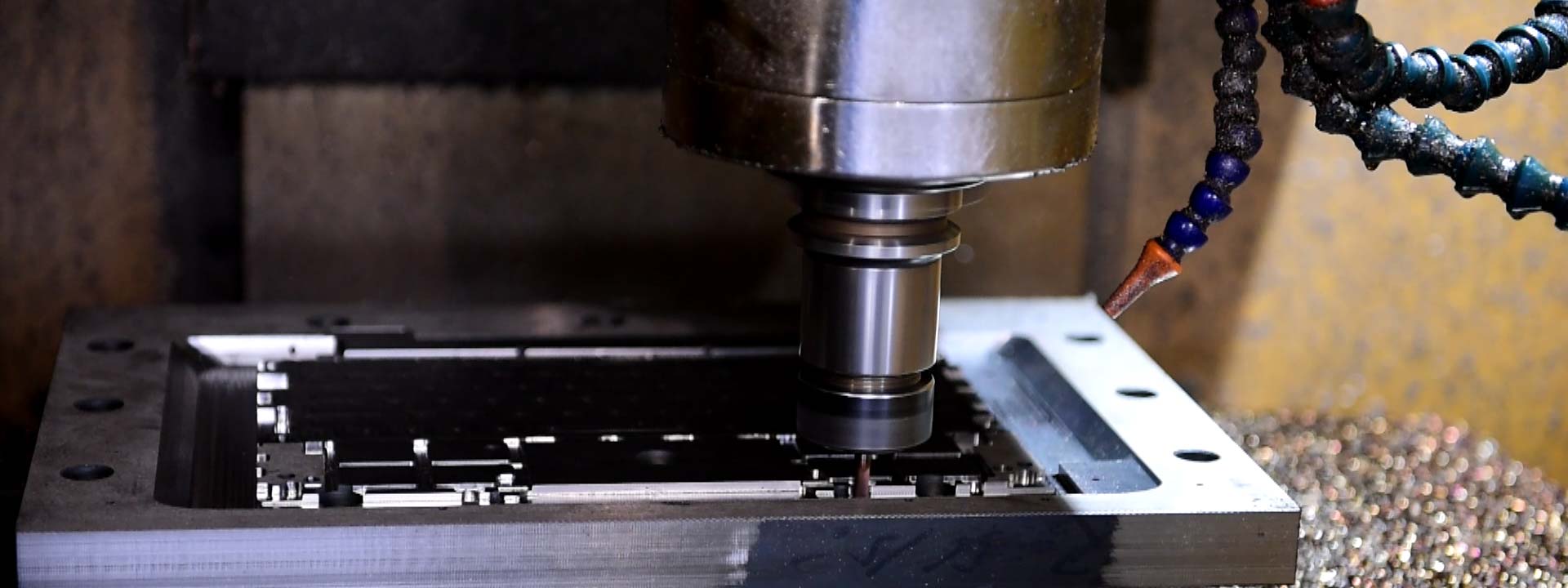
Die Casting Dies Manufacturer-Sunrise Metal-Your Fantastic Partner in China
Die casting die is the most crucial part of die cast production. It has a great impact on the end result. Sunrise Metal is the leading manufacturer of die casting dies in China. Our engineers work on every possibility to build the most efficient and reliable tools that help in die-cast processes for every industry. From dies to molds to the CNC machining and surface finishing, they are working to develop just the right tools. Sunrise Metal uses the most advanced techniques to develop premier die cast tools.
Validation Technology & Mold Stimulation
Sunrise uses the advanced AutoCad solution for mold stimulation which helps in building the right tool. Latest technologies like CAD/CAM are used by our mold designers who analyze the mold flow to create the right molds. These technologies help build the right solution for die casting needs.
Strong Technical Mold Design
Sunrise designers use the mold simulation results to build a strong mold design that goes with the die casting process. This in-house team also helps the customer with their concept visualization, functional analysis, mold flow analysis, and complete mold design.
One-stop Tooling Shop
Sunrise in-house team builds the solution for mold construction as well as any tool design. We believe in providing and using the most advanced tools. Therefore, our team of experts has come up with such solutions that help increase the efficiency of each process with premier tools.
Your Die Casting Dies Coming From Sunrise High-end Mold Machining Equipment
Competent Die Casting Dies Capability To Fulfill Your Projects
Our die cast and mold designers utilize the latest technology in engineering and mold flow analysis, including flow technology & other engineering software use by Pro Engineer/CREO & AutoCAD.
Team of experienced mold engineers can help you with your concept visualization, functional analysis, mold flow analysis, and complete mold design.
Tooling design & Mold construction & Tool validation & Repair and Maintenance.
Productive Die Casting Dies Supported By High-Tech Process Machines At Sunrise
Recent Die Casting Dies Projects
Ultrasmooth die casting tool & dies designs and manufacturing processes are at the center of Sunrise Metal’s commitment. Currently, we are engaged in various projects with long-standing clients:
- Advanced Equipment
- Premium Quality
No. | Name | Stroke | Q’ty |
1 | Mazak 7-axis turning&milling Machine | Ø658*1011MM | 1 |
2 | Mazak /Hass 5axis CNC machine | Ø850/Ø600 | 4 |
3 | 3-axis CNC machine center | 2000*1500MM | 1 |
4 | 4-axis CNC machine center | Ø250*800MM | 8 |
5 | 3-axis CNC machine center | 1000*600*600MM | 20 |
6 | CNC Lathes | Ø320*800/Ø610*1000MM | 2 |
7 | Sodick Wire cutting Machine | 400*400*200MM | 3 |
8 | EDM machine | 500*400*400MM | 2 |
9 | Surface grinder | 600*300*200MM | 1 |
No. | Name | Brand | Q’ty |
1 | CMM | Carl Zessis | 1 |
2 | CMM | SanYou | 1 |
3 | Spectrometer | China | 1 |
4 | Microscope | China | 1 |
5 | Projector | China | 2 |
6 | X-ray Detector | SANDT | 1 |
7 | Cleanliness Test Equipment | China | 1 |
8 | Leakage Test Equipment | China | 2 |
9 | Salt Spray Testing Equipment | China | 1 |
10 | Pneumatic Measuring Instrument | China | 2 |
11 | Hardness Testing Machine | China | 1 |
12 | Color Meter Machine | China | 1 |
13 | Thickness Testing Machine | China | 1 |
14 | Electronic Balance | China | 1 |
15 | Density Balance | China | 1 |
Get A Free Consultation
Complementary engineering consultant for your Die Casting projects for skillful suggestions and solutions based on your CAD and Step drawings. Sunrise Metal can offer full chain service if you have any demands on aluminum die casting.
DIE CASTING DIES – THE COMPLETE FAQ GUIDE
Sunrise Metal is a one-stop solution for Aluminum die casting. With 4 dedicated facilities and 182 professionals, Sunrise leads the in-house manufacturing of die cast dies, aluminum die casting, CNC machining & Surface finishing. Sunrise has an experience of more than 10 years in a wide range of industries including automotive and aviation. For die casting mold, Sunrise owns a complete die casting tooling in-house.
- What is die-cast die?
- Why are the premier tool and die-cast facilities important for die-cast production?
- How are some of the best die casting tool designs prepared?
- What are the manufacturing procedures of the die casting dies?
- Which industries make use of high-pressure die-cast tooling?
- Is there a high die-cast tooling cost involved in the process?
- Which mold materials can be used when making die cast mold?
- What are the different types of molds prepared for the aluminum die casting process?
- Which mold flow technology and engineering software are used at Sunrise?
- Does die cast mold require regular maintenance over time?
- What is multiple-cavity die cast tooling and what are its applications?
- Which methods can enhance the die casting mold life?
- What is mold flow simulation for die casting tooling?
- What are the advantages of die casting dies?
- How does the die casting dies work in high-pressure die casting machine?
What is die-cast die?
Die casting is a process of producing aluminum, zinc, and other metal parts in high volumes. Molten metal is forced into die cavities to obtain certain shapes. The process requires dies and many other tools for production. Die cast dies are the tools required in the process.
Die has to align with all the requirements of the customer. The shape, size, and even color of the product will be affected by the die. The unique and special features of each product are the result of the right die. To make the right die for a part, these factors need to be kept in mind
- Size of the required part
- Volume required
- Core Slide Requirement
- Insert requirement
- Family set production
Why are the premier tool and die-cast facilities important for die-cast production?
To achieve maximum quality results, die casting mold plays an important role in the production. The grade of the molds used in the die casting should be minimum premium. These molds are utilized in die casting facilities in controlled environments due to the following reasons.
Critical Requirements
Every die cast product has different requirements that may include some very intricate designs and detailed structures. To carry these out, premium quality mold is required or it can affect the end results. Die cast mold will vary according to every alloy and material that is to be used.
Mechanical and chemical properties of alloys
The mechanical and chemical properties of every alloy are different from the other. This means that different quality tooling will be required for each alloy. Sometimes, premier tools also allow production from many different alloys.
The environments required for each alloy are also different. The die casting facilities are able to cope with any requirements and hence are very important.
High temperatures and pressures
The temperatures and pressures required for the production of die casted products are very high. This requires controlled environments that are only attained in the facilities set especially for die casting. This results in premier die cast products.
How are some of the best die casting tool designs prepared?
Die casting tools are being prepared in a large volume every day. These tools are made and sometimes customized to meet the requirements of the product to be designed. When the tools are designed there are certain things that are considered. These include:
Size of the product
When you are making a tool for die casting, you need to consider what size product is to be manufactured using this tool. For example, the mold of the product is to be made the exact size you want. Any changes will directly impact the end result.
Material
Tool designing needs to consider the material of the tool. This depends on the material that is to be cast and also the temperatures and pressures it is going to endure. This is important to maintain the quality of the casted product.
Geometry
The geometry of the die casted product is very important in the making of tools. Complex geometries, net shapes, and many other features depend upon the right tools. The design of the tools is prepared to provide these features.
What are the manufacturing procedures of the die casting Dies?
Die cast tools were made through drawings in the past. But this has changed now. Certain technologies have come into existence to provide high-quality tools for die casting.
CAD/CAM design
Computer-Aided Designs give an optimized calculation of the tools to be manufactured. They are used by toolmakers to characterize the cast parts with a uniform structure. This designing phase considers the casting process, melt flow, cooling of metal, geometry, and dimensions of the part to be cast. The design should ensure the high surface quality and fine grain structure of the part that will be cast using the tool. The tutorial below teaches how to design molds using CAD-CAM software.
CNC machining
CNC machining is used to form the tools from the CAD design. The computer-controlled process provides precision in the process. This makes the tool foolproof and reliable.
Cut Erosion Machines
This process is used to cut the dimensionally complex tools. The process provides precise results and great operating comfort. The tools are machined to be quick safe and reliable.
Which industries make use of high-pressure die-cast tooling?
High-pressure die cast die has become important for certain industries. Whether it is aerospace, aviation, or the automotive industry, die cast die is a solution for each one of these.
Die cast die has its advantages in various industries. Some of them are:
- Medical Industry: Certain medical parts have complex nature and high pressure die casting dies helps build precise high-quality parts
- Automotive industry: Automotive industry requires new solutions every day that helps in lowering fuel consumption. High-pressure die-cast die helps precisely.
- Marine industry: From heavy parts to small custom parts, high-pressure die-casting tooling allows building each solution for the marine industry.
- Telecom Industry: To help with all the networking solutions, high-pressure die-casting tooling always comes in handy.
Is there a high die-cast tooling cost involved in the process?
Die-cast tooling cost depends upon their usage. Before you go into calculating the cost of it, it is important to know the components that make up the process. Molds and dies are not considered cheap and if someone promises that, there’s a high chance of it not being true.
The cost of the die-cast tooling is for the quality it provides. Going for a cheaper alternative will be problematic down the road. The high costs of these tools denote quality and precision that make the final products stand out. It provides superior tool design, longer tool life, and exceptional results for the die cast product. In addition, little to no maintenance is required for these high-quality tools which make the tools cheaper in the long run.
Which mold materials can be used when making die casting mold?
The die cast mold are made from hard materials that are resistant to the environments they are put in. It mainly depends upon the part to be cast from them. Steel is the most common material used in the production of tools for die casting. It is used in different forms.
Alloy Steel
This is by far the most used alloy of steel for die cast mold. It provides the strength and intricate design that the product required.
Carbon Steel
Carbon steel is also considered competitive in the market due to its ability to easily deform. Carbon steel and alloy steel also provide competitive prices.
Stainless Steel
Stainless steel is more expensive than the former steel forms but is used where corrosion resistance and rust resistance is the priority. It provides durability and stability to the tools.
What are the different types of molds prepared for the aluminum die casting process?
Aluminum die casting uses certain types of molds for the preparation of aluminum die cast products. These molds support the handling of melted metal in different forms.
- Flood molds: The molten metal is flooded into the mold which is the sculpture of the product to cast.
- Box molds: These molds are created by forming a box around the sculpture to be cast. The box is engraved with the form of sculpture.
- Block molds: These molds are formed by creating a block around the sculpture. The sculpture is then taken out of the block.
- Pressure molds: These molds use pressure to fill in the material that is to be cast. It removes the air from the mold.
- Injection mold: These molds use the injection technique for the process of aluminum die casting. The material is injected in the mold and is allowed to cool down and take a solid form.
Which mold flow technology and engineering software are used at Sunrise?
Sunrise is the manufacturer of top-class competent die casting tools. To provide these solutions, we have been using the most advanced technologies. Sunrise uses the latest and most efficient AutoCad engineering software for the development of tools. CAD and CAM software is used to design and then develop the right tools at Sunrise.
This software helps in predicting the flow of molten metal and hence provides the necessary information required to build the molds as well as dies for the metal.
Does die cast mold require regular maintenance over time?
Maintenance of die cast mold is necessary to increase the life of the tools. A cheap low-quality die cast mold will require regular maintenance with very short intervals and can also give up quickly. The product obtained from these tools will also be of low quality. Die cast mold of higher quality also needs maintenance but that maintenance is on a regular base, not as frequently as low-quality mold. Premier die cast mold has a longer life and keep on producing high-quality products for a long time.
What is multiple-cavity die cast tooling and what are its applications?
Multiple-cavity die cast tooling is an innovative process that enables the efficiency of die casting. Very complex and detailed parts are made using this technique. It supports the casting of small and light parts.
Working
The sliders of the die contain multiple cavities on them. Some support four cavities and can go up to six cavities. The moving of each cavity is independent of the other. These ensure the repeatable opening and closing of the sliders to provide flexibility. This allows efficient and rapid cooling of the molten metal. After the metal cools down, it is dismounted with pressure using all cavities.
Application
Multi-cavity die cast tooling is used in the production of small parts that need more detailing. Large parts are made using conventional die cast solutions. Multiple-cavity die cast tooling provides consistency and accuracy to the cast parts.
Which methods can enhance the die casting mold life?
Die casting tools of a high-quality have a longer life span. But this life can still be enhanced using certain techniques.
Tool Operation
Die cast tools come with certain instructions that help when using the tools. If the tools are operated without following the instructions, the life span can be impacted greatly. To enhance the life of die cast tools, they are operated carefully and with expert handling. It is not a good idea to expose the tools to conditions they are not suitable for.
Tool Welding
To enhance the life of die cast tool and to repair it, tool welding is the best option. It does not affect the functionality of the tool and makes it as strong as before. This extends the service life of the tool.
What is mold flow simulation for die casting tooling?
Die casting tools are created using a certain process. Mold flow simulation is one of them. CAD/CAM software are used to simulate the flow of molten metal in the tools. This shows how the molten metal will flow through the die and the molds. We can see how the mold will get filled with the high-temperature metal and how will it affect the tool.
Using the procedure of mold flow simulation, the die casting tool is manufactured. An optimal solution is found out using this process. This makes the tool adapt to the process that is going to take place when casting a material.
What are the advantages of die casting dies?
Die cast dies is the most important part of the process of die casting. This can highly impact the end result. When making the die cast dies, only premier dies are prioritized. This is because they provide long-lasting advantages:
- The quality dies help in high volume production
- The need for secondary operations is reduced.
- The machining costs are reduced and long-life products are obtained.
- Dimensional tolerances of the casted parts are obtained using the right tooling.
- Complex geometry parts with tight tolerances are produced using these tools.
- Efficiency in the production processes especially for large manufactures.
How does the die casting dies work in high-pressure die casting machine?
The process of high-pressure die casting needs the right die to obtain ideal results. This is how the die works in the process
Process:
Molten metal feeds the die with high pressure. The cover die allows the molten metal to run into the mold. The molten metal cools down in the mold and takes its form. The mold is sculptured in the form of the part to be produced. When the metal is settled in the form required, it is ejected out of the die using the ejector half of the die. Ejector pins push the set part out of the die and close behind for the next part.