ZINC ALLOY ZAMAK 3
Zamak 3 is also known as Zinc alloy 3, ZnAl4, or ASTM AG40A. More than 70% of die casters in North America use Zamak 3 alloy for zinc die casting. It has balanced material properties and serves as the standard or reference alloy for rating other Zamak series alloys.
Zamak 3 Characteristics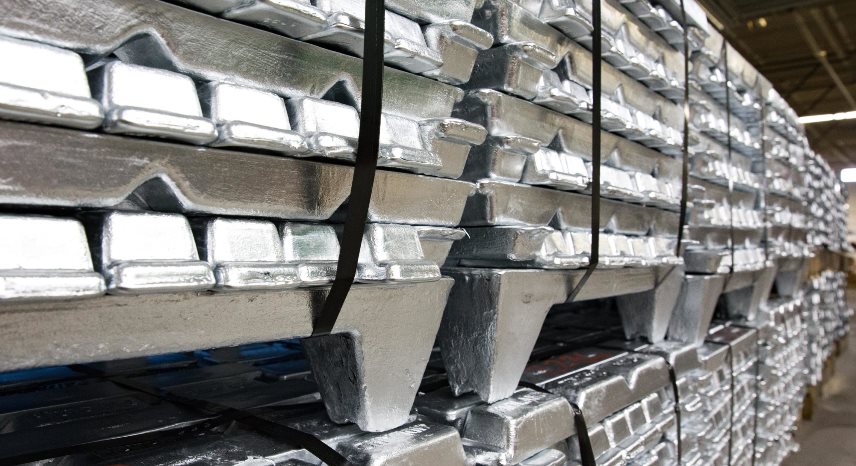
Zamak 3 alloy requires hot chamber equipment for casting. It offers a great combination of ductility, strength, plating, and finishing characteristics. The nominal composition of Zamak 3 alloy includes 96% Zinc and 4% Aluminum.
Zamak 3 alloy has excellent castability and exhibits better dimensional stability in the long run. It has lower tensile strength than Zamak 2 but is more resistant to corrosion and has better impact strength. Also, the impact strength and elongation at fracture increase as the alloy ages.
Advantages
Zamak 3 has multitudes of benefits including,
- Good fluidity properties that contribute to its castability
- Parts with Intricate shapes and thin walls can be easily cast
- Has balanced material properties
- Supports a wide range of surface treatments such as chromate, painting, plating, etc.
- Exhibits excellent damping properties at elevated temperatures
- The vibration attenuation property is also great compared to aluminum alloys
- Parts can be recycled
Applications
The balanced material properties of the alloy make it ideal for most of the common die-casting applications. Some typical applications include automotive components, furniture accessories, home decoration parts, washroom fittings, lighting fixtures, etc.
Mechanical Properties
Parameters | Value |
Ultimate Tensile Strength | 283 MPa |
Yield Strength (0.2%) | 221 MPa |
Brinell Hardness | 82 HB |
Shear Strength | 214 MPa |
Compressive Strength | 414 MPa |
Impact Strength | 58 J |
Fatigue Strength | 47.6 MPa |
Young’s Elasticity | 96 GPa |
Elongation | 10 % in 50mm |
Physical Properties
Parameters | Value |
Melting Range | 381-387 °C |
Density | 6.60 g/cm³ |
Electrical Conductivity | 27 % IACS |
Thermal Conductivity | 113 W/mK |
Coefficient of Thermal Expansion | 27.4 µm/m°K |
Specific Heat Capacity | 419 J/kg-°C |
Poisson’s Ratio | 0.30 |
Alloy Composition
Contents | Value |
Zinc (Zn) | Balance |
Aluminum (Al) | 3.9-4.3 % |
Copper (Cu) | 0.10 % (max) |
Iron (Fe) | 0.035 % (max) |
Magnesium (Mg) | 0.03-0.06 % |
Lead (Pb) | 0.004 % (max) |
Cadmium (Cd) | 0.003 % (max) |
Tin (Sn) | 0.0015 % (max) |
For the most part, it should be your choice of alloy for zinc die casting. But, if you have any special requirements for your parts, you can opt for other Zamak alloys. Each has slightly different characteristics to perfectly fit your needs.
If you are not sure which Zinc alloy to choose for your project, you can reach out to our experts for assistance. We are a Zinc die casting manufacturer in China with more than 10 years of experience in the industry.