Sunrise Aluminum Die Casting Components
Aluminum casting products at Sunrise are developed to deliver on performance, durability, and efficiency in all types of projects.
We are involved in manufacturing aluminum die casting parts delivering excellence. The material being used in the production is selected carefully and meticulously to expand possible applications. Looking learn more about aluminum die casting.
Aluminum alloy has been a special in-demand option in the market because of its beneficial features and cost-effectiveness. Over the years, the die casting process has led to breakthroughs in industries.
Your Perfect Aluminum Die Casting Parts Coming from Sunrise High End Production Equipment
Aluminum die cast components are produced using high-tech machinery and sophisticated tooling. At Sunrise, we are equipping high advanced manufacturing equipment and we will keep on investing necessary high-end machinery. With the advanced equipment, we can keep our production accurate and reliable.
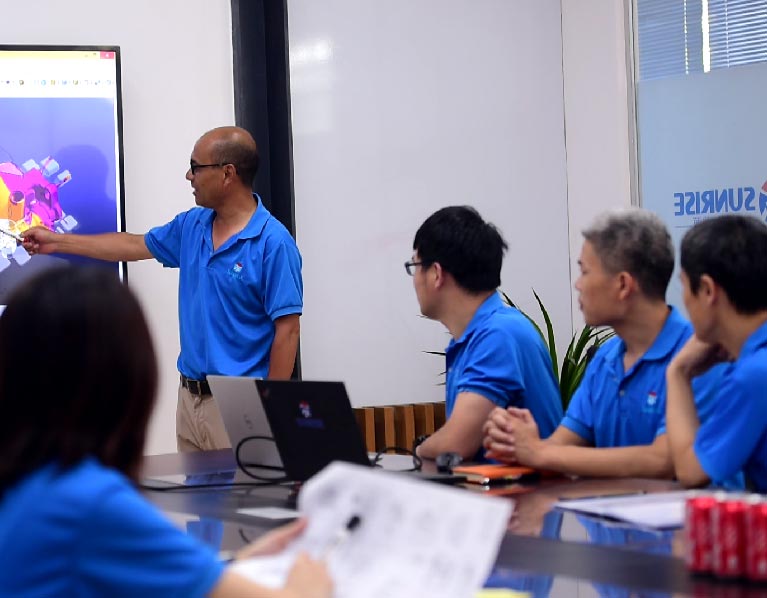
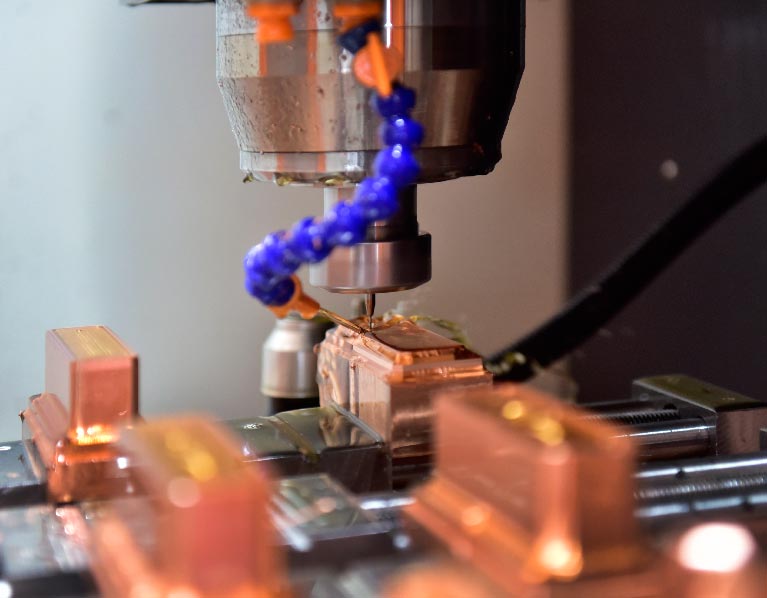
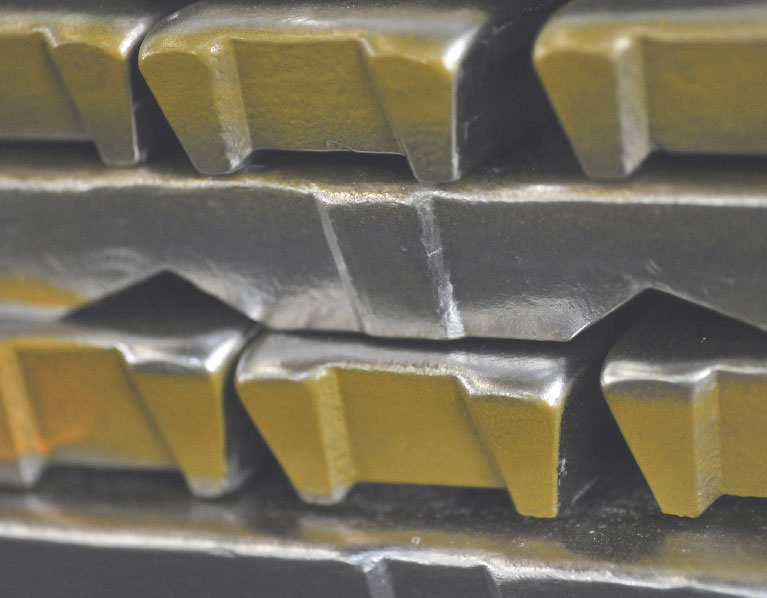
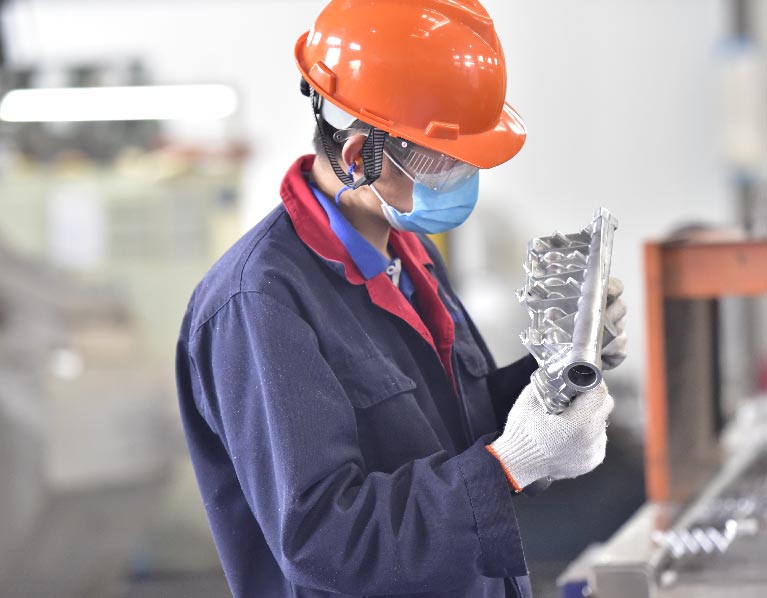
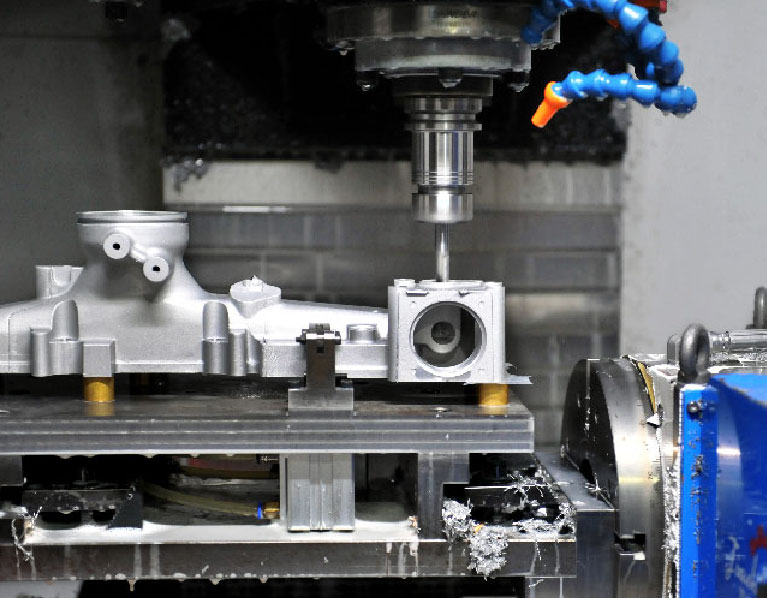
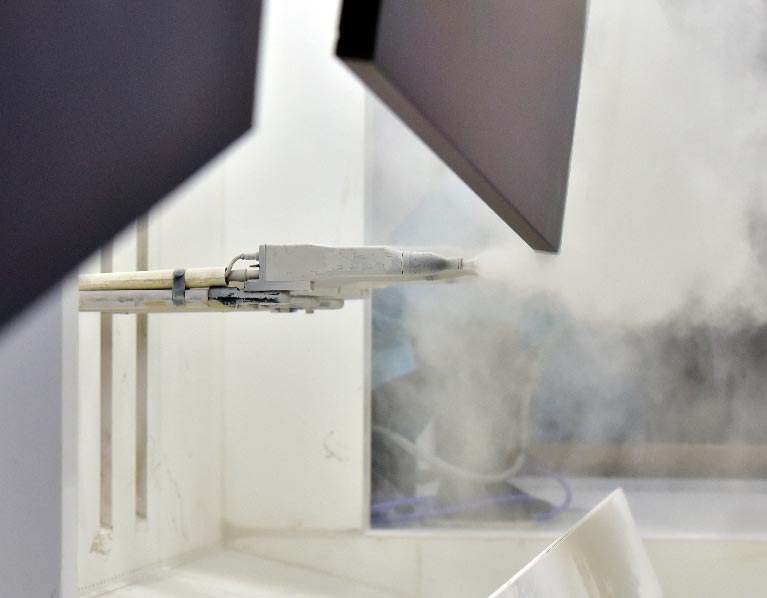
Advanced Measuring Equipment Ensure the Quality of Aluminum Die Casting Products
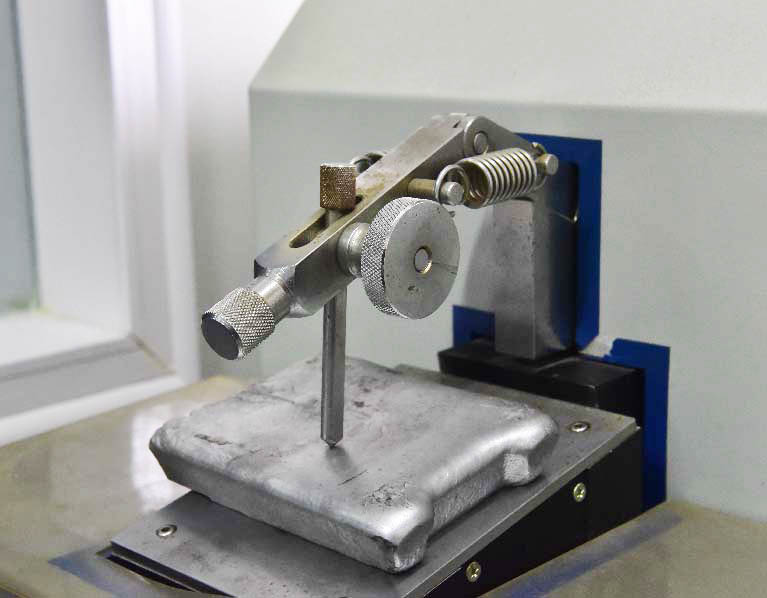
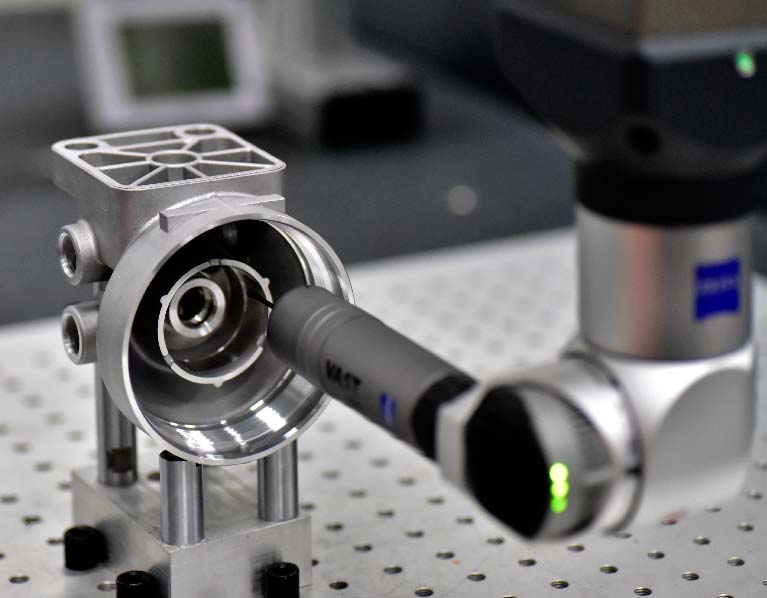
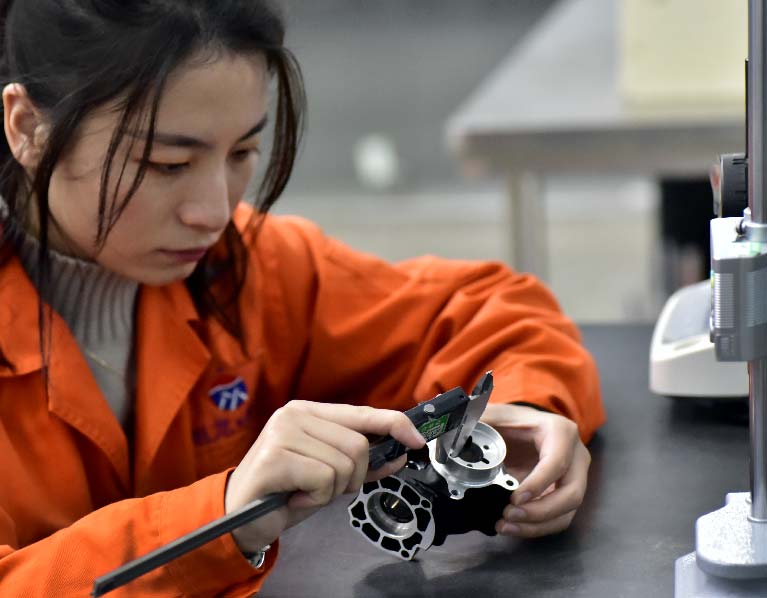
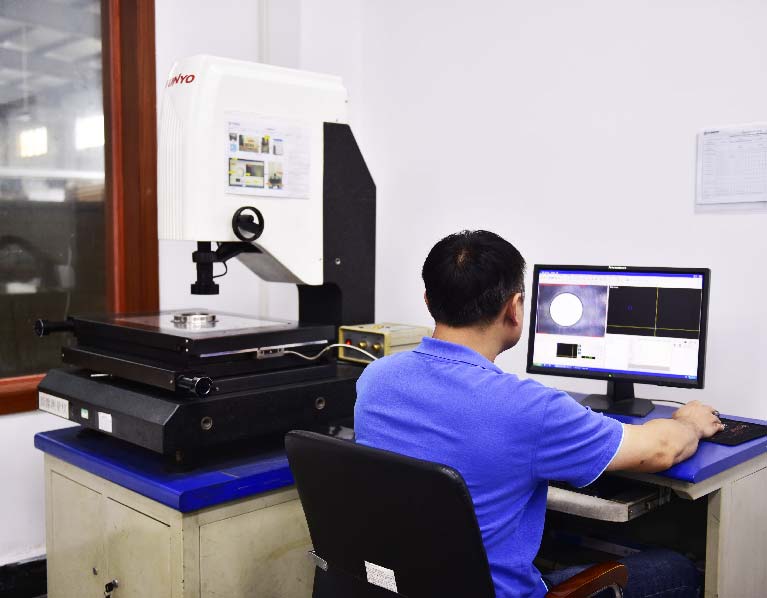
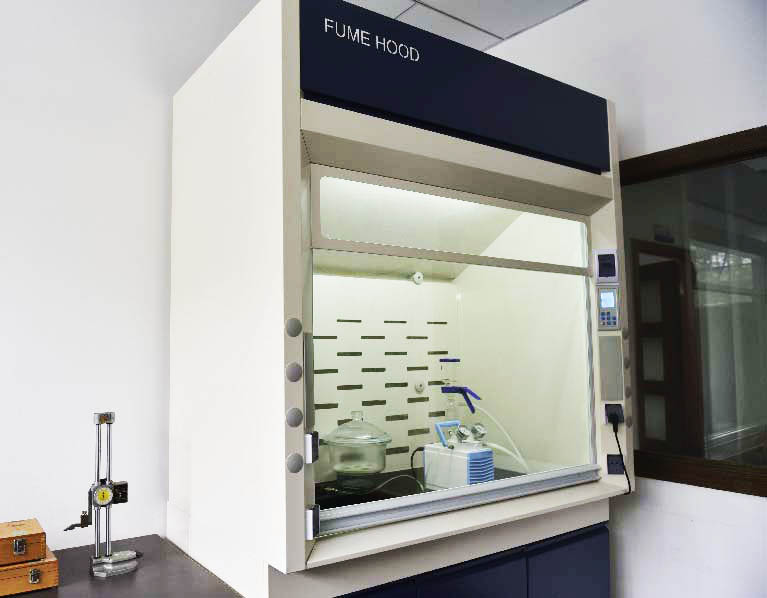
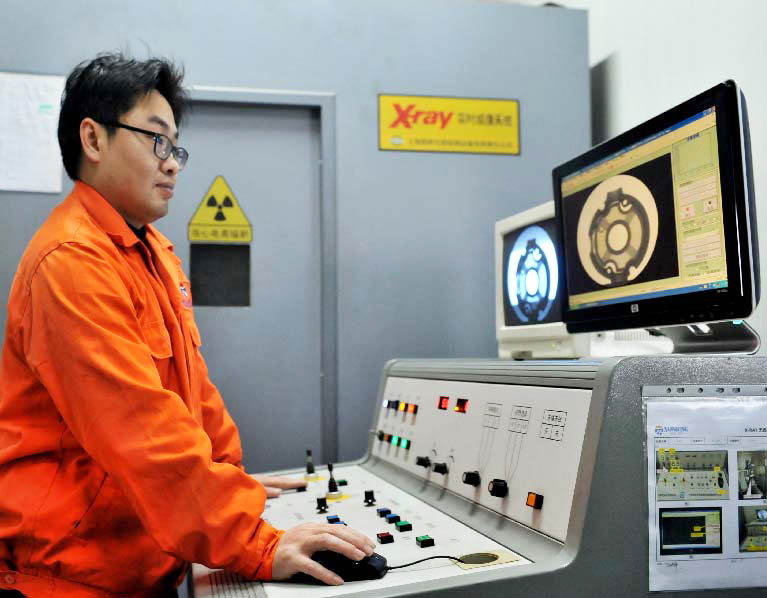
Aluminum Die Casting Samples
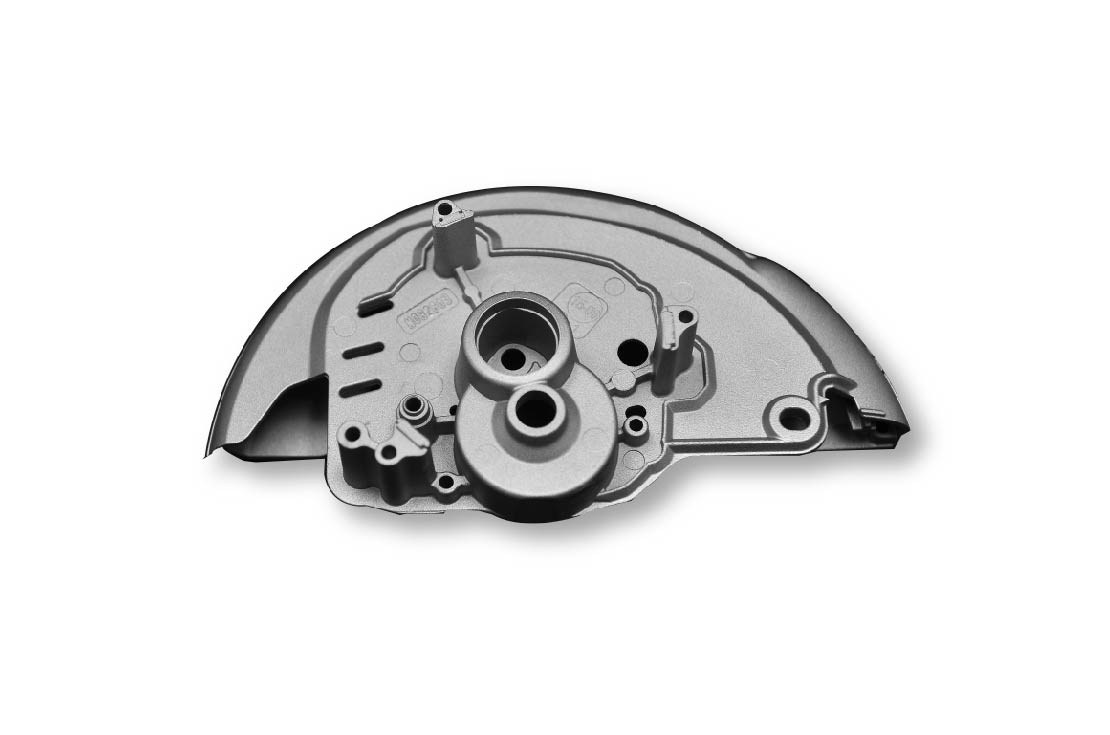
Part Name: POWER TOOL HOUSTING
Material: ADC380
Size: 300x150x80mm
Weight: 450g
Machine Tonnage: 400T
Surface Finish: Powder Coating
Production Process: Die Casting–Trimming–Deburring–Shot Blasting
–CNC Machining–Chromating–Coating–Printing–Screening–Packaging
Applied Industry: POWER TOOL
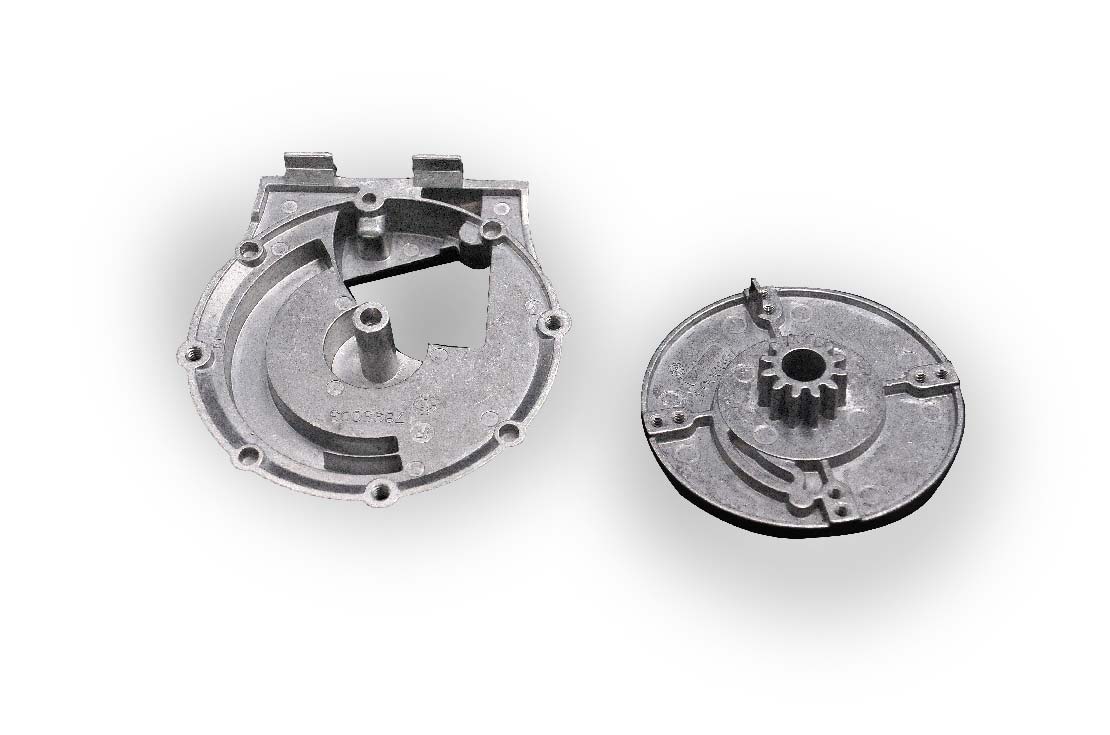
Part Name: GEAR VALVE
Material: ADC12
Size: 140x133x45mm
Weight: 230g
Machine Tonnage: 160T
Surface Finish: Powder Coating
Production Process: Die Casting–Trimming–Deburring–Shot Blasting
–CNC Machining–Chromating–Coating–Printing–Screening–Packaging
Applied Industry: CRUISE
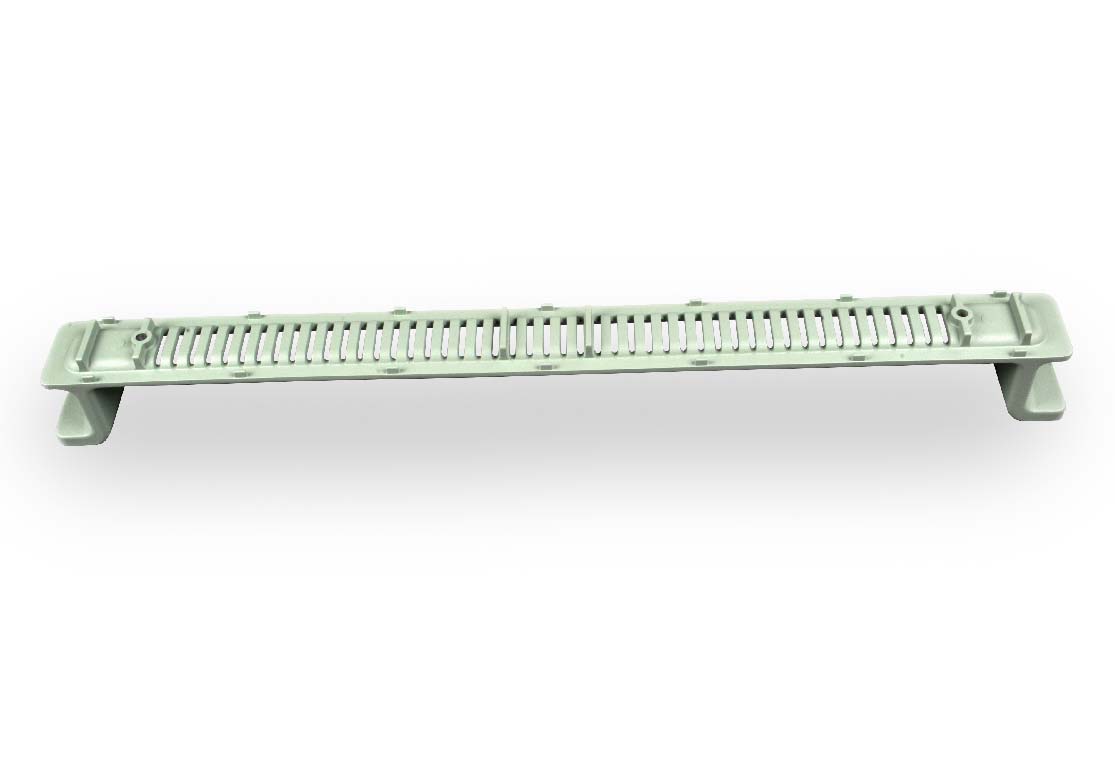
Part Name: Medical Casting BRACKET
Material: AlSi12
Size: 412x46x36 mm
Weight: 182g
Machine Tonnage: 400T
Surface Finish: Chromating
Production Process: Die Casting–Trimming–Deburring
–CNC Machining–Powder Coating–Screening–Packaging
Applied Industry: Medical
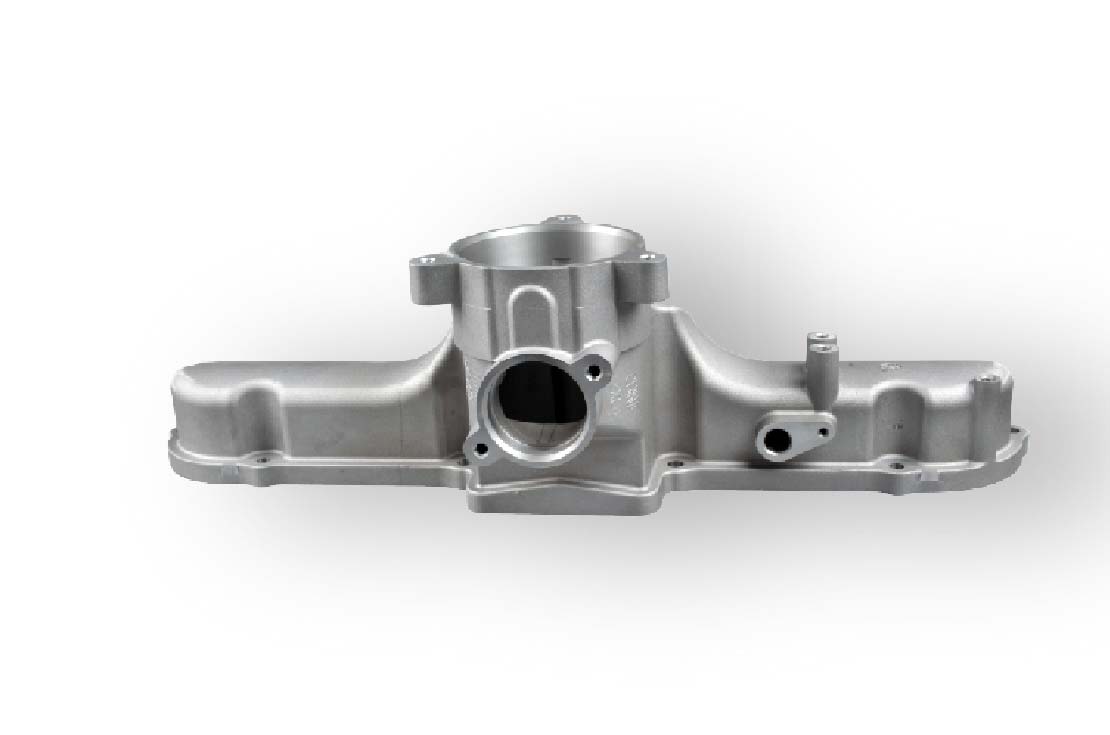
Part Name: Automotive Intake Tube
Material: ADC12
Size:451x138x125 mm
Weight: 1340g
Machine Tonnage: 800T
Surface Finish: Chromating
Production Process: Die Casting–Trimming–Deburring–Shoot Blasting
–Shoot Blasting–CNC Machining–Chromating
Applied Industry: AUTOMOTIVE
ALUMINUM DIE CASTING PARTS:
THE ULTIMATE FAQ GUIDE
Die Casting Aluminum is the ideal production method for a high volume of parts.
There are many reasons why Aluminum alloys are the most common die-cast metal.
For example, you can have lightweight parts without sacrificing strength. The Aluminum die-casted parts also offer more surface finishing options. Besides, it can stand up to better-operating temperatures.
The components manufactured by die-casting Aluminum also are corrosion-proof, highly conductive, a small stiffness, and exceptionally best strength-to-weight ratio and outstanding RFI and EMI shielding properties. The use of Aluminum is green and sustainable, meaning it has no adverse effect on the environment.
The Aluminum Die Casting is fast and also enables an excessive volume of die casting components to be created rapidly and more cost-effectively. Combine all of the prior info, as well as discover why Aluminum die casting is probably the most preferred choice for customers worldwide.
Our years of experience in die casting aluminum products/parts and the advantages “Sunrise Metal” offers are beyond any other industry. Our industry production experience is certified and centered around the parts requiring close tolerances and strict surface finishes.
- What is the importance of Aluminum Die Casting Parts?
- What are the applications of Aluminum Die Casting Parts?
- Why are Surface Treatment Systems applied to Aluminum Die Casting Parts?
- What are the Typical Mechanical Properties of Aluminum Die Casting Parts?
- What are the characteristics of Aluminum Die Casting Parts?
- What are the advantages of Aluminum Die-Casted Parts?
- Why prefer Aluminum over other metals in Die Casting?
- What are the design tips for Aluminum Die Casting Parts?
- Why choose Aluminum Die Casting for your parts?
- What are the essential facts about using Aluminum alloys for Die Casting Parts?
- What is the Wall Thickness in Aluminum Die Casting Parts?
- What is the excellent castability of Aluminum alloys for Die Casting?
- What is the Versatility and Performance of Die Casting with Aluminum?
What is the importance of Aluminum Die Casting Parts?
Aluminum die-casting parts are probably the most prevalent in these days as it’s utilized in a wide range of industries.
One of the core benefits is that they’re lightweight & keep the capability to resist probably the highest operating temperatures among all of the die casting alloys.
Furthermore, Aluminum has the right level of dimensional stability for complicated shapes and thin-wall applications.
These parts also are chosen and required because of their corrosion resistance and exceptional mechanical properties making them a premium selection for a wide range of industrial applications.
Aluminum die-casting components also have very high electrical and thermal conductivity and also EMI shielding attributes, making Aluminum an excellent option for enclosures for social networking and telecommunication applications.
Besides, it offers shielding-properties while providing excellent heat dissipation for the electric components.
When it comes to handheld applications, Aluminum is an ideal choice because of its lightness.
Aluminum die-casting parts also preferred in automotive and aerospace programs for weight reduction and energy efficiency.
Nevertheless, these areas are also simple to the computer for high precision needs and could be anodized, painted, powder-coated, etc. without dealing with any difficulty.
What are the Applications of Aluminum Die Casting Parts?
Aluminum Die Casting is a vast casting technique serving nearly every application worldwide with significant lead time and consistent performance parts improvements.
The following industries are using the Aluminum Die Casting Parts at a large scale:
- Heavy Equipment
- Medical Devices
- Connectors
- Electrical
- Marine Parts
- Aerospace Parts
- Automotive
- Power Tools
- Consumer Electronics
- Computing
- Networking & Telecommunication
- Handheld Devices
- Industrial Machinery
- Robotics
Why are Surface Treatment Systems applied to Aluminum Die Casting Parts?
The surface treatment is an essential activity because it forms a protective barrier against environmental exposure and to improve resistance to wear and also brings a decorative finish to castings.
Decorative finishes can be put on to the parts through painting, powder coat finishing, plating, polishing, etc.
Nevertheless, protection against environmental oxidation for Aluminum die casting areas may be attained iridate, painting, anodizing, and coatings.
Improved wear resistance could be accomplished with Aluminum die casting items by tough anodizing.
Impregnation of Aluminum die casting parts may be used where a part design doesn’t let the generation of a pressure-tight die-cast through porosity influence by overflow die design as well as the reconfiguration of hard-to-cast functions.
Systems employing anaerobic are required to output sealed, pressure-tight casting with smooth surfaces.
What are the Typical Mechanical Properties of Aluminum Die Casting Parts?
There are some essential mechanical properties of aluminum die casting products.
- Tensile strength (310 MPa): The resistance of Aluminum parts to breaking under tension.
- Yield Strength (276 MPa): In Aluminum, the yield issue is a stress-strain curve, which indicates the cap and start of elastic behavior.
- Elongation (12% to 17%): Increase in length of Aluminum parts before its fractured, when subjected to stress.
- Hardness (60 to 107): Property of Aluminum components that allows them to fight deformation, indentation, penetration, as well as to scratch.
- Shear strength (207 MPa): Strength of Aluminum parts against the type of yield failure when it fails in shear.
- Shear Modulus (26 GPa): The ration of shear stress to the shear strain.
- Impact Strength (Approx. 690 MPa): The capability of Aluminum to withstand s suddenly applied load and is expressed in terms of energy.
- Young’s Modulus (69 GPa to 70 GPa): The stiffness of Aluminum parts.
What are the characteristics of Aluminum Die Casting Parts?
The choice of Aluminum Die Casting components is about the evolution of mechanical and physical properties as well as chemical composition, but most notably, also of inherent lightweight aluminum alloy qualities and their effects on die casting parts.
Furthermore, possible machining and final surface finishing is also a relevant term to consider.
The following are the unique characteristics that are important to consider when selecting the most suitable Aluminum die casting part.
Resistance to hot cracking & pressure tightness
- Corrosion Resistance
- Machining Ease & Quality
- Polishing Ease & Quality
- Electroplating Ease & Quality
- Anodizing – Appearance
- Strength at Elevated Temperatures
- Lightweight
- Strength-to-Weight Ratio
- Electrical Conductivity
What are the advantages of Aluminum Die-Casted Parts?
Aluminum Die-Casting Parts offers a vast majority of benefits.
However, some of the most unique and vital benefits it offers are the following:
- Aluminum die-casted parts are light
- Subtle corrosion resistance to standard atmospheric and marine atmospheres and can be enhanced by anodizing
- High reflectivity and can serve in decorative applications
- Aluminum Die-Casted parts retain their toughness at shallow temperatures
- Aluminum die-casting parts are excellent conductors of electricity and heat
- They are non-toxic and readily recycled
Why prefer Aluminum over other metals in Die Casting?
Aluminum is preferred over other die casting parts because of its low cost, design freedom, part integration, weight reduction, accuracy, stability, high-speed production, heat dispersion, heat tolerance, strength, multiple finishing techniques availability, simplified assembly, and excellent corrosion resistance.
Following the primary tooling and development expenditures, Aluminum die casting turns into one of the most cost-effective methods for producing high volume parts.
Thin wall aluminum die-casting products provide finishes with much greater design flexibility.
Aluminum die-casting can deliver extremely complex parts very precisely and reducing cost and weight overall while improving strength and quality.
Aluminum offers an optimum balance of power, weight, and price, making in great material for weight-sensitive applications requiring strength and durability.
Aluminum die-casting parts are durable also dimensionally stable while keeping close tolerances.
Not one other area has the dimensional versatility as well as heat dispersion qualities of die-cast aluminum parts.
Aluminum die-casting parts can fit the complexity present in plastics while running efficiently in high-temperature environments.
In applications demanding a higher tolerance to oxidation environments, Aluminum provides exclusive benefits over alternate materials.
Furthermore, lightweight Aluminum die-casting components provide the best-combined durability against UV damage, water, and salt.
What are the design tips for Aluminum Die Casting Parts?
Significant segments on the Aluminum die casting design are the choice on sorts of separating lines that will part the segments and make a contact surface between 2 or possibly more parts.
The spot that the engineer puts the line is dictated by geometrical shapes and furthermore the resiliencies of the different surfaces.
You will find 2 possibilities – the engineer can often go using a straight parting line or maybe a broken parting line.
Our recommendation is designing parts with a straight splitting sort since it is the most reasonable choice so far as tooling costs.
When making a decision, the engineer should consider the following factors:
Customer’s Specifications: The customer’s tolerance requirements must be the priority and can sometimes be challenging. However, these requirements and specifications must be a priority.
Die Costs: A straight splitting line can help bring down the cost of tooling.
Machining: Aluminum die-casting components that require post-production machining or even often require critical tolerances or perhaps could have finishing specifications should be one of the core emphases of the engineer.
Aluminum Flow: The value of the filling procedure is wholly determined by the positioning of the gate inlet. However, through flow simulation software, the production process can be predicted, and design can be further enhanced.
Want to know more design tips? You definitely need to check out our Ultimate Design Guide For Aluminum Die Casting Parts.
Why choose Aluminum Die Casting for your parts?
Aluminum die casting is the perfect creation technique for high volume parts.
Especially parts that require unique properties to perform under general or some unique environments.
Also, the lifespan of Aluminum die casting typical molds and tooling is between 80k and 100k of shots.
These common reasons alone show why Aluminum is the best die casting manufacturing method for your parts and an ideal option worldwide.
The die-casted parts through Aluminum give EMI/RFI protecting, unbending nature, and solidness with negligible weight.
Furthermore, due to Aluminum’s electrical performance, aluminum die casting becomes ideal for electronic connectors and housing.
The property of Aluminum’s withstand in high operating temperatures makes the die-casted parts even more unique.
What are the essential facts about using Aluminum alloys for Die Casting Parts?
Die casting is a flexible means of developing Aluminum into a broad array of products and parts.
Products as power transmissions and car engines are all produced through the Aluminum die casting process.
Following are some of the essential facts about using Aluminum for die casting parts:
Die casting for lightweight and strength: Aluminum’s qualities of lightweight and strength bring primary benefits when die-cast into parts.
Die casting must include a part-removal design: Aluminum die casting products must be made to suit every time of the strategy.
Aluminum die-casting parts with cavities: Sometimes producing cavities within die casting is an important part.
Die-casting in the early history of Aluminum: Irrefutably the principal commercial Aluminum die-casted parts were castings, including lighting up parts similarly as cook wear.
Though generated by way of a centuries-old process, these parts were considered unique and new.
What is the Wall Thickness in Aluminum Die Casting Parts?
The usual wall structure thickness for Aluminum die casting products can range from between 0.040 in (or maybe 1.016 millimeters) to 0.200 in (or maybe 5.08 millimeters).
Furthermore, the minimum wall thickness in large Aluminum die casting parts is 0.080 inches (or 2.032 mm), and minimum wall thickness in small Aluminum die casting parts is 0.040 inches (or 1.016 mm).
However, the wall thickness of these parts depends on:
- The finalized size of the part
- The application of the part
- The part’s configuration
- The Aluminum alloy used for die casting the part
What is the excellent castability of Aluminum alloys for Die Casting Manufacturing?
Die casting is one of the core routs for producing aluminum parts.
Excellent castability for lightweight aluminum alloys has somewhat high fluidity, shallow melting point, quick casting cycles, a comparatively small tendency for very hot cracking, good as-cast surface finishes, and substance stability.
In hypoeutectic alloys, it’s common to refine the overall size of the aluminum crystals by grain refinement for applications requiring a subtle amount of mechanical properties.
In Al-Si alloys, a treatment (eutectic modification) is often used to change the eutectic silicon from the coarse plate-like into excellent fibrous morphology, which is considered as less harmful to the mechanical performance of the Aluminum die-casted parts.
Die casting has its unique strategy for filling the alloy into the mold/die and feeding the solidification shrinkage.
What is the Versatility and Performance of Die Casting Aluminum?
Aluminum die casting products are light, include outstanding physical qualities, substantial dimensional stability, substantial power conductivity, and can easily stand up to higher operating temperatures.
Since corrosion is resisted by the Aluminum and in a position to cast flawlessly, the vast majority of all die casting created worldwide are produced from aluminum alloys.
Aluminum is a flexible material and used for the vast majority of applications, providing physical designers with significant advantages in manufacturing little areas that can stand up to higher operating temperatures.
Aluminum die-casting parts are generally utilized in medical industries and defense as a sturdy and light alternative to different metals while keeping ideal stability.
The Aluminum die-casting parts are likewise exceptional warm conductors for heat dissemination while saving flexibility and inflexibility when utilized for EMI/RFI protecting inside the telecom just as hardware ventures. Thus aluminum die casting heat sink is widely used in various industries.