Sunrise Die Cast Frame Components
Die-cast frame products at Sunrise are developed to deliver durability, strength, and efficiency in all types of projects.
Sunrise is involved in producing die-cast gears delivering optimum strength, and enhancing the frame’s power. The material being used in the production is selected carefully and strictly to expand possible applications.
Aluminum alloy has been a special in-demand option in the market because of its beneficial features and cost-effectiveness. Over the years, the die casting process has led to breakthroughs in the die casting frame parts.
Sunrise Aluminum Die Cast Frame Manufacturing Capability
With deploying advanced manufacturing technology, Sunrise Metal creates a highly versatile aluminum project box. Under the assistance of our skilled professionals, we develop and manufacture products ensuring its quality features such as durability and optimal quality.
All die cast frame products are tested and checked during the production and before shipping –all throughout the production process. Its dependability has been highly appreciated by our valued customers for their easy usage controls and superior performances.
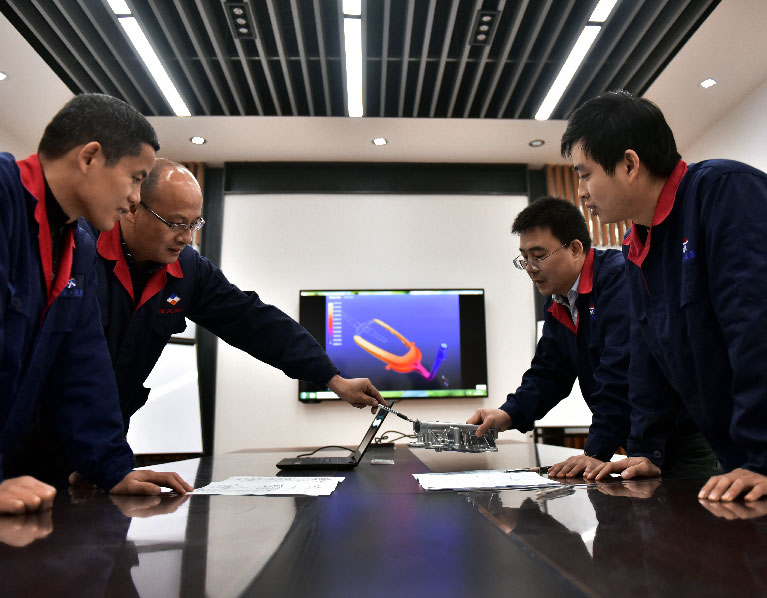
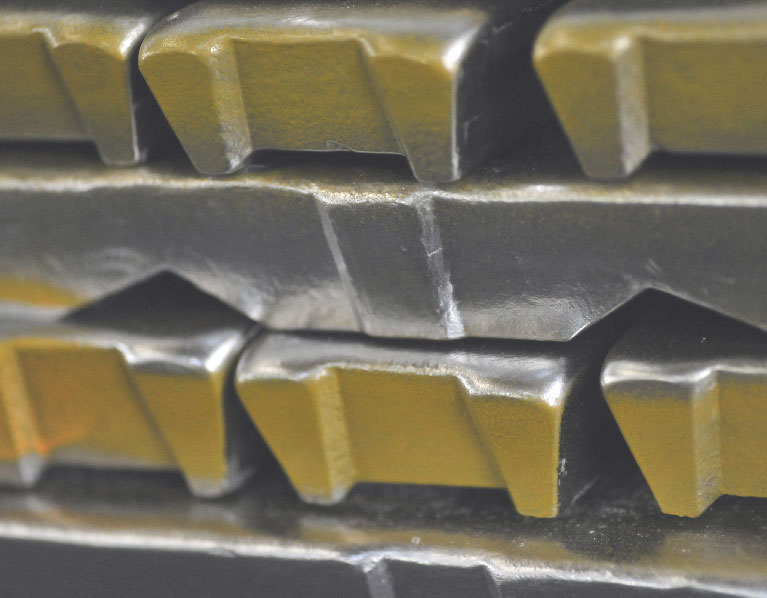
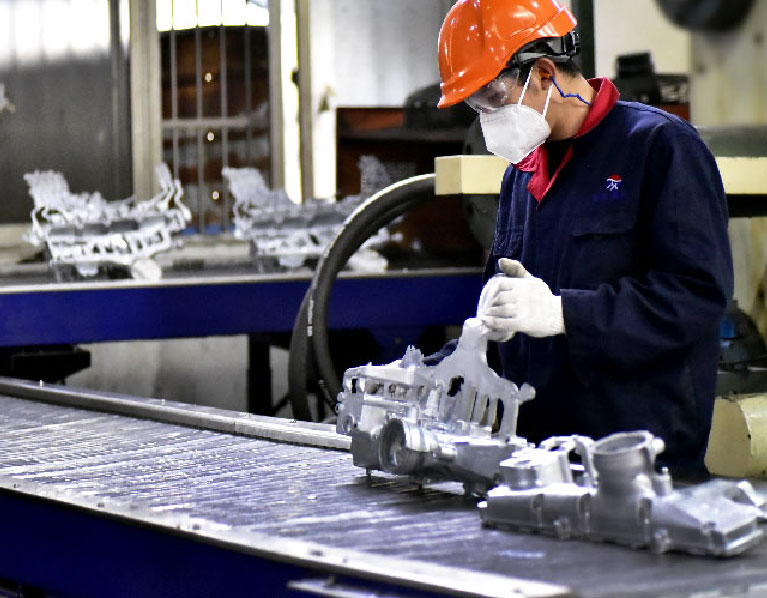
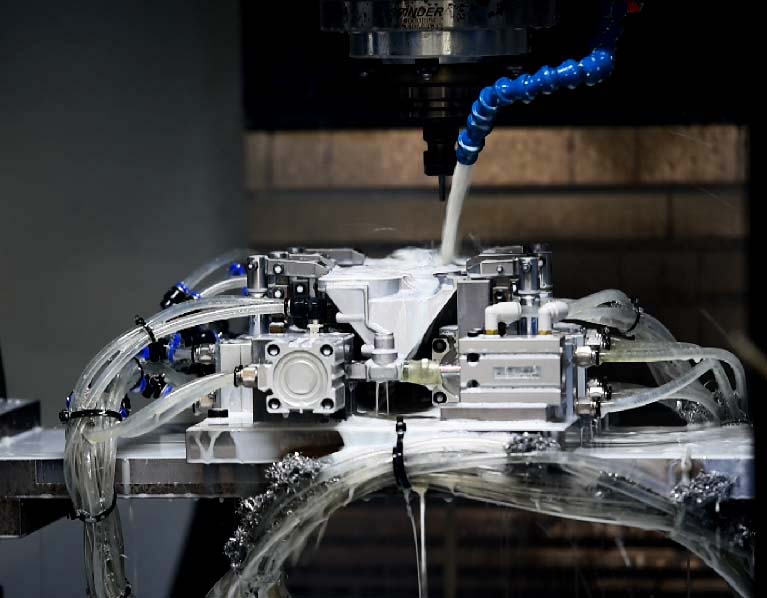
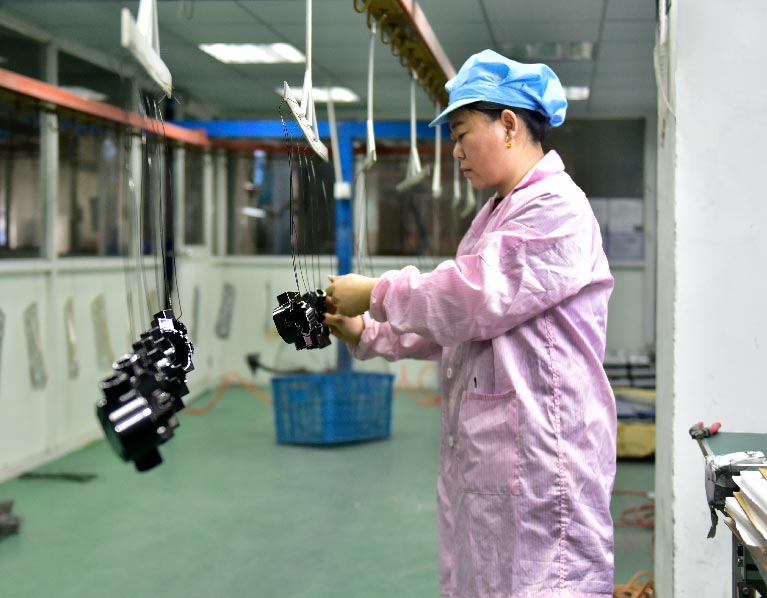
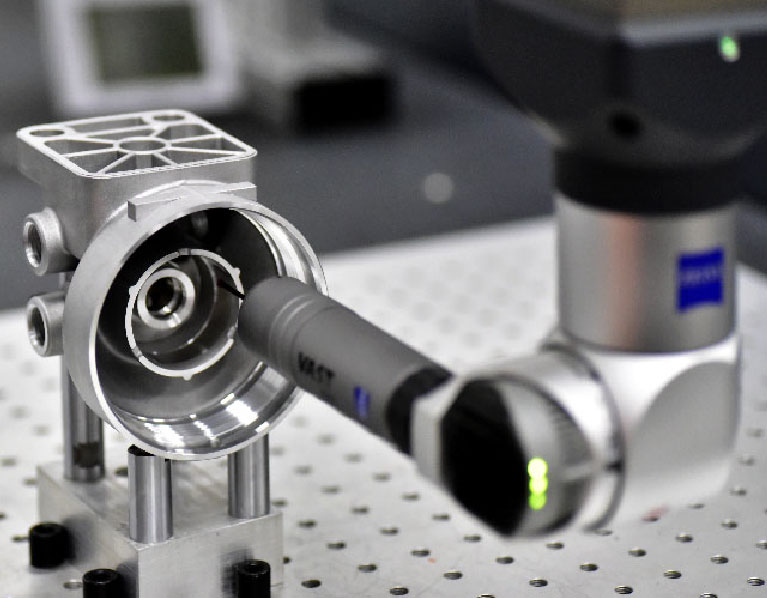
Advanced Equipment For Aluminum Die Casting Products
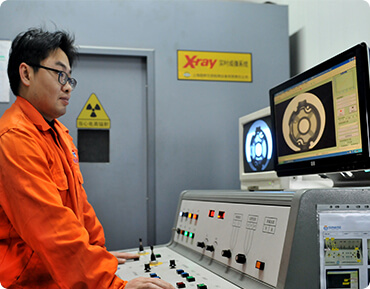
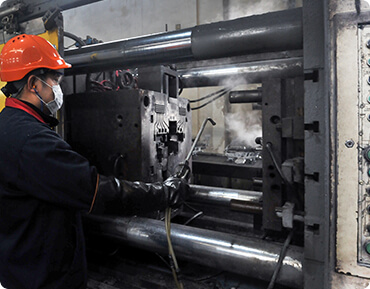
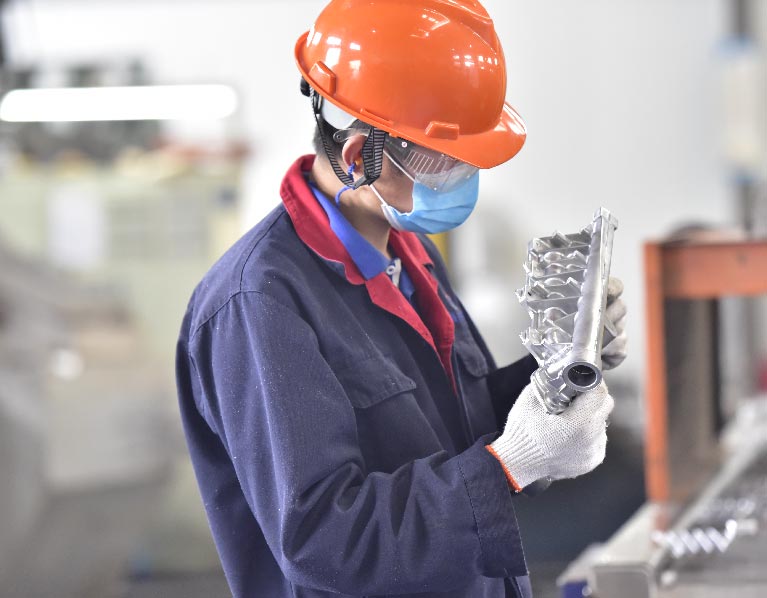
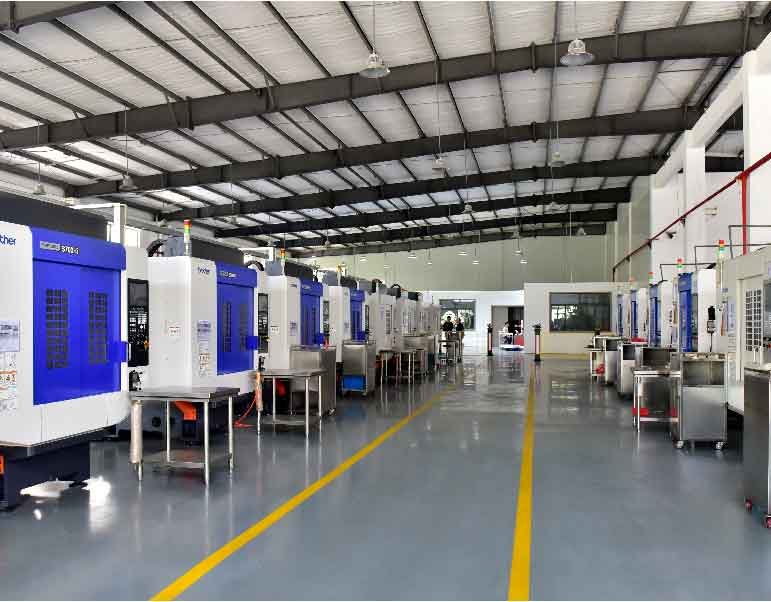
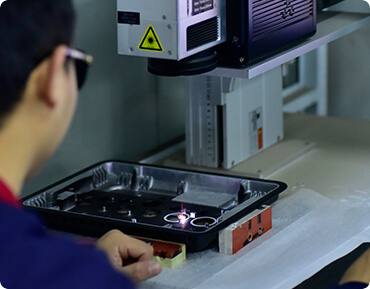
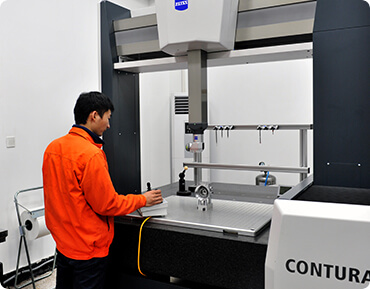
Recent Die Cast Frame Projects
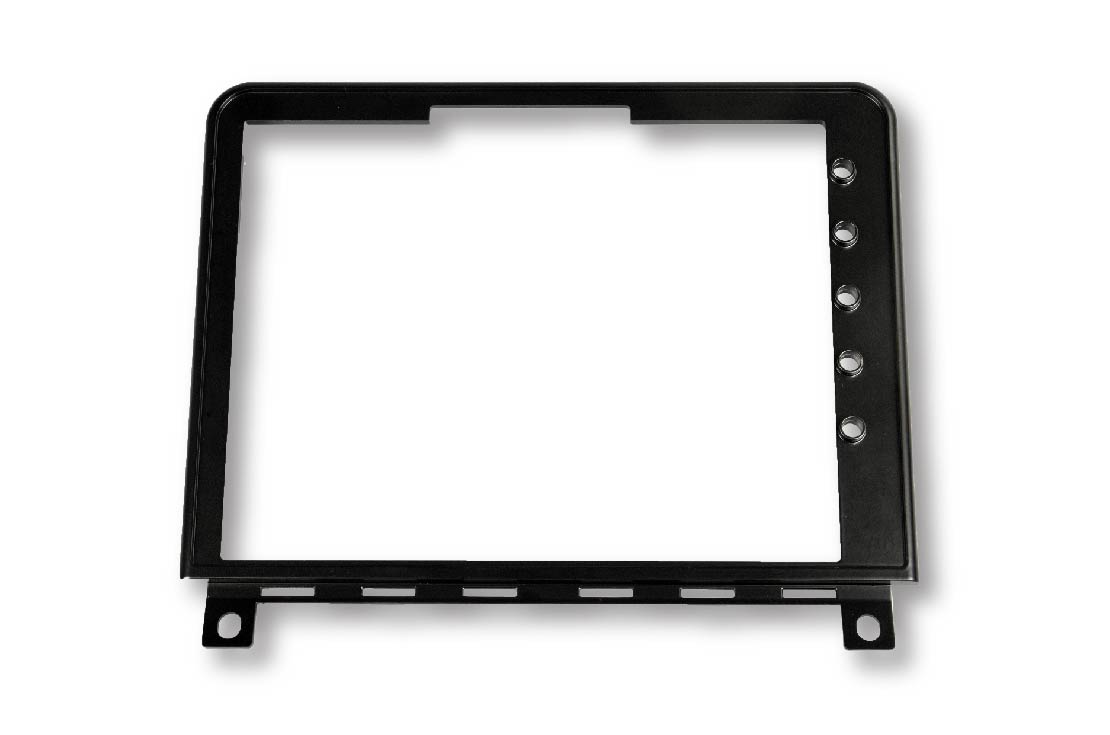
Part Name: Surface Frame
Material: AlSi12
Size: 292*244*22.5mm
Weight: 230g
Machine Tonnage: 400T
Surface Finish: Powder Coating
Production Process: Die Casting–Trimming–Deburring
–CNC Machining–Chromating–Powder Coating–Screening–Packaging
Applied Industry: MEDICAL
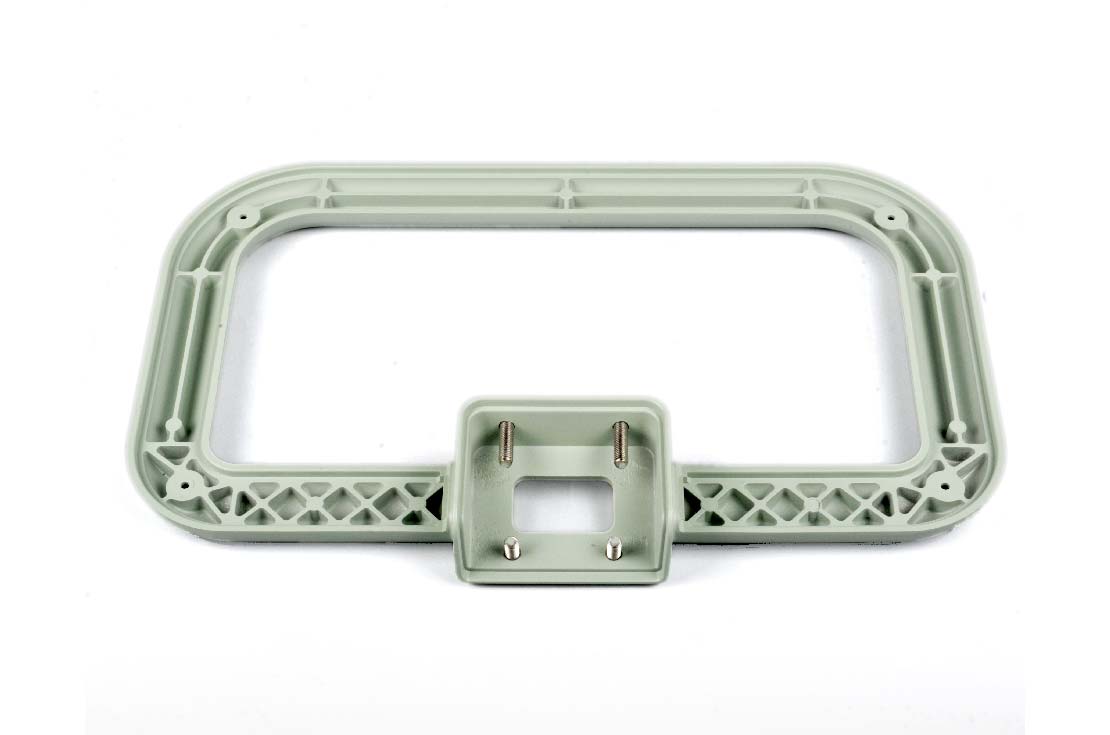
Part Name: Medical Frame
Material: AlSi12
Size: 357x222x44 mm
Weight: 773g
Machine Tonnage: 500T
Surface Finish: Chromating
Production Process: Die Casting–Trimming–Deburring
–CNC Machining–Assenbly–Powder Coating–Liquid Painting–Screening–Packaging
Applied Industry: Medical
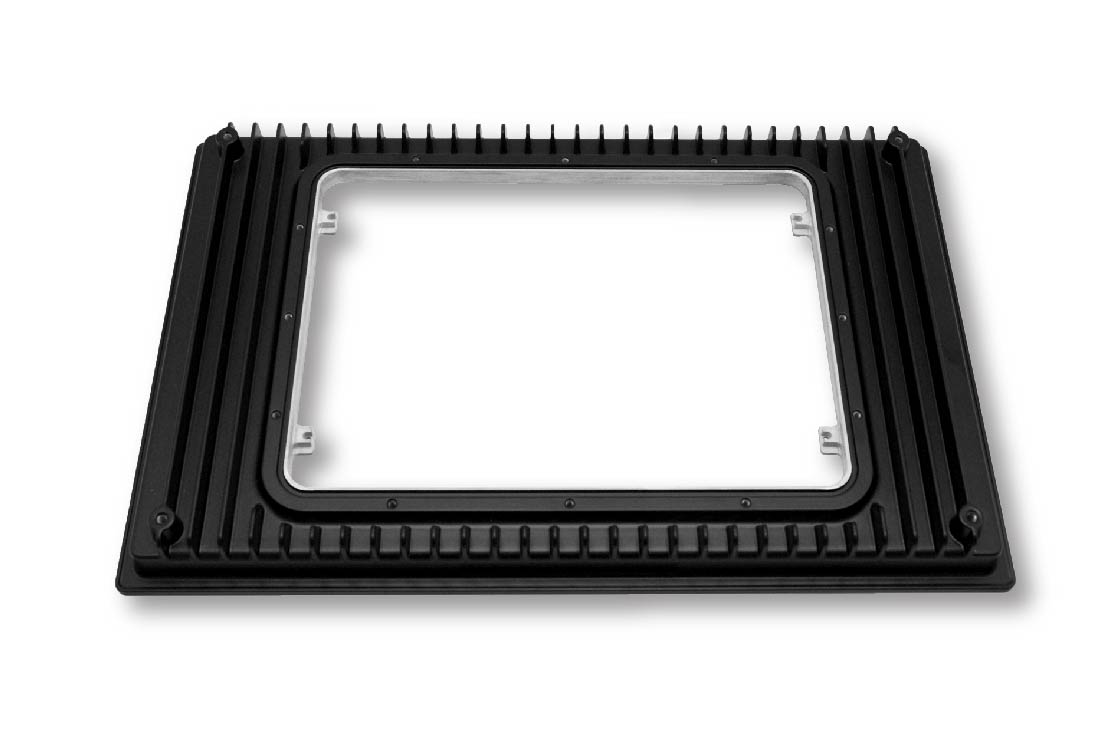
Part Name: Dispalyer Frame
Material: AlSi12
Size: 462*290*37 mm
Weight: 1480g
Machine Tonnage: 800T
Surface Finish: Chromating
Production Process: Die Casting–Trimming–Deburring
–CNC Machining–Chromating–Powder Coating–Screening–Packaging
Applied Industry: MARINE
DIE CAST FRAME:
THE ULTIMATE FAQ GUIDE
A die cast frame is a lightweight and strong component with a major cost advantage for manufacturers.
Sunrise Metal produces die cast frames using the best quality aluminum alloys for high durability and reliance. Applications of these high precision products are in the marine, electronic, housing, and automotive industries with a huge demand for die cast frames.
- What is a die cast frame?
- What are the applications of a die cast frame?
- What are the advantages of a die cast frame?
- What is the process behind the production of a die cast frame?
- What are the different die casting materials used to produce diecast frames?
- Why are aluminum alloys preferred in the production of die cast frames?
- What is the cost of producing a die cast frame? How can it be optimized?
- What are the main characteristics of a die cast frame?
- Why are die cast frames preferred over other types of frames (such as welded parts)?
- How do companies ensure the best design for a die cast frame?
- Are die cast frames durable and reliable for the long run?
- Are there any special surface treatments offered for diecast frames manufactured by Sunrise?
What is a die cast frame?
A die cast frame is one of the most useful parts created in the die casting process. The die casting is a process to manufacture dimensionally correct metal parts. The process is efficient and is taken up by many manufacturers. Die casting is often used to manufacture parts that are required to be lightweight and strong. Frames are the basic structure of any machinery. All the important parts are integrated into the frame to make up a complete component. Diecast frames are the most reliable for use. Industries are moving towards the improvement of frames in order to achieve a unibody structure and die casting is making it easier to do so.
What are the applications of a die cast frame?
Die casting is being used in many industries today and is expanding its uses on a daily basis. Diecast frames are the structure of any machinery or component. It is being applied in different industries today including marine, medical, electronic and automotive.
Automotive industry
The automotive industry is using die-casted frames as the supporting structure. Die-cast frames or chassis work as skeleton of the vehicle. Frames were once separate from the body of the automotive but die casting has introduced the casting of different parts within the structure or the frame. Unibody cars are being encouraged as they are also reducing the weight of the vehicles. Rather than welding different parts together, they are being cast together which is reducing the need for machining and is also producing stronger structures.
Medical equipment
The frames being used in the medical industry make use of die casting techniques. Different equipment required in the medical procedures is being die casted. The frames required for this equipment have to be durable and strong. Dental equipment, diagnostic equipment, surgical equipment, medical x-ray equipment, and even the equipment being used in the hospital wards for the feasibility of patients is using die casting technique in the production.
Marine Equipment
The marine engine parts are usually made through die casting. The frames required to develop compact equipment are also die casted. Marine engines require to die casting for their casings as they are supposed to work in the water too. Different machining processes are also applied to die cast frames in order to make the marine equipment work in a different environment.
What are the advantages of a die cast frame?
Die casting is used to manufacture frames of different components in different industries. This is due to the many benefits it provides.
• Die casted frames provide favorable strength properties.
• Such frames have low density and high machinability.
• They have high surface treatability.
• Die casted frames are spark free meaning they can also work in flammable environments. The frames are resistant to sparking.
• These frames have a near-net shape and are dimensionally correct.
• They have high electrical and thermal conductivity.
• The frames generated through die casting are highly productive and are highly automatable.
• They connect other parts of the whole set up more conveniently.
• They show improved thermal management.
• The produced component is light in weight but is durable.
• Overall cost of the production is reduced using the die-casted uniframes.
What is the process behind the production of a die cast frame?
Die cast frames are being manufactured with the aim of producing components of lower weights and higher strengths. Die casting plays a major role in the achievement of this goal.
Melting
The first step in the production of die cast frames is the melting of the alloy being used in manufacturing. The melting process should use the optimum melting solution. The machine being used should offer high metal quality after melting.
Transportation of molten metal
The transportation of molten metal from the melting chamber to the dosing chamber should be done carefully. The transport is one of the different factors that affect the quality of die casted frames. Safety is considered while transportation.
Dosing
Molten metal is then dosed into the molds of the frames. Dosing is carefully done in order to achieve a near-net shape of the frames. This should prevent oxides from forming inside the closed system. Metal is being fed to the machine which is then being dosed to the mold.
What are the different die casting materials used to produce diecast frames?
Die cast frames are produced using different non-ferrous metals to achieve efficient results depending upon each application.
Aluminum
Aluminum is becoming a priority in the industry as it provides electromobility among many other advantages. Aluminum and its alloys are used due to their low density and good castability. Frames are cast to achieve lower weights and aluminum best serves the purpose. So aluminum die casting manufacturing is the most popular process for die-cast frames.
Zinc
Zinc is also used by many manufacturers as a substitute for aluminum. Zinc is used where strength and hardness is the requirement while die casting frames. It has the capability of producing thin walls and producing stable frames. Highly complex frames can be die casted using zinc. Zinc die casted frames are a perfect alternative to machined and stamped components.
Copper
Copper is chosen by different manufacturers as it is cost-effective when it comes to the production of frames. Copper is also a better conductor of electricity than aluminum and zinc. Copper also avoids mold failure due to thermal fatigue.
Why are aluminum alloys preferred in the production of die cast frames?
Aluminum and its alloys are preferred over other metals due to certain benefits that it provides. Die cast frames are also manufactured using aluminum for these benefits.
Lightweight
Aluminum die casting frames are light in weight. This makes the component it is employed in lighter in weight as a whole. Many industries gain from this feature of aluminum, especially the automotive industry. This feature of aluminum helps in making the vehicle fuel efficiency and reducing Carbon dioxide emissions.
Finishing and machinability
The frames that are aluminum die casted have higher machinability. Any processes to be applied to frames are easy when the constituent component is aluminum. Aluminum also bears good finishing characteristics.
Stiffness
Aluminum is stiff in nature which also makes it more strong and durable. Frames die-casted using aluminum might be light in weight but they still provide the strength required to hold the components together.
What is the cost of producing a die cast frame? How can it be optimized?
Initial costs for the production of die cast frames are higher than other traditional processes. This is due to the machinery and the measures that are taken to make the process error-free. Since the method is more efficient than the other methods, it is more cost-efficient in the long run. The frames that are die casted have more strength and are more durable. This reduces the need of constant maintenance and hence costs regarding maintenance are reduced. The frames manufactured are also more productive.
To optimize the costs of the process, different techniques like simulation are used. This gives know-how of the frame to be manufactured. The end result can be seen virtually and the changes are made beforehand. This reduces the cost involved and the time to be invested.
The machinery being used in the production is also kept maintained. This reduces the chances of any errors or keeps impurities from the product. The cost for the process is optimized by keeping it all serviced.
What are the main characteristics of a die cast frame?
Die cast frames are the structure of any component. Different parts are placed in the frame to create one complete piece. It can also be defined as the outline of a setup. Die casted frames should show these characteristics
- They should be able to deal with the weight of the whole body and anything attached to it.
- The frame should be able to endure the outer forces that are to be employed on the complete component.
- It should not be impacted through sudden collisions and should hold together the complete assembly.
- It should have a tendency to join other parts with it.
- The frame should be machinable and nonsparkly.
- Any torque created inside the setup of the frame should be dealt with.
- The frame should provide support to the system.
- Die casted frames should be light in weight and should not affect the efficiency of the component as a whole.
Why are die cast frames preferred over other types of frames (such as welded parts)?
Die casted frames have proved their superiority over welded parts. Traditional manufacturing processes are not as advantageous as die casting for die casting provides these benefits.
- No distortion or heat affected areas. No stress is applied in manufacturing.
- Die casted frames are manufactured on the same pattern but other fabricated frames involve human error. They do not come out the same.
- More complex die casted frames are manufactured using die casting which is not possible using other traditional manufacturing processes.
- Die casted frames do not require the assembly work as compared to other processes that require the joining of each and every part after manufacturing.
- Die casting gives control to the designer of every single angle of the frame. The designer can decide the areas that need more material than the other. This also saves a lot of material and hence reduces waste.
- Some processes like welding also affect the frame’s overall structure. Stress in any dimension can cause an impact on the other sides. This is not the case in die casting.
- Die casted frames offer better machinability as compared to other processes.
How do companies ensure the best design for a die cast frame?
Die cast frame designs need a lot of research and study before manufacturing. The designer needs to calculate every angle before going into the production phase. Some of the many factors that are considered are:
Thickness
The thickness of the frame is to be calculated carefully. The frame has to be thick enough to endure any stress but should not add more weight and make the frame heavier. The thickness of the frame should be able to resist any pressure.
Space inside frame
While designing, one thing kept in mind is the room inside the frame. This is the space in which other remaining parts are placed. This space should be wide enough to take up all of the parts but not so wide as to increase the total surface area of the component. It should also be made as attractive as possible.
Foundation
The foundations of the frame are made strong as it is going to serve the purpose of supporting and enclosing the whole structure. It should be compact.
Are die cast frames durable and reliable for the long run?
Die casting is a process that creates durable components. This process creates durable, reliable, and accurate frames. The frames are built through careful considerations. Die casting can produce even complex parts and near net shapes.
This makes them strong enough. The reliability and durability depend upon the material being used in the manufacturing of frames.
When comparing the metals, aluminum is proved to be more suitable for the die casting of frames. Aluminum and its alloys provide more advantages which are prioritized by manufacturers- reliability and durability are two of them.
The metal also provides better machinability and low maintenance requirement which also shows that frames produced using aluminum alloys are more reliable in the long run. Other metals like zinc, copper, and brass also produce reliable frames. Manufacturers choose one of these metals to achieve the required results.
Are there any special surface treatments offered for diecast frames manufactured by Sunrise?
Sunrise Metals has been working to manufacture reliable products using different methods such as CNC machining, rapid prototyping and precision die casting. It also specializes in the manufacturing of die casted frames. The die-casted frames are then treated through certain processes.
Plating
Sunrise uses the process of plating on metal frames. This is out by covering the surface of the frame with a metal that is deposited all over it.
Chromating
The technique of chromating is used by Sunrise to make the die casted frame more reliable and to make it more corrosion resistant. An oxide layer is placed over the frame which makes the metal frame react with the oxide layer. The chromate is formulated over the surface and saves it from any other reactions.
Liquid painting
Liquid paint is applied on the die casted frame surface. A spray or pressurized vessel evenly distributes the paint all over the surface. Sunrise uses this technique in order to increase the life of the die casted frame.
Powder coating
Powder coating is a dry finishing process that involves the use of finely ground pigment particles Electrostatically charged particles are sprayed on to the component parts and that are electrically grounded before the process. A uniform coating forms as a result and leads to the high durability of all parts.