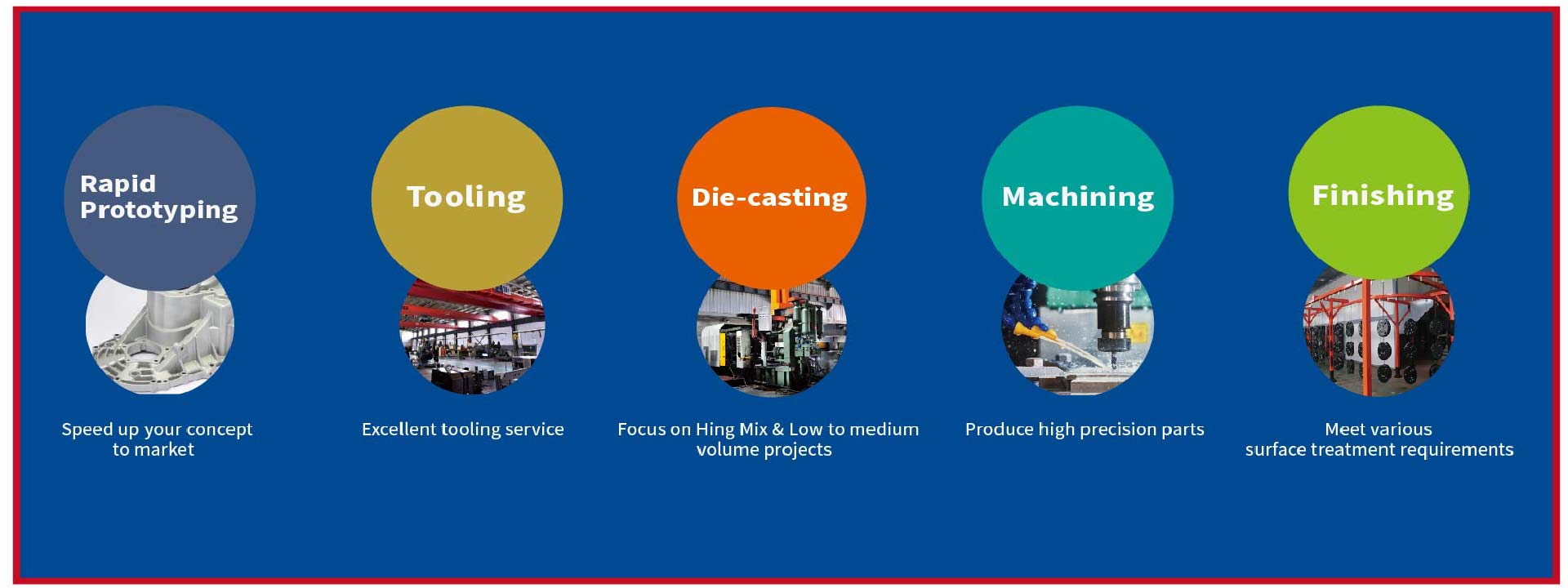
LOW VOLUME DIE CASTING ONE-STOP MANUFACTURER IN CHINA
- ISO9001:2015 & IATF 16949:2016 certified company
- One-Stop High Mix, Low Volume Die Casting Service Provider
- 10+ years experience, 4 facilities & 182 professionals
- Our Fast production assures you always on-time delivery
We customize all orders to suit your budget and business plan so that you can run your production lines smoothly!
DIE CASTING CAPABILITY
Sunrise Metal offers a wide range of services other than just die casting. The goal of our company is to provide you a one-stop solution for your project. Starting from rapid prototyping to quality surface finishing, Sunrise Metal helps you get the final product with ease and here in one place.
Rapid Prototyping
Sunrise Metal is committed to making real-life products out of your dreams. When it comes to rapid prototyping, we can deliver you the desired products in ½ the time compared to other manufacturers with the highest quality assurance.
Our high mix and low to medium volume prototyping workshop allow you to have the best output within a very short amount of time. Sunrise Metal is one of the leading companies in this sector when it comes to R&D. Along with advanced technologies, professional and experienced engineers, we ensure that our clients are getting the best service for their projects.
Die Casting Tooling
Our state-of-art in-house tooling shop allows us to provide complete solutions from tooling design, manufacturing, modification, and maintenance to tooling end management.
Sunrise Metal has years of experience in die casting tooling, which reflects on your final product, and the quality of the mold. Our rapid tooling service only takes 2-4 weeks or less, depending on your volume and requirements.
The advanced equipment and machines make us capable of providing world-class service in making any molds or tools.
Low Volume Die Casting Production
With 280T to 1600T machines and two specialized die casting facilities, we have the highest capabilities to deliver the best quality parts for our customers. The broad scope of materials, machines, and years of experience help us make the exact product that meets your demand well.
Sunrise Metal has been serving customers worldwide with premium quality die casting parts for more than 10 years. Being one of the leading die casting manufacturers globally, we take 100% responsibility for our products’ quality.
CNC Machining
To meet our customers’ demand worldwide, Sunrise Metal equipped 23 sets of CNC Machining Center and 4 CNC Lathe in our die casting shop. This enables us to provide not only the machining for die casting parts but also provide machining from solid, extrusion, gravity casting, forging, etc.
The high-tech engineering and expert workforce allow us to provide a precise and highly accurate CNC machining service according to your requirements.
Surface Finishing
To give our customers a one-stop solution, we’re providing a world-class surface finishing service to go with the quality of our manufactured parts.
Sunrise Metal aims to meet all our customers’ demands and help you get everything in one place. To do so, we’re now capable of serving you with various high-quality surface finishing options that go with your final products. All our surface treatments are ROHS & REACH compliant.
We’re providing:
• Shot Blasting • Powder Coating • Liquid Painting • Electroless Nickel
• Anodization • Silk Screening • Pad Screening • Chromate-Surtec 650
RICH MANUFACTURING EXPERIENCE ON 2500+ ALUMINUM DIE CASTING PARTS
HOW SUNRISE METAL MAKE YOUR LOW VOLUME DIE CASTING PROJECTS RUN SMOOTH
We hire experienced quality engineers and deploy advanced quality equipment. We take strict quality control for every production process. All we do is to assure product quality.
With an average of 10 years’ experienced engineering team, we provide you DFM, engineering support during the whole project life.
We provide you one-stop service integrating Rapid Prototyping, Die Casting Tooling, Aluminum Die Casting, CNC Machining & Surface Finishings.
ADVANCED ALUMINUM DIE CASTING PRODUCTION EQUIPMENT AT SUNRISE METAL
YOU CAN EXPECT STRICT QUALITY CONTROL ON LOW VOLUME DIE CASTING PARTS
GLOBAL CUSTOMERS VISIT
As an expert die casting company, Sunrise Metal provides aluminum die casting service worldwide. Many global clients visit Sunrise Metal to check our capability and capacity. Through on-site factory tour, they trust us and award us with more business. To better know our customers’ business needs and products, we also regularly visit our global customers.
Warmly welcome you to visit us.
Global-based Customers
- ISO9001 & IATF16949 Certifications
- Tooling Equipment
- Die Casting Equipment
- CNC Machining Equipment
Die Casting Tooling WorkShop (Nantong) | ||||
Machining Type | Brand | Model | Stroke | Unit |
Grinder | TATUNG-OKUMA | KGS-615AHD | From 380mm to 1600mm | 4 |
Drilling | ShenYang Machine | Z3050*16/1 | 1600mm | 1 |
Sawer | Juli | MJ034W | NA | 1 |
Lather | Shanghai 2nd Machine | C6250A | 1000mm | 1 |
EDM | EDM Korea YIHAWJET Taiwan | NA | From 438mm to 1100mm | 8 |
CNC | Local Brand | SONYU-SL850 | From 850mm to 3015mm | 5 |
Wire Cutting | Local Brand | DK7763 | 800*630mm/1000*800mm | 2 |
Milling Machine | Local Brand | QJM-S2 | NA | 4 |
High-speed Cutting Machine | Local Brand | 906148 | 750mm | 1 |
Deep Hole Drilling | Local Brand | DHD-1513 | 1513mm | 1 |
Die Spotting Machine | Nice Dongguan | NC150-1511 | 1400mm | 1 |
EDM/wire cutting Combined Machine | Local Brand | DK7755 | 550*630mm | 1 |
EDM for very small hole | Local Brand | DD703 | 300*400mm | 1 |
3D Laser Scanner | Sikan Hangzhou | HSCAN771 | NA | 1 |
Kunshan Die Casting WorkShop | |||
Die Casting Machine Type | Brand | Ton | Unit |
Aluminum Die Casting Machines | LK | 280T | 1 |
LK | 400T | 1 | |
LK | 500T | 1 | |
LK | 800T | 1 | |
Nantong Die Casting WorkShop | |||
Die Casting Machine Type | Brand | Ton | Unit |
Aluminum Die Casting Machines | LK | 280T | 1 |
LK | 300T | 1 | |
Yizumi | 400T | 1 | |
Buhler | 500T | 1 | |
LK | 630T | 1 | |
Toshiba | 800T | 1 | |
LK | 1600T | 1 |
CNC Machining Production Equipment | ||
No. | Equipment | Q’ ty |
1 | CNC Lathe | 4 |
2 | CNC Machining Center | 17 |
3 | Fanuc CNC Machining Center | 2 |
4 | Hass CNC Machining Center | 2 |
6 | Grinding machine | 4 |
7 | Saw Machine | 1 |
8 | Drilling Machine | 2 |
GET A FREE CONSULTATION
If you are looking for a Chinese aluminum die casting manufacturer, contact Sunrise Metal. When you have any hesitation or any design doubt on your aluminum die casting projects, Sunrise Metal Engineering Team can be your free consulter. Sunrise Metal gives suggestions on your custom aluminum die casting parts at 3 aspects:
1. Your design evaluation.
2. Feasibility analysis for mass production.
3. Project time and part’s cost-saving.
Contact us now, to see how we can help you with your Aluminum Die-casting projects.
LOW VOLUME DIE CASTING: THE ULTIMATE FAQ GUIDE
Low volume die casting is an increasingly popular option for many product categories. In case, you require a few parts/prototypes, you are in right spot, we work with you every step of the way, from discussion to production.
- What is Low Volume Die Casting?
- What are the Advantages of Low Volume Die Casting?
- What materials does Sunrise Metal use?
- What are the Applications of Low Volume Die Casting?
- What is Low Volume Die Casting Tooling?
- What is the difference between Low Volume Die Casting vs. Investment Casting?
- How to know that Low Volume Die Casting is best for your project?
- How to reduce Die Casting costs with better designs?
- What is Precision Low Volume Die Casting?
- How Sunrise Metal control the quality of Low Volume Die Casting production?
- How our Low Volume Die Casting Services save you cost?
- How to choose the best solution for different volumes?
- How does the complex geometry of parts affect the Die Casting?
- Does Low Volume Die Casting have certain limitations?
- What is the purpose of Low Volume Die Casting?
- How to utilize the advanced process of Low Volume Die Casting?
- How Sunrise Metal achieve high-precision in Low Volume Die Casting?
- Are the Complex Low Volume Die Castings prone to porosity?
- What is the MOQ of Sunrise Metal for Low Volume Die Casting production?
- How does Sunrise Metal ensure the on-time delivery of Low Volume Die Casting products?
- What is Sunrise Metal’s 1-Stop Low Volume Die Casting Manufacturing Service?
- Why prefer Sunrise Metal for Low Volume Projects?
What is Low Volume Die Casting?
Low Volume Die-Casting is a specialized service that offers complete production-quality parts in a limited manner, depending on the selected manufacturing process.
It’s increasing rapidly and a popular option for a vast majority of product and part categories. It also enables us to more limited investment in tooling and materials while offering rapid market access and quick response to shorter part life cycles.
Furthermore, low volume die casting is a bridge between early prototyping and high-volume production. These low volumes can be from 1 to 3,000 pieces. It’s a fast part manufacturing method for low quantity parts before the final and required die casting production.
At Sunrise Metal, we can produce hundreds of thousands of parts rapidly through our low volume die casting services. Most of the time, the majority of customers think that manufacturing costs per part go down as production volumes go up.
That is a fact but not in the case of low volume die casting. At Sunrise Metal, we offer an excellent way for you to avoid a large investment while still producing high-quality die casting parts.
Our skilled engineers will be there to help you along every step of low volume die casting; from initial product design review to quality inspection of your produced and finalized part.
What are the Advantages of Low Volume Die Casting?
- It creates a communication and relationship bridge between initial prototypes and full-scale final production
- It reduces overall costs with no minimum order quantity
- The overall process is a fast one and provides rapid access to emerging markets
- Allows faster design changes and facilitate rapid response to shorter part life cycles
- Our customers can get the exceptional applicability from the test product through low volume die casting
- The required parts can occupy the market as quickly and efficiently as possible
- It facilitates us by not requiring a considerable money investment to know the rationality of the structure and the ease of assembly from a durable but expensive tool
- You can find issues and severe functional problems during the production phase without impacting the mass production plan
- Complex parts also can be produced rapidly and handled precisely
- Low volume die casting can save much time, and you can experience functional parts on a physical level very early, even before the final production.
What materials does Sunrise Metal use?
In Aluminum, Sunrise Metal uses the popular four alloys, including A380, ADC12, AlSi12, AlSi9Cu3.
Aluminum has a density of about 2.71 g/cm³ and is the most common and used die casting alloy worldwide.
A380: We choose A380 aluminum alloy in low volume die casting because it offers the perfect and natural combination of mechanical, thermal, and casting properties.
It’s the most utilized Aluminum die casting alloy and contains an exceptional amount of pressure tightness and fluidity naturally. It also offers resistance to hot cracking. A380 has excellent machinability.
ADC12: We prefer ADC12 because of its extreme lightweight and resistance against corrosion.
If you are looking for low volume die-casting ease, ADC12 is for you. It’s mechanical and physical properties are excellent.
AlSi12: It is an Aluminum Silicon mixture die casting alloy. It’s used and known for its exceptional mechanical properties.
AlSi9Cu3: It is also one of the most common low volume die-casting aluminum alloys and consist of three materials Aluminum, Silicon, and Copper.
We use AlSi9Cu3 only for some specialized industries. It has robust mechanical properties and is a perfect solution to ultra-lightweight automotive parts.
What are the Applications of Low Volume Die Casting?
We provide low volume die casting services to many international businesses related to different applications. Some of these applications are the following:
- Complex net-shaped die casting parts
- Automotive because aluminum parts contribute to lightweight requirements and are proven fuel-efficient
- Networking and Infrastructure equipment in telecommunication and computing industries
- Handheld medical and other industrial devices
- Electronic connectors and housing
- Heavy industrial and general equipment
- Medical and hospital computerized equipment
- Marine parts
- Aerospace parts
- Power tools and consumer electronics
- Industrial machinery and robotics
What is Low Volume Die Casting Tooling?
Sunrise Metal is experienced in high-yield, durable, and complex custom parts with qualified tolerances for low volume die casting tooling. We provide precise tooling services for low volume die casting. Furthermore, we produce small unit parts of different sizes up to large machines.
We deliver top-quality die-cast tooling through each relative service. With every new requirement and specification, our skilled team finds the best way to facilitate our customers with exceptional quality parts.
Conventional, long-life die casting tooling is costly and sometimes makes it hard for low volume production. These low volume production scenarios require specialized low-volume tooling.
Without productive and innovative thinking, the per-piece costs can increase to the extreme. For example, manufacturing medical and hospital equipment and parts are where low volume production is mostly required for validation purposes.
Sunrise Metal use low volume die casting tooling for cost-effective production. However, our techniques will not let the overall cost increase and most suitable for lower volumes. Problem-solving is what we are specialized in.
The following are some of the best cost-effective strategies for low volume die casting tooling:
- Single Cavities: The problem with multi-cavity die-casting molds is that they provide high volume production and expensive. If low volumes are required, a single cavity solution is preferred and is sufficient and significantly reduces mold costs. The same logic applies to complex die casting parts. Least complex and tools that require single operation help reducing the overall cost.
- Modular tool design: Use flexible inserts that are easily interchangeable and exchangeable so that they can be swapped in and out of the die set. Most importantly, it’s an incredibly useful approach for scenarios in which parts are required in a range of sizes.
- Soften tooling: Aluminum is the most preferred material for low volume die casting tooling, and it opens the door to a less hard and durable solution. It will cut time and save money as a result. Aluminum’s thermal properties are essential along the way. And aluminum’s features can cut costs by eliminating the need for cooling galleries.
What is the difference between Low Volume Die Casting vs. Investment Casting?
Die casting is one of the most advanced and oldest manufacturing techniques. However, the necessary die casting process hasn’t changed much. Today’s die casting machines and methods are more advanced and using the latest technology. You can reach your end product or part in many different ways, but the question is, which one is most beneficial and precise?
Low volume die-casting and investment casting are considered as the most similar and standard processes.
The Low Volume Die Casting Process:
Initially, the process starts with melting the alloy. Afterward, the molten alloy is poured into the die cavity made out of steel. When the metal solidifies, it’s carefully ejected from the tool. The same process is repeated for every time until the production requirement is met. This is the general mechanism of die casting, and the process sometimes depends on the material used. Because using Aluminum will give you rapid outputs and decrease the overall low volume die-casting costs.
The Investment Casting Process:
Low volume production using investment casting is typically a more time-consuming and costly process. It starts with manufacturing a prototype. This prototype is made out of wax and copies the exact part. Afterward, the prototype is dipped into liquid ceramic. Then the ceramic hardens, and the wax starts to melt. In the end, it leaves you with a ceramic mold. Afterward, the molten metal is poured into the ceramic cavity where it solidifies. After the whole process is finished, the ceramic mold is crack opened, and the required part is removed carefully.
The mold that was used to make the wax patterns is reusable. However, the ceramic mold that was crack opened is disposed of with each part manufactured. Its complex process and high material usage are way more expensive and time-consuming.
Conclusion:
Low volume production projects need to be handled with extreme care. These projects require rapid production, cost-effective solution, and quality outputs. These things only can be achieved through low volume die casting.
At Sunrise Metal, we focus on four essential things while working on low volume die casting projects:
- The overall production volume
- Tolerance capabilities
- Overall cycle time
- Final part cost
How to know that Low Volume Die Casting is best for your project?
Die casting is one of the oldest known, and its process is simple and powerful. This process can manufacture all types of shapes, including the ones with complex designs. These parts are used in the vast majority of industries, from marine and communication to aerospace and electric. Rather than comparing low volume die-casting with other similar processes, we’ll simply run through some key considerations when it comes to low-volume production.
Our observations and selection depend on the following considerations through which you can know why low volume die casting are best for your projects:
- Design Complexity: It’s important to know about the part’s design complexity. Sunrise Metal focuses on part geometry and design details because it plays a crucial part in choosing the most appropriate process. Sunrise Metal offers excellent design flexibility, and we manufacture too complex designs with utmost precision.
We can achieve results with maximum dimensional precision, complex geometries, and thin-walled through low volume die casting. Low volume die casting services offers good dimensional results.
- Material Selection: A wide range of alloys can be used in low volume die casting. However, aluminum alloys are most preferred for fast production and cost-effective solution.
- Annual Usage: One of the most significant disadvantages of every other process instead of die casting is that they only make sense for large volume production. You can use these processes, but the final decision usually makes by focusing on minimum tooling costs. You can achieve the best quality parts rapidly and cost-effectively through die casting.
- Part Size: There can be some part size limitations during low volume die casting, but the limits always apply after observing the required part completely. Every casting technique comes with its size limitations. However, die casting is the most less restrictive of them all. The thing that requires the focus is that the larger the part, the larger the tool, the larger the tooling cost.
How to reduce Die Casting costs with better designs?
Die-casting has become essential to manufacturing across various industries. Therefore, minimizing the overall costs of this widely used proves is critical to improving profitability. It is proven a simple process with low incremental and tooling costs. Many factors contribute to the complexity and cost of the die casting process.
The following are the most important nine ways of designing your parts in-order-to reduce die-casting costs:
- Minimize the number of undercuts: The definition of an undercut is that it’s a part of the design that barricades its withdrawal from die casting mold. These are classified as internal and external undercuts based on their location within the part geometry. There can be exterior or inside undercuts. Most importantly, molding undercuts require side activities that can add 20-25% to the overall cost. Side actions are required due to an increase in machining complexity. The overall process increases the cycle times by 15-20%. That’s the reason why we prefer fewer undercuts in your part design so that overall die casting cost can reduce.
- Minimize the wall thickness: To minimum acceptable level required for the application, there comes the need to keep the wall thickness of parts as close as possible. Doing so will reduce the cycle time. Reduction in injection time and cooling time automatically affect the overall production time and volume of material consumed. Decreasing the volume of the part required has a direct correlation to the production cost. Shorter cycle times and less material waste will automatically reduce a significant portion of the overall cost. That’s why thin walls are the preferred choice for low volume die casting.
- Keep wall thickness uniform: Designing parts with various wall thickness can result in uneven cooling, causing deformation. It will increase the chances of bubbles formation, hot tears, ejector marks, and dimensional inaccuracies. A high quantity of manufactured parts with defects ending up in the rejection area increases production costs due to an increase in defect rate. Not only do they cost resources and time spent on lousy design parts go to waste. But also, more inefficient cycles are required to meet the customers’ requirements.
- Use fillets and radii in the mold cast: Part’s Sharpe angled edges in the design cause stress concentration and increase the fracture rate. Which also becomes the reason behind the extreme cost. We can avoid this by including fillets and radii. Fillets are the inner corners of the part, and radii are the outer ones, which provide rounded edges in your part design. Remember, increasing the radius of the edges too much can cause shrinkage porosity. Thus, your die casting part design needs to use optimum dimensions.
- Minimize the number of sliders: In low volume die casting, we can decrease the number of side actions by performing unique methods. Like, instead of just two mold halves coming together to shape the part, another piece is required that moves in from the side. This extra mold piece also helps to form the part surfaces in a way that helps the part to quickly release from the die casting molds. However, each additional direction increases the overall part costs by 15-20%. Even if the required parts need side-action, try to align all the parts to one side to reduce low volume die-casting costs.
- Include appropriate draft angles: Holes and widows of the parts require more drafts than inside and outside wall features.
Using incorrect drafts or excluding it can result in fractured and damaged parts and extended production times.
- Include ribs (and webs): To increase stiffness and add strength to the part, including ribs. This will result in a lighter part that’s sturdier than its standard version. A thin wall with ribs is sturdier, and the resulting part can be extremely lightweight and durable.
- Design sturdy bosses: The bosses are singular features added to a die casting. A boss refers to a mounting feature that can receive a screw or thread-forming screw. We suggest using ample fillets and ribs in your die casting part design to ensure that molten Aluminum can easily flow into the boss area. Designing the bosses poorly can result in waste, so it’s essential to pay extra attention to the details.
- Decide on hot vs. cold chamber die casting: Your low volume die casting requirements can be fulfilled precisely by selecting the most appropriate die casting methods.
What is Precision Low Volume Die Casting?
Sunrise Metal is specialized in Aluminum die casting, and our team is the most skilled in the industry. Our high-level engineering sets high standards for precision low-volume die casting. To achieve maximum precision, we produce parts with high tolerance tooling.
We offer fast and cost-effective production. Our versatility enables us to die-cast competently, for low volume production, large and small parts, simple and complex designs. Our sole purpose is to enhance the functionality and improve the manufacturability of your parts through our precision low-volume die casting. Our experienced team always reviews the part designs in detail, sharing insights and exchanging ideas that enable us to achieve precise final results and improve performance.
How Sunrise Metal control the quality of Low Volume Die Casting production?
As an experienced low volume die casting manufacturer, how do Sunrise Metal control the quality of production
- Sunrise Metal’s quality policy is “Continuous Improvement, Rapid Results, and Customer Satisfaction.”
- In the term of Sunrise Metal quality standards, we are always maintained our principles
- We follow the customer’s requirements and parts specifications strictly
- Our material’s authenticity for die casting is guaranteed
- To ensure our customer’s low-volume die-casting parts with high-quality and stability, Sunrise Metal has established an impressive set of management and quality-control processes from the feed to the process.
How our Low Volume Die Casting Services save you cost?
The majority of our new customers think that low volume die-casting costs per part go down as the volume goes up. If you want to make cheap parts, you should produce them in high volume. But, it’s not necessary because if you’re going to high volume die-casting production, then you must make a more considerable investment in more expensive tools. Furthermore, it needs to be hardened and heat-treated more carefully to withstand high temperatures and complex environments.
With this in mind, low volume die-casting is an excellent way to avoid large investments while still producing high-quality and completely functional parts.
The typical scenario we discussed before doesn’t apply here. In case the tool doesn’t require to be durable, it can be more economical for you to purchase and faster to heat treat.
- DFM: Design for Manufacturing helps our clients to optimize the parts and mold design to save cost.
- Rapid Tooling: Our rapid tooling service reduces the mold cost and makes a noticeable difference.
- One-Stop Solution: Sunrise Metal is a one-stop die casting services provider and on-time delivery.
By comparison, high volume production requires massive investment and inventory of alloys and equipment.
To cover these expenses, you place a large minimum order quantity. An experienced engineer in low-volume production knows that the same amount of parts can be processed faster and cost-effectively without demanding any significant minimum order quantity.
How to choose the best solution for different volumes?
If you wonder that what solution should you choose to match the quantity and quality you required, Sunrise Metal got you covered! Our engineers will analyze your design and test it. After performing some tests, we discuss the core problems and defects your part can face. For low volume production, rapid prototypes and rapid tooling are the best solutions for customers worldwide. For medium and large volumes, die casting with production tooling is better. In these cases, tooling works alongside production to optimize the output of highly finishing die-cast parts.
After a complete professional evaluation, we state the best and most productive method suitable for your quantity at hand. Also, we make sure that our customers are informed about how the quality may differ in each type of process involved in the low volume production.
Welcome to contact Sunrise Metal if you have any requests about choosing a solution for different volumes.
How does the complex geometry of parts affect the Die Casting?
The complexity of part is always an essential factor to consider in low volume die casting. A complex part may have a different tool life compared to a part with simpler geometry. In low volume die casting, thanks to the superior part design freedom, the production is flexibly guided by design. By integration functionality into the die casting part during low-volume production, Sunrise Metal succeeded in significantly decreasing the number of individual parts and the assembly cost. As a result, the output parts are lightweight, durable, and cost-effective. We save time and money with minimum cost.
Different part geometry also affects the overall production cost along with production speed. That’s why it’s essential to pay attention to the part’s design along with material and surface finish.
Does Low Volume Die Casting have certain limitations?
- When working on low volume die casting projects, the complex parts can be handled easily but with not a maximum level of dimensional accuracy. However, the parts are fully functional but not as stable as final production. That’s the reason why further processing of die casting is required before final use to achieve maximum dimensional accuracy.
- Limitations on mechanical strength properties and porosity
- Safety hazards due to the handling of hot metals. However, at Sunrise Metal, our safety and environmental protocols are strict, and we don’t make mistakes.
- It’s also important to keep track of temperatures. The term superhot is the temperature difference above the melting point of the alloy at which it’s poured. The term also refers to the amount of heat needed to be removed from the molten metal between pouring and solidification.
What is the purpose of Low Volume Die Casting?
At Sunrise Metal – China, our low volume die casting services serves the clients the following purposes:
- “Replacement” die-casted parts that are no more in production or are otherwise unavailable for some other reason. These’re often parts for repair.
- Our low volume die-casting services provide a bridge between initial prototyping and final high-volume die-casting production. This is the point where the parts will be manufactured using production (hard) tooling. Some people call it “pre-production parts.”
- Low volume die casting parts are the parts made after the initial prototyping phase. These are the production parts but only for having the exact idea about how the part operates and what it faces in specific environments. Lowering our customer’s tooling costs, improving cash flow, are reducing the production time are some secondary purposes we provide our customers at Sunrise Metal.
How to utilize the advanced process of Low Volume Die Casting?
Low volume die-casting intends to produce a specific number of parts using the process of die casting in a brief timeframe. Sunrise Metal can provide the quality and advanced die casting solutions our customers required. However, our attention is on customer satisfaction and surpassing the majority of our client’s requirements. We also support our clients with their course to showcase. When the improvement stage is near its completion, and plans are decided, following prototype production, we are frequently approaching to give low volume die casting solutions.
Sunrise Metal can offer a scope of solutions and advantages. However, the critical advantage is that our low volume die casting and tooling expenses are essentially lower than high volume die casting.
The following are the advanced processes Sunrise Metal utilize and offer:
- 3D Printing
3D printing also helps to reduce tooling costs, facilitates us with customized production, and bring products to market rapidly. The 3D printing process allows us to incorporate time-saving manufacturing for better balance. A 3D printer can manufacture parts with virtually zero limits to the complexity of design simply by programming the printer appropriately.
- Rapid Tooling
Rapid tooling is quickly becoming a cost-effective way and a lean option for low volume production. Different processing technologies are involved in rapid tooling, depending on the part design.
- Rapid Prototyping
One of the revolutionary technologies for low volume production is rapid prototyping When it comes to manufacturing, rapid prototyping is experiencing reformation and revolution. It plays a major part in cost-effective production.
How Sunrise Metal achieve high-precision in Low Volume Die Casting?
If you in search of low-volume die-casting production but want high precision for your parts and projects! We produce parts with high-precision, and our rapid solutions help to achieve the best precision in low volume die casting.
High precision also can be achieved through tooling. Maximizing the part accuracy while machining. It’s important for machining that the design drawings are absolutely precise. Without measuring anything there can be few changes for improvement. Measuring and keeping track of everything and control the process of die casting improves the accuracy of parts to a maximum level. Furthermore, it also helps us to achieve high-precision.
Sunrise Metal can handle low volume die casting production requirements with our compact machines and experienced engineers and designers.
Through these aspects, we achieve the high-precision in low volume die casting. The greatest and most important value in finding problems and bugs early is being able to address them with your partners before it becomes difficult, expensive, and time-consuming. Our fast production and overall rapid solution also help achieve precision and speed up your move to the market.
Are the Complex Low Volume Die Castings prone to porosity?
We believe that porosity is a commonly misused term and understood concept. There can be multiple potential sources of porosity in low volume die casting. Furthermore, there’re also many reasons for porosity.
Environmental gasses mostly cause porosity. This can be controlled with metal quality, vacuum melting, and proper de-gassing procedures at the melt deck.
Another primary source of porosity is that it occurs due to turbulence and splashing when the die casting metal is poured. It causing the environmental air in the mold to become entrapped. A proper gate, runner, and design, useful pouring techniques, and filtering can be used to minimize the overall turbulence. And it’s used to reduce the entrapment of environmental air.
In the end, what some refer to as porosity is shrunk inside the die-casting due to the volumetric change that occurs in the alloy as it changes from liquid to solid. The shrink can be eliminated or reduced by choosing a good die casting design. The selection of critical gate sizes and locations can eliminate the shrinkage.
Good alloy selection, proper poring temperature control, and finalized part cooling is fundamental to decrease and eliminate shrink during the low volume die casting. If the parts are precisely and adequately designed, and the die casting processes are controlled accurately, porosity can be minimized.
Our experience helps us to deliver effective and efficient production. Our customers can achieve effective and efficient low volume die casting production through our one-stop die casting solution. Our rapid tooling services are also great and one of the best ways to achieve effective and efficient low volume production.
Our one-stop die casting services achieve effectiveness and efficiency by:
- Maximizing the cost-saving
- Output better quality
- Shorter lead times
- Minimizing the risks
Our rapid tooling services achieve effectiveness and efficiency by:
- Shorter production times
- Allows full fit and function testing
- Discovery of any design flaws early on
However, the rapid tooling life cycle varies depending on the different factors like the geometry of the part, size, and complexity of its design.
Our customized, low volume die casting services are also a way of the future and enable us to more limited investment in tooling and materials. Furthermore, this also allows an effective production solution. Our rapid access to markets and fast response to shorter product life cycles also an effective way to achieve efficient low-volume die casting production.
Sunrise Metal continually invests in the latest die-casting techniques and rapid manufacturing technology.
What is the MOQ of Sunrise Metal for Low Volume Die Casting production?
Low volume die-casting aluminum alloys are lightweight while processing high dimensional stability for complex design parts and thin walls. Due to our specialty in low volume die casting, we are very flexible in order quantities.
Sunrise Metal’s quotes always break down the overall cost by MOQ’s; there can be a price premium if the order is below 3.000 pcs. Or there can be an alternative, cost-effective solution to our customer’s project if the order is below 1,500 pcs. (Remember! These numbers are just, for example).
How does Sunrise Metal ensure the on-time delivery of Low Volume Die Casting products?
Sunrise Metal measure the OTD (On-Time Delivery) through the following and keep track of the overall progress:
- Calendar Days vs. Working Days: It’s the most common misunderstood term between customers. Do the five days include weekends? It’s acceptable either way, but customers must clear the complete detailed routine.
- Promise Date vs. Required Date: Required Date vs. Promised Date: Require date describes the deadline by the customers, and the promise date describes the date committed to meet by low volume die casting services provider. Near Sunrise Metal, the promise date is the best practice.
- Percent of line item vs. percent of the quantity ordered: A line item is a single part, and we calculate the overall parts per day we need to die-cast to meet the promised date.
Below are the ways through which we improve OTD:
- By ensuring and maintaining the accurate inventory records
- We create realistic production schedules and maintain them at any cost
- We monitor efficiency on every step and maintain it
- Build a strong relationship with our customers
What is Sunrise Metal’s 1-Stop Low Volume Die Casting Manufacturing Service?
Sunrise Metal is specialized in serving international customers looking for low volume die casting services. We are preferred because of our low cost, high-quality parts, and rapid production. Our skilled engineers can guide you from product inception to production.
We are some of the few well-known die casting services providers who offer all the services related to die casting.
Our techniques and methods are based on the latest technology, and we offer the guaranteed same outputs as required by our customers. Our 23+ years of die casting experience means Sunrise Metal is a tier-one low volume die casting services provider for large international customers. Due to our specialty in low volume production, we are incredibly flexible in our client’s order quantities. However, the minimum quantity of parts depends on the part’s complexity and size.
- DFM (Design for Manufacturing)
Using low volume die casting services, creating a fully optimized part design before tooling is important. Because it can make the entire process more efficient and result in more quality at a lower cost. Utilizing DFM for optimization purposes is good practice.
This is an excellent service and cost-effective way to produce parts without using any additive processes. Rapid prototyping is ideal for Aluminum. Rapid prototyping is mostly utilized for low volume production.
- Rapid Tooling
Rapid tooling does not require time-consuming and costly pattern making. Rapid tooling is, therefore, widely employed in many industries to produce low volume parts and prototypes. It helps reducing lead casting design time and accurate the introduction of new components.
Die casting is considered as the most rapid and economical part production technique. All parts produced using die casting have uniform quality and involve relatively low unit costs.
- CNC Machining:
CNC machining has shorter lead times and offers higher precision and repeatability. It requires a detailed manufacturing plan and unique for low volume production. However, the basic principles of CNC machining are similar to traditional manufacturing methods.
The surface treatment service includes anodizing, printing, painting, and coating. Furthermore, it’s just not limited to these four treatments. It’s a possible way to obtain sufficient resistance against environmental hazards, including high-temperature oxidation.
Why prefer Sunrise Metal for Low Volume Projects?
Our 23+ years of low volume die casting experience, and our skilled team is enough to output excellent results at all aspects of the die-casting life-cycles. These results vary from DFM (Design for Manufacturing) initialization to problem-solving during part production.
Furthermore, the following are the reasons why the majority of clients prefer Sunrise Metal over other low volume die casting manufacturers from China:
- Through Sunrise Metal, you can get the lowest overall manufacturing cost for small to medium orders
- From design requirements to manufacturing and assembly, Sunrise Metal is a professional and skilled low volume die casting services provider in China, with international clients.
- Our skilled team and English-speaking staff work directly from the client’s design to production.
- Sunrise Metal own and manage the entire life cycle of low volume die-casting manufacturing projects
- We solve problems, and each of our clients values our ability to turn complex part design specifications into finalized functional parts.
- Sunrise Metal handles all aspects of low volume die casting from design specifications and testing requirements to part manufacturing, surface finishing, and assembly
- Sunrise Metal is using its advanced technological innovation and skilled professionals from manufacturing high-quality die-castings most cost-effectively with its 23+ years of experience in die-casting
- To meet our worldwide customer’s low-volume die-casting requirements, our team proudly provides a range of die-casting services deployed with industry-leading agility.
- We believe that high-quality die-casting materials are the initial and most crucial step to high-quality parts. We offer advanced material inspection and verification to ensure that all the alloys meet your product specifications.