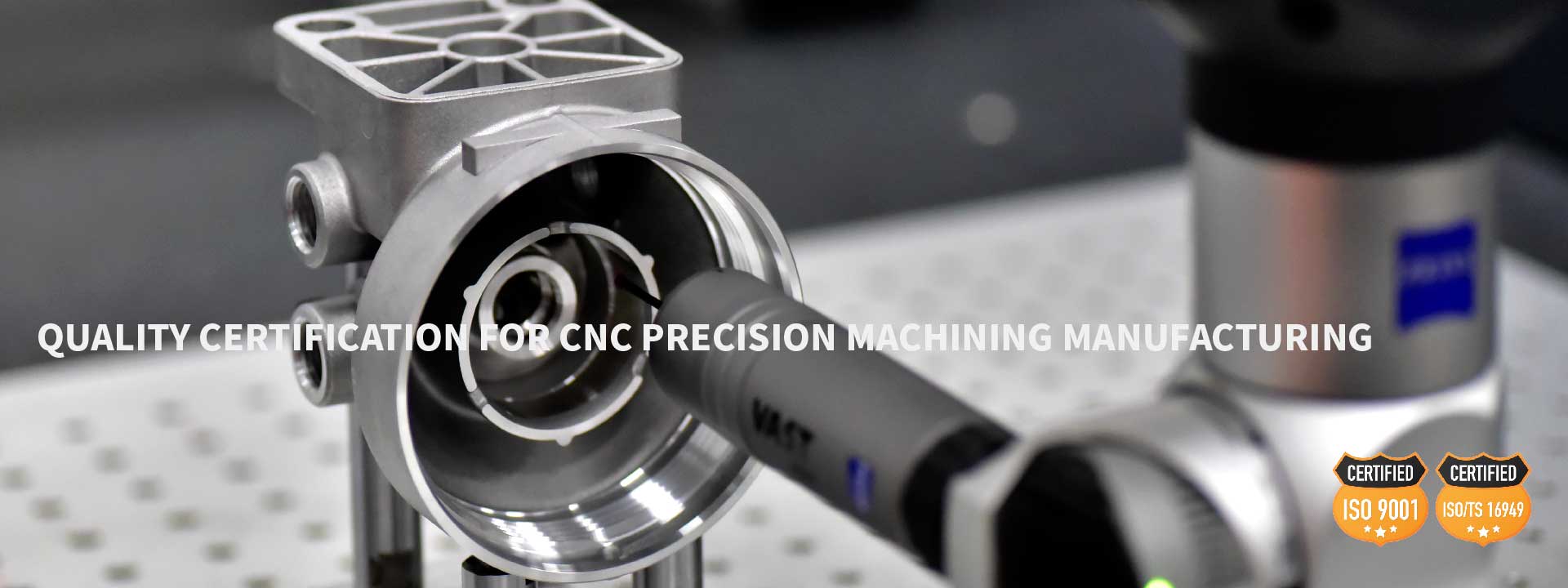
Your Brilliant CNC machining Manufacturer in China
Sunrise Metal’s CNC machining is capable of manufacturing Rapid Prototypes and Production Parts. We have 1 dedicated Rapid prototyping plant which is focused on CNC machining prototyping parts. We also have another Independent CNC machining shop to make mass production of CNC machining parts.
- With our high advanced CNC machines, we have 2 sets 5 axes and a 7 axis CNC machine, we can off you very complicated customized CNC machining parts.
- All the customized CNC machining parts we offered, are effectively under our strict quality inspection. Sunrise metal is equipped with many high precision testing instruments, such as fully-automatic scanning CMM—made by Carl Zeiss, X-ray detector, Spectrometer, etc.
- Sunrise Metal, an ISO9001 & ISO 13485 & IATF16949 certified CNC machining supplier, has built a comprehensive fast production system—include rapid prototyping and fast tooling technology, we always promise you on-time delivery to all your projects.
Sunrise Metal Is Ready for Your CNC machining Parts
Sunrise Metal is Capable to Offer You Customized CNC Machining Parts with any quantity
Sunrise Metal equipped with 68 sets CNC machines in our Rapid prototyping facility and another 23 sets CNC machines in our CNC machining shop.
We can help you make CNC machining parts with the material, such as ADC12, A380, A413 and AlSi12, Steel, Copper, and many kinds of plastic, etc.
We also can do Ultrasonic cleaning, surtec650, powder coating, and liquid painting, silk printing, anodizing and plating, etc. surface treatments for your parts. All these surface finishing are ROHS and REACH applicable.
Your Perfect CNC Machining Parts Coming From Sunrise High End Manufacturing Equipment
Recent CNC Machining Projects
As a government-approved High and New Tech Enterprises, Sunrise Metal has got 16 Patents on CNC machining or Tooling. It‘s a kind of reward and encouragement to our team, it’s also a kind of assurance to your projects.
- Experienced Team
- Advanced Equipment
- Global Clients
- Premium Quality
- Fast Delivery
Sunrise Metal has a dynamic workforce including organized teams of experienced engineers, professional customer service representatives, quality assurance officers and skilled production workers. Following international guidelines on cooperation and production standards, they make the best team for your projects.
No. | Name | Stroke | Q’ty |
1 | Mazak 7-axis turning&milling Machine | Ø658*1011MM | 1 |
2 | Mazak /Hass 5axis CNC machine | Ø850/Ø600 | 4 |
3 | 3-axis CNC machine center | 2000*1500MM | 1 |
4 | 4-axis CNC machine center | Ø250*800MM | 8 |
5 | 3-axis CNC machine center | 1000*600*600MM | 20 |
6 | CNC Lathes | Ø320*800/Ø610*1000MM | 2 |
7 | Sodick Wire cutting Machine | 400*400*200MM | 3 |
8 | EDM machine | 500*400*400MM | 2 |
9 | Surface grinder | 600*300*200MM | 1 |
No. | Name | Brand | Q’ty |
1 | CMM | Carl Zessis | 1 |
2 | CMM | SanYou | 1 |
3 | Spectrometer | China | 1 |
4 | Microscope | China | 1 |
5 | Projector | China | 2 |
6 | X-ray Detector | SANDT | 1 |
7 | Cleanliness Test Equipment | China | 1 |
8 | Leakage Test Equipment | China | 2 |
9 | Salt Spray Testing Equipment | China | 1 |
10 | Pneumatic Measuring Instrument | China | 2 |
11 | Hardness Testing Machine | China | 1 |
12 | Color Meter Machine | China | 1 |
13 | Thickness Testing Machine | China | 1 |
14 | Electronic Balance | China | 1 |
15 | Density Balance | China | 1 |
Get A Free Consultation
Skillful engineering consultants for aluminum CNC precision machining parts. Specialized and project relevant advice will be based on your CAD and Step drawings.
Here is just a small part but an important way that we’re serving you on CNC machining projects.
Sunrise Metal can offer full chain service for you if you have any demands on aluminum die casting projects, looking learn more about aluminum die casting.
CNC MACHINIG-THE COMPLETE FAQ GUIDE
CNC machining makes use of computer programs to produce industrial components. It’s an advanced method that caters to the manufacturing of parts that cannot be completed using die casting. Sunrise makes use of the latest technology and high-grade machinery to implement computer-controlled operations for the best results.
- What is CNC machining and what is it used for?
- What steps are included in the CNC machining process?
- What are the different types of CNC machining operations? (eg. Drilling, milling, tuning)
- What kind of machining support software is used to run the CNC machining process?
- What is the link between metallic manufacturing and CNC machining?
- What are the differences between NC, DNC, and CNC machining?
- What processes are automated by CNC machining?
- What are the advantages of CNC machining?
- What materials are used in CNC machining and which ones are most suitable?
- Is CNC machining a costly process?
- What are the different types of CNC machines and tools in use by Sunrise?
- What additional tools and components are used within the CNC system to carry out complex tasks?
- What are the ways to overcome faulty CNC machine programming?
- Are there any suitable alternatives to the CNC machining process?
- What kinds of parts and components can be produced by CNC machining?
- Which industries utilize the CNC machining process?
- What challenges are faced in the CNC machining process when producing large parts and heavy components?
- What CNC machining services are provided by Sunrise?
- What is meant by CNC lathe machining? What is the difference between CNC machining and CNC lathe?
- What is the difference between CNC machining and VMC machining?
- What is the difference between CNC machining and PLC machining?
What is CNC machining and what is it used for?
CNC machining or ‘Computer Numerical Control’ machining is a process of manufacturing industrial components that applies the use of computer programs. It regulates the movement of machining tools such as lathes, grinders, and others. Unlike additive manufacturing processes like 3D printing, CNC machining is a subtractive manufacturing process that removes material from the stock piece.
The features that cannot be produced using die casting are tailored with CNC machining. The detail and speed that CNC machining provides are not achievable with any other casting process. CNC machining has proven to be beneficial in lots of ways. CNC provides a great precision to the cutting of small parts with accuracy. CNC uses numeric control to provide precision so that all the parts cut by the CNC protocol are exactly the same. CNC has made it really easy for the operators by its computer-controlled operations.
What steps are included in the CNC machining process?
CNC machining is a subtractive process that is used to create dimensionally accurate parts using computerized machinery. The process is carried out in the following steps:
- Setting up machinery: The machine is completely set up. All the coolant levels and oil is checked to be full. The requirements are met before starting the machine.
- Starting up: Machine’s power and control switches are turned on.
- Loading tools and part to be machined: All the tools that are to be involved in the process are loaded. The part that is to be machined is also placed in its position in the machinery.
- Setting up dimensions: Once the part to be machined is placed and all the tools are ready to be launched, the dimensions are entered. The dimensions include length offsets and the positioning of every angle. This determines how the tools of the machinery will move in order to acquire a specific shape.
- Load the CNC program: The CNC program is loaded into the CNC machine using a memory drive. It is better to dry run the program. Dry running is testing the program in which part to be machined is not affected. The machines are pointed towards the air. It just shows how the tools are moving.
- Run program: The program is run on the part and any adjustments that are required are made in between the machining.
- Shut down the program: Once the machining is done, the program shuts down and stops all the machinery. The machined piece is taken out of the CNC machining center and is cleaned to remove the powdered surface.
What are the different types of CNC machining operations? (eg. Drilling, milling, tuning)
CNC (Computer Numerical Control) machining is an efficient way of machining the required parts. It is carried out by many operations. Some of them are as follows:
- CNC milling machine
CNC milling is a process used to form basic geometric shapes of parts that are being machined. This is carried out using rotary cutters. The workpiece is placed in the machine. It is made stationary while the high-speed rotating tool moves around the piece. The process removes extra material from the part. Required depth, angle, and cutting direction is fed into the program to form the exact geometry.
- CNC turning machine (or lathes)
This CNC machining operation is used to form spherical or cylindrical shapes. The angles of rotation, depth, and directions are fed into the machine. This operation has stationary cutting tools and the workpiece moves according to the fed instructions. Using this process, parts with tight tolerances are manufactured efficiently.
- CNC routers
CNC routers work a lot like CNC milling machines. The rotary cutters move around the stationary workpiece. What’s different about CNC routers is that it is used to produce intricate designs out of metal. It uses CNC to route tools towards the piece and carve it. The designs created with CNC routers are detailed and have a good surface finishing.
- CNC drilling machine
The CNC drilling machine drills through the metal pieces. The machine is computer numerical controlled and can sometimes multitask. With the different tools, it can also work as a milling or turning operator. The CNC drilling can be made more efficient by attaching more spindles to the machine. This will enable the drilling of more holes at the same time.
What kind of machining support software is used to run the CNC machining process?
CNC machining requires a program to run the machinery. The code written for it is called the G-code. CNC machining process requires support software to run the programs of CNC machining. The software that supports the process is:
- CAD software
CAD (Computer-Aided Design) software is used to design the products that are to be manufactured using CNC machining. The software is used by programmers to create a model. The model is then exported to the software to create a design that the program is going to follow while machining the part. A technical drawing is prepared using the software and the CAM software is fed with the design.
- CAM software
CAM(Computer-Aided Manufacturing ) is used to produce a technical solution to the design that is created by CAD. This software provides the manufacturing process that CNC machines will follow. The software will take up the design and will examine it thoroughly. All the dimensions will be measured by the software and a technical solution will be produced. This solution will be fed to the CNC machine in order to produce dimensionally accurate parts.
- CAD/CAM software
The CAD/ CAM software is a combination of both CAD and CAM software. This software produces a technical design of the part to be produced and then instructions for controlling the manufacturing process are carried out. This software is to help the engineers in designing and manufacturing the whole parts more efficiently.
What is the link between metallic manufacturing and CNC machining?
Metal manufacturing is the process of applying different operations on the metal in order to obtain tools and machinery for different purposes. CNC machining is used to make the process of metallic manufacturing more efficient. Here’s how CNC machining works on metals.
The machine is controlled by a computer. The computer is fed with a G-code that is specially written for the machining process. This code will tell the machine how to work on the metal in order to turn it into a usable tool. The following things are instructed to the machine in order to work on the metal part.
- The machine is instructed on where to place the tip of the tool on the metal part to be machined.
- The instructions on the speed of the tool are fed.
- The machine is also fed with the instructions on the direction in which the tool will move on the metal block.
- The axes in which the machine will move is also instructed to the machine.
The metal part manufactured through CNC machining is very precise. Every metal part created with the same instructions set will be exactly the same. This makes the process of replication fast and easy.
What are the differences between NC, DNC, and CNC machining?
The different manufacturing processes in the industries are chosen according to the preferences of each manufacturer. NC (numerically controlled) manufacturing, DNC (Directly Numerically controlled) manufacturing, and CNC (Computer Numerical Control) manufacturing are the 3 common manufacturing processes named in the automated manufacturing processes.
- NC machining
The machining is numerically controlled i.e. using letters, numbers, and symbols. It is not controlled by humans. The code is fed to the machine and the tools move accordingly. It is an additive process hence the code also controls the rate at which metal is fed to the machine. The program is written using the drawing of the desired part. It can be controlled manually as well as through a computer. The program is entered into the machine. This is done by punching holes in the program tape using a punching machine. The tape reader reads the program and carries the operation of the machine control unit.
- DNC machining
DNC machining is a manufacturing system that controls a number of machines using computers by a direct connection to it. CNC machine tools are networked through this manufacturing process in order to create more complicated tools that might require different operations to be done simultaneously. The program that is fed to the computer is distributed to different machines. The program is sent directly to the machine one block at a time for the production of more complex parts.
- CNC machining
CNC machine is an NC machine but a computer as its machine control unit. The program written for the machine is saved in the memory of the computer. This is done to use the same program for future productions. The program is fed to the computer and is sent to the microprocessor. It is then processed and is sent to the feedback unit which sends it to a control unit. The control unit controls the machine’s working from this point.
What processes are automated by CNC machining?
CNC machining is a process developed to automate the process of manufacturing. The process manufactures a new metallic part using a metallic block with very little manual help. The whole process has many parts that are automated. The automation depends upon the G-code that is written for CNC operations.
Worktable
Worktables in CNC machining have all the tools attached to it. They can be movable depending upon the operation being carried out. They are programmed to automatically move a certain distance. As the code runs, the worktable automatically moves as required. A pulse is received by the control system to judge the movement of the worktable. Rotary worktables are also automated. These worktables rotate to move the workpiece around the machining tools.
Tools
Tools are automated using the G-code. The automation includes the tool changing process. The machine is programmed to change the tools after a certain time in order to avoid any tool malfunction. This function is also used to switch between the lathing, milling, and drilling tools while working on a metal piece. Automation of tools also includes the automatic movement of tools around the workpiece. The tools are programmed to move within certain limits to create precision.
Automatic starting and stopping of machines
The machine is programmed to start working as the code is fed into the system. The machine works on the tool and is programmed to stop working when the piece is ready. The machines are sometimes programmed to release the workpiece and move the tools away until a new workpiece is placed in the station.
Automatic feeding of workpiece
This is an additional part of the CNC machining which is added to the process in order to make it more efficient. This automatically feeds a new workpiece into the station to operate on it. As the operation is completed, a new workpiece takes its place and so the process continues without any manual labor.
What are the advantages of CNC machining?
CNC machining has proven to be superior over conventional machining methods. This is due to the many advantages that CNC machining provides. Some of them include:
Automation
CNC provides automation of the machining process to a certain level. This reduces the manual labor involved in the machining process. The operator that had to work on each tool while machining now only has to give around half an hour to set up the whole machinery. The CNC machine works on its own and does not require close attention.
The operator just has to keep check of any errors that might occur in the program. The operator, after setting up the machinery, has more free time which can be utilized in operating other processes. The cost of hiring more people is saved using the process and hence makes the process more economic.
Speed
CNC machining provides speed in the process. Nothing is to be changed manually. The machine switches everything on its own. The complete process doesn’t require stopping or restarting of the machinery which fastens the process.
Safety
The CNC machining process provides the safety of the operators as well. The operator doesn’t have to work with the cutters by himself. Any malfunction can only detriment the machine and not the operator, unlike the conventional methods that work with open guard machining processes.
Precision
The process shows high precision as the factor of human error is reduced to almost zero in the working of tools. The machinery works under precise calculations hence forming structurally accurate parts.
What materials are used in CNC machining and which ones are most suitable?
CNC machining is implied on different materials due to the high automation and the precision it provides. The most common among these are
Metals
CNC machining provides almost endless options for customization of the metal parts. This makes it suitable for almost every industry. Metal parts are used in the industries where strength, hardness, and thermal resistance is required. The CNC machining works on these metals
- Aluminum
Aluminum has good formability and weldability. It offers improved corrosion resistance and is suitable to produce electronic hardware.
- Brass
Brass provides resistance to most chemicals as well as corrosion. The brass parts created using CNC machining are used in commercial products as well as in fittings and contacts.
- Copper
Copper is CNC machined to provide more electrically conductive parts. Copper parts are weak against acids and might corrode but are corrosion resistant in most environments. The copper machined parts are used in electric contacts and domestic appliances.
Plastic
Different forms of plastic are CNC machined to produce accurate parts. The ceramic peak is used to provide excellent dimensional stability and stiffness. The machined parts are impact resistant. PVC is also CNC machined to produce flame, corrosion, and chemical-resistant parts. Nylon provides high machinability and is, therefore, suitable for many industrially used plastic parts.
Wood
Wood is also CNC machined to produce intricate designs. The machining is carried on different types of wood e.g. softwood, hardwood, plywood, and many more.
The most machinable of the three materials is metal. Metal parts are also most suitable as they provide more durability and can retain small details.
Is CNC machining a costly process?
CNC machining is considered costly due to the high prices of its machines. The machines are no doubt really high in prices as compared to the machines of other processes. But there are certain factors that make CNC machining more cost-effective.
Machine Cost
The cost of the machine is not measured by the price in the market. It is measured by finding out the ratio between its life and the price. The CNC machine has a life of around 8 years which is more than that of other conventional method machines. Adding the errors in the cost, conventional methods become way more expensive than CNC machining.
Material Cost
One of the main advantages of CNC machining is that it uses way less material while machining as compared to other processes. As much material that is subtracted from the metal block is reused as could be in other processes like SLC. This also reduces the price of material making CNC machining more cost-effective.
Labor cost
The labor cost is lowest for CNC machining. The process is mostly automated and uses only one operator for its working. The operator just has to set up the machine and start it. After starting the machine, he can handle the processing of other machines as well.
This shows that a single operator can manage multiple CNC machines simultaneously unlike other methods that need multiple operators for every single machine. This also is added to the cost of machining making CNC machining a better option when it comes to cost.
What are the different types of CNC machines and tools in use by Sunrise?
Sunrise uses the advanced technology of CNC machining to cast and machine different metal parts. The machines and tools used by Sunrise for this purpose are
CNC machining centers
Sunrise uses 23 CNC machining centers from different companies. The machining centers have different interchangeable tools and can be used for any CNC operation. The automatic tool changer enables the milling, clothing, and grinding in the machining centers. The centers also contain a table that clamps the workpiece and can make it stationary or movable both.
Grinding Machine
Sunrise has 4 units of CNC grinding machines. The machines contain a rotating grinding tool that removes the material from metallic pieces by grinding material. Hard-fine machining of the parts is obtained using these machines at Sunrise.
CNC saw machine
Sunrise contains an automated saw tool that is numerically controlled. The metallic piece is sawed using the machine with complete automation. The CNC saw cut the parts with a speed of 100-160 inches per minute.
CNC drilling machine
Sunrise uses CNC drilling machines when drilling the metal parts. These machines are also used to mill and lathe too. They are fast machines for drilling as they use multiple spindles for their work.
CNC lathe
To design customized parts, Sunrise uses the CNC lathe or turning machine. The machine utilizes the process to make parts for automotive, aerospace, and many other industries.
What additional tools and components are used within the CNC system to carry out complex tasks?
CNC machining centers are employed to make the process of machining automated. The process is still not completely automated. Sometimes additional tools are added to the machining centers to make them more automated
Feeding machine
CNC machines are joined with a feeding machine. This component itself feeds metal to the clamp for processing. Once the required part is obtained, it takes out the machined part and puts another metal block into the clamp. This reduces the manual work of feeding the machine. Using this component, many parts are achieved even if the machines are working without any supervision.
Work-holding Solutions
The work-holding tools are used to provide extra grip on the tools. Loose parts can cause extreme damage to the machined parts. The worktable is added with a work-holding tool to avoid the tool from flying, breaking, or damaging the spindle.
Stocking the material
The material that is being subtracted from the CNC machines is stocked for reuse. This can be achieved by adding an extra component of a stocking pot to the machine. The powdered material will be saved in the pot and will be used for SLS.
What are the ways to overcome faulty CNC machine programming?
CNC machines are known to be reliable and efficient. They can still face difficulties that might seem minor but can change the outcome of the process. One of the major faults that CNC machining can face is the fault in CNC machine programming. New employers have difficulty finding their way around the faults as they might not be fully aware of the system’s program. These faults are overcome by the following ways:
- The employees should have proper training. They should know how to control any errors that are found.
- The employees should have a complete understanding of G and M codes that are used in the process.
- The program should have correct calibration data, compensation data, and offset information captured.
- If the system doesn’t work, shut down the whole machine and completely reboot the system.
- Minimize the variables and remove the parameters that are not being used from the program. They can sometimes be the cause of trouble in the whole process.
Are there any suitable alternatives to the CNC machining process?
CNC machines are suitable when it comes to the machining of different materials. But SNS machining is not always ideally used. This can be due to many factors, one of which might be the initial investment. Alternatives to CNC machining are used for the process of machining. These include but are not limited to:
3D printing
3D printing is an additive manufacturing process which means the metal is added around the design created for a part. Liquid molecules or powdered grains are added particle by particle around the 3D model produced using CAD. Digital data is gathered for the required part and is then used for additive manufacturing. The parts produced using 3D printing are precise.
Rapid Molding Process
Rapid or digital molding is also considered to be an alternative to CNC machining. This process also starts with the 3D model produced using CAD software. The part is then molded and machined in only a couple of days instead of a couple of weeks. The process is time-saving and cost-efficient.
What kinds of parts and components can be produced by CNC machining?
CNC machining has its applications in many industries. The type of parts and components that can be machined using CNC are
Fitting
Fittings are used to connect one part to another. CNC machining is used to produce precise parts. Any miscalculation can lead to weak connections and might even damage the connected parts as well. CNC machining is used to ensure no miscalculation happens.
Housings
Housings protect other parts from outer damages. Any faults in the housing can damage the part. For structurally correct parts, housings are made through CNC machining.
Ball joints
CNC machining is used to produce ball joints that are employed in metal parts to ensure their movement. CNC machining produces these parts for the movement of these parts to a certain angle.
Which industries utilize the CNC machining process?
CNC is just a simple acronym that is used to describe the process of computers programming the machines used in manufacturing. It includes many important steps of manufacturing including stamping, drilling, cutting, shaping metal, shaping plastic and wood and foam as well as other materials. CNC machinery ensures greater consistency and quality when it comes to precision.
CNC using industries have aligned their operations because of CNC and have become much more efficient at mass production of custom parts. There are special skills and training required to operate CNC machines and program them.
There are many industries that are benefitting from the manufacturing improvement created by CNC. Few of these industries are
- Aerospace
- Automotive parts manufacturing
- Medical machine manufacturing
- Transportation
- Defense
- Telecommunication
- Marine industries
- Electronics
CNC is best for enabling a great level of precision and accuracy in manufacturing parts and offers great tolerances for parts of all sizes. One of the great examples for companies using CNC would be Toyota Americas Corporation.
Video: Toyota Americas Corporation utilizing CNC Machining process
What challenges are faced in the CNC machining process when producing large parts and heavy components?
CNC machining comes with a lot of challenges when it comes to the larger parts. To help you understand the challenges better we have put together some common challenges in the CNC machining process.
Redesigning
This is one of the challenges because in CNC cutting the process is not the challenge but the preparations for it. Precisely, you have to make sure that the machinist and design engineers are all up to speed. Whenever a machinist receives a drawing, it is looked at to determine:
- If the part can be made
- How the part will be made
- What are the attributes that are important for the type of machine?
Irrespective of how detailed the drawing is but having a closer look can unveil those deficiencies in the drawings. The drawings must be made after proper research to avoid going back to it again.
Requiring more steps in the process
Larger parts are not easy to handle when it comes to machining. Every single inch of the part is to be machined when even the clamp is not supporting the part. CNC machining has proved its usability for smaller parts but larger parts are still not perfected using CNC.
Choice of materials
Choosing the right material is one of the most important parts when machining. You might think that every material is workable in the CNC machine. However, you may discover later that the material selected doesn’t work well with every machine not because of the machine but because of the quality of material and when that material is to be used in a larger part, its properties are more prominent. Larger parts are greatly affected due to the choice of material.
What CNC machining services are provided by Sunrise?
Sunrise Metal provides complete CNC machining solutions for different manufactured products. The machining services are provided not only for die casted parts but for solid extrusion, semi-solid casting, etc. Different CNC machining services are consolidated at Sunrise Metal.
Sunrise CNC lathing
CNC lathing services at Sunrise uses 3 & 4 axis CNC turning centers that are programmed to meet your requirements. Our turning machines produce high quality and cost-effective solutions by working with tough and high-temperature metals. Custom made parts through turning machines show reduced lead times and tight tolerances. Sunrise has in house facilities to manufacture parts with exceptional material compatibility.
Sunrise CNC milling
Sunrise provides advanced CNC milling services that involve milling machines ranging from 3- axes to 7 axes. The professionals are proficient in CAD and CAM designing and provide custom CNC milling solutions. Sunrise produces milled parts that are used in different industries like defense, medical equipment, and many more. It produces milled parts of precise structure and shape.
Sunrise CNC Machining services
Sunrise provides its services for every CNC operation. For this purpose, CNC machining centers are employed in the service centers of Sunrise. Machining centers from Haas multi-task and provides tools and elements that make Sunrise a stop shop for every client. Sunrise is equipped with advanced technology to make the process of machining faster and more efficient.
What is meant by CNC lathe machining? What is the difference between CNC machining and CNC lathe?
CNC Lathes are machines that are operated with Computer Numerical Control (CNC) system that offers precise design instruction for the machines. CNC Lathes are the type of machine in which the material or a part is clamped and rotated by the main spindle whereas the cutting tool that works on the material is moved in various axis and is mounted.
There are two types of CNC machines, CNC milling, and CNC lathe and there is a significant difference between the two.
In the CNC lathe machine, as explained above the job is mounted on the spindle for proper balancing. In the Lathe machine, the job has rotational motion and the tool only has linear motion. The tool moves forward and backward as well as up and down while the job only rotates.
However, in the milling machine, the job is not rotated but it does have a linear motion while the tool has a rotational motion. The job is mounted on the fixture on the axis while the tool is mounted on the spindle.
What is the difference between CNC machining and VMC machining?
CNC Machining
CNC is a type of motion control system which basically means that it doesn’t use cams or templates to cut parts but it is rather controlled by a computer. VMC is also a type of CNC machine and it is mainly enclosed and used for cutting materials basically. These are generally very precise and expensive machines. Here is a photo of the popular VMC machine that uses CNC protocols.
VMC Machining
There is no such difference in both these machines. it just means that one exists as a specific type to the other. The modern VMC machines are controlled by CNC. The CNC is mainly the computer and motion handling part of the machine. The rest is just spindle (known as cutting head) and frame. CNC technology is also used to control lasers, water jets, plasma cutters, saws, and 3D printers too.
What is the difference between CNC machining and PLC machining?
CNC Machining
CNC abbreviated for Computer Numerical Control is just an application that is used to control a multi-axis machine tool including milling machine or a lathe but it also could be a tube bending machine punch press or alike. The CNC controller is mainly a specific purpose controller that uses a microcomputer; however, it could be a general-purpose computer or even a PLC. Even before computers were readily available forerunner was NC and used solid-state logic, timers, relays, etc. to provide the application.
PLC Machining
A PLC abbreviated for Programmable Logic Controller is a general-purpose logic controller that was designed for allowing the users to make their own applications. The users select their appropriate I/O and function modules for tasks such as communications and multi-axis servo control as well as programming the PLC to perform the required tasks.
To conclude CNC is designed for very precise motion control and can make use of both CNC and PLC. CNC is best for motion control while the PLC is best for on/off type control.