Sunrise Die Cast Gear Components
Sunrise die casting gears are developed to increase the performance, durability, and efficiency. We are involved in manufacturing die cast gears delivering optimum strength which enhances the gear power and effectiveness.
The casted gears’ quality is being checked and tested during the whole production. Considering various quality parameters we make sure the component meets the required standard.
Die cast gear is processed to new technologically tested machinery and tooling which makes fast production time. We are a well-known reliable premier company of high-quality units. We manufacture output in the most efficient manner. Under the supervision of our professional staff, we manage to develop a large scale of high performance. Looking learn more about aluminum die casting.
Sunrise Die Cast Gears Manufacturing Capability
In Sunrise, we ensure high-quality production of a wide variety of die-cast gears available in different sizes, shapes. We offer visually appealing designs and parts with a long-serving life to suit industries’ needs. The production process of die casting gears is executed utilizing advanced technology and high-grade aluminum material. The whole process is being monitored rigorously. These will assure you smooth production run with the whole production cycle. High-quality, competitive cost and timely delivered shipment is our objective.
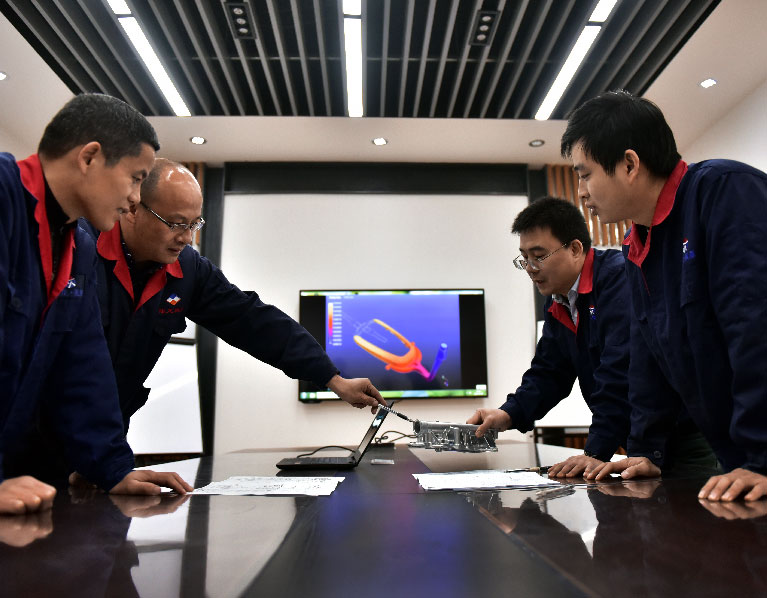
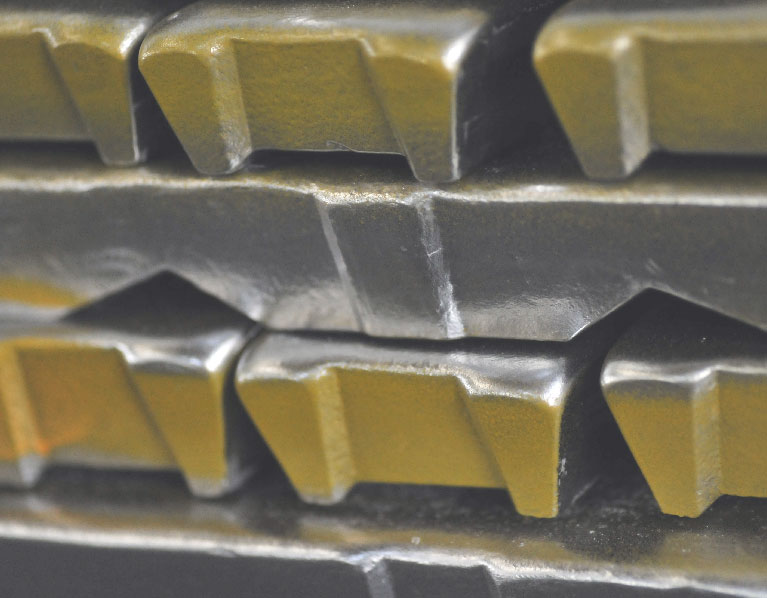
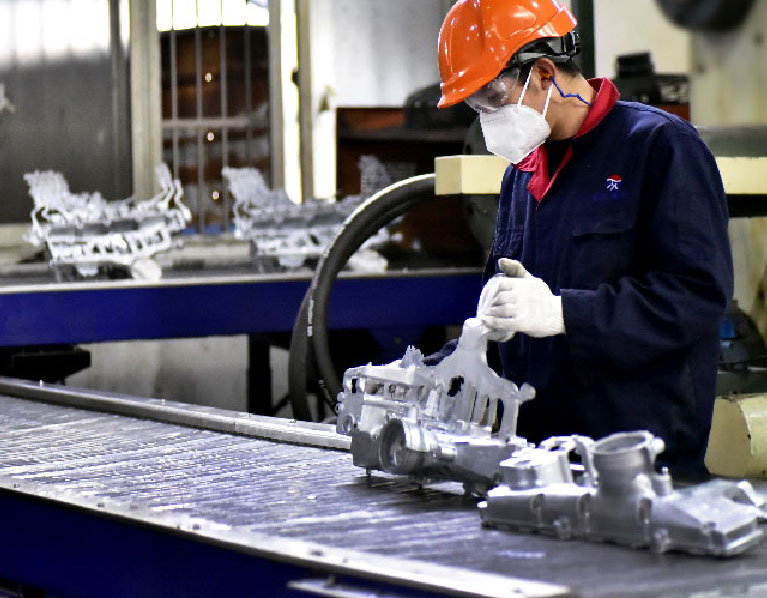
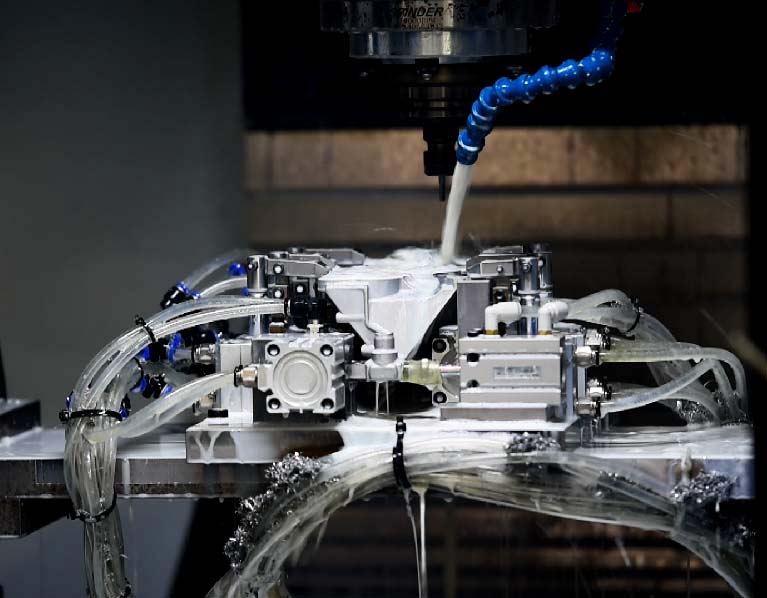
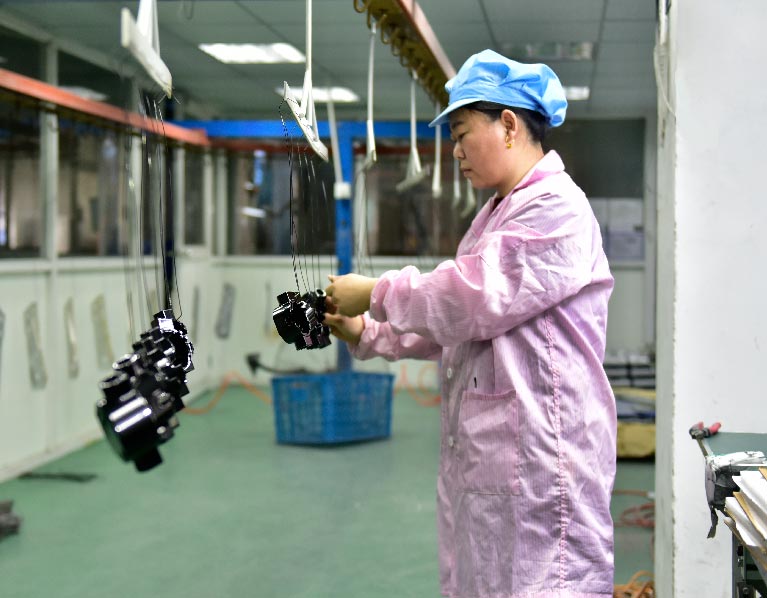
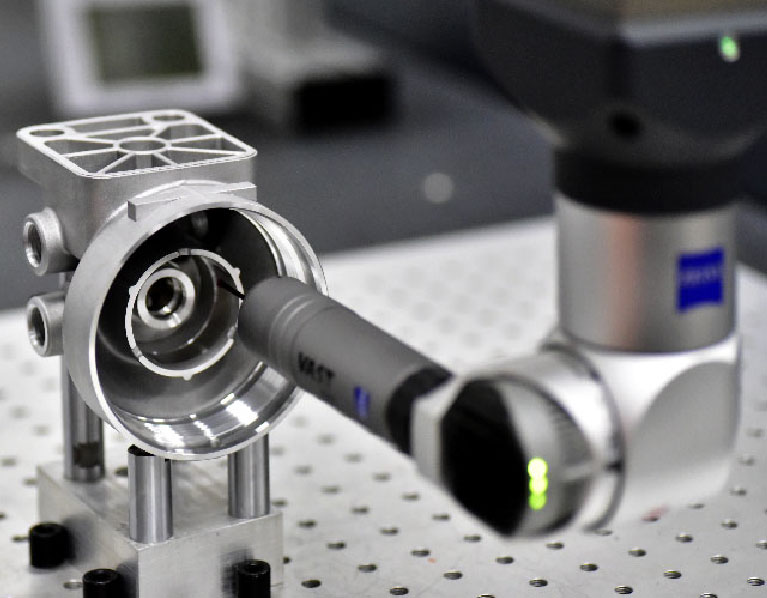
Advanced Equipment For Die Cast Gears Components
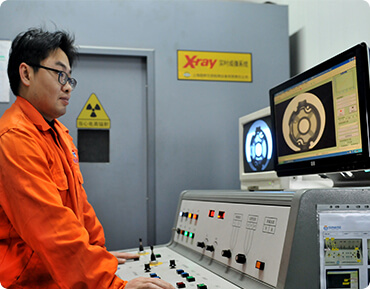
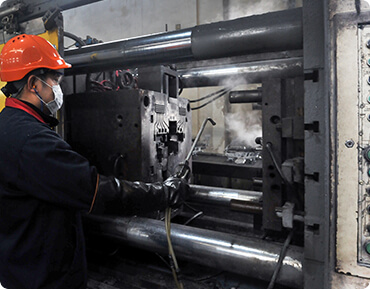
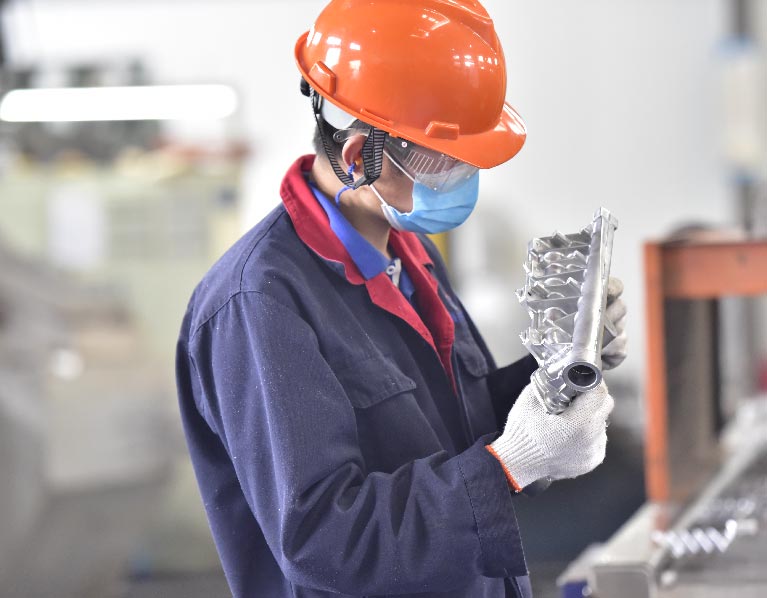
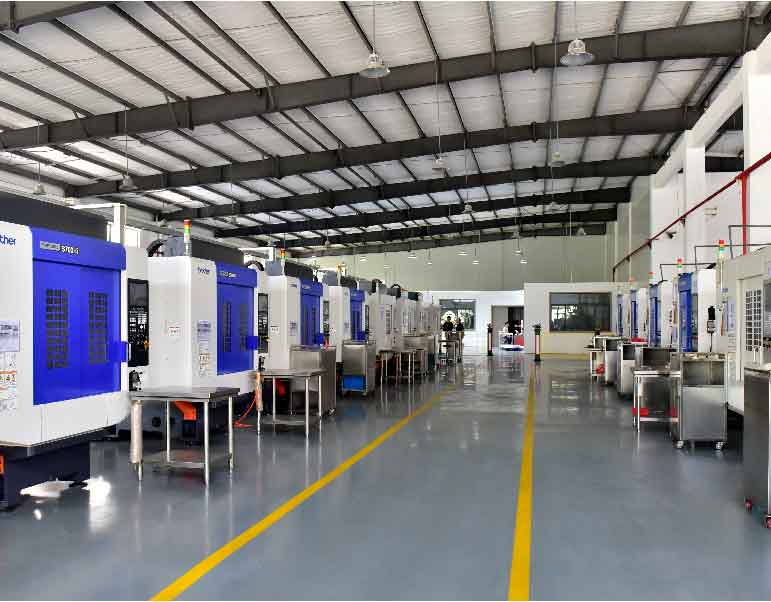
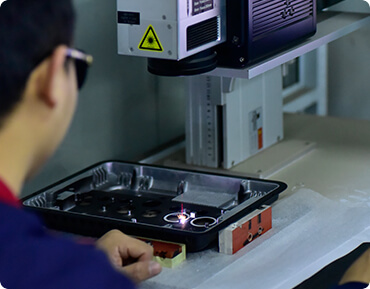
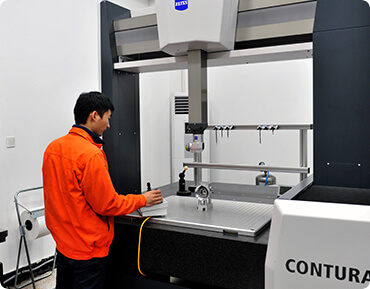
Recent Die Cast Gears Projects
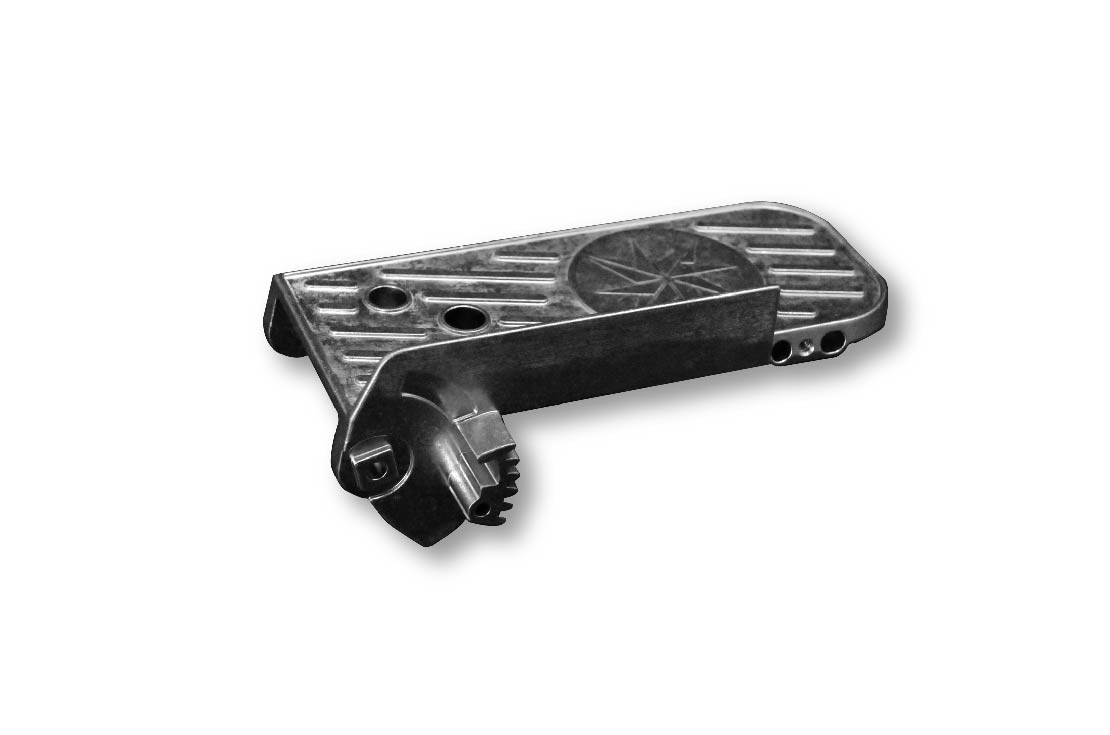
Part Name: Pedal
Material: A380
Size: 232×116.x91mm
Weight: 515g
Machine Tonnage: 280T
Surface Finish: Shot blasting
Production Process: Die Casting–Trimming–Deburring-
–CNC Machining–Chromate–Packaging
Applied Industry: Marine
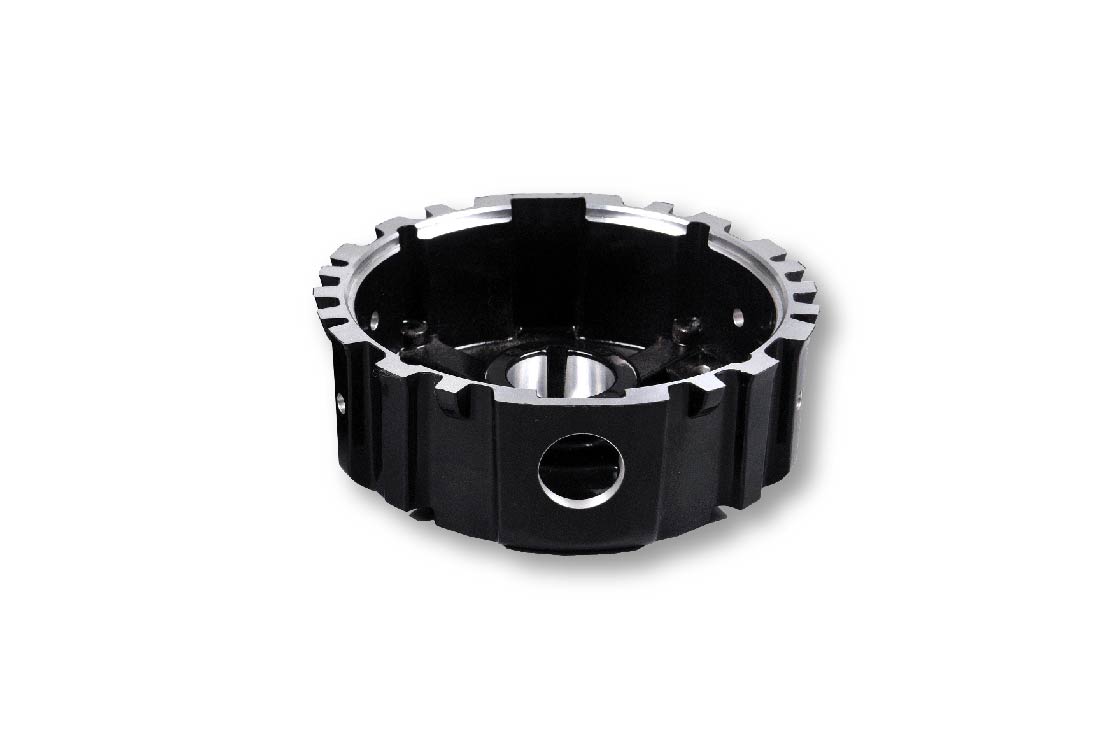
Part Name: Motor Cover
Material: ADC12
Size: 101x100x35mm
Weight: 198g
Machine Tonnage: 160T
Surface Finish: Chromating
Production Process: Die Casting–Trimming–Deburring
–Shot Blasting–CNC Machining–E-coating–Chromating–Powder Coating–CNC Machining–Screening–Packaging.
Applied Industry: General(Electric Motor)
DIE CAST GEARS: THE ULTIMATE FAQ GUIDE
Die casting is the most feasible and economic method for mass production of Gears. That’s why the leading industries prefer Die Casting for producing gears. Sunrise Metal has advanced die casting facilities and we can ensure high-quality gears for your company.
We tried to cover most of the basic queries about die cast gears. If you have any other questions in mind you can always contact our customer support.
- What are Die Cast Gears?
- What is the manufacturing process of Die Cast Gears?
- What are the advantages of Die Cast Gears?
- What are the applications of Die Cast Gears?
- What materials are suitable for Die Cast Gears?
- What are the features of Aluminum Die Cast Gears?
- What experience do you have in manufacturing Die Cast Gears?
- Can I give heat treatment to Die Cast Gears?
- Can you design the Die Cast Gears model for me?
- How do you ensure the Die Cast Gears quality at Sunrise Metal?
- What is your production capacity for Die Cast Gears?
- Why should I choose Sunrise Metal for Die Cast Gears?
What are Die Cast Gears?
Die Cast Gear is the mechanical housing that holds together the mechanical gear setup known as the gearbox. It is often termed as Gear case or housing as well. They are mostly used as a part of the transmission of vehicles.
Gears can be really complex and machining all of them can be expensive. But most casting methods are not suitable for manufacturing gears. Die Casting is probably the most viable solution for mass-producing gears.
That’s why Sunrise Metal puts their trust in die casting for manufacturing mechanical gears. You can always expect to get precise and durable die-cast parts.
What is the manufacturing process of Die Cast Gears?
The Manufacturing of Die Cast Gears is explained below step by step.
Modeling
In order to die cast your gears, you need to have a 3d model ready. Use a Computer-Aided Design (CAD) software for modeling your gears.
Once you are done with modeling it has to be optimized for tooling. The Design for Manufacturing (DFM) is required for tooling the die casting mold known as die.
Tooling
Once the DFM is ready you can proceed with tooling your dies. That is mainly done by CNC Machining, which is a computer-controlled method for machining parts.
Casting
Melt your desired materials under high temperature until they reach a workable state. Then pour the molten material in the shot cylinder, where it will be pushed into the die cavity under high pressure. Then allow the casting to cool down and solidify.
Post-Casting Operations
Once it is solid, take apart the dies and remove the casting. Eliminate any casting defects and remove excess metal, or provide special features in the Die Cast Gear by Trimming, Deburring, Shot Blasting, and CNC Machining.
Once the casting is complete, you can choose to apply additional surface finishes for your gears. Usually, the Die Cast Gears are given a Chromating Surface finish.
What are the advantages of Die Cast Gears?
Die Casting has many features that make it a favorable option for manufacturing Gears. The advantages of Die Cast Gears are as follows,
Tight Tolerances
This is true for almost any die casting materials. The die casting in general can produce parts with very fine precision. This is due to the fact that the die cast tooling is done using CNC Machining. That’s why Die Cast Gears has excellent precision.
Short Lead Time
The main advantage of die casting is that even the most complex Gears can be manufactured with almost the same amount of effort and time. Except for the one-time initial tooling, the rest of the operations in die casting take a very short time.
Smooth Surface Finish
Die Cast Gears really have smooth surface finish. You can even leave it with its default surface finish after casting. Die Cast Gears can be given with different types of surface treatment very easily.
Supports Thin-Walls
Thin-walls can be easily provided in Die Casting. Because die casting has very tight tolerances and High-pressure vacuum assisted die casting operations ensures the integrity of the whole casting. The provision of Thin-walls allows manufacturers to make lighter Die Cast Gears.
That should clarify the fact why Die Cast Gears are so popular. Sunrise Metal always chooses the best and that’s why it focuses on Die Casting for manufacturing gears with high-precision and durability.
What are the applications of Die Cast Gears?
Die Cast Gears are mainly used in the automobiles and Aerospace industry. The demand for gears is increasing and the companies are always looking for a better and cost-effective solution to meet the demands.
Machines that have rotary components usually need Gears for protecting the internal gearbox and containing the liquid. So, Die Cast Gears are used in all-wheel is driven vehicles and moving equipment.
What materials are suitable for Die Cast Gears?
Die Cast Gears are mainly produced from non-ferrous metals. There hasn’t been any reliable technology yet that can die-cast ferrous metals properly.
The suitable metals for Die Cast Gears are,
- Aluminum
- Magnesium
- Zinc
- Brass etc.
Although these materials can be used for die casting, Gears require metals with good mechanical strength. For that reason, Aluminum Die Casting is a preferred choice for the manufacturing of Die Cast Gears.
Normally, Aluminum is not as strong and durable as ferrous metals such as Iron. But there are different Aluminum alloys that have very superior mechanical properties.
What are the features of Aluminum Die Cast Gears?
Aluminum Die Cast Gears have more or less become an industry standard. Manufacturers are switching to Aluminum as a better option due to the tons of features it can offer. Let’s have a look at the features,
Lightweight
One of the best things about Aluminum Die Cast Gears is that they are almost three times lighter than Gear cases made with Iron. This is especially important for the Automobiles and Aerospace industry.
The weight of parts is very crucial for airplanes and they are also closely linked with fuel consumption. This is a reason why manufacturers need lighter parts for vehicles and most importantly for airplanes.
Strong and Durable
Certain varieties of Aluminum alloy are used for the production of Die Cast Gears. Aluminum has great mechanical strength compared to the weight. It also has great corrosion resistance and is able to sustain in harsh conditions.
Excellent Material Properties
Aluminum has great thermal and electrical conductivity. That makes Aluminum a great choice for Die Cast Gears. Because the gearbox inside the Gears generates a massive amount of heat. Aluminum’s inherent superior thermal properties make it a perfect fit.
Economical
Aluminum is simply one of the cheapest metals available. Compared to the mechanical and material properties of other materials it provides far more superior performance. So, strong and durable gears can be manufactured at a lower cost.
We hope it gave you a good idea of why Aluminum is becoming more and more popular. That’s why Sunrise Metal focuses entirely on Aluminum Die Casting in order to provide High-Quality Gears to the customers at a reasonable price.
What experience do you have in manufacturing Die Cast Gears?
Sunrise Metal has been in the die casting business for more than 10 years. And we have successfully manufactured a good number of Die Cast Gears for many automobile companies till now.
We mainly focus on Aluminum die casting. We have produced some remarkable die-cast gears using ADC12 Aluminum Alloy. Here’s a sample of two engine housing weighing 7300g and 6000g. They were both cast using a 2500 tonnage machine.
Can I give heat treatment to Die Cast Gears?
In normal conditions, No. It’s not like you can’t, but you wouldn’t. Giving Heat treatment to Die Cast Gears can result in surface blisters. Because the die casting process usually leaves pores inside the casting.
But, here at Sunrise Metal, we have advanced die casting facilities to ensure you almost pore-free Die Cast Gears. You can then heat treat them using some special guidelines.
Although, heat-treating your Die Cast Gears is usually not needed unless you have very high strength requirements and need to alter some properties. Aluminum Die Cast Gears already has excellent strength and desirable material properties.
Can you design the Die Cast Gears model for me?
Yes! We can help you design or even design the Die Cast Gears model for you.
We have talented engineers who entirely focuses on designing. The vast experience on the subject allows them to choose the best design considerations and give cost-saving suggestions as well.
If you don’t have a design ready, we can help you design the model and prepare the Design for Manufacturing too. So, you don’t have to worry about any design issues. We can help you at every step of manufacturing the Die Cast Gears.
How do you ensure the Die Cast Gears quality at Sunrise Metal?
Sunrise Metal will ensure you top-notch Die Cast Gears with our excellent quality control measures and advanced QA Test equipment. Here are some of our achievements and capabilities that add credibility to our claims.
Latest QA Test Equipment
We have the latest QA test equipment in our shop for quality control of Die Cast Gears in every step of manufacturing. Our QA test equipment such as X-Ray Detector, Cleanliness Tester, ZEISS CMM, Digital Caliper, etc. can ensure the quality of your gears from tooling to finishing.
Talented Quality Control Team
We entrust the quality control to vastly experienced and well-educated professionals. They will make sure you get what you paid for. So, be sure to get premium quality control for your Die Cast Gears.
Certified by ISO 9001 & IATF 16949
The ISO 9001 & IATF 16949 certifications are given to a company only when they can pass some quality control parameters. We are proud to declare that, we have achieved both of these certifications for our strict quality control and superior management.
So, quality assurance is the least of your concern. We aim to serve our customers with the best of our abilities.
What is your production capacity for Die Cast Gears?
Sunrise focuses on High mix, Low Volume production of die-cast parts. We will accept any small to medium die casting requests from our customers. We can take orders of up to 5000 Die Cast Gears.
you can count on us for a small number of high mix Die Cast Gears; Because big suppliers aren’t interested in low volume orders and small suppliers can’t maintain quality for your parts.
Sunrise Metal accepts orders for Die Cast Gears as low as 100 pcs. So, small or big, any company can benefit from our advanced Die Cast Gear Manufacturing capabilities.
Why should I choose Sunrise Metal for Die Cast Gears?
Sunrise metal is equipped with advanced Aluminum to die casting facilities. We can provide you the best solution for Die Cast Gears manufacturing. We have,
Advanced Equipment
We have a wide range of Die casting Machines, and CNC machines available here at Sunrise Metal. So, we are capable of getting even the critical most job done and manufacture high-quality Die Cast Gears.
Half of the project lead time
We use the latest technology and equipment that can potentially cut the production time by half. Our fast solution will ensure that you get delivery of your Die Cast Gears on-time and stay ahead of your schedule.
One-Stop Solution
We have 4 dedicated facilities to provide you a one-stop solution. Besides Aluminum Die Casting facilities, we have in house Rapid Prototyping, Die Casting Tooling, CNC Machining, and various Surface Finishing service available.
Certified for Quality Control
We are a certified ISO 9001 & IATF 16949 manufacturer. We claimed the title for ourselves with our strict quality control measures and advanced QA test facilities. We will make sure that you the Die Cast Gears quality remain constant.
10+ years of experience
Sunrise has more than 10 years of experience in this field. Our experienced employees and engineers make use of their expertise in the field and we can make helpful suggestions for your Die Cast Gears.
Superior R&D Facilities
We have superior research and development facilities dedicated to making our services even better. The researchers at the R&D are working tirelessly to keep our facilities updated with the latest technology.