ZINC ALLOY ZAMAK 2
Zamak/Zamac is an alloy of Zinc consisting of Aluminum, Magnesium, and Copper as the primary alloying elements. Zamak 2 is also known as ASTM AC43A, ZnAl4Cu3, or Kirksite. It has the highest hardness, and strength out of all Zamak series alloys. Let’s have a look at its properties, applications, and advantages.
Zamak 2 Characteristics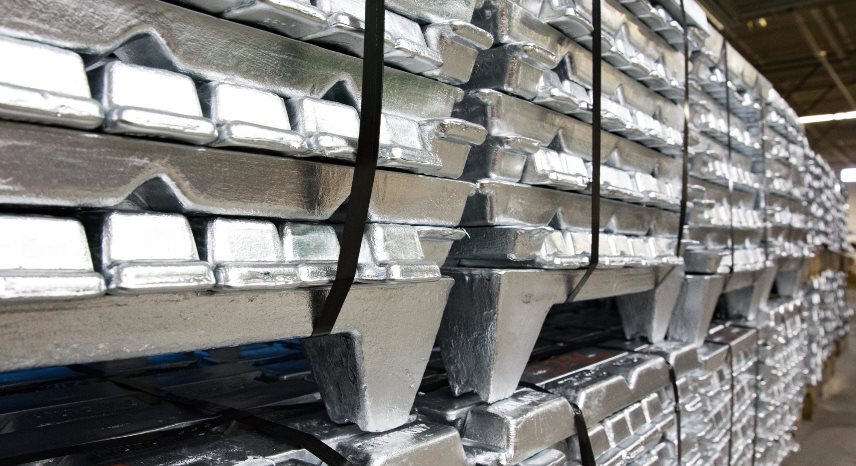
Zamak 2 has a high copper content (2.5-3%) in it which contributes to its excellent mechanical properties and creep performance over the long term. It has a low melting point and can be cast using a hot chamber machine. The alloy has excellent resistance to hot cracking and good cold defects.
Moreover, it has great vibration attenuation and damping capacity. It can absorb shocks from impacts much better than other metal alloys. The alloy also exhibits good corrosion resistance and can be machined, polished, anodized, chemical coated, or electroplated with ease. Therefore, the post-processing of castings can be carried out conveniently.
Advantages
Zamak 2 offers some exclusive benefits compared to other die casting metals and Zamak alloys. Which include,
- Great vibration attenuation and damping capacity
- Better wear and corrosion resistance
- Retains hardness and high strength after long-term use
- The effect of creep is less than other Zamak alloys
- Castings are recyclable
- Longer die life
Applications
Zamak 2 is suitable for the production of small diecast components. Industries requiring small components have a large demand for Zamak 2 alloy parts. The automobile industry uses it for casting Interior parts, gears, door handles, brake paddle, etc of a vehicle.
A wide range of applications can be noticed in home appliances or furniture. Door hinges, knobs, locks, handles, lighting fixtures, washroom faucets, valves, etc. often use Zamak 2 alloy parts.
Mechanical Properties
Parameters | Value |
Brinell Hardness | 100 HB |
Ultimate Tensile Strength | 359 MPa |
Yield Strength (0.2%) | 283 MPa |
Shear Strength | 317 MPa |
Compressive Strength | 641 MPa |
Fatigue Strength | 58.6 MPa |
Impact Strength | 47.5 J |
Elongation | 7 % in 50mm |
Physical Properties
Parameters | Value |
Melting Range | 379-390 °C |
Density | 6.60 g/cm³ |
Electrical Conductivity | 25 % IACS |
Thermal Conductivity | 104.7 W/mK |
Specific Heat Capacity | 419 J/kg-°C |
Coefficient of Thermal Expansion | 27.8 µm/m°K |
Poisson’s Ratio | 0.30 |
Alloy Composition
Contents | Value |
Zinc (Zn) | Balance |
Aluminum (Al) | 3.9-4.3 % |
Copper (Cu) | 2.7-3.3 % |
Magnesium (Mg) | 0.025-0.05 % |
Iron (Fe) | 0.035 % (max) |
Lead (Pb) | 0.004 % (max) |
Cadmium (Cd) | 0.003 % (max) |
Tin (Sn) | 0.0015 % (max) |
Zamak 2 vs Other Zamak Alloys
A qualitative comparison of the characteristics of Zamak 2 alloy against the other Zamak family alloys has been shown below.
Characteristics | Zamak 2 | Zamak 3 | Zamak 5 | Zamak 7 |
Dimensional Accuracy | Average | Very Good | Very Good | Excellent |
Dimensional Stability | Very Good | Good | Good | Very Good |
Corrosion Resistance | Very Good | Good | Good | Very Good |
Casting Ease | Excellent | Excellent | Excellent | Excellent |
Pressure Tightness | Good | Excellent | Very Good | Excellent |
Part Complexity | Excellent | Excellent | Excellent | Excellent |
Resistance to Hot Cracking | Excellent | Excellent | Very Good | Excellent |
Resistance to Cold Defects | Very Good | Very Good | Very Good | Excellent |
Surface Finishing Ease & Quality | Excellent | Excellent | Excellent | Excellent |
Machining Ease & Quality | Excellent | Excellent | Excellent | Excellent |
*Here, A grading scale of Excellent, Very Good, Good, Average, and Poor has been used to show the comparison. None of the Zamak alloys have any characteristics that can be regarded as poor.
Sunrise Metal is an expert zinc die casting manufacturer with a wide range of choices for Zinc alloys including Zamak 2. If you need any help choosing the right Zinc alloy for your product, you can contact our experts for assistance.