This made the automotive designers go towards more die casting solutions.
The car weight reduction problem called for using parts made up of die-casted aluminum rather than steel or iron. The fuel efficiency regulations can only be met with more and more use of die cast aluminum.
Big names in the automotive industry are making use of die cast aluminum to substitute with heavy bodies. As the vehicles are becoming fuel-efficient with the use of die cast aluminum parts, it is also helping in the reduction of greenhouse gas emissions.
In order to optimize manufacturing, how does a company choose between conventional die casting and multi-slide die casting?
Choosing between conventional die casting and multi-slide die casting depends on the weight requirement of the manufacturer. The tools operation and their construction are where the two processes differentiate.
Conventional die casting has single or multiple cavities. It provides efficient casting for larger parts and does not require any secondary operations on completion. It provides a net shape and complete cooling system which increases the rate of production.
Multi-slide die casting is efficient when it comes to smaller parts that need detailing. No assembly or machining is required in the process. It is the same as conventional die casting in this respect. Tools with complex geometries are easily manageable through multi-slide die casting.
Both of the methods have their own unique benefit. At Sunrise Metals, both of the methods are alternatively used as per the requirement to provide with best quality products.
Does a firm achieve significant cost savings and high production speeds as a result of choosing the right die-cast method?
Choosing the right die casting method takes up a lot of calculations. In order to achieve efficiency, save cost, and get high production, the pros and cons of each die casting method are considered. The following factors must be kept in mind
Total product
The total amount of product to be produced must be considered as each method can produce a specific amount of product per batch.
Time
The time in which a product has to be achieved in the finished form is to be considered. The rate of completion of the process is different for each die-cast method.
Size
The size of the product matters a lot as some methods are ideal for smaller castings only and others for larger.
If a firm needs to achieve the ideal results, all of the mentioned factors are considered and the process is started after careful calculations. In this way, a significant cost is saved and efficient results are achieved.
What are the main cost drivers for the casting method?
Casting methods mostly have the same cost drivers which are as follows:
Material
The cost for the material of die-casting is measured by calculating the amount required and the unit price of the material. The required amount of material is determined by the part that is to be made. The part to be manufactured is measured and an estimate is driven.
Machinery
This is the cost of the machinery being used in the processes and the other resources that machinery uses during the production. For example, the heat or the electricity utilized by the machinery during the die casting process increases the cost of the process.
Labor Cost
Labor working is one of the cost drivers. Labor’s wages or salaries are a part whereas the expense during the training of labor is also a cost driver.
How is the material cost-optimized during the process?
- The material costs can be optimized by careful calculations. It is to be considered while planning the process through the following steps:
- Reducing the scrap and any wastage of the material directly reduces the cost of the process.
- Using simulation techniques that tend to lower the amount of material to be used.
- Decreasing the thickness of the wall will reduce the cycle time and the material being consumed. As the material consumption decreases, cost decreases proportionally.
- Keep the thickness of the walls constant. A constant measure will cause fewer defects and hence lesser wastage is obtained which will optimize the cost.
What are the advantages of a fully automated aluminum die casting process?
- A fully automated aluminum die casting process is beneficial in many aspects.
- This system offers almost 60% cost savings for the manufacturer and for the buyer as compared to the traditional manual die casting processes.
- As the process is fully automated, no labor force is required for the system to work.
- This also reduces the risk factors in handling the processes at the expense of man effort.
- This fully automated process is continuous. The working never stops and hence the production rate gets higher.
- The machinery itself cleans the metal for any scrap thus perfecting the product. The scrap is taken back to get melted and reused. This reduces the cost of the process.
What are the best methods of building casting prototypes and why?
Manufacturing casting prototypes is a growing industry itself. Different processes are used to cast a prototype which is then used as molds in the casting process. Some of the best methods are discussed below:
CNC machining is a form of subtractive manufacturing. It is suitable for both plastic and metals. It offers high accuracy and produces molds that have better mechanical properties in all dimensions. It might be an elite method but comes at a greater cost.
3D Printing
3D printing is a form of additive manufacturing. It creates parts layer by layer using metal powders. Laser or some other form of energy is used to solidify the mold. This prototyping method gives the freedom of shape, accuracy, and speed while reducing the cost.
Both methods have their own pros. Sunrise Metals make use of both of the techniques to create the prototypes required in the die casting process.
What are the differences between die casting and CNC machining?
The two methods are widely being used in the production of structural components of many systems. But to decide which method to choose between the two, it is important to know the difference.
CNC machining
CNC machining is the subtractive method of producing metallic parts. The metal is sculpted through the machinery and an end product is obtained. It is a completely automated process hence provides efficiency. The process is highly recommended by professionals when a small number of parts are required.
Die Casting
Die casting uses the molten metal injected into the mold. The metal then takes the form of the mold. Many different techniques are applied to the metal in order to achieve the desired product. The process provides a surface detailing advantage.
What is the best way to design a die cast component without compromising on ROI and scalability?
Return on investment and quality are sometimes alternative outcomes when the die cast process is not carried out with proper calculations. Scalability and greater ROI can be achieved in simple steps:
Innovation
Innovation in the process leads to groundbreaking advancements. It is the requirement of the process from the very start till the delivering of the product.
Sourcing
This step ensures the availability of less expensive parts and producing cost-effective results. The supply is managed by keeping the end result in mind. Farsightedness is necessary in the step.
Careful Calculation
A careful calculation of the material involved and all the product provides for efficient results. This will not only decrease the cost but also strives for greater quality.
How does the use of aluminum in the die casting process help achieve high returns?
Aluminum is often preferred over other non-ferrous alloys that can be die cast. The main reason for this is that aluminum provides a higher return on investments. This happens because of the following capabilities:
- Aluminum die casting produces lightweight products but is very strong.
- It can produce aesthetic end results and provides a good finishing. This makes the product attractive.
- A large number of products are obtained in a comparatively shorter amount of time. The fast rate gives an edge to the process.
- The near net shape is achieved even before the finishing of the product. Extra work on the product is avoided through aluminum die casting. Mechanical properties, however, if required, can be improved through treatments.
Why should I opt for aluminum die casting services by Sunrise Metal?
Sunrise metals is a professional aluminum die casting company in Shanghai, China. We provide elite aluminum die casting services that are applicable in almost every industry. Sunrise Metal provides fast aluminum die casting solutions upon your requirement.
Whether it is the response time of our representative or the manufacturing of product, prototyping or production, Sunrise Metal believes in faster customer service.
The most suitable solution will be provided to you. Engineers and designers at Sunrise Metal are working 24×7 to meet your needs with their services that include and are not limited to:
- Feasibility analysis for the design and manufacture of tooling and components.
- The ability to work with CAD systems, Mold flow simulation systems, and PPAP.
- Identify potential manufacturing problems and propose construction suggestions to avoid them.
- Value engineering to help reach a lower cost for customers.
What kind of engineering techniques are employed by Sunrise Metal to ensure efficient and cost-effective mass production?
Sunrise Metals employs different techniques on metals in order to achieve efficient metal components.
Sunrise Metals prototyping workshop provides many prototyping techniques, such as 3D printing prototyping, CNC machining prototyping, prototyping tooling, and a lot more. These techniques provide efficient and high-end prototypes.
Die Casting
Different die casting methods are followed by sunrise metals in order to achieve the ideal products for the clients. Ranging from tooling design, mold flow simulation, manufacturing, modify, maintenance to tooling end management, a complete solution is provided.
Aluminum Die Casting
Sunrise Metals has 2 aluminum die casting shops in Kunshan & Nantong, China. 160T to 1650T die casting machines are used to cast ADC12, A380, AlSi12 & other die casting aluminum alloys.
Processes like drilling, tapping, turning, and milling are carried out by Sunrise casting using CNC machining. These are carried out in order to achieve casted or milled products.
The following surface finishing processes are offered at Sunrise Metals:
- Shot Blasting
- Powder Coating
- Liquid Painting
- Electroless Nickel
Which machines are used in high pressure die casting production processes?
Pressure die casting processes make use of two different types of machinery.
Cold chamber machine
The cold chamber machinery is built with detail and under the guidance of qualified and highly experienced engineers. This machinery is handled manually and sometimes semi-automatically. The machine has an extra-long base to support all the processes. The die lock works on the mechanism of hydraulics used in the injection. An ejection cylinder is found at the end.
Hot chamber machine
The hot chamber machine consists of an injection area. This is where all the processes involving injection are carried out.
- The die is later closed and the casting process starts.
- The plunger seals the mold to solidify the metal.
- The cores retract and the casting is remaining in the ejection part.
- The ejection part ejects the casted metal out of the ejector die.
How can small and medium-sized companies in the automotive/aerospace/industrial/ communication/medical/marine sector benefit from Sunrise Aluminum Die Casting Services?
Sunrise Metals is dedicated to providing the best solutions of aluminum die casting for all levels of all sectors. Sunrise Metal also works for small and medium-sized companies, who are struggling to find the right aluminum die casting company in China for their orders and the right aluminum die casting suppliers in China.
These companies have a small demand which might become expensive for them. Sunrise Metals meets every demand of these companies by staying affordable. High precision products are provided to these companies with the order limit as low as 10 parts and as high as 5000 parts.
Quick deliverables due to quick production arrangements are provided to these businesses at an affordable price.
What are some of the die cast tooling capabilities offered by your die casting company?
Sunrise Metals offer different die cast tooling capabilities:
Tooling design
Before the process starts, tooling designers work on the blueprints to find any flaws in the process.
Mold flow simulation
A simulation of how the mold will flow into the chambers and mold is carried out using simulation tools to analyze the results.
Tool end management
The tools being used in the process are managed and all the information regarding them is integrated. This helps in their management.
Management and Modification
The process is managed through different techniques to increase productivity. Any modification necessary is implied at any point of the process.
Does die cast aluminum rust?
No, die cast aluminum does not rust. It is one of the major advantages of die cast aluminum. Being highly corrosion-prone makes die cast aluminum ideal for a number of products around the home as well as industry. Aluminum can withstand high temperatures as high as 100 degrees centigrade. Aluminum also has the ability to function even after the outer layer of a product apparently corrodes So, in the toughest of working conditions die cast aluminum still works just fine. Some examples could be outdoor furniture and kitchen products like cookers.
How are die cast metals inspected for defects?
Inspection of die-casted metals is a critical step for quality assurance. There are a number of tests for defect detection in die casted metals. These include:
- Ultrasonic Inspection: An ultrasonic signal is sent through the casting and the return signal exposes the defect as the wavelength of the returning signal is changed.
- Visual Inspection: Testing is done by inspecting the product through naked eye. It is helpful in finding surface level defects.
- Radiography: It is an expensive technique used only for detecting inner surface defects. X-ray pictures expose cracks, voids and tears under the outer surface
- Sound testing: Casting is hit by an object and the sound it produces indicates a flaw. However, the exact location of the flaw can’t be estimated.
- Pressure testing: Testing is done for the products that need to be leakproof. The pressure is applied via a gas or a liquid. Defective material will leak under pressure.
- Magnetic Particle Testing: Technique is used to reveal fine cracks or holes on the casting surface. The casting is magnetized and particles of steel and iron are spread over the surface. Any defect will interrupt the magnetic field formed as a result of this process.
What are the advantages of non-destructive inspection for die-casted metals?
Inspection of defects may bring a degree of damage to the die-casted metals. Depending on the magnitude of such damage defect inspections can be divided into destructive and non-destructive inspections.
Non-destructive testing is advantageous as it is more detail-oriented. Multiple non-destructive tests can be carried out on the casting simultaneously and may reveal more than one defects in the casting.
Since the non-destructive tests are less damaging to the casting, they are more feasible if the production cost of die-casted metals is high. Moreover, destructive casting also has the drawback that it may not reflect the entire problem with the sample. It has the tendency to miss the most sensitive of problems.
Why is destructive inspection for die-casted aluminum preferred over the non-destructive inspection?
Destructive inspection is carried out by destructing part die-casted metal to understand its performance and behavior under different circumstances.
Although destructive inspection destroys part of the produced material, it is still preferred because:
- When there is mass production, destroying a negligible part is beneficial
- The tests are easier to carry out
- They yield better results and are easier to interpret
- The product is inspected at a molecular level and more efficient readings are taken.
- Comparison is drawn better for the different types of stress levels.
- As in the case of non-destructive inspection, no professional expertise is required.
How is scrap reduced in aluminum die casting?
Aluminum die casting produces high-end products with smooth surfaces. However, improperly controlled casting methods can result in the production of scrap. Scrap causes the slowing down of the rate of production. At the same time, it also causes an increase in the cost of production.
To overcome these issues, scrap production with the product must be reduced and in order to do so, the following methods are used:
Metallurgical Quality Calculation
This is to check the quality of the initial source of aluminum. The chemical composition and the cleanliness of the metal directly impact the amount of scrap being produced. The more the impurities in metal, the more scrap is obtained.
Optimization of process
The process is optimized by strict calculations to obtain the maximum benefits. Operating conditions are calculated under which the metal can produce minimum scrap and be more productive. Control factors for the process are drawn and are then established.
Why is there a limitation in the height and weight of components prepared through die casting methods?
Die casting produces parts with low dimensions tolerance and high surface quality. The method is preferred by the manufacturers over the other production techniques but it has certain limitations.
Die casting can only produce parts that have weights ranging from 30 grams to 10 kg. The machinery only supports the given weight as after this limit the machine doesn’t give efficiency and is not possible to handle.
This limitation is not only on the weight of the casted products but also on the height. Larger parts are not supported by the process. To produce parts out of the weight limit, other casting processes are used. Thus, it is only for the parts that are lightweight and demand certain softness.
How can the automotive industry benefit from aluminum die cast products?
Automotive parts are one of the major applications of aluminum die casting.
With the new regulations introduced in the automotive industry, the automotive are required to be as light as they could be. This increases fuel efficiency and reduces Carbon dioxide emissions from the engines. Aluminum die casting is producing lighter parts with more efficiency.
Many automotive parts that were made from steel are now being replaced by aluminum parts. It is said that by 2025, the use of aluminum die-casted products will increase by 60%.
Automotive manufacturers are benefitting from the rich experience of die-casted parts provided by Sunrise Metals. They have provided reliable services to clients all around the globe. Visit us to explore the capabilities provided by Sunrise Metals.
What are the advantages of using aluminum die cast products in the telecommunication industry?
The telecommunication industry is advancing at a high pace. It is said to expand at an even higher rate in the future and the need for the die casted parts in the industry is going to increase with it.
The telecommunication industry finds the applications of aluminum die cast in the following sectors:
Fiber Optic connectors
A reliable and easily connectable fiber optic is necessary for communication to take place. These connectors make use of aluminum die casting in their manufacturing. They are made to stand the harsh environments like high temperatures and humidity.
Networking Equipment
Networking equipment in the telecommunication industry also requires to die casted aluminum products in their making. A wide range of equipment is being developed by using this technique. The connector housings used in networking, are made through die casted aluminum.
Internal parts of telecom devices
Small parts used in telecom devices make use of aluminum die casting. The process grants rigidity and durability to the devices.
What variations of the basic die casting process can be applied?
Different variations of the die casted products give the same results. To choose between the processes, the type of melted metal, part geometry, and part size are considered.
The following variations are used for casting:
Vacuum die casting
This process produces minimal porosity as the insertion of molten metal is done through a vacuum. The molten metal is forced into the mold using a cylinder chamber that pushes the metal through a vacuum. The gas inclusion is limited through this process.
This process is used for metals with low fluidity. The molten metal is inserted into the mold and is squeezed closed filling up the recessed portions of the mold. Squeeze casting produces dense products.
It is mainly used in fiber applications.
Improved precision is achieved through this process. The metal is cut into smaller parts and is melted. When a slushy texture of the metal is formed, it is inserted into the mold.
What quality systems are followed by Sunrise Metal to ensure products are in-line with international standards?
Sunrise Metal follows quality assurance with the process, technology, material, and method. The quality systems followed by Sunrise Metals are:
X-Ray Detector
X-ray detectors are used in order to test the casting parts for shrinkages, porosity, and cracks. Sunrise Metals use the technique to detect the defect patterns and give the maximum throughput. The geometric measurement of some internal parts is also measured by Sunrise Metals through this technique.
Cleanliness Detector
Sunrise Metals uses the cleanliness detector to find the purity of the metal to be casted and the casted product. This yields the product of the highest quality.
Zeiss CMM
Zeiss Coordinate Measuring Machines (CMM) are used by Sunrise Metals to check the product multidimensionally. They are multi-sensor systems that give reliable inspection.
Digital Caliper
To get extremely accurate measurements of the products, Sunrise Metals use the digital calipers. They measure the internal and external distances with complete accuracy providing exact calculations for the processes.
What are some of the applications of pressure die casting?
Pressure die casting makes use of high pressure die casting machines that inject the molten metal with a risen pressure. The mold is closed at high pressure. This process produces structural components which find their applications as follows:
- A diverse range of automotive castings such as engine blocks, gearbox casings, oil sumps, engine mounts, and structural parts like cross-car beams are manufactured.
- Aerospace engine parts also make use of pressure die casting.
- Thin wall components are also built using this technique like screws and liners are made using the technique.
- Light alloy parts are manufactured with precision using pressure die casting.