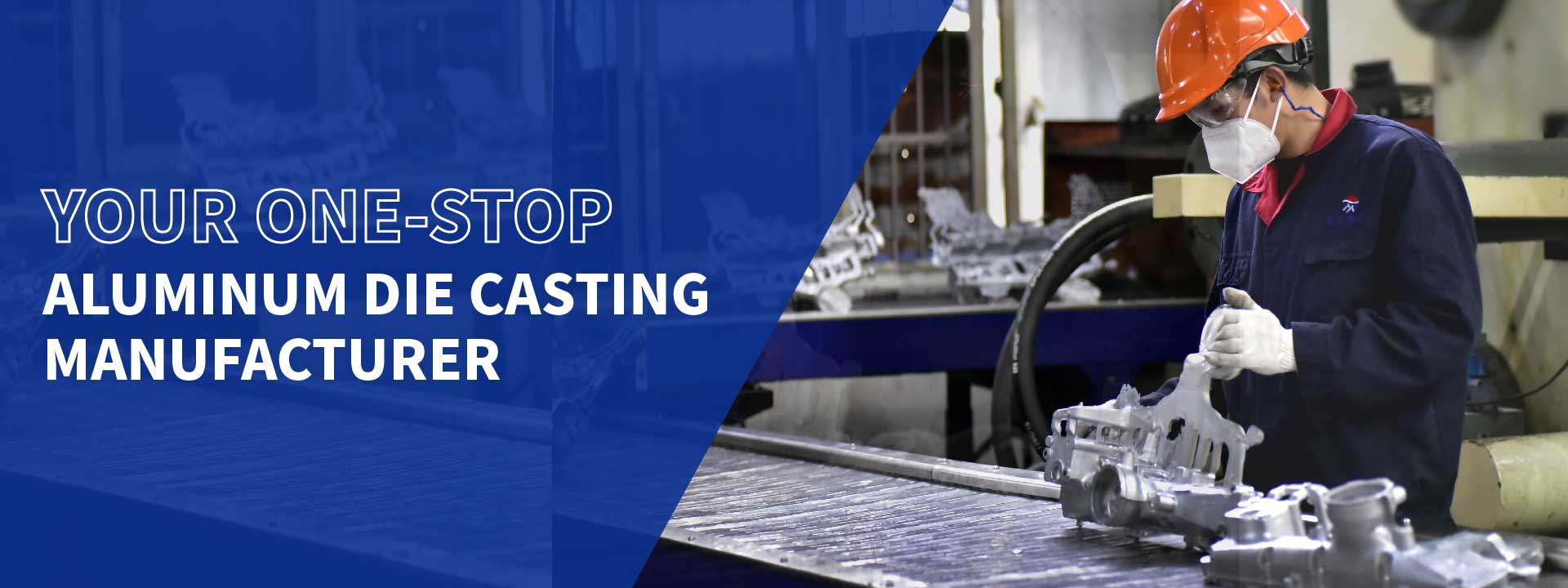
CAST ALUMINUM CUSTOMIZED SERVICE IN CHINA
- ISO 9001:2015 & IATF 16949:2016 certified aluminum cast manufacturer
- One-Stop Cast Aluminum Service
- Provider 10+ years experience, 4 facilities & 182 professionals
- Our Fast production assures you always on-time delivery
- Welcome High-Mix, Low volume Projects
We customize all orders to suit your budget and business plan so that you can run your production lines smoothly!
RICH MANUFACTURING EXPERIENCE ON 2500+ CAST ALUMINUM PARTS
HOW SUNRISE METAL SUCCEED YOUR CAST ALUMINUM PROJECTS
We hire experienced quality engineers and deploy advanced quality equipment. We take strict quality control for every production process. All we do is to assure the best quality of the products and services we provide to you.
With an average of 10 years’ experienced engineering team, we provide you DFM, engineering support during the whole project life.
We provide you one-stop service integrating Rapid Prototyping, Die Casting Tooling, Aluminum Die Casting, CNC Machining & Surface Finishings.
ADVANCED ALUMINUM DIE CAST PRODUCTION EQUIPMENT AT SUNRISE METAL
YOU CAN EXPECT STRICT QUALITY CONTROL ON CAST ALUMINUM PARTS
GLOBAL CUSTOMERS VISIT
As a leading cast aluminum company, Sunrise Metal provides aluminum die cast service worldwide. Many global clients visit Sunrise Metal to check our capability and capacity. Through on-site factory tour, they trust us and award us with more business. To better know our customers’ business needs and products, we also regularly visit our global customers.
Warmly welcome you to visit us.
Global-based Customers
- ISO 9001 & IATF 16949 Certifications
- Tooling Equipment
- Die Cast Equipment
- Machining Equipment
Die Casting Tooling WorkShop (Nantong) | ||||
Machining Type | Brand | Model | Stroke | Unit |
Grinder | TATUNG-OKUMA | KGS-615AHD | From 380mm to 1600mm | 4 |
Drilling | ShenYang Machine | Z3050*16/1 | 1600mm | 1 |
Sawer | Juli | MJ034W | NA | 1 |
Lather | Shanghai 2nd Machine | C6250A | 1000mm | 1 |
EDM | EDM Korea YIHAWJET Taiwan | NA | From 438mm to 1100mm | 8 |
CNC | Local Brand | SONYU-SL850 | From 850mm to 3015mm | 5 |
Wire Cutting | Local Brand | DK7763 | 800*630mm/1000*800mm | 2 |
Milling Machine | Local Brand | QJM-S2 | NA | 4 |
High-speed Cutting Machine | Local Brand | 906148 | 750mm | 1 |
Deep Hole Drilling | Local Brand | DHD-1513 | 1513mm | 1 |
Die Spotting Machine | Nice Dongguan | NC150-1511 | 1400mm | 1 |
EDM/wire cutting Combined Machine | Local Brand | DK7755 | 550*630mm | 1 |
EDM for very small hole | Local Brand | DD703 | 300*400mm | 1 |
3D Laser Scanner | Sikan Hangzhou | HSCAN771 | NA | 1 |
Kunshan Die Casting WorkShop | |||
Die Casting Machine Type | Brand | Ton | Unit |
Aluminum Die Casting Machines | LK | 280T | 1 |
LK | 400T | 1 | |
LK | 500T | 1 | |
LK | 800T | 1 | |
Nantong Die Casting WorkShop | |||
Die Casting Machine Type | Brand | Ton | Unit |
Aluminum Die Casting Machines | LK | 280T | 1 |
LK | 300T | 1 | |
Yizumi | 400T | 1 | |
Buhler | 500T | 1 | |
LK | 630T | 1 | |
Toshiba | 800T | 1 | |
LK | 1600T | 1 |
CNC Machining Production Equipment | ||
No. | Equipment | Q’ ty |
1 | CNC Lathe | 4 |
2 | CNC Machining Center | 17 |
3 | Fanuc CNC Machining Center | 2 |
4 | Hass CNC Machining Center | 2 |
6 | Grinding machine | 4 |
7 | Saw Machine | 1 |
8 | Drilling Machine | 2 |
GET A FREE CONSULTATION
If you are looking for a Chinese cast aluminum supplier, contact Sunrise Metal. When you have any hesitation or any design doubt on your aluminum die cast projects, Sunrise Metal Engineering Team can be your free consulter. Sunrise Metal gives suggestions on your custom cast aluminum parts at 3 aspects:
1. Your design evaluation.
2. Feasibility analysis for mass production.
3. Project time and part’s cost-saving.
CAST ALUMINUM: THE ULTIMATE FAQ GUIDE
If you’re in an OEM, ODM, or any manufacturing industry, you probably know about cast aluminum or at least heard about it. And if you didn’t, don’t worry, we’re going to cover from the basics to advance today.
Like aluminum die casting, this is one of the greatest manufacturing processes in terms of design, flexibility, affordability and many more benefits.
Companies worldwide, including larger aerospace, marine, automobile companies to small electronics companies are leaning toward the casting process due to the advanced benefits and features it has to offer.
No matter which industry or company you belong to, everyone needs high-quality casting parts and a reliable cast aluminum solution from the manufacturer. And for new buyers, that can be quite challenging.
This article aims to guide you through the most important and commonly asked question about cast aluminum. So you have a better understanding and can find quality aluminum casting for your project.
- What is cast aluminum? Why is it important?
- What is cast aluminum alloy? What are some examples?
- What are the advantages of cast aluminum?
- What is the applicable surface finishing for Cast aluminum?
- What is the difference between cast and wrought aluminum alloys?
- What is the cast aluminum process?
- Is cast aluminum magnetic?
- Is cast aluminum toxic?
- What is the difference between cast aluminum vs. machined aluminum?
- What is the difference between cast aluminum vs cast iron?
- What is the difference between cast aluminum vs. forged aluminum?
- Can I use an aluminum mold to cast aluminum? How to make a reusable mold to cast aluminum?
- Why use cast aluminum patio furniture?
- How to melt aluminum for casting?
- How to bond cast aluminum together?
- What are the differences between die cast aluminum vs sand cast aluminum?
- What are the real-life applications of cast aluminum?
- Why chose Sunrise Metal as your cast aluminum parts manufacturers?
- What are the defects for casting aluminum manufacturing?
What is cast aluminum? Why is it important?
When molten aluminum is poured into a mold and creates a mold shape when cooled down, it is called cast aluminum. Basically, aluminum casting is a process that involves pouring liquid metal into a mold. And when the liquid takes the desired shape as it cools.
Cast aluminum parts are widely used for medical, aerospace, marine, automobile and various other industries to manufacture complex parts. More than half of the aluminum used in vehicles is made from this process.
The reason why companies are so dependent on cast aluminum manufacturing is obvious. It allows them to get the desired products in the highest accuracy and great strength and other benefits it offers.
Especially companies that need complex items like aerospace or marine industries. They often require a very custom design with high levels of complexity. And for this reason, the manufacturing process is the best choice for them to get exactly what they need.
The application of casting in the automobile industry is growing at a rapid pace. Various industries are now primarily dependent on parts made by casting.
The cost of the process is relatively cheaper as well. So when you’re purchasing a bulk amount of parts, you need to minimize the cost as much as possible without hampering your parts’ quality.
With the highest accuracy, great strength and more affordability, this is one of the greatest choices for manufacturing parts for any industry. With this manufacturing process, you will certainly get satisfied with your final product. All you have to do is ensure the quality of casting products from your manufacturer.
What is cast aluminum alloy? What are some examples?
Cast aluminum alloys are often 3xx series alloys that are used for the aluminum casting process. These alloys generally have great surface finishing and low melting points. Also, they offer great strength and are capable of controlling grain structure as well.
Aluminum alloys are used for many products that we use every day. Starting from kitchen items, furniture to marine engine parts, these alloys are used for a wide range of products.
Before the metal alloys are ready to be used in various applications, it goes through the casting process. Which makes it stronger, durable and adds the amazing features we get with the final parts.
Here are some examples of that:
Al-Si-Mg: They are one such material group and they are particularly popular for their excellent castable, intrinsic hardness and good corrosion resistance. Al5052, Al6061, Al6063, Al7072, Al7075, etc.
Al-Si-Cu: These alloys are particularly well for aluminum die casting. ADC12, A380, AlSi12, A413, etc. Which are some of the commonly used alloys in this segment.
What are the advantages of cast aluminum?
Cast aluminum parts are widely used in various industries around the world. Because of the flexibility and wide range of characteristics, they are popular among manufacturers as well.
Here are the major advantages:
- Aluminum casting can produce complex parts with the highest accuracy, enabling cast aluminum manufacturers to replicate the exact design and reduce the need for machining. Parts of cast aluminum are used by all the major industries due to the design accuracy and fewer defects.
- The parts are lightweight materials while offering outstanding strength as well. Although cast iron is much stronger, considering the weight to strength ratio, cast aluminum parts are way ahead of any other casting process. Because of the low cast aluminum weight, it’s used for the automobile and aerospace industries.
- Compared to other processes, these parts are less expensive and affordable for all industries
- Outstanding thermal conductivity.
With the cast aluminum process, we get many amazing benefits that other manufacturing processes fail to offer. This is why the casting process is so widely used in our everyday life and various industries.
What is the applicable surface finishing for Cast aluminum?
Cast aluminum solutions include various surface finishing that will make the parts corrosion-resistant. Here are some of the surface finishing methods offered by Sunrise Metal:
- Anodizing
- Chromate
- Powder coating
- Painting
- Plating
- Sandblasting
- E-coating
- Soft-touch paint
These surface finishing make the final products corrosion-resistant and more effective.
What is the difference between cast and wrought aluminum alloys?
Cast and wrought alloys are two main categories when it comes to aluminum alloys. The easy way to describe them is that cast aluminum alloys are generally in melted form, whereas the wrought alloys are worked in the rigid form.
Cast Aluminum Alloys: This alloy contains aluminum as their primary metal and compared to wrought alloys, there is a larger proportion of alloying elements present in them. However, the tensile strength is lower than the wrought alloys.
Wrought Aluminum Alloys: The word ‘wrought’ indicates that the metal is shaped or in solid form. Wrought aluminum alloys have similar elements in them. The difference is that they contain elements lower in percentage.
Key Differences
- The main difference is cast aluminum alloys are liquefied in a furnace before casting and the wrought alloys are worked in its solid form.
- Cast aluminum has a higher percentage of alloying elements than wrought aluminum alloys.
- Wrought aluminum alloys have higher tensile strength compared to the others.
- The machining process makes wrought aluminum. Cast aluminum alloy is made by melting in the furnace.
- Cast aluminum alloys have some internal and external defects, whereas the other one doesn’t.
- Cast aluminum alloys are cheaper than wrought.
- Cast aluminum alloys are more flexible and can be shaped into various models easily.
- Welding and machining are easier for wrought aluminum alloys than cast aluminum alloys.
- Wrought aluminum alloys have better surface finishing.
- Cast aluminum alloys have a comparatively lower melting point and are strong at high temperatures as well. But, wrought aluminum alloys have a high melting point and are weak at high temperatures.
What is the cast aluminum process?
This can be done by various methods available for casting metals. Generally, the process requires some common elements like melting the metal, making molds for casting aluminum, pouring into molds, etc.
Before starting the process, you need to ensure the mold is right because the mold will directly affect the shape, accuracy and finishing of the final product.
The mold can be made out of various elements. Steel and sand are often used for making a mold. Reusable aluminum molds can be a great choice for this too. The mold’s melting point should be higher than the molten metal.
If you use sand for making the mold, you’ll need to use a pattern actually to shape the mold. When the sand has taken the shape of the pattern, it’s removed from the sand. The sand is pressed or rammed to make the desired shape.
When the sand has perfectly taken shape and can be used as a mold, you can pour the liquid aluminum into it. Then what you need to do is wait for the liquid to cool off and take the mold’s shape.
When you’re using a steel mold, the process gets much easier because you don’t have to press the sand or make a new mold every time for a new casting. Generally, steel mold is reusable and you can use one mold to make various parts.
However, once the melted metal is poured, you’ll need to wait for it to be completely cooled off. After the metal is cold, it takes the shape of the mold and forms an external layer of aluminum oxide, enabling the parts to be corrosion resistant.
After the process is done, depending on the final product and requirements, the part might need machining, welding, or any form of surface finishing.
Is cast aluminum magnetic?
Cast aluminum is not a magnetic metal. It’s one of the most used metals in the world. Because of the many features and benefits, it offers. One of them is that it’s completely non-magnetic metal.
However, in high magnetic fields, it can show a slightly magnetic attraction. But in normal circumstances, we can safely say that this is a non-magnetic metal.
Is cast aluminum toxic?
No, it’s not toxic at all. Because aluminum casting is widely used for cookware, you might be concerned about the safety of using this metal for cooking food.
Because of the high heat conduction ability and easy to clean surface, they are widely used worldwide.
In 2003 it was broadcasted that the metal was linked with Alzheimer’s disease. However, it was a false alert and when tested, scientists found no link whatsoever between aluminum cookware and the disease.
But that was not really advertised widely. Because, after all, “we’re safe” is not quite big news for the news media. This is the reason why, after so many years, people still have doubts about it.
The amount of aluminum leaches into food is very low to harm the food. Although, you shouldn’t cook acidic foods like tomatoes, citrus or vinegar. Because the metal can be reactive with these acidic foods and alter the taste of them.
The cookware is a completely safe material to use for cooking. Naturally, it contains no harm to food or the human body. The quality aluminum casting uses surface finishing like anodizing. And that makes the surface even safer for your kitchen.
What is the difference between cast aluminum vs. machined aluminum?
Cast aluminum and machined aluminum both processes are used to make new parts with aluminum. However, they both function in very different ways.
Machining is a subtractive method where automatic equipment removes material from a workpiece and gives the piece the desired shape. Cast aluminum is a process where a mold is created according to the design and then melted aluminum is poured into it. After cooling down, the molten metal takes the mold’s shape.
Machining doesn’t require any heating or melting activity but does require an automated machine with perfect programming, which can cost more than the casting process.
Aluminum alloy casting can be done as a DIY project and with proper experience, safety measurements and the right elements, you can do it yourself. But the machining process requires a professional touch and can only be done in an equipped facility.
Both of these processes are necessary for various reasons. Companies usually need very complex designed and customized shapes and designs with their own requirements and budget.
Based on the client’s requirement, manufacturers or suppliers choose the best option for the particular design.
What is the difference between cast aluminum vs cast iron?
Both materials have a wide range of applications in our daily life and industrial uses. However, because of the different structural systems, weight, cost and other factors, the applications vary significantly.
Cast aluminum is heavily used in automobile, marine, aerospace, medical and other industries. Because it’s lighter than iron metals and the strength to weight ratio is great.
Cast iron wouldn’t be a great choice for those industries. As they are heavyweight material, aerospace, marine or automobile companies wouldn’t use it because it will increase the weight of their vehicle.
Cast iron is more expensive and less flexible. But that doesn’t stop cast iron from being used in other applications.
A group of iron-carbon alloys with more than 2% carbon content is known as cast iron. Aluminum casting is a process engaged in pouring liquid metal aluminum into a mold.
Cast iron is heavier than cast aluminum. Also, cast iron requires a long to preheat due to its low thermal conductivity and higher heat capacity. Because of high heat retention, cast iron usually takes a longer time to cool down. Cast aluminum oxidizes more slowly than cast iron.
Whilst cast iron is stronger than aluminum, it’s a brittle metal and aluminum isn’t. If there’s any fault in manufacturing, the metal can fracture instantly or over time. Different surface finishing methods make aluminum more prone to rust and corrosion.
Although cast aluminum can be scratched easily and has a shorter lifespan compared to cast iron, however, if treated properly, both these materials can last a really long time.
What is the difference between cast aluminum vs. forged aluminum?
Aluminum forging is very different from machining or casting. In the casting process, we see that molten aluminum is poured into the mold and when it cools off, the molten metal takes the shape of the mold, which enables us to get the desired shape of our parts.
In forging, the metal is shaped by localized compressive forces.
Temperature:
As you can imagine, the two processes are very different from each other. And the core difference is in the temperature.
In forging, the temperature is lower and below the melting point limit. Because in this process, you don’t need to melt the aluminum. All you need to do is heat it to the extent that it becomes soft and shaped using forces.
The casting process requires a very high temperature, well above the melting point, because it requires the metal to be melted and poured.
Number of steps
The casting process has a higher amount of steps to be done. First, you need to make a pattern according to the shape and then make the mold, melt the metal, pour the metal into the mold, seal off the mold and then open up the mold.
As you can imagine, with casting manufacturing, there are no shortcuts and you have to go through each of them.
Forging seems easier compared to casting. Because you’ll need to heat the metal and apply forces to shape it. There’s no additional step required.
Effectiveness and accuracy
Although the forging method seems easier, you can’t forge large or complicated items using this process. Forging can be perfect for smaller parts or parts that don’t require a complicated shape.
For this kind of part, the casting process is perfect. Because it can produce way larger parts than forging, when it comes to the accuracy of a complicated design, casting is one of the best metal manufacturing processes available today.
For instance, if you’re working with a hook, knife, gardening tools or this kind of item, forging can be the right option. But if you’re manufacturing engine parts or telecommunication parts, you need to rely on the casting process.
Strength
Forged aluminum has higher strength compared to any other alternatives, including cast aluminum. It also has higher wear resistance.
Performance
Because of the high performance and strength, forged aluminum is used for wheels, aerospace body parts, gear equipment and many more. Because of the high density and strength, they can handle high impact and shock, which makes it perfect for harsh uses.
Cost and lead time
Forged aluminum costs less than cast aluminum. It also has a lower lead time than the other alternative, making it an affordable option if you have a low budget.
More time spent on the production equivalent more money. While the production process is already cheaper and lead time is less, you can save a good amount of money by choosing forged aluminum for your parts.
Can I use an aluminum mold to cast aluminum? How to make a reusable mold to cast aluminum?
Yes, you can use aluminum to make the mold for your cast aluminum project. Keep in mind that the aluminum alloys used for molding must have a higher melting point than the molten aluminum.
When producing 1 or 2 parts, easier methods like sand casting are perfect, especially for DIY projects. But when you need a bulk amount of parts, sand casting can be time-consuming and need a lot of work hours.
You need to make a permanent mold that can produce many parts and doesn’t require to change it after each part is produced. Making molds for casting aluminum is not very hard once you know the basics of it.
Multiple ways can produce a mold of your production. The mold should be at least two parted and opened and sealed off easily.
And most importantly, you need the mold to be highly accurate and precise. Otherwise, all the parts produced with this mold will have defects, leading to a heavy loss. For this reason, you need to choose the right method to make your mold.
Machining can be the best option for making a precise and accurate mold for your die cast material production. With machining, the mold will certainly have no defects if done right, and the end product will be exactly as you require.
Why use cast aluminum patio furniture?
In recent years, cast aluminum patio furniture has become a household item. Not just in houses- restaurants, hotels, parks and offices also started to use this amazing furniture set.
Looks
One of the main reasons why people so love these furnitures is their looks. They are perfectly suitable for both indoor and outdoor uses. And when used indoors, it enhances your interior of the house.
The slip and sharp look with beautiful colors make it perfectly go with any room or position.
Low cost and low maintenance
Compared to any other furniture form, you get a lovely deal when you choose to buy this one. If you’re not sure about this, go to your nearest furniture shop or check online. Cast aluminum offers nice and beautiful furniture with very affordable pricing.
Unlike other fancy furniture, it doesn’t have a high maintenance cost, making it even more favorite for budget buyers. The furniture is effortless and fast to clean so that you can save a lot of time on that too.
Lightweight but stable
Unlike wooden or steel furniture, they aren’t heavy. In fact, this furniture is so lightweight; you can lift multiple chairs at a time. So when moving to a new home or changing your interior, you don’t need to hire people to move your furniture.
No rust
Iron and steel furniture might have more strength than this, but cast aluminum patio furniture will never rust, unlike them.
Rust is a common issue among most metals and although it has a longer lifespan, steel and iron also rust over time. Fortunately, cast aluminum furniture is free of this defect, thanks to its effective surface finishing methods.
Varieties
When you decide to buy this furniture, you’ll be amazed at how many variations of designs and colors are available.
You can choose your furniture according to your interior or exterior design that will suit you the most.
Comfort
In general, the cast aluminum patio furniture doesn’t require a cushion as a mandatory item. But you can always use it for an increased amount of comfort or giving it a new look with your customized and designed cushion too.
Outdoor Use
The Best thing about this furniture is that they are weather-resistant and can be used outside in all weathers. You can have your furniture set up in the garden, rooftop, or on your balcony and enjoy a wonderful time out there.
With wooden furniture or any other alternatives, they’re more suitable for indoor use and not for the outdoors. If you love spending time outdoors or in your garden, you’re going to love these cast aluminum outdoor furniture.
How to melt aluminum for casting?
Compared to other metals like steel or iron, aluminum has a low melting point that should be kept in mind from the beginning. Cast aluminum melting point is 660.32 degrees Celsius.
The process:
- First put on safety glasses, heatproof gloves, long sleeve shirt, and full pants. Keep in mind that the process requires extreme heat and your skin can be damaged easily with any mistake.
- Then enter the aluminum metals into the skillet. Put as many as possible at each time and close the lid.
- Now lit up the kiln and set the temperature at a rate where it melts the aluminum but not the steel pot we’re using.
- When the aluminum is melted, use a tong to remove the crucible from the kiln. Those materials are useless and you can easily remove them when the pure aluminum is melted.
- Now that you have melted aluminum, it’s ready to be poured into the mold right away. When pouring the metal, ensure that all the safety measures are taken and no accidents take place.
- After pouring, give it 15-20 minutes to cool off. When it’s cold, the metal takes the shape of the mold and then removes the mold from aluminum and you have the final product.
How to bond cast aluminum together?
Often we need to bond multiple pieces of aluminum together. And many ways can bond cast aluminum. But you need to do it in the right way.
Often people try and fail to glue the aluminum for various reasons. One of them is that their glue fails. But one important thing to keep in mind is that the reason for this is not the glue; it’s the oxide layer on top of the aluminum.
The oxide forms very well with the glue but doesn’t have a strong bonding with the aluminum, so when the oxide comes off from the aluminum, we blame the glue for not working.
Today we’ll see the two most effective ways to bond cast aluminum.
Gluing Aluminum
Gluing is one of the most used methods to bond this metal. Because it’s easy and less complicated, you can use this method as well.
First, you need to clean and clean the surface where you want to apply the adhesive. Wash the area with mild soap and then dry it off with a rag. After that sand, the area so it will adhere to the glue even more.
Now apply the glue to the area and hold it against the other piece. You can use a thin wood and clamp it to make the bond more sticky and powerful.
After a couple of minutes, the bond should be formed, let the glue dry off and you’ll have perfectly bonded aluminum pieces.
Weld cast aluminum
Keep in mind that not all cast aluminum are weldable. Depending on the casting composition and how the casting was created, most of them are weldable, but some aren’t.
sand castings, permanent mold castings, and investment castings- are usually weldable at ease.
First, you’ll need to clean the area like the other method we’ve discussed above to weld the metal. But in addition to that, it’s better to preheat the surface to make sure you’re getting the best result.
I suggest using the MIG welding formula to bond two cast aluminum. For this welding, you can use plain argon gas or argon helium mix. Be careful about the mix when the pieces are very thin.
Start the welding with a clean electrode. You can use a string bead technique while moving the welding machine. However, it would be best if you didn’t change the angle of your electrode.
While moving toward point A to B, you should increase the speed. This will help minimize the cracking of the bond.
When you’re in the horizontal position, try to point the gun in an upward direction.
What are the differences between die cast aluminum vs sand cast aluminum?
Die cast aluminum is a type of aluminum where the metal is forced to melt under high pressure to characterize them into desired shapes on the mold cavities. A mold cavity is a tool created from two hardened tool steel dies.
The process’s pressure is maintained during solidification, after which the mold is opened, and aluminum is removed. The molds in this operation are called dies, so the name is die casting.
Sand casting, also known as a sand molded casting, is a casting metal characterized by sand as the mold.
This is the simplest and most popular casting method among DIY lovers and small manufacturers as well.
Greensand, regenerated sand mixed with synthetic binders, is used during the casting process. In this process, the mold is created by mixing sand, clay, and water.
The mold will have two or more parts; they’re placed in the mold halves. The two halves are locked together, and molten aluminum is poured into it. It will take a long time for the molten metal to cool down as sand and clay do not absorb heat.
Chills can be used as a catalyst for faster cooling. Allow it to solidify, and de-sand the casting. The heat from the molten metal dried out the moisture making the cast easy to crack open when the metal has cooled.
Aside from the difference in the casting processes, die cast materials and sand casting have different applications.
Medical devices manufacturers mostly use die casting, whereas cylinder heads, valves, engine blocks, pump housing, etc. can be made from sand casting.
The sand casting process is cheaper, and its wall thickness is thicker than die casting.
What are the real-life applications of cast aluminum?
This is a process that allows us to create custom design products with aluminum metal. From our kitchen items to the aerospace industry, cast aluminum production is needed everywhere.
Automobile
Vehicles are one of the ideal examples of this process. As you probably know, the automotive industry is hugely dependent on it and vehicles usually contain many aluminum metals. Out of all the aluminum, more than 50% of them are cast aluminum.
Marine
The marine industry is another example of industries that require cast aluminum regularly. Starting from the engine to various devices, it is used for manufacturing a lot of the parts for them.
Medical
The parts are needed for making complex medical devices or equipment. Medical equipment is very complex and requires the highest accuracy and precision. Cast aluminum is the perfect choice for them to make quality parts with the right measurements.
Aerospace
The aerospace industry requires parts that can stand up to harsh weather conditions, is precise and has the best quality, and cast aluminum meets them all. The most important thing for them is to get the design right.
Often they require a very unique and complex design and other than this process, the design would be tough to manufacture.
Engine Parts
In every engine, we can find a significant amount of cast aluminum in it. Because the engine requires many smaller parts that are precise and complex and helps operate the engine smoothly. Casting engine parts using aluminum reduces the cost while ensuring the highest quality of the material.
Cookware
Cast aluminum cookware has been extremely popular since its beginning. Before that, we used to use cast iron cookware. And iron materials are very heavy and not very easy to use while cooking.
Today, in almost every home and kitchen, we can find cookware made of cast aluminum.
Why chose Sunrise Metal as your cast aluminum parts manufacturers?
Cast aluminum parts are used by OEM/ODM, small to large companies for different types of products. Although they all have their unique set of requirements and designs, they all look for ultimate quality and affordable prices.
When you’re looking for a cast aluminum parts manufacturer, you need to check these qualities:
- Can they deliver the highest quality parts at an affordable rate?
- Can they deliver before the deadline?
- Communication of the manufacturer
- Do they provide an all in one solution?
Because finding a manufacturer is very easy, but finding ‘the right manufacturer’ can make or break your project.
Sunrise Metal’s 1-stop, all in one solution, allows you not to get the best quality only, you get all the other related services done in one place.
This means you don’t have to hire three different manufacturers for rapid prototyping, casting and surface finishing. Here at Sunrise Metal, we take care of your project as one of our own. You get all the required services from us in one place.
Image: 19.sunrise-metal
Sunrise Metal is committed to providing an excellent experience to our customers worldwide when it comes to quality. This is the reason we’ve been honored to work with some of the world-renowned brands and made them our happy and regular clients.
When you work with us to cast an aluminum manufacturing service, we try to deliver more than we promise. From consulting, design to final products, you get to communicate with us in every step of the process. So you know what’s happening with your order.
Our quality control team does multiple through testing before, during and after the production. So we can deliver only the best result for you.
Our decades of experience and skilled workforce allow us to give you the perfect service, not only for cast aluminum manufacturing but also for all the relevant services necessary to make your project successful.
What are the defects for casting aluminum manufacturing?
Casting defects are those unwanted irregularities that are tried to be avoided and, if occurred, can cause the parts to be rejected.
Let’s see some of the major defects that can occur in the manufacturing process:
Pouring Metal Defects
When the molten aluminum cannot fill the mold cavity, this defect occurs. What happens is that a small area of the final products remains unfilled. This also occurs when two fronts of liquid metal can’t fuse properly. They leave a weak spot and therefore, a defect occurs.
as porosity defects
In melted form, the metal can hold a large volume of dissolved gas. However, once it hardens, it can’t. When the liquid metal has dissolved gas in it and starts to cool down the dissolved gas forms bubbles.
This defect hampers the strength and durability of the cast aluminum. This is why cast aluminum manufacturers try to avoid gases like hydrogen to dissolve in the molten metal.
Shrinkage defect
This defect occurs when the solidification starts. Shrinkage defects have two types, open shrinkage defects and closed shrinkage defects.
Open shrinkage defects form on the surface of the casting parts. Closed shrinkage defects form within the casting.
Metallurgical defects
Metallurgical defects have two types, hot tears and hot spots.
Hot tears are also known as hot cracking. As the name implies, it involves cracking of the metal as it cools. This occurs due to low-quality aluminum alloys and poor mold design.
Hot spots occur when a hard part of the metal is cooled down before the surrounding area. This occurs due to the wrong formation of the melted aluminum.
Today we discussed every bit of cast aluminum topics we get asked quite often. We put together this massive article to eliminate any confusion that you might have had about the process.
We understand that ordering casting service is not the easiest job to do, especially when you’re ordering for the first time. There’re many things to consider in terms of importing rules and regulation, right design, budget, quality and deliverability.
You need more than manufacturing; you need a partner who can take care of your manufacturing side. Sunrise Metal is committed to reducing the stress of all kinds of casting manufacturing.
With us, you get the best quality and less hassle. We’re always here to listen to what you have to say. This article was designed to give you a brief idea about the process. Before ordering or purchasing, you need to know more than that. And we welcome you to get in touch with us and have a visit to our facilities if possible.