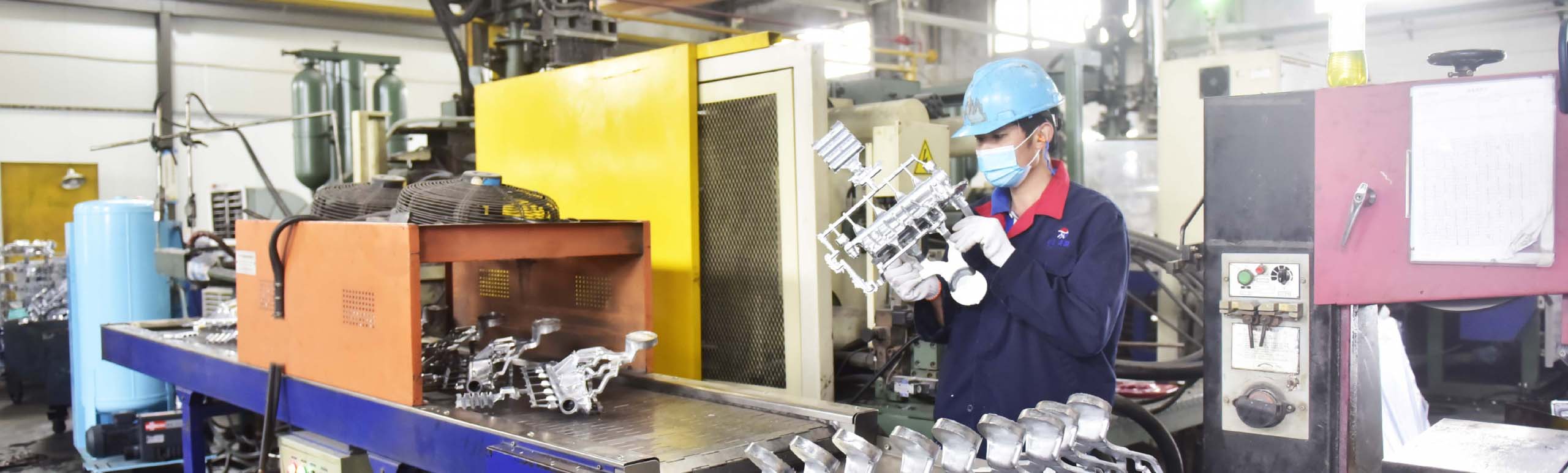
Die Casting Manufacturer - Your Top choice in China
Sunrise Metal is a professional and custom die casting factory in China, with complete solutions for all industries. Our processes maximize component productivity and efficiency using the best resources in the market.
Our high-performance die casting machinery and technology produce unmatched outputs in terms of cost and quality. With a comprehensive overview of the production process, our technical engineers will help you throughout the operations of your project.
From concept designing to production, along with all technical support, we will tailor manufacturing solutions to suit your needs. Our expert designers comply with industry standards and continuously improve the production process to bring you the highest quality die casting products.
2500+ Die Casting Parts Manufacturing Experience From 500+ Global Clients
Sunrise Offers Full Die Casting Capability To Help Your Projects
Our professional engineers can offer design solutions in a variety of industries. We can help you by designing parts to suit mass production & employing state-of-the-art die casting technology & enabling consistently high-quality output.
We implement rigorous quality control measures to eliminate any deficiencies detected on the product. All stages of your project are completely protected with our quality management system. Sunrise complies with international certifications: ISO 9001 & IATF 16949.
As a professional die casting China company, Sunrise Metal continuously invests advanced machinery and technology to produce precise, consistent components: Superior testing equipment and inspection techniques followed by a quality control team, expansive production capability to offer superior die casting and tooling and economical yet full of reliable quality features components.
Our Reliable Die Casting Parts Are Producing From Sunrise Contemporary Manufacturing Equipment
Exhibition for Die Casting Projects
With top procedures at Sunrise Metal in China, you can get quality, efficient, and easy to operate automation to fit precise business needs. The casting created in the process varies in dimensions and weight, and full specifications, according to project requirements.
Die casted parts are commonly used to house thin-walled enclosures and in a variety of appliances and equipment applications. As a cost-effective and productive process, we guarantee quality and success for all our customers.
The die casting components for automobile industries, marine, industrial and commercial, medical, and networking sectors.
- Team Advantage
- Capability Advantage
- Location Advantage
- Order QTY Advantage
Sunrise Metal has skillful organization teams, including experienced engineers, professional customer service specialists, quality control and skilled production workers. Together, they perform at an outstanding pace and impress customers with their abilities.
With 4 dedicated facilities,182 skilled professionals in China, we provide our customers 1-stop die casting solution including rapid prototyping, die casting tooling, die casting, CNC machining, and surface finishing to our customers worldwide.
Our company is located in Yangtze River Delta, with 9 Airports, 2 world busiest ports of Shanghai & Ningbo. And the most dense High speed train networks in China/world.
If you have the trouble finding the right die casting supplier in China, Small suppliers cannot ensure the quantity. You need Sunrise Metal where our mission satisfy the demand of your high mix and low to medium volume die casting projects.
Get A Free Consultation
Free engineering consultants for High Pressure Die Casting parts for your projects. If you want to find a right die casting company in China to consult on your die casting project, You can consult Sunrise Metal. Our team creates value for customers and provides solutions based on CAD and Step drawings.
DIE CASTING: THE ULTIMATE FAQ GUIDE
Die Casting is one of the fastest and cost-effective methods for the mass-production of high-quality parts. That’s why the leading companies all around the world prefer to die casting over other methods. Sunrise Metal is your reliable one-stop Die Casting manufacturer with advanced Die Casting Facilities in China.
You will find answers to most of your queries about Die Casting and our service in this guide. If you have any other questions, you can contact our Customer Care as well.
- What is Metal Die Casting?
- What are the types of Metal Die Cast?
- How does Die Casting work?
- What are the advantages of Die Casting?
- What is Pressure Die Casting?
- What is Vacuum Die Casting?
- What is Gravity Die Casting?
- What is Squeeze Die Casting?
- What is Semi-Solid Die Casting?
- What are the types of Pressure Die Casting?
- Is High-Pressure Die Casting better than Low-Pressure Die Casting?
- When should I choose Die Casting?
- How do you prepare the dies?
- What are the types of dies used for Die Casting?
- What is Draft Angle in Die Casting, and why is it necessary?
- What are inserts in Die Casting?
- What is the difference between Hot Chamber and Cold Chamber Die Casting?
- Is Die Casting expensive?
- What are the different methods of Metal Forming and Casting?
- How is Die Casting better than Injection Molding?
- How is Die Casting better than Forging?
- How is Die Casting better than Stamping?
- How is Die Casting better than Investment Casting?
- How is Die Casting better than Extrusion?
- How is Die Casting better than Sand casting?
- What metal alloys are suitable for Die Casting?
- How do you deal with Porosity in Die Casting?
- What is Aluminum Die Casting and how is it done?
- What are the advantages of Aluminum Die Casting?
- What geometric features should I consider designing a tooling model?
- What surface finishes are available for die-cast parts?
- Can you share your experience in die casting?
- What facility do you have for die casting?
- Can you design the die-cast tooling for me?
- Do you provide DFM and PPAP for tooling?
- Why should I choose Sunrise for Die Casting?
What is Metal Die Casting?
Die Casting is a metal casting technique that is done by forcing molten metal under pressure inside an enclosed mold. This process can mass-produce a product in a short amount of time.
The mold used for casting the metal is called a die. This is why the process is known as metal die cast. The die is usually divided into two parts. One part is static, called a fixed die, the other one is portable, called a moving die.
The dies themselves need to be designed and machined first before they can be used for casting. The process of making dies is called tooling. It is mainly done using CNC Machining, which is a precise and sophisticated process.
That’s why Dies made by CNC Machining is able to manufacture parts with very good precision and repeatability. As an expert die casting factory in China, Sunrise Metal has tooling shop in-house including advanced CNC Machining facilities that can ensure high precision tooling.
We have our own Die Casting facility powered by the latest technology. We can provide you a one-stop solution for Rapid Prototyping, Die Casting Tooling, Die Casting, CNC Machining, and various Surface Finishing.
What are the types of Metal Die Cast ?
Metal Die Cast may be classified into different types according to the method or machine used for casting. Though, the Metal Die Cast process is mainly classified into two types based on which type of machine is used.
They are,
- Hot-Chamber Metal Die Cast
- Cold-Chamber Metal Die Cast
These are two fundamental metal die casting methods that can be done using various techniques. Some of them are,
- Pressure Die Casting
- Squeeze Die Casting
- Vacuum Die Casting
- Semi-Solid Die Casting
- Gravity Die Casting
All of them have their perks and may be adopted for die casting. You will find the details of these methods later on in the guide. We aim to provide you with the proper knowledge of die casting so that you can better understand our die-casting services.
How does Die Casting work?
Die Casting requires some preliminary tasks to be done before you can start producing parts. Die casting can be done using different techniques. The basic process involved in metal die cast is described below.
- First of all, the tooling of the dies is required done. That will require a 3d CAD model of the part. The dies are machined to perfect dimensions using the model data using CNC Machines.
- Once the dies are ready, they are placed into the die casting machine and enclosed together.
- Then molten metal is poured inside a hole that is linked with the dies.
- The molten metal inside the hole is pushed under pressure, and it spreads uniformly inside the die cavity.
- Then it is left for a while for cooling down, and the dies are separated once it’s done.
- There will be some excess metal attached to the parts that are trimmed down using a trim die.
Then your part is complete. The whole process is automated and takes a very short amount of time. You can check out the video below to see how die casting is done.
What are the advantages of Die Casting?
Die Casting is one of the most efficient and methods available for mass-producing metal alloy parts. Most of the industries that need large quantities of high-quality parts resort to metal die cast for producing them.
Let’s have a look at the advantages of metal die casting that makes it better than others.
High Production Capacity
Die casting is one of the most favored metal casting techniques in the industry for mass production of parts. Once die casting tooling is done, the die can be used for a long time to produce a large number of parts.
The production capacity of die casting can be increased multifold by introducing multiple cavities in the die. Dies have a long lifespan and can be repaired if it is damaged. So, you can continue production without any worries for a long time.
High Dimensional Accuracy
Die cast parts can maintain a very tight tolerance. This is basically because Die casting tooling is done using CNC Machining. And CNC Machining can create molds for die casting with extreme precision.
That’s why die casting has very good repeatability. Parts produced in this method will have homogeneous properties and identical dimensions. So, you can rest assured about the quality of the parts.
Short Lead Time
Die Casting is faster than most other metal casting techniques. Die tooling is the only prerequisite for die casting. With today’s advanced CNC machines that can be done in a fairly short amount of time.
And the tooling process is fully automated and more efficient than ever. Only a 3d model of the parts is required tooling of the dies.
Lightweight and Durable
Die Cast parts can be made lightweight and durable at the same time. Die casting can provide excellent dimensional stability, and thin walls can be incorporated in the design. That allows us to greatly reduce the weight of parts.
But that doesn’t compromise the strength. Die casting is generally done using strong non-ferrous metal alloys such as Aluminum.
Great Surface Finishing
Another thing great about die casting is the fact that it needs little to no additional surface treatment. Die casting can create parts with various types of smooth or textured surface finishes.
So, you don’t have to waste time and resources on the surface treatment of your parts. That makes die casting even more efficient and cost-effective.
As you can see, Die Casting has multitudes of perks. That’s why Sunrise Metal puts its trust in Die Casting to provide its customers with high-quality parts in the most efficient manner.
What is Pressure Die Casting?
Pressure die casting is done by varying the pressure at which the molten metal is being poured. Pressure die casting has been really popular lately due to the advantages it can offer and greatly boost your production.
Depending on the extent of pressure, this process can fine-tune between the cost and quality requirements of your parts. That’s why Pressure die casting is often combined with other techniques to improve performance.
The main charm of pressure die casting lies in its speed of manufacturing. The melt solidifies rapidly and retains good dimensional tolerance. So, it can cost-effectively mass-produce quality parts.
What is Vacuum Die Casting?
Vacuum Die Casting is a casting process done by removing the air from the die cavity using a vacuum pump. The air suction will be done before and during the injection of molten materials. That induces a high-pressure difference during die casting.
Creating a high pressure inside the cavity is the main purpose of the vacuum. That’s why this process is also known as vacuum-assisted high-pressure die casting.
This process reduces porosity inside the die-cast parts. That can help increase the strength and rigidity of the product. It also enables heat treating and welding and improves the surface finish of the parts.
What is Gravity Die Casting?
Gravity Die Casting process involves filling the die cavity with molten metal or alloy from a container under the force of gravity. No other external force is required for this process. Though the mold may be tilted during the filling process.
Gravity Die casting is an old technique and has been used for metal casting for a long time. There are fewer pores in the parts due to the gradual filling of the cavity.
The parts also achieve a nice surface finish, and additional treatment may not be required depending on the quality requirements. This process can yield parts with good mechanical properties.
The process is usually done manually, but it can be automatically using some simple mechanism. The gravity die casting process is rather slow and may not be ideal for mass production of parts.
What is Squeeze Die Casting?
Squeeze Die Casting is basically a combination of gravity and low-pressure die casting. The casting is done in a similar fashion to the gravity die casting. But the die needs to be preheated first.
The die cavity is slowly filled with molten material. Once the whole cavity is filled, then pressure is applied to the melt. That shrinks the volume of the melt inside the cavity and greatly reduces the chances of leaving gas pores inside the manufactured parts.
Parts produced using this method will have very good mechanical properties. But this process is done in successive steps, and that will increase the production time and cost too. It may be adopted when you have high strength requirements for the parts.
What is Semi-Solid Die Casting?
The Semi-Solid Die Casting process works with non-ferrous metal alloys while keeping the temperature such that the melt is neither solid nor liquid. It combines the benefits of both Casting and Forging.
The semi-solid die casting process may be done slightly differently depending on the alloy used for production. Alloys with high temperatures can be used in this process, but that is still not much feasible due to the lack of suitable die material.
Die castings done is this process can manufacture parts with a near-net shape. That means that it can produce parts with quality equal to the final parts. Because the parts may not need or need a minimum level of finishing once produced.
This method can save some production costs due if you are ok with a traditional finishing. But it is a sophisticated process and sensitive to ambient temperatures. So, in order to maintain the operating conditions, expensive equipment is required.
What are the types of Pressure Die Casting?
Pressure die casting is classified based on the extent of pressure that is applied during the casting process. It can be classified into two types.
- High-Pressure Die Casting
- Low-Pressure Die Casting
High-Pressure Die Casting
In the case of High-Pressure Die Casting, the molten metal is poured in a chamber, and it is pushed inside the dies under very high pressure. Die casting that is done this way is to ensure that the molten metal reaches all critical areas of the parts.
Low-Pressure Die Casting
Low-Pressure Die Casting uses less pressure, and the mechanism is also different. Usually, the die is placed above, and molten metal is pushed upward with pressure. When the casting is full and solidifies, the pressure is released.
Is High-Pressure Die Casting better than Low-Pressure Die Casting?
Most of the industries prefer High-pressure die casting over Low-pressure die casting. Because High-Pressure Die Casting is much faster and yields more precise parts compared to Low-Pressure Die Casting.
Low-Pressure Die Casting can produce complex parts with parts of great strength value. The parts can maintain good precision and has a high production capacity as well. But the lead time is relatively high and results in a slower casting cycle.
Another problem with Low-Pressure Die Casting is that the wall thickness requirement is much larger. So, the provision of thin walls is harder in this case. High-Pressure Die Casting eliminates some of these issues.
The high pressure applied on the melt forces it to travel places with tight tolerances. That’s why the manufacturing of complex parts is possible in this method. The possible chances of defects in the parts are also minimized.
The surface finish obtained by High-Pressure Die Casting is also very good. That reduces the need for further surface treatment of your parts. That can save both time and resources for producing your parts.
Because of these facts, High-Pressure Die Casting is preferred more often for efficient and cost-effective manufacturing.
When should I choose Precision Die Casting?
Precision Die casting is preferred over other technologies of casting, mainly when you need to produce a large number of parts fast and accurately. You can produce parts much more cost-effective as well.
There is a wide variety of metals to choose from as well. There are different alloys offering varieties of physical property to meet your requirements. There is also the option of producing parts with different textures.
But a significant reason why people choose metal die cast is because of the repeatability it can offer. You can get identical parts for your product with lower production time. That’s really important when you need consistency in your manufactured goods.
How do you prepare the dies?
Die is a special type of tool that is used to manufacture products or parts by means of a machine press. But before they can be used to manufacture anything, the die itself needs to be designed and produced first.
The process of making a die is called tooling. It is usually done by manual or CNC Machining. Manual die tooling is not preferred now due to a lack of accuracy and possible chances of manmade error.
Now the tooling process is done by a Computer Numerical Control machine. All you need to have is a 3d model of your product or part. The Model is then programmed to be read by a CNC Machine.
The Model is usually divided into two or more parts to make the tooling process simple. Once all the initial preparation is done, the rest of the job is automated.
The material used in the die is also important. The die material is usually chosen based on your product material and quantity to be manufactured. Die made with high-quality materials will last long, but of course, it comes with a reasonable increase in the cost.
What are the types of dies used for Die Casting?
There are different types of dies available for use in metal die cast. They may be differentiated based on their structure or purpose. Which type of die should be used usually depends on production quantity and part’s design.
Dies may be classified into these categories based on their structure:
- Single Cavity Die
- Multiple Cavity Die
- Unit Die
- Combination Die
A single cavity die will have only one cavity when dies are formed together. That will allow only one part to be die-cast at a time. While multiple cavities die to have more cavities and have the ability to produce several parts at once.
A unit die is more like a smaller die of specific dimensions that can fit inside a master die. Unit dies are a great way to reduce costs. Combination dies are more like a variation of multiple dies, and it has multiple cavities with different designs.
What industries are using Die Casting?
Die Casting is widely used by industries all over the world for mass producing high precision parts. Its high repeatability, speedy and cost-effective production method has enabled industries to ensure continuous supply of their products at lower cost.
Some major industries that are using Die Casting are,
- Automotive
- Aerospace
- Electronics
- Medical
- Home Appliances
- Kitchenware
- Military
- Telecommunication
- Marine etc.
There are other industries as well that use Die Casting for mass production of their product components.
What is Draft Angle in Die Casting, and why is it necessary?
Draft Angle is the amount of taper provided along the wall of the die cavity. It is provided along the parting line of the dies. It allows easier separation of the die-cast part from the dies. Without it, there can be a significant rise in the production difficulty and, eventually, the cost.
The typical example of a draft angle would be glass. Regular glass has a minimum diameter at the bottom and maximum at the top. Now Imagine a glass of water is frozen. You can easily take the ice out of the glass.
But if the glass has a smaller diameter at top and larger at the bottom, what would happen? It would look similar to a glass put upside down. Now, when you freeze the water inside a glass of this shape, can you pull out the ice? No. Because the ice would be stuck.
A similar phenomenon will happen if you don’t include a proper draft angle in your design. The more draft angle you can provide in the design, the easier it will be to detach your parts from the mold after casting is complete.
It may not seem like a big deal at a glance. But you will face production difficulty such as the creation of vacuum and friction during ejection from the die. That can damage your parts and die as well. So, all designs need to have proper draft angles while designing.
What are inserts in Die Casting?
Die Inserts are detachable smaller dies used in die-cast manufacturing. Die Inserts are much smaller than a regular die and require much fewer materials. It can simply be placed inside a bigger fixed master die where there is space to place the insert in it.
Die Inserts need less investment compared to a conventional die. There will be a significant saving in materials needed for die manufacturing. Because you will only need to have one full-sized die. Then you can use smaller sized inserts in them.
That is very handy for making high mix parts of low volume economically. But the frequent inserts shuffling may not seem appealing when your production demand is great. Multiple die-cast machines with regular dies may be desirable for parallel production of parts.
You may be thinking about designing a multiple cavity die insert for high mix parts production. But Inserts are smaller in size and may not have enough space to incorporate a multiple cavity inside.
What is the difference between Hot Chamber and Cold Chamber Die Casting?
Most of the metal die cast can be done using either a Hot Chamber or Cold Chamber method. But which one to use actually depends on the material used for casting. Both of them are important processes, and one doesn’t necessarily fulfill the needs of the other.
Hot Chamber Die Casting is used for metals with a low melting point. The advantage of this system is that the material can be molten in the casting machine. The melt can simply be collected through a hydraulic-powered piston.
That helps reduce the time between casting cycles. But Metals with high melting point such as Aluminum can’t be used in a Hot Chamber Die Casting Machine. Alloys of Zinc, tin, led are suitable for this process.
Cold Chamber Die Casting, on the other hand, deals with metals alloys with a high melting point. That is the reason. Aluminum die casting is always done with Cold Chamber Die Casting. Magnesium and copper also have a high melting point and are suitable for this method.
The metal needs to be molten outside of the Casting machine in case of Cold Chamber Die Casting. That slightly increases the duration of the casting cycles. But the materials used in this are stronger and more durable.
So, Cold Chamber Die Casting allows casting with better materials. That’s why it is more preferred in the industry for the production of high-quality parts.
Is Die Casting expensive?
Not really, it is rather cheaper than most other methods of casting. Metal Die cast is a technology used for mass production of parts. The initial cost of tooling is a bit high, but that is only a one-time investment.
Metal Die Casting is one of the most sophisticated processes for metal casting. It can create parts with extremely tight tolerances and very good surface finishing. You can accept near net shape parts with die casting.
If you want to achieve a similar result with other methods of casting then you have to take into consideration the speed of production, mechanical properties, and surface finishing of your parts. Don’t forget about the overall production cost as well.
Industry leaders put their trust in die casting due to its production capacity, quality, and cost. When you are going for mass production of your parts, the initial investment will be the least of your concerns.
While there may be some cheaper options, there is often material restriction, and production lead time may be greater. Most methods will also require your parts to go through additional surface treatment that will ultimately increase your production cost.
So, if you need to mass-produce quality parts fast and precisely, then die casting would be a cost-effective solution.
What are the different methods of Metal Forming and Casting?
Die Casting is one of the many casting methods available. Other metalworking techniques have their own advantages and limitations. Each of the methods has their specific applications and have certain material and quality restrictions.
Let’s have a look at the different methods available for casting and forming metal parts:
- Die Casting
- Injection Molding
- Forging
- Stamping
- Extrusion
- Investment Casting
- Sand casting
The number of options available for metalworking may be tempting and leave you confused about which one to pick. So, you can check out the relative comparison between other methods to make sure whether die casting is what you need.
How is Die Casting better than Injection Molding?
Injection Molding, also known as Plastic Injection Molding, is a process of manufacturing by injecting molten material inside a mold. The process of Injection Molding and Die Casting is basically the same, and some of you may confuse these two processes.
The main difference in both of the processes is the material used for production. Die Casting is a metal casting technique where various metal alloys, commonly Aluminum, are used as a production material.
In the case of Injection Molding, glass or polymer is used as a material depending on your requirement. If you need metal parts or parts with high strength, thermal, and electrical conductivity, then injection molding is not needed.
If you are a plastic product manufacturer and need plastic parts, then Injection Molding would be sufficient. Because Injection Molding operates at lower temperatures and uses cheaper materials.
The mold production is done in the same way in both cases. So, the overall cost of production for low volume parts would seem too high for plastic parts. You may decide to go for die casting instead, which will yield better quality and more durable parts.
How is Die Casting better than Forging?
Forging is a manufacturing process that involves shaping metal to the desired shape using compressive forces. Forgings are one of the oldest techniques for metal casting and have been used by metalworkers whom we refer to as a blacksmith.
Forging used to be a manual process where metal is given shape by hammering. But today’s advanced technology has redefined the process of forging metal. Now, the process is mostly automated and done much more efficiently.
Forging is often preferred for producing parts even stronger than a machined casting or pure machined part. But forged parts require a great deal of processing, and the production time is more compared to that of die-cast parts.
Forging can’t produce parts as accurate as die-cast parts and often require machining afterward. Die casting can produce parts with very tight tolerance, and the production speed and cost of die casting is much less compared to forging.
So, for mass production of any parts die casting would be a better choice that will ensure a good quality standard with less time and money.
How is Die Casting better than Stamping?
Stamping is a manufacturing process where a flat sheet of metal is pressed against a die to give it the desired shape. That’s why it’s also known as Pressing. The most common stamping process is done by punching the sheet using a machine press.
The other stamping processes include blanking, blending, flanging, embossing, etc. Die Casting, and Stamping is a totally different process and carried out for manufacturing different types of parts.
Stamping can work with both ferrous and non-ferrous metals, unlike die casting. But it is limited to sheet metals only and can’t work with ingots and billets. So, when you need simple flat metal parts stamping may be much faster.
Die Casting, on the other hand, has a vast manufacturing capability. It is possible to manufacture parts ranging from simple to very complex. The initial tooling cost is much less for simpler parts, and that actually makes die casting a viable choice for flat metal parts production as well.
How is Die Casting better than Investment Casting?
The principle of Investment Casting is based on an old metal casting technique known as lost-wax casting. Investment casting requires several steps to be followed for manufacturing a part.
First of all, the shape of your desired parts is formed using wax. Then the wax is dipped inside a slurry of a suitable refractory material. Once the refractory material hardens, the wax can be melted by heating and removed.
That way, you will get mold and use it to cast metal parts. Castings done this way have the capability to produce parts with some special geometric features, which is often not possible to produce using most other manufacturing methods.
Investment Casting is also preferred for its ability to produce parts with high precision, and it can work with both ferrous and non-ferrous metal. But, the downside of Investment Casting is that it has a longer lead time compared to other methods.
Investment casting has a significant amount of production costs involved. Unless the parts to be manufactured, have a geometry that can’t be manufactured easily using other methods, die casting would yield parts much faster and cost-effectively.
How is Die Casting better than Extrusion?
Extrusion is a manufacturing process used for producing metal parts with a fixed cross-section. It is done by pushing material through a die of the desired cross-sectional profile. That will yield a long part with uniform cross-section.
The long sections can be cut at a specified length according to the design requirements. Extrusion is a continuous process and can produce parts continuously. SO, a large number of parts can be manufactured with a minimum lead time.
Due to the way this process is done, Extrusion can only produce parts with a long section, and a uniform cross-section. Materials may need to be heated as well for easier Extrusion. But that increases the chance of oxidation of the metal.
Die casting has no limitations like Extrusion and can produce parts of almost any shape. Unless you need long bar-like parts with a uniform cross-section, die casting would be a better choice.
How is Die Casting better than Sand casting?
Sand casting has been a popular metal casting technique all over the world. Sand Casting uses sand as a mold material. Sand is a very common material and available everywhere. That is a major factor affecting the cos of Sand Casting.
Sand molds are very cheap to create, and sand also has good refractory properties. Sand Casting needs very low investment and can be done without any expensive equipment. That’s why many local manufacturers use Sand Casting.
But a cheaper solution won’t necessarily be the best one. Sand Casting is only cheap when done in smaller quantities. Sand casting has very poor casting quality. It is not so accurate and often has defects in the parts.
Sand Casted parts have a rough surface and need additional treatment later on. If you need a smooth surface for your parts, that will ultimately increase the production cost. So, Sand Casting is not a choice for parts that have delicate applications.
That’s why the leading companies choose to die casting for producing high quality and precise parts. Even though the initial high cost, die casting is proven to be more economical in the long run.
What metal alloys are suitable for Die Casting?
Die Casting is normally used to cast non-ferrous alloys. There are a good number of non-ferrous metals out there, but only a few of them are preferred for metal die cast. They are,
- Aluminum
- Zinc
- Magnesium
- Copper
- Brass
- Lead
- Tin
Aluminum Alloys are the most popular ones out of them. Magnesium and Zinc are also used for utilizing their properties in some cases. These are easy to handle and cast and have more demand.
Each of the materials has its special properties and used when that property is required in part. The melting point is an important parameter in metal die casting. If the manufacturer has a cold chamber die casting facility, then alloy with a high melting point would be suitable.
Low melt point Alloys such as Magnesium and Zinc are suitable for a Hot chamber die casting process. Aluminum has a high melting point and is suitable for a Cold Chamber Die casting process.
How do I choose the right material for metal Die Casting?
There are several factors to keep in mind when selecting the material for die casting. Die casting is basically a process for casting metal. So, based on what parameters you should choose the metal is the real question here.
Let’s have a look at the parameters to consider when choosing a metal for die casting.
Mechanical Strength
The requirement of the mechanical strength of your part is necessary when choosing a metal. The application of your part should be considered for this.
Your parts must be able to withstand the load imposed on it during service conditions. If your parts have a medium strength requirement then most of the metals will be just fine.
Thermal Conductivity
Thermal properties are very important for die-cast parts that will be used in engines, cookware, and other products that deal with high temperatures. For high thermal conductivity Aluminum is recommended.
Electrical Conductivity
You may need your parts to have a high electrical conductivity or have insulating properties. That depends on the field of application of your parts. Make sure you choose the material considering the scope of usage of your parts.
Cost
Now comes the most important part, cost. No matter which metal is used, you have to keep in mind the budget as well. Don’t go for costly materials to achieve properties that greatly surpass your requirements.
But deciding on a cheaper metal without assessing all the parameters will result in compromising the quality. Always go for something that balances between both cost and performance.
What is Porosity in Metal Die Casting and why does it occur?
Porosity is the gas pores or voids that are formed during die casting. It is a type of defect in die-cast parts. It is usually formed once the molten metal cools down. Because there is a large amount of dissolved gas present in the melt that is released upon solidification.
There are other reasons as well that can cause gas pores to form in a casting. Such as the turbulence during pouring the melt or due to metal shrinkage which causes vacuum holes to generate.
Porosity can be minimized to a certain extent, but it can be hard to get rid of it completely. The percentage of porosity induced by different metal die casting methods are different. The way the material is prepared and cast play a big part in controlling porosity.
The gas pores may form on the surface of the casting or inside of it depending on the casting method. Porosity in casting is not harmful if it is present in a low amount. But an increased percentage of porosity in a casting can affect the mechanical strength of it.
How do you deal with Porosity in Die Casting?
Porosity can be formed due to several factors. So, it is important to take care of all the possible causes to keep the percentage of porosity to the minimum. Sunrise Metal has advanced quality control equipment and experienced engineers, who are experts in dealing with porosity.
Here’s a detailed explanation of how porosity can be dealt with.
Controlling the temperature
The temperature of the metal and die is an important factor. Some metal alloys have different gases such as Hydrogen, Nitrogen, Oxygen dissolved when in their liquid form. These can cause gas pores to form after casting.
It can be reduced by melting the metal in a vacuum of low-solubility gases. Lowering the superheat temperatures can help reduce the porosity. The die can be heated as well to remove the excess moisture that can cause hydrogen gas to form.
Proper design for manufacturing
Any parts need a design for manufacture first. Some design considerations are required for the proper casting of your parts. There should be a provision of gates, vents, and overflow in the die casting mold to allows easy removal of the air.
Otherwise, the air gets trapped inside the dies, and pores are formed in the casting. Sunrise Metal’s expert team of engineers can carry out these tasks to ensure pore-free die casting.
Machine Operating
The shot speed and pressure of a die casting machine affect the porosity of the casting. When the melt is pushed into the die cavity at high speed the turbulence is increased. That causes more air to enter the die cavity.
It can be minimized by creating a vacuum. It will allow the air inside the die cavity and those entering from outside to be flushed out faster.
What is a trimming die and what is its function?
Trimming Dies are a special type of die that is used for removing the excess metal from a die casting. The trim die is used for finishing operation rather than casting. It is also known as cutting die as it cuts metal from the parts.
Due to the way die casting is done, there will be some excess metal called flash attached with the casting. Trimming dies are passed through the periphery of the casting to remove the flash. There are other ways to remove flash as well. But this is a much quicker process.
What factors determine the cost of metal die casting?
There are so many factors that control the cost of die casting that it is hard to describe them all. But we shall give you a quick overview of most of the major cost determining parameters in die casting.
Here’s a list of the important parameters,
Production Volume
This can be considered the most important parameter in die casting. Die cast tooling is a bit costly. If your order quantity is low then the cost of tooling increases the overall per parts production cost.
But the tooling is just a one-time investment. The dies can be used for producing a massive quantity of parts. When you need mass production of parts the cost of tooling is evenly distributed to the number of parts.
That drastically reduces the long-term production cost compared to other costing methods.
Type of Material
Die casting is mainly done with non-ferrous metals. You can choose among different metal alloys that have modified material properties. You have to consider the most cost-effective metal alloy that meets your requirements.
The interesting fact about alloys is that you can choose a cost-effective metal and still have some of the desired mechanical properties you need.
Precision Requirements
The level of accuracy you want to achieve in your products can increase the initial tooling cost. Die casting tooling is done with CNC Machines. If you need parts with very high tolerance then the tooling requires more time and better machines.
These increase the tooling cost a bit. But that will ultimately become negligible in long term production. That’s why die casting is the most preferable cost-effective solution for mass production of high precision parts.
Surface Finishing
There are varieties of surface finishing available for die castings. If you want any specific type of surface finishing that will contribute to the overall production cost of your parts.
Die cast parts already have a good surface finish. So, if you are ok with the default surface finish that will actually reduce your production cost.
Strength
Strength is of utmost importance if the die-cast parts will be subjected to heavy loading. Automobile parts are a good example of that. Die cast parts with such application needs to have the proper mechanical strength.
So, you have to choose the metal alloy that can provide enough strength to meet your requirements. That will require metal alloys which will obviously cost more. But for regular parts, you can choose a cost-effective metal alloy with reasonable strength.
What is Aluminum Die Casting and how is it done?
Simply stated, Aluminum Die Casting is a metal casting process where Aluminum is used for die casting. The Aluminum used may be mixed with other materials to create Aluminum alloys, which have improved properties than regular Aluminum.
The die casting process for different metals is different. Aluminum has a very high melting temperature. That’s why Aluminum is required to be die-cast using a cold-chamber die casting machine.
Only the process of melting and storing Aluminum is different. The rest of the die casting process is the same as that of other metals. Aluminum is molten in a separate container in this process to avoid damaging the die casting machine due to high temperatures.
The molten Aluminum is poured in the cylinder and push it inside the die cavity under high pressure. Once the Aluminum melt solidifies inside the die cavity, the dies are taken apart to retrieve the casting.
The excess Aluminum attached to the casting is then trimmed to finish the process. Manufacturers can choose to leave it as it is or apply a specific surface finish to the die-cast parts.
What are the advantages of Aluminum Die Casting?
Aluminum is one of the most popular metal for die casting. There are different Aluminum alloys available. Each has special properties such as increased strength, thermal conductivity, etc.
Let’s have a look at some of the advantages Aluminum die casting can offer.
Cost-Effective
Aluminum is one of the cheapest yet quality metal available due to its abundance in nature. That’s why Aluminum is considered to be the most cost-effective solution by manufacturers around the world.
Another perk of Aluminum is that it is very easy to handle. That’s why Aluminum die casting can reduce production costs.
Good Mechanical Strength
Aluminum die casting has very good strength. Some variations of Aluminum alloys can achieve strength almost equal to that of cast iron.
Aluminum can be heat treated as well to further improve their strength. So, You can ultimately hope to achieve excellent strength by spending less.
Lightweight
Aluminum parts are very lightweight metal yet strong and have great strength to weight ratio. This is the sole reason for many industries to choose Aluminum over other metals.
Aluminum parts have brought about revolution especially in the automotive and aerospace industry. This is allowing manufacturers to produce much lighter vehicles.
Excellent Surface Finishing
Aluminum die casting has a nice surface finish and feel to it. That’s why product manufacturers can choose to provide further surface treatment to save costs.
The amazing part is that Aluminum die casting can also be coated and treated to provide various other sorts of excellent surface finishes as well.
High Thermal and Electrical Conductivity
Aluminum parts have excellent Thermal and Electrical Conductivity. They can withstand extreme temperatures that are not possible by any other materials used for die casting.
This allows Aluminum die casting to be used in very rough environments. Aluminum parts are largely adopted in modern electronics due to their thermal and electrical properties.
Sunrise Metal always chooses the best to ensure the highest quality for our work. Now that you have a good idea of the benefits Aluminum Die Casting can offer, you would understand why we prefer it over others.
How is Aluminum Die Casting better than Zinc Die Casting?
Every metal has its unique physical and mechanical properties. Zinc may be preferred when there is a need for a specific feature that is only present in Zinc. Other than that Zinc is not used as frequently as Aluminum.
Zinc also has good strength and thermal conductivity like Aluminum. It has good fluidity and supports a good number of finishes. Recently the cost of raw material for Zinc has been almost equal to Aluminum as well.
So, why is Aluminum so popular? We have sorted out some points for explaining why Aluminum is chosen over Zinc.
- A very important difference between them is their weight. Zinc weights much more than Aluminum. That alone makes Zinc a less favorable option when the weight of your parts is a major concern.
- Zinc has a low melting point and it is not suitable for use in an environment with heavy temperature. Aluminum on the other hand can withstand high operating temperatures.
- Zinc die casting can maintain very tight tolerances and sometimes preferred for miniature die casting. But for medium to large die-cast parts, aluminum will provide very good results.
Sunrise Metal knows your needs. We have some Zinc die casting machines in our shop as well, in case you need small die-cast parts. Because that is usually the only time you may feel the need for Zinc Die Casting.
How is Aluminum Die Casting better than Magnesium Die Casting?
The most important fact about Magnesium die casting is that it can produce parts even lighter than Aluminum. Some parts are produced using magnesium die casting for that reason.
But lighter parts may not be able to compensate for the other properties that are lacking. Here’s a list for you comparing between them.
- Magnesium alloys are less available material in the market. So, Magnesium is simply more expensive. Aluminum would provide a more cost-effective solution unless you have any need for the physical and mechanical properties unique to Magnesium.
- Magnesium die casting has inferior mechanical strength than Aluminum. It is unable to withstand heavy stress and tends to bend. So it is not suitable for the production of die-cast parts that will be subjected to heavy stress.
- Magnesium is much softer than Aluminum as well. That makes them less stable and they are required to be machined more carefully.
- Magnesium die-cast parts usually require additional surface treatment for some applications that increase the production cost. There are fewer surface treatment options available for Magnesium die casting too.
- Magnesium can’t be heat treated to improve its properties like Aluminum.
Because of the above-stated facts, Aluminum remains a better and cost-effective solution for die casting. Magnesium is used less often unless there is a specific need for its special properties.
What geometric features should I consider designing a tooling model?
Die cast tooling is done by CNC Machining. And how you prepare the die casting tooling design can greatly affect the feasibility of the die casting process. Considering some parameters in the tool design will simplify the die casting process and reduce your manufacturing cost.
The important geometric to consider in die casting tooling are discussed below.
Provide Draft Angle
A draft angle is the tapering provided along the walls of the die casting. It allows easier removal of the die-cast part. Not having a proper draft angle will lead to complications after the casting process and increase the production cost.
Dies without proper drafting angle can also cause defects in the die casting by producing vacuum or excess friction.
Avoid fine details
Die casting tooling cost is proportional to the time required for machining. The complexity of your parts can significantly increase the tooling time.
Try to avoid any deep pockets and unnecessary detailing that can be omitted. You will be able to reduce the tooling cost significantly.
Round Sharp Edges
Use fillets or round up any sharp edges. That can significantly reduce the machining time. Use fillets of the same radius at all corners. Avoid any tight tolerances and thin walls. They take time and care to machine. That will make the cost go up.
Proper Wall Thickness
Always try to maintain a uniform wall thickness. Try not to provide wall that are too thick. That will increase the cooling time and increase the production cycle time. Proper wall thickness reduce the chances of defects in your parts as well.
Minimize Undercuts
Try to minimize the number of external undercuts you provide in your design. It may be possible to proceed with casting by aligning the undercuts with the die parting line.
But too many undercuts can make the die casting process complicated. So, it try to reduce the number of undercuts even if needs some redesigning.
These are the most basic guidelines you should follow. Of course, there are tons of other tips and tricks to successful designing. You will learn more as you keep working with us.
What surface finishes are available for die-cast parts?
After you are done with the casting and machining of your parts, we can also help you choose a good finishing. We can provide a wide range of aesthetic, functional, and protective coatings.
Our in house and nearby partner suppliers can provide the following types of surface finishing for your die-cast parts.
- Bead Blasting
- Tumbling
- Cleaning
- Chromating
- Powder coating
- Wet painting
- E-coating
- Anodizing etc.
Sunrise Metal comply with the RoHS and REACH standards for surface treatment of your die-cast parts. We can give you assurance for high-quality surface finishes with our advanced QA test equipment.
Is there any advantage of Aluminum die-cast parts over Steel?
We all know that Steel has superior strength over Aluminum. But that doesn’t necessarily make Aluminum a less favorable option. Aluminum is favored by die casting manufacturers for its multitudes of benefits.
We have highlighted the aspects that make Aluminum a better choice.
- Normally Aluminum has less strength compared to Cast Iron. But some Aluminum alloys can achieve strength almost equal to cast Iron when used for die casting.
- Aluminum is a non-ferrous metal. So, it is not susceptible to rusting such as iron. That greatly increases the scope of application of the die-cast part.
- Aluminum requires less surface treatment as well since they don’t rust like Iron. That can help reduce the cost of production.
- Iron is very heavy compared to Aluminum. This makes Iron a less favorable option when the target is to produce lightweight parts.
- Iron is a ferrous metal and it can’t be die-cast. That really puts Iron at a disadvantage. The process for casting iron is mostly much costlier than die casting.
- The cheaper options available for casting Iron are not good enough as they lack precision. That’s why today’s Industry leaders who want high precision parts at lower cost prefer Aluminum over Iron.
You should have a good idea about why manufacturers are preferring Aluminum parts over Iron nowadays. Aluminum has brought about revolution in the manufacturing industry and enabled manufacturers to sell products at a cheaper rate.
Can you share your experience in die casting?
Sunrise Metal is a well-established die casting company in Shanghai, China. We have been in the manufacturing industry for over10 years. Our superior engineering capability and advanced die casting facility will make sure that you get the best quality parts.
We have already obtained the ISO 9001 & IATF 16949 certification for our company. We have four dedicated facilities for providing you with a One-Stop solution. We have 182 skilled professionals who are capable of guiding you from the design stage to prototyping your product.
We have produced die-cast parts for many industries till now. Some of the industries include,
- Medical Device
- Marine Electronics
- Automotive Component
- Telecommunication & Networking
- Laboratory Instrument
- Aerospace
- Smart Metering
Here are some samples of die casting parts manufactured by us in China.
What facility do you have for die casting?
Sunrise Metal has rich Die Casting facilities and a wide range of equipment in our die casting shop. We have die casting machines capable of carrying out all sort die casting operations. So, you can count on us for high quality die-cast parts.
Currently we have a total of nine Die Casting machines of varying tonnage . So, we can carry out all small to large scale Die Casting operations.
We also have two Zinc die casting machines to carry out small scale miniature die casting operations as well. So, you don’t have go anywhere else if you need to produce some smaller parts during the project.
You can check out the complete list of our die casting equipment.
What equipment do you have for Die Cast tooling?
Sunrise Metals have all sorts of equipment that you will need for Die Casting tooling. We have high precision CNC machines that can carry out complex tooling operations very fast and accurately.
Along with a wide range of CNC Machines, we have several EDM, WEDM, Grinder, Sawing machines as well. That greatly contributes to our work efficiency and allows us to do all sorts of die-cast tooling operations.
Our wide range of Die casting tooling equipment should be enough to give you a hint of our die casting capabilities. So, you can count on us for high-quality parts with extreme precision and on-time delivery.
You can check out the complete list of our die casting tooling equipment from this link
How can OEM/ODMs benefit from Die Casting?
Die Casting has been really popular with the Original Equipment Manufacturer (OEM) and Original Design Manufacturer (ODM) recently. It has opened new windows of opportunity for them.
In the past, most OEM/ODMs didn’t have access or couldn’t afford a casting method for producing high precision parts. So, OEM/ODMs often resorted to low-cost casting methods that weren’t unable to yield them quality parts.
After the advancement of the die casting technology, many new OEM/ODMs have emerged. Die casting has allowed them to produce high precision and strong parts for their products in a more cost-effective manner.
So, OEM/ODMs are preferring to die casting over other casting methods. Die casting has been exceptionally popular with them recently. It has been proven to be one of the most cost-effective casting processes yet.
What is your die-cast tooling capabilities?
We have an advanced die casting facility available to provide our customers with high-quality parts. We provide multitudes of die casting operations. Some of our In-house die casting tooling capabilities are listed below.
- Die Manufacturing
- Die casting inserts
- Die repairs
- Tooling modifications
- Die casting tooling
- Trim die manufacturing
We aim to provide you a one-stop solution. So, you don’t have to worry about wandering here and there for various types of operations that are associated with die casting tooling.
How much precision can you reach for the die-cast tooling?
Sunrise Metal carries out Die Casting tooling operations using CNC Machines. We have a wide range of CNC Machines including high precision and high-speed CNC Machines. We have the latest 7-Axis and 5-Axis CNC Machines as well.
Our advanced machining facility can achieve a precision of about ± 0.005 inches for die casting tooling. We can achieve more precision, but that is often not preferred by the manufacturers as it will significantly increase the tooling cost.
Die Casting is known for its ability to produce parts with high repeatability. It will yield parts with a high level of accuracy with constant quality. That’s why manufacturers prefer to die casting for the production of high precision parts.
Sunrise Metal also has advanced QA test equipment to check the accuracy of your parts. So, you can rest assured about the precision of our die casting services.
How can you assure the quality of Die-Cast parts?
Sunrise Metal is always concerned about its product quality. We have experienced professionals and advanced quality control equipment to thoroughly test die-cast parts for any possible errors.
ISO 9001 & IATF 16949 certified
We are an ISO 9001 & IATF 16949 certified company. A company is declared to be ISO 9001 certified when they achieve the ability to provide products that meet customer requirements and gain satisfaction. They should also have strong management, corporate culture.
IATF 16949 certification is given if the company can show continual improvement in its services and customer support. They have to strictly follow some guidelines to prevent any product defect and reduce wastage.
Advanced Measuring Equipment
We are continuously investing in advanced QA Test equipment. It is because we want to provide our customers with high-quality parts. We always make sure of the accuracy and quality of your parts.
Dedicated Quality Control Team
We have a well trained and experienced team of experts who are dedicated to monitoring the quality of production from the incoming material to finished parts.
With our strict quality control measures, you can rest assured to expect high-quality parts and on-time delivery. We never compromise the quality of our work and try to give you our best.
What QA Test equipment do you have for Die Casting?
As a professional die casting factory in China , Sunrise Metal has advanced QA test equipment and quality control experts capable of operating the equipment efficiently. We have the equipment to assure the quality of tooling, casting, and finishing of your parts.
Here’s a list of our QA test equipment.
- X-Ray Detector
- Cleanliness Tester
- ZEISS CMM
- Spectrum Meter
- Digital Caliper
They can detect any type of integrity or finishing defect that may be present in your parts. So, you can rest assured about the quality of the finished parts.
How can you ensure the confidentiality of my die-cast part design?
Sunrise Metal will never disclose your personal information or your design to a third party. We respect our customer’s confidentiality and make sure they do not face any issues.
We shall never take or post pictures of your products without your consent. We have been in this business for almost 10 years now. None of our customers ever had to deal with any issues regarding confidentiality.
Sunrise will even sign a confidentiality agreement with you if needed. So, you can rest easy about the confidentiality of your designs.
How do I Get a Quote for Die Casting?
Getting a quote is very simple. You can Get a Quote by emailing us the details of your project and the parts you want to manufacture. Our customer support team will respond to your quote request as soon as possible.
You can follow these simple steps to request for a quote.
- Attach the 3d model of your parts if you have one ready.
- Give us a description of the type of parts and their field of application.
- Mention your order quantity.
- Tell us the precision requirements for your parts.
- Let us know if you have any criteria to meet a deadline.
Do let us know If you don’t have a model ready for tooling. We have talented engineers who can help you design the tooling model.
Can you design the die-cast tooling for me?
Yes, we have talented designers who can design the tooling model for you. You can count on us if you don’t have a model for tooling ready yet.
If you already have a model ready, then you ask us for cost-saving suggestions. Because how you design your model plays a big part in the time and resources required for tooling.
Die Casting tooling is the only costly part of die casting. So, designing it in a way that’s easier to manufacture will save a great deal of money.
Our expert engineers can make constructive design proposals to help you optimize your model. That will make it easier to manufacture and reduce the overall cost.
Do you provide DFM and PPAP for tooling?
Yes, we will provide the Design for Manufacturing (DFM) and PPAP for you.
You only need to focus on getting the model ready. We will optimize and simplify your parts design to make it easier for the machine to process. Then it can be manufactured much faster and cost-effectively.
We can also get you through the Production Part Approval Process (PPAP). So, you can rest assured about getting high-quality parts.
Sunrise Metal focuses on High mix, Low Volume production of die-cast parts. We will accept any small to medium die casting requests from our customers.
We typically take orders for up to 5000 parts. We have sufficient die casting machines to finish casting your parts in time.
If you need to die-cast a small number of high mix parts; you can count on us. Because big suppliers aren’t interested in low volume orders and small suppliers can’t maintain quality for your parts.
Sunrise Metal accepts die casting orders of quantity as low as 100 parts. You can always put your trust in us for manufacturing high-quality parts at a reasonable cost.
Why should I choose Sunrise for Die Casting?
Sunrise metal has advanced die-cast tooling and die casting production facilities in China. Customer satisfaction is our top priority and is dedicated to providing our customers with the best quality parts.
There are a ton of other die casters out there. So, why choose us? Take a look at these facts to find out what’s special about us.
10+ years of experience
Sunrise has more than 10 years of experience in this field. Our previous experiences help us improve and provide better service to our customers. We are always improving and using our experience to provide you the best possible solution.
Half of the project lead time
We have advanced Die Casting facilities that can reduce the production tooling time by up to fifty percent. We ensure high-quality parts while keeping the production time minimum. So, you can rest assured to get on-time delivery.
4 Dedicated Facilities
We have 4 dedicated facilities to provide you a one-stop solution. Besides Die Casting facilities, we have in house Rapid Prototyping, Die Casting Tooling, CNC Machining, and various Surface Finishing service available.
So, you don’t have to waste your time dealing with multiple suppliers for your overall product development.
Advanced Equipment
We have a wide range of Die casting Machines, and CNC machines available here at Sunrise Metal. So, you can rest assured about our Die Casting and tooling capabilities. We can get even the most critical task completed.
Exceptional Quality Control
We have advanced QA Test equipment to ensure the highest quality possible for your parts. We have a dedicated quality control team who is always working hard to keep our customers satisfied with quality parts.
Superior Engineering Capability
We have 182 skilled professionals dedicated to providing you with high-quality products. They can help you design, manufacture, and control the quality of your parts. We can also provide you with cost-effective suggestions for Die Casting.
Here you will get more information about Sunrise Metal.