Sunrise Die Cast Heat Sink Components
Die cast heat sink products at Sunrise are developed to deliver on performance, durability, and efficiency in all types of projects.
We are involved in producing and manufacturing automotive casting parts delivering optimum strength, and enhancing engine power. The material being used in the production is selected carefully and meticulously to expand possible applications.
Aluminum alloy has been a special in-demand option in the market because of its beneficial features and cost-effectiveness. Over the years, the die casting process has led to breakthroughs in the aluminum heat sink parts. Looking learn more about aluminum die casting.
Sunrise Aluminum Die Casting Manufacturing Capability
Aluminum die cast components are produced using high-tech machinery and tooling, leading to fast production time. At Sunrise Metal, we experienced success in the market and private sector through manufacturing quality aluminum casting parts.
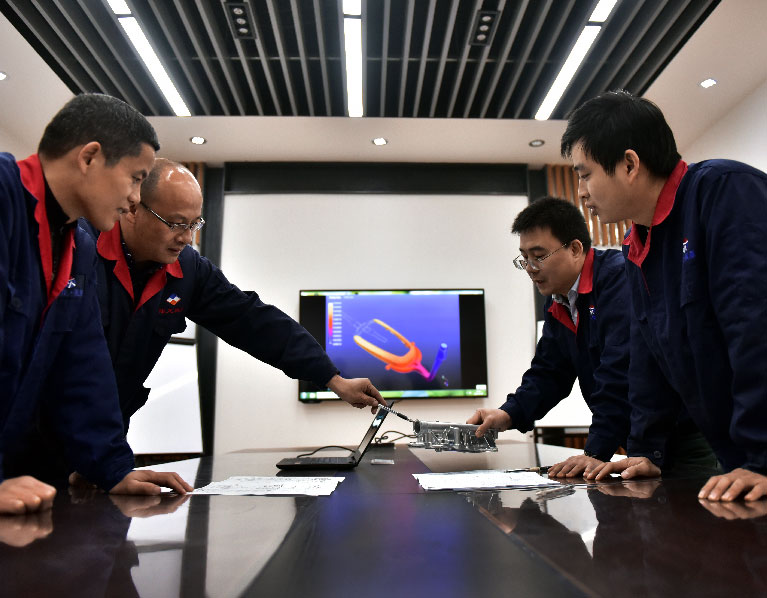
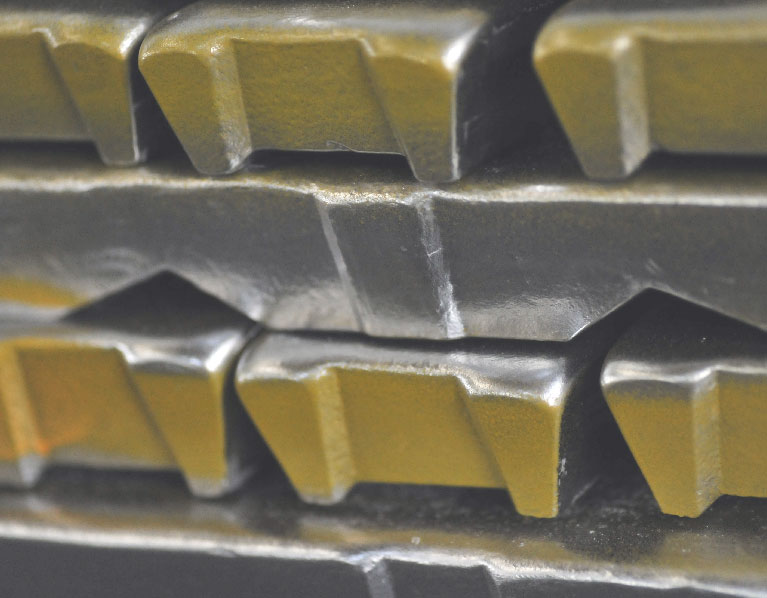
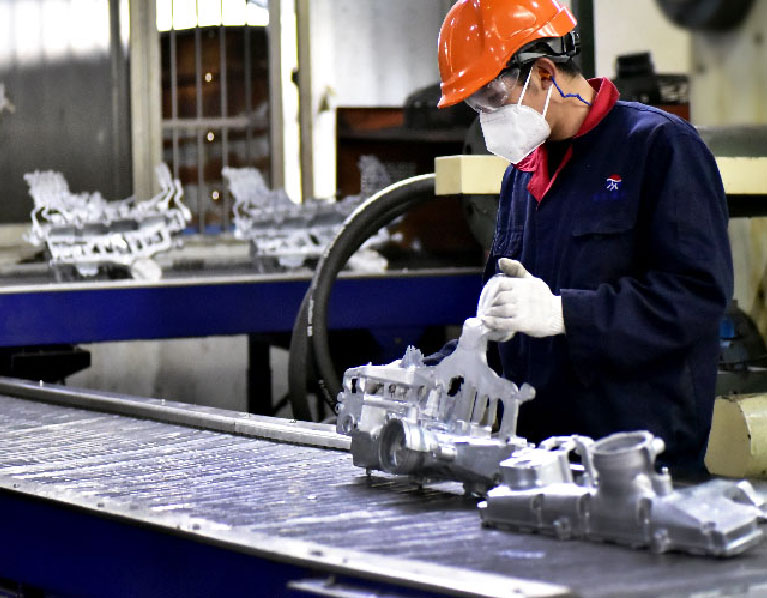

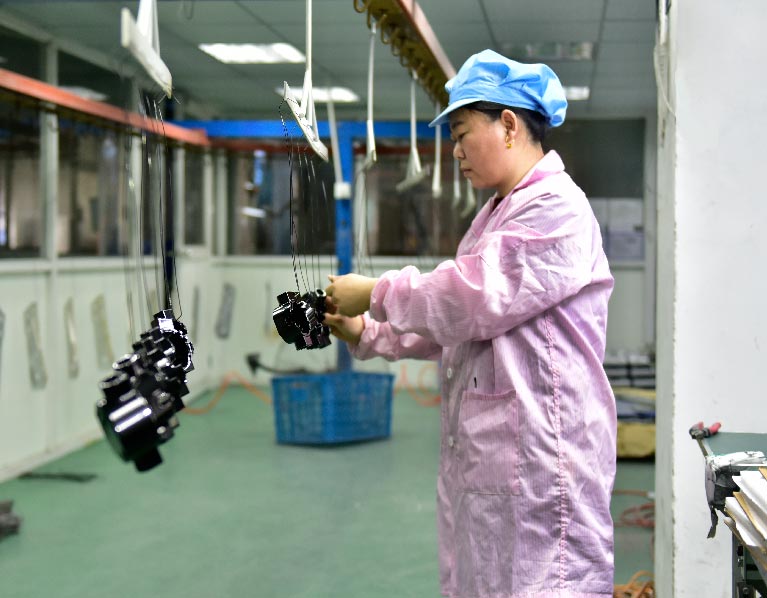
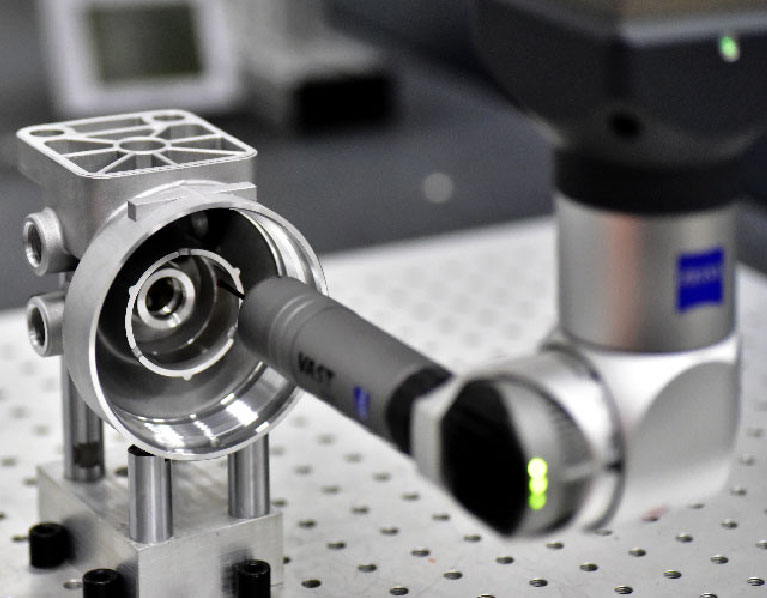
Advanced Equipment For Aluminum Die Casting Products
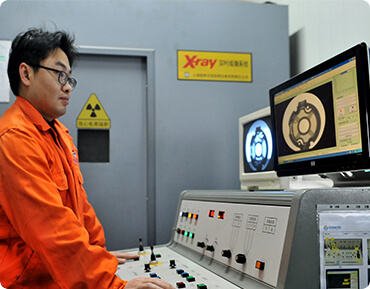
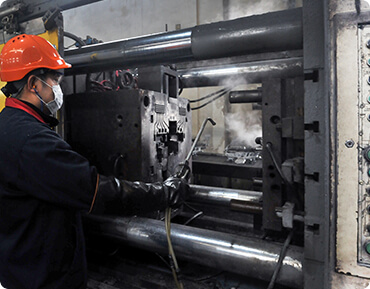
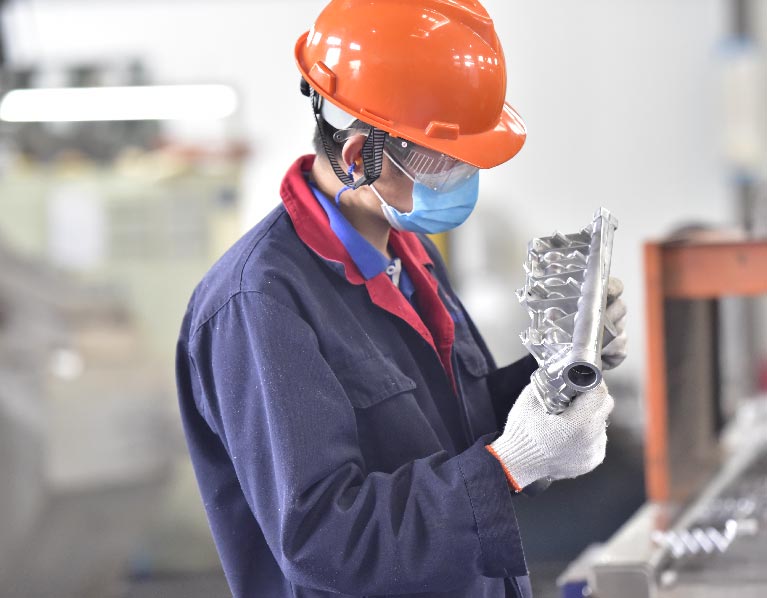

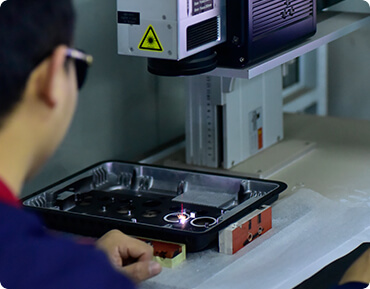
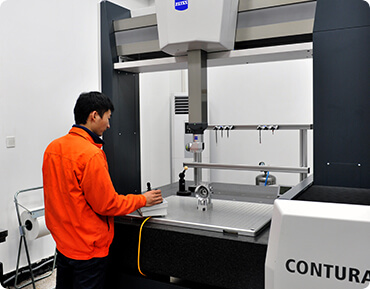
Recent Die Cast Heat Sink Projects
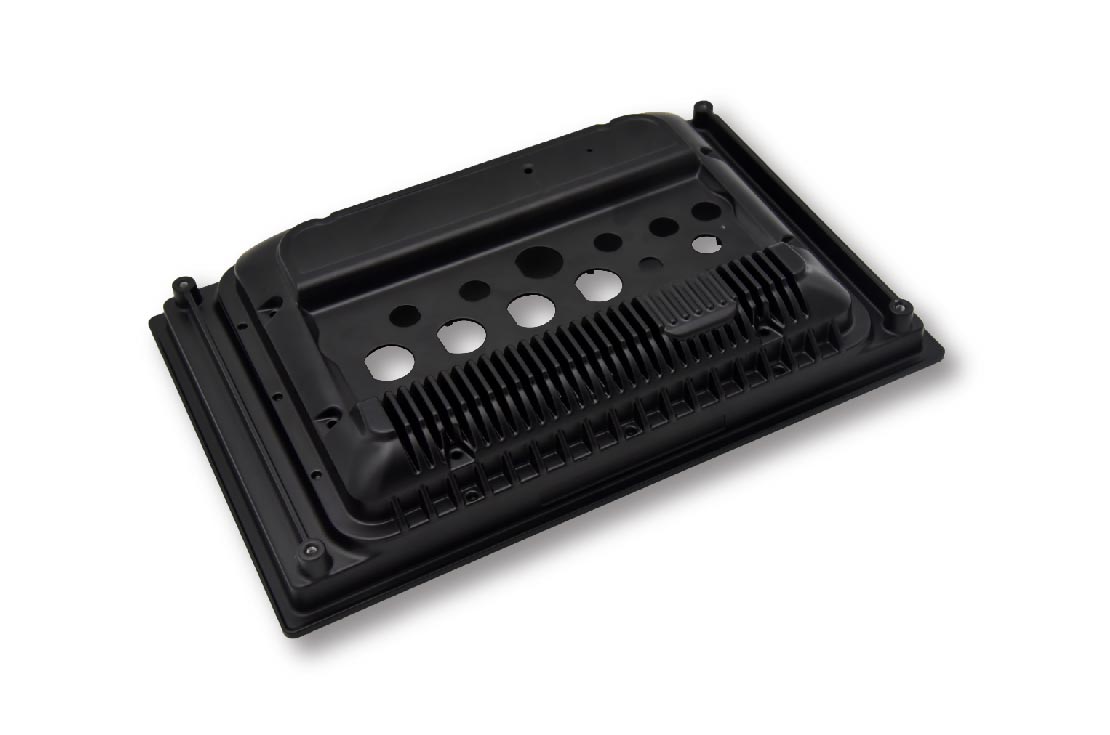
Part Name: Heat Sink Cover
Material: AlSi12
Size: 317*229*38mm
Weight: 1230g
Machine Tonnage: 800T
Surface Finish: Powder Coating
Production Process: Die Casting–Trimming–Deburring
–CNC Machining–Chromating–Powder Coating–Screening–Packaging
Applied Industry: MARITIME
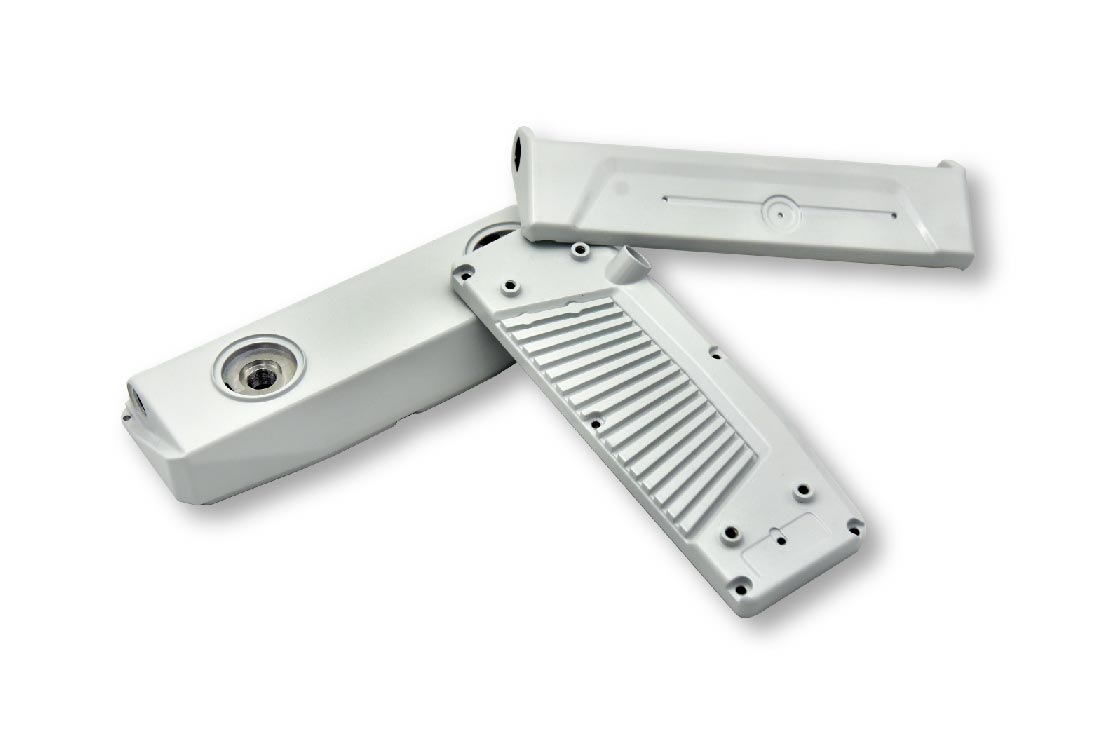
Part Name: Heat Sink Battery Cover
Material: AlSi12
Size: 182*70*38mm
Weight: 432g
Machine Tonnage: 280T
Surface Finish: Powder Coating
Production Process: Die Casting–Trimming–Deburring
–CNC Machining–Chromating–Powder Coating–Screening–Packaging
Applied Industry: MARITIME
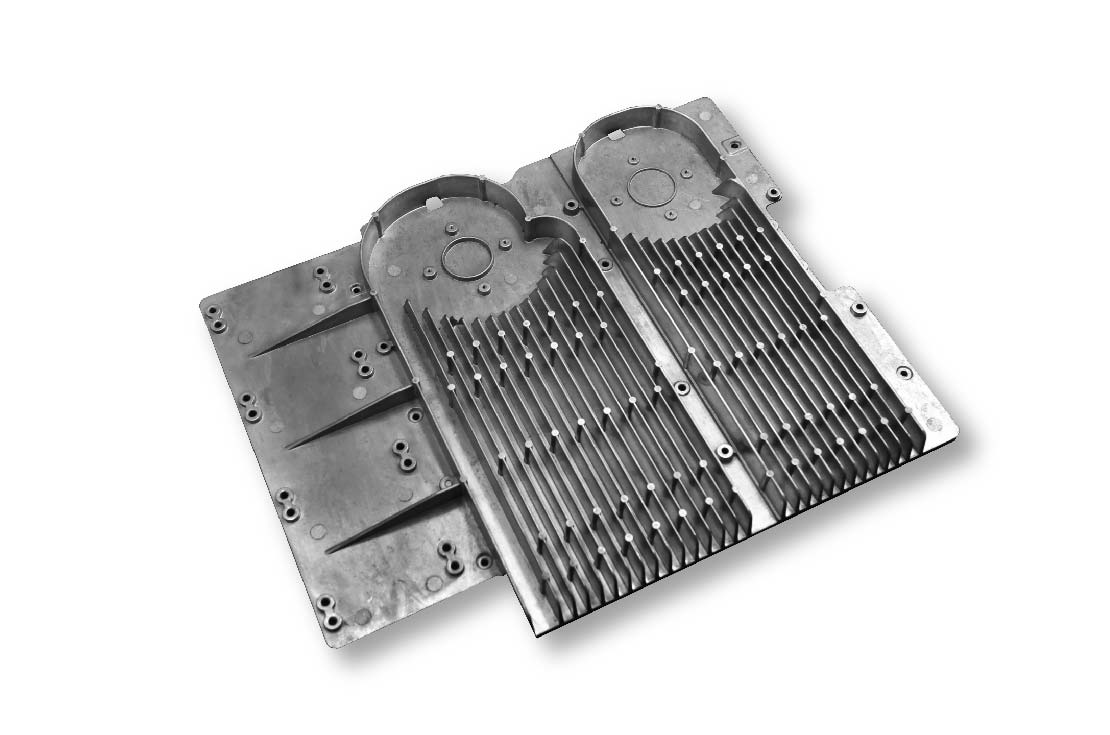
Part Name: Circuit Board Heat Sink
Material: AlSi12
Size: 355x283x29 mm
Weight: 1665g
Machine Tonnage: 500T
Surface Finish: Chromating
Production Process: Die Casting–Trimming–Deburring
–CNC Machining–Chromating–Screening–Packaging
Applied Industry: MEDICAL
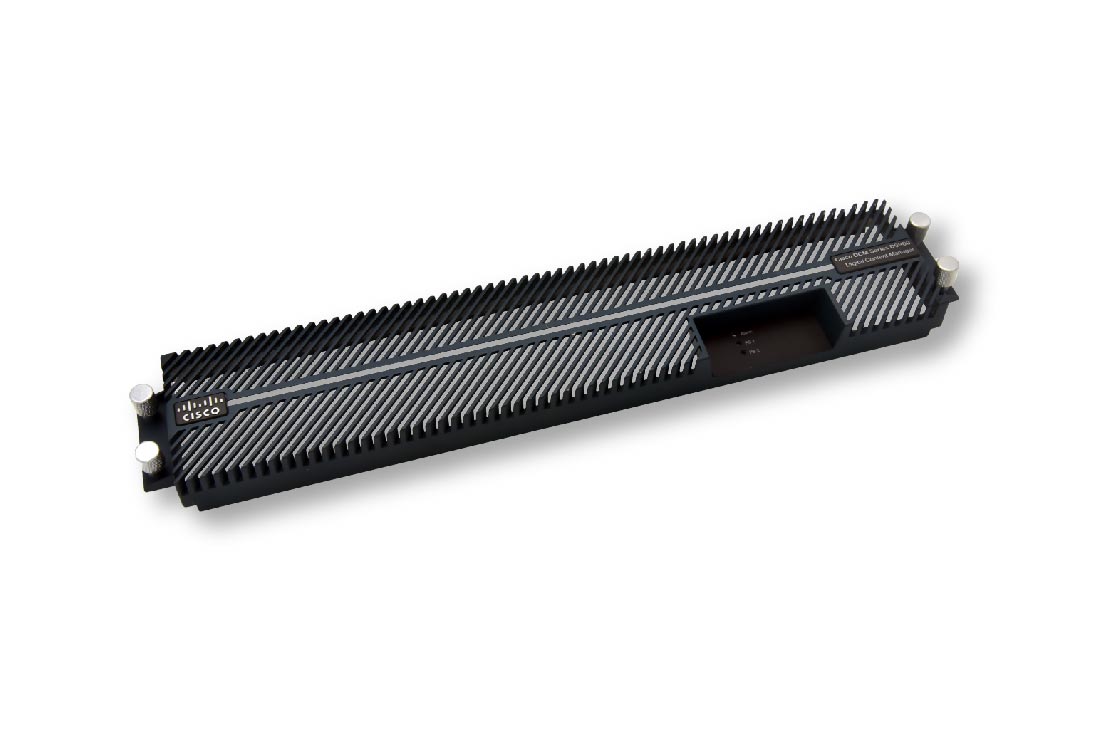
Part Name: Heat Sink Bracket
Material: AlSi12
Size: 412x46x36 mm
Weight: 182g
Machine Tonnage: 400T
Surface Finish: Coating
Production Process: Die Casting–Trimming–Deburring
–CNC Machining–Coating–Screening–Packaging
Applied Industry: MEDICAL
DIE CAST HEAT SINK: THE ULTIMATE FAQ GUIDE
A die casting heat sink is ideal for transferring heat to the environment and balances the energy in the resultant component. It is an essential part of the aluminum die casting production process and can be applied to various industries.
Sunrise Metal makes highly efficient aluminum heat sinks to make such devices that use electrical processes can avoid any failures.
- What is a die casting heat sink?
- How does a die casted heat sink work?
- Why does a die casting heat sink have fins?
- What materials are best for manufacturing a die casting heat sink?
- What are the advantages of using a high pressure die casting heat sink?
- How is the heat absorbing capability of the die casting heat sink increased?
- What is high density die casting? How is a die casting heat sink more efficient?
- What are some of the applications of die casting heat sinks?
- What are the advantages of using an aluminum die casting heat sink?
- In what ways are die casting heat sinks better than extruded heat sinks?
- What sort of machining is required for an aluminum die casting heat sink?
- How does the size of die casting heat sink affect the thermal management?
- What is the difference between an active and passive die casting heat sink?
- How is the design of a die casting heat sink made more efficient?
What is a die casting heat sink?
Die casting heat sink is used to cool down different components. It follows the heat dissipation effect which occurs when a hot component is placed in a relatively cooler environment. The component transfers its heat to the environment resulting in a cooler self.
Die casting heat sink is an important part of die casting as it releases the trapped heat from the part and balances the energy. The aluminum heat sink is casted for many electronic devices. The aluminum heat sink cools them in order to avoid any failures due to all the electric processing inside the device.
How does a die casted heat sink work?
Different types of heat energies are produced in the devices. It can be electrical, mechanical or produced due to friction. Die casted heat sink works to prevent the heat from accumulating inside the system and improving its life span. The heat sink works in the following steps:
- The system produces heat from all the processes occurring inside.
- Heat moves toward aluminum heat sink through either active or passive methods. Heat pipes are also applied sometimes to move the heat away from the source.
- Heat transferred to the aluminum heat sink spreads across the fins. Since the aluminum heat sink is a conductor of heat, therefore the flow is smooth.
- Heat slowly moves away from the aluminum heat sink and releases into the surroundings which are cooler than the source and aluminum heat sink.
Why does a die casting heat sink have fins?
Die casting heat sink works to dissipate the heat and fins are an important part of this setup. These are narrow plates through which heat travels from a hotter place to the cooler environment. It enters through one end of the fins and keeps on dissipating into the fluid until it reaches the other end.
The fins reduce the heat transfer to the other side as they keep on decreasing the temperature of the components. The spacing between fins play a vital role in the heat dissipation effect. If the space between the fins is narrow, less heat will transfer and hence the component will cool down slowly but if the spacing is kept wide, the air easily passes through it and cools down the component.
What materials are best for manufacturing a die casting heat sink?
As a die casting heat sink is required to transfer heat from the casted components, therefore the material for the heat sink should be a conductor. The following materials are used in the manufacturing of the aluminum heat sink.
Copper
Copper has the highest thermal conductivity as compared to other ideal materials for heat sinks. It shows a conductivity of 223 BTU. This makes it suitable for the production of heat exchanging devices.
Aluminum
Aluminum has a very low conductivity when compared to copper but still has a high conductivity i-e 118 BTU. Aluminum also makes up a good heat dissipater. The aluminum alloy which is mostly used in the production of the heat sink is A356.0. This alloy provides improved thermal properties.
Brass
Brass has even lower conductivity than aluminum. With a thermal conductivity of only 64 BTU, brass is still used for producing heat sink. Brass heat sink conducts heat in an efficient manner.
What are the advantages of using a high pressure die casting heat sink?
Die cast heat sink provides more efficient working of electrical devices. Since the heat sink is die casted, it adds to the benefits.
- The designs can have a variety due to casting.
- The fins for the heat sink can be in different shapes and different sizes with different gaps.
- Complexities of the heat sink designs are reduced. This reduces the need of machining.
- Different channels for heat dissipation can be added.
- The method is cheap when it comes to the production of heat sink due to lesser machining needs. Large volumes make it even cheaper.
- A freedom of product orientation comes with die casted heat sinks. Heat flow is maintained regardless of the orientation of the component.
How is the heat absorbing capability of the die casting heat sink increased?
Die cast heat sink has the ability to cool down electrical and mechanical devices due to its ability to absorb heat. To improve the efficiency of this process, different techniques are applied.
The fins of the heat sink have a direct impact on its working. The spacing between the fins and the number of fins can be increased or decreased to improve the heat sink’s working. Another way to increase efficiency is by embedding inserts in the heat sink. This can create continuity in the heat sink and thus improve the capability of the heat sink to absorb more heat.
What is high density die casting? How is a die casting heat sink more efficient?
High density die casting is more efficient than the standard die casting methods. This process makes the casting procedure more advanced by working with more thermally manageable alloys.
HDDC makes use of a combination of different metals and their alloys to overcome the limitations seen in traditional die casting methods. The parts obtained through high density die casting have better thermal and mechanical properties.
Die casting heat sink is still prioritized over high density die casted heat sinks due to its reliability. Die casted heat sink produces less porosity and is highly suitable for electronic devices. It is cheaper than the HDDP heat sink as a single alloy is being utilized in the production. Lesser machining also makes it cost-efficient.
What are some of the applications of die casting heat sinks?
Die-cast heat sinks are popular in various industries today. Their accuracy and cost-effectiveness make them an attractive option for many buyers. They are incorporated in almost every industry today.
Automobile
Die cast heat sink finds its uses in the automobile industry and is proving to be really beneficial. They are attached to the sensors of the mobile and their control units. Heat sinks combined with radiators are even used in the engines of the automobile and assure the proper working of the mobile. They are even being used in E mobile sensors and engines.
LED
The LED display industry uses this method to ensure the heat flow. LED screens and lights need regulated thermal controls. This is done to extend their lifetime. Heat sinks uniformly distribute the heat in the appliances and provide cooling facilities.
What are the advantages of using aluminum die casting heat sink?
Aluminum is a good conductor of heat. It is prioritized over other metals in the production of heat sink due to its many benefits.
Electrical Conduction
Aluminum is electrically conductive therefore they can be integrated into electrical appliances. They even act as EMI shields in the appliances.
Design
The aluminum die cast heat sinks are highly moldable and hence are designed to increase the features of the heat sink. They are designed in such a way that very little or no machining is required. This makes them cost-effective. All of the features are designed simultaneously.
Pin fin designs
The aluminum heat sinks not only have fins but a pin fin design. This provides a greater density of fins in a lesser areas. Using this design, the heat sink orientation is also made perfect.
In what ways are die casting heat sinks better than extruded heat sinks?
Heat sinks are manufactured using die casting as well as extrusion. Heat sinks developed using extrusion are being used at an industrial level and are now being replaced with cast heat sinks. The reason for the replacement is the limitation of extrusion.
- Extruded heat sinks only work where there is adequate airflow whereas die cast heat sinks do not have such limitation.
- Extruded heat sinks require a lot of machining as well as post-machining handwork. Die-cast heat sinks require very little to no machining.
- A die cast heat sink provides a greater height to thickness ratio than extruded heat sinks.
- Die cast heat sinks have better aerodynamic and cooling efficiency.
What sort of machining is required for an aluminum die casting heat sink?
Aluminum die cast heat sinks is very beneficial. To make it more efficient, different techniques are applied to the heat sink.
To produce a neat and smooth-edged aluminum die casted heat sink, deburring is applied to it. This is required when an unwanted surface appears on the product. Sometimes drills are used for this purpose.
Wet coating
This is a technique in which liquid paints the object in order to make it more durable and presentable. Aluminum die-casted heat sinks are wet coated using spray guns or pressurized vessels.
Powder coating
Colored powder particles that are charged are sprayed over an aluminum die casted heat sink in order to increase the life of the part. This prevents the heat sink from chemical and detergent impacts.
How does the size of die casting heat sink affect thermal management?
The cooling from die cast heat sink depends upon three factors: surface area, material, and airflow around the heat sink. The heat sink’s surface area or size directly affects the thermal management.
The bigger the die cast heat sink better will be the heat flow. The bigger heat sink will have either more fins or more spacing between the fins. This will make die casted heat sink a better conductor of heat. The bigger surface area will allow more air to pass through it and the heat that heat sink is conducting outside will cool down faster through convection.
What is the difference between an active and passive die casting heat sink?
Heat sinks are configured using two methods- active and passive methods. The type of configurations defines the efficiency of the heat sink.
Passive heat sink
This die cast heat sink makes use of convection methods. The heat itself flows towards the fins due to its buoyancy with no other control systems. The process is continuous and is constantly generating airflow around and inside the heat sink. This configuration is cheaper but is less effective than active configuration.
Active heat sink
The active die casted heat sink makes use of additional fans employed inside the setting. These fans blow the hot air from inside the component to the heat sink. Sometimes, a case fan is used instead of common fans that draw the cooler air from outside and blow the hot air from inside. This process is efficient as it increases the total thermal gradient.
How is the design of a die casting heat sink made more efficient?
Die casted heat sink provides an efficient solution to the heat-conducting problems. This can be made even more efficient by applying some techniques over it.
Fins
The fins of the heat sink are placed for the flow of heat from the component to a cooler environment. Increasing the aspect ratio of fins also increases the efficiency of the heat sink. The distance between the base of the heat sink and the fins has to be reduced in order to increase the heat flow.
The efficiency of the heat sink also depends upon the shape and size of the fins. These are configured on the basis of the type of component heat sink is working with. The arrangement of fins also affects the heat flow.
Material
The material used in the production of die casted heat sink directly affects its efficiency. The ideal material is the one with the highest thermal conductivity. The selection of material is based upon different factors including conductivity and price of the material.
Heat sinks attachment
The way die casted heat sink is attached to the device defines how the heat is conducted to it. To increase the efficiency, the heat sink is attached at the most appropriate place using methods like standoff spacers, flat spring clips.