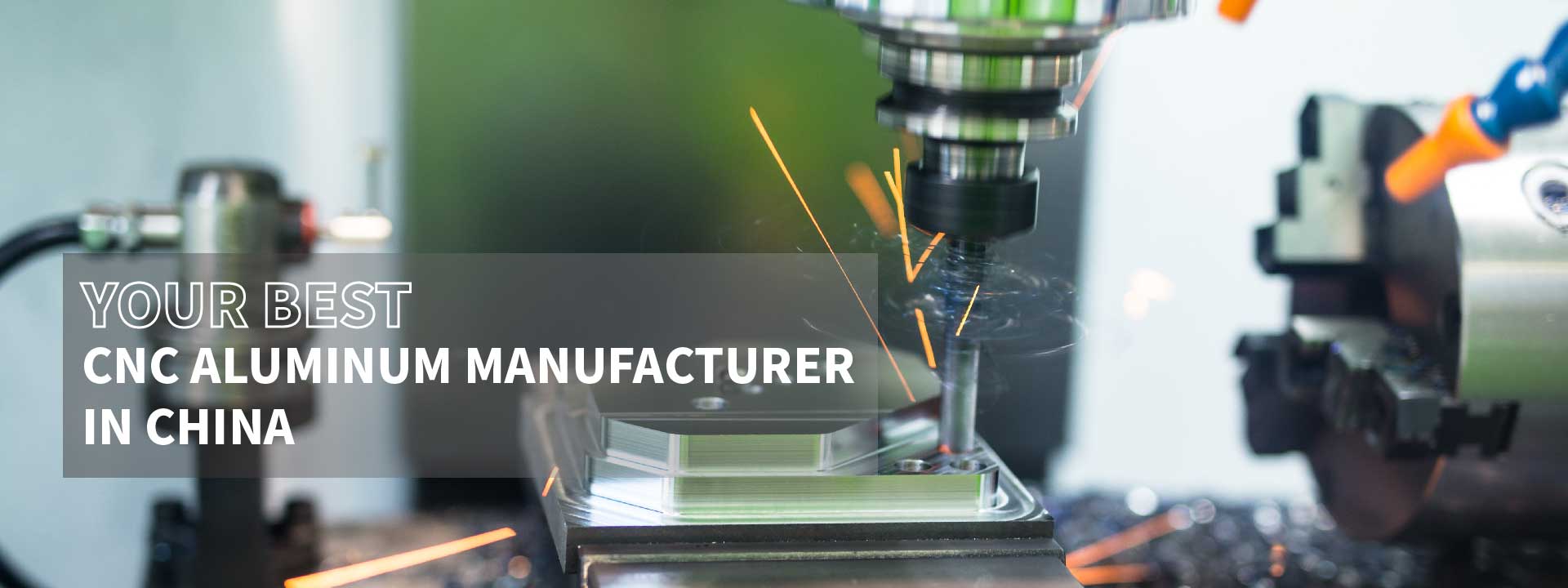
CNC ALUMINUM MANUFACTURER IN CHINA- SUNRISE METAL - Your Best Supplier
Sunrise Metal is the one top of the line Aluminum CNC facility that specialized in CNC Aluminum parts production. With over 23+ years’ experience in the CNC Aluminum field, we created the ideal CNC Aluminum parts. We resolve to offer you the high-caliber and exceptionally brilliant CNC Aluminum parts at a competitive budget.
- Produce top-grade and cost-effective Aluminum CNC parts
- Experience, accuracy, and powerful machinery
- Design and produce complex custom Aluminum parts
- Simultaneously realized various and large quantities of production
- Provides the clients with high-quality CNC Aluminum parts in a comparable timeline
- Timely shipment, one-stop instant service
YOUR PRECISE CNC ALUMINUM PARTS COMING FROM SUNRISE HIGH-LEVEL MACHINING EQUIPMENT
HELPING YOUR PROJECTS GREAT SUCCESS WITH SUNRISE STRINGENT QUALITY CAPABILITY
Sunrise Metal invested many Modern measuring instruments, such as Carl Zeiss CMM, X-ray Detector, and Spectrometer and Cleanliness testing Lab, etc. To assure you of good quality with your parts, we will continually invest in Inspection instruments and training on our employees.
Quality is the top priority of our work. To achieve our promise on quality to our customers, we introduced the third parties to help improve our quality control Management system. We have built a very effective QC management system under the instruction of ISO, we are ISO9001, and IATF 16949 certified CNC machining manufacturer.
With our high-level measurement lab, We execute strict inspections to our aluminum die casting parts, from raw material to out-going parts. Sunrise Metal guarantees all parts are up to your requirements.
10000+ CNC ALUMINUM PARTS MANUFACTURING EXPERIENCE FROM 500+GLOBAL CLIENTS
CNC ALUMINUM PARTS WITH SURFACE FINISHING
Sunrise Metal tries all our effort to offer a 1-stop solution service to your CNC aluminum parts.
Wide range of material: Al6061, Al6063, Al5052, Stainless Steel, Copper, and many kinds of plastic, etc.
Second surface finishing source: Anodizing, Chromate, Powder coating, wet painting, E-coating, Chrome Plating, nickel plating, Silk printing, etc.
All our parts are meet ROHS and REACH requirements.
- Advanced CNC Machining Equipment
- Premium Quality Measuring Instruments
No. | Name | Stroke | Q’ty |
1 | Mazak 7-axis turning&milling Machine | Ø658*1011MM | 1 |
2 | Mazak /Hass 5axis CNC machine | Ø850/Ø600 | 4 |
3 | 3-axis CNC machine center | 2000*1500MM | 1 |
4 | 4-axis CNC machine center | Ø250*800MM | 8 |
5 | 3-axis CNC machine center | 1000*600*600MM | 20 |
6 | CNC Lathes | Ø320*800/Ø610*1000MM | 2 |
7 | Sodick Wire cutting Machine | 400*400*200MM | 3 |
8 | EDM machine | 500*400*400MM | 2 |
9 | Surface grinder | 600*300*200MM | 1 |
No. | Name | Brand | Q’ty |
1 | CMM | Carl Zessis | 1 |
2 | CMM | SanYou | 1 |
3 | Spectrometer | China | 1 |
4 | Microscope | China | 1 |
5 | Projector | China | 2 |
6 | X-ray Detector | SANDT | 1 |
7 | Cleanliness Test Equipment | China | 1 |
8 | Leakage Test Equipment | China | 2 |
9 | Salt Spray Testing Equipment | China | 1 |
10 | Pneumatic Measuring Instrument | China | 2 |
11 | Hardness Testing Machine | China | 1 |
12 | Color Meter Machine | China | 1 |
13 | Thickness Testing Machine | China | 1 |
14 | Electronic Balance | China | 1 |
15 | Density Balance | China | 1 |
GET A FREE CONSULTATION
If you have any hesitation or any design doubt on your CNC aluminum, Sunrise Metal would like to be your free consulter. Sunrise Metal gives suggestions on your CNC aluminum parts at 3 aspects:
1. Your design evaluation.
2. Feasibility analysis for mass production.
3. Project time and part’s cost-saving.
Contact us now, to see how we can help you with your Aluminum Die Casting projects.
CNC ALUMINUM:
THE COMPLETE GUIDE
Sunrise Metal‘s CNC aluminum service is endeavoring to give you capable strategy and conventional quality with an expert team who break down your undertaking cautiously, make sense of the best answer for you, and procedure your custom machined parts most efficiently to save your time and cost. Furthermore, you can find out the answers if you have any questions about CNC ALUMINUM from this complete FAQ guide.
- What is CNC Aluminum?
- What is the CNC Aluminum Parts?
- What are the benefits of CNC Aluminum?
- What is the Resistance to Corrosion of CNC Aluminum?
- What is the Electrical Conductivity of CNC Aluminum?
- What is the Anodization Potential of CNC Aluminum?
- What is the CNC Milling Aluminum?
- How to combine CNC Aluminum with Aluminum Extrusion?
- How to combine CNC Aluminum with Aluminum Die Casting?
- What is the selection process of choosing the right material for CNC Aluminum?
- What are the best Aluminum alloys for machining & series classifications?
- Why choose Aluminum material for CNC Machining?
What is CNC Aluminum?
A CNC (Computer Numerical Control) machine operates through a computer-aided software; it can either be for parts design prototyping or a complete parts production. Aluminum is the most preferred metal for CNC machining, as it holds excellent machinability, and is the favored and best-quality metal in the majority of manufacturing areas.
Aluminum offers some excellent thermal, physical, and mechanical properties. Besides, the aluminum metal is generally simple to shape, particularly in drilling processes, as in CNC aluminum machining. Additionally, we respect aluminum alloys compared with other lightweight metals, for example, magnesium and titanium alloys.
The use of Aluminum alloys in CNC machining is spread massively; the production of CNC Aluminum automotive parts and other CNC parts has been extreme and preferred.
Its high machinability describes Aluminum. The cutting forces that are applied to Aluminum are impressively lower than steel or metal, for example. The mechanical heap of the tools, workpiece, and the machines is as needs be stunningly lower; the vitality consumed per unit volume of the workpiece is moreover correspondingly lower.
The low explicit weight of Aluminum is another reason for its CNC preference; it likewise impressively reduces centrifugal forces (inertial forces), particularly in turning workpieces.
Sunrise Metal has been working with Aluminum for over 23+ years. We can utilize our item know-how in our machining focuses and pick the real material parts and machining forms customized to the material.
What is the CNC Aluminum Parts?
The technology of CNC machined Aluminum has produced CNC parts and components that guide in a vast majority of services (Turning, milling, and grinding). Furthermore, well-machined CNC aluminum prototypes and parts are becoming popular in the engineering division.
Aluminum machined parts are regularly produced based and depend on the Aluminum alloy type. Aluminum alloys are high in quality, best in strength, and low in material-density. However, the aluminum CNC parts have the immense tolerance to control even “0.01MM”. The CNC machine can make remarkable and quality aluminum components and parts.
Coming up next are some of the Aluminum CNC parts:
- Spline Shafts
- Front Panels
- Dowels Pins
- EMI-Housings
- Lighting Fixtures
- Medical Devices
What are the benefits of CNC Aluminum?
For CNC machining, Aluminum is one of the essential material decisions because of its exceptional physical and mechanical properties. It is robust and accessible, which makes it an ideal decision for mechanical parts.
Furthermore, its oxidized outer layer is resistant to corrosion from the sections and parts. These advantages have made aluminum parts standard for a vast majority of ventures;
However, they are commonly preferred in the auto, aviation, healthcare, and electronic system industries. Aluminum additionally offers specific points that rearrange, upgrade, and improve the procedure of CNC machining.
Rather than different metals with comparable material properties; Aluminum offers exceptional machinability: a unique number of its appraisals can be viably entered by cutting tools, chipping enough while being anything but difficult to shape.
Along these lines, Aluminum can be machined multiple occasions quicker than iron or steel. This answer clarifies a portion of the critical benefits of CNC Aluminum — reasons why it is one of our most broadly mentioned Aluminum CNC prototyping and production processes.
Following are some unique benefits of Aluminum CNC:
- Short CNC Aluminum Parts production period
- Enhanced Economic process
- Quality over quantity preference (Volume goes up, and the price goes down)
- Accuracy of Aluminum CNC Machining can be controlled
- Moderate level of intricacy
- Nominal to high tolerances
- Wide range of sizes can be machined
What is the Resistance to Corrosion of CNC Aluminum?
One of the fundamental reasons why engineers prefer Aluminum over other metals for their machined parts is because the material is anything but complicated to the machine and their resistance to corrosion.
While this would appear to be more of a higher degree advantage for the engineers manufacturing the parts, it likewise has unique advantages for the business requesting the part, just as the end-user that will, in the long run, use it.
Different aluminum grades contrast fundamentally in their resistance to corrosion — the amount they can withstand oxidization and chemical harm. Fortunately, the majority of high-grade alloys for CNC machining are the most resistant.
Aluminum Alloy 6061, for example, offers superb corrosion resistance, as do diverse combinations on the lower end of the quality range. Strong aluminum combinations may be less resistant to corrosion as a result of the closeness of alloyed copper.
What is the Electrical Conductivity of CNC Aluminum?
Aluminum has exceptional physical properties that make it a perfect decision for both mechanical and perspective CNC machined parts. Two of the most supreme are Aluminum’s high-level of solidarity and high electrical conductivity.
Furthermore, the two of which make the Aluminum reasonable for fundamental parts, for instance, those required in aviation and auto industries.
Although not as conductive as certain other potential materials, Aluminum (pure-form) has an electrical conductivity of approximately 37.65 million siemens per meter at standard room temperature.
Alloys may have lower conductivities, yet aluminum materials are on a fundamental level more conductive than, for example, treated steel.
What is the Anodization Potential of CNC Aluminum?
CNC aluminum parts are incredibly famous in the majority of hardware industries, not because of the quality and weight advantages they offer but, because they also fulfill the certain core requirements, since the significant crucial considerations as well.
Also, Aluminum is highly responsive to surface finishes; it can be treated through anodization, a surface finishing method that helps thickens the oxidized external layer, and a defensive layer of the aluminum CNC parts.
The anodization method, which took place after the CNC machining is done, includes the flow of electric current through the CNC aluminum part in an electrolytic acid bath and results in a piece of Aluminum that is more corrosion-resistant and protective against any physical and environmental effect.
Colors can discover their way through the permeable areas of the outer layer and are less inclined to chip or drop since they are implanted inside the great outside of the metal part.
What is the CNC Milling Aluminum?
At the point when the milling cutter is applied to the parts, the cutting is adequate. A while later, it prompts cutting heat and deformation.
The perfect strategy for avoiding this issue is pre-drilling with more marvelous tools than just the milling cutter and a while later put the mill and milling cutter.
The enormous impact on the cutting limit is the amount of cutting profundity (or back depth). To keep up efficiency and diminish the quantity of cutting.
Furthermore, A CNC milling can settle the issue by speeding up the machine and diminishing the cutting power.
How to combine CNC Aluminum with Aluminum Extrusion?
Aluminum remains the top-rated and quality metal choice for ventures and engineers from years; there are ways to join CNC machining with other assembling procedures/processes to make more complex, quality, and higher-performing aluminum parts.
Doing so can maximize the usefulness of Aluminum while receiving the rewards of various creative forms. For being a multi-purpose manufacturing process, CNC aluminum also used to refine or upgrade aluminum parts made with the help of other hardware or machining techniques.
Extrusion and die casting methods can each be enhanced with the CNC machining technology to improve and enhance the quality of aluminum parts. Expulsion is a unique way of forcing molten material (mostly Aluminum) through an opening in a die, delivering an extended portion with a consistent profile.
While aluminum expulsion is a ground-breaking strategy for making practical & functional fragments with quality surface completions and complex cross-segments, it is limited in scope, since those cross-areas must be predictable over the part.
However, except if the part is adjusted after extrusion. Since aluminum extrusion will, in general, include flexible, bendable, and machinable Aluminum grades like 6061 and 6063, the extruded parts would then be able to be post-machined — cut in different manners utilizing a CNC machining focus.
Combining the aluminum extrusion and aluminum CNC is an incredible method to create reliable and quality aluminum parts with complex cross-segments and sporadic geometries through the CNC machined for Aluminum extrusions.
How to combine CNC Aluminum with Aluminum Die Casting?
Aluminum Die Casting methods are the aluminum parts manufacturing procedure in which liquid metal is forced into a mold cavity with high pressure or press.
It is commonly used when making parts in more massive amounts since the necessary tool steel dies are costly to manufacture. Alongside steel, magnesium, and zinc, Aluminum is one of the most notable, well-known, and preferred metal for die-casting.
Furthermore, die-cast aluminum parts usually have an exceptional surface finish and dimensional consistency. These crucial benefits can be achieved together with the advantages of CNC machining.
By die-casting aluminum parts at that point, including further cuts utilizing a machining center, it is conceivable to manufacture parts with a remarkable finish and more complex geometries than would be possible utilizing either process all alone.
What is the selection process of choosing the right material for CNC Aluminum?
CNC machining is one of the most well-known techniques used to fabricate parts and items. The Computer Numerical Controls (CNC) usage allows aluminum parts to be manufactured using a profoundly automated procedure, which has the high ground on numerous traditional manufacturing methods in terms of speed, production rate, and precision. Furthermore, deciding the correct material for the procedure can be an overwhelming task.
Various factors need to be considered when choosing the most appropriate material for your parts, including functionality, value, resistance to corrosion, quality, weight, and corrective appearance.
Here are the necessary (or core) steps of the material selection process for Aluminum CNC :
Step 1: Define the material requirements: These requirements are considered essential and include mechanical, thermal, or other material requirements, as well as Aluminum CNC costs, quality, and surface finishes.
Furthermore, our primary focus is on the condition that the parts can be used in and the components it communicates and intact with, and that’s what defines the material requirements.
Step 2: Identify the CNC materials: Shortlist a few most suitable candidates’ materials that fulfill all (or the most required) requirements of your CNC Aluminum part design.
Step 3: Select the most appropriate material: A compromise is usually required here between at least two of the design requirements (for instance, mechanical execution and cost).
What are the best Aluminum alloys for machining & series classifications?
Aluminum alloys have an exceptional strength-to-weight ratio, a high electrical and thermal conductivity, and resistance to corrosion. They can be expertly machined and have a low mass expense, so they are regularly the most affordable choice of making custom CNC machined aluminum parts and prototypes.
Furthermore, the CNC Aluminum blocks can be anodized, making a hard, defensive layer on their surface.
- Aluminum 6061 is considered as the most common block of aluminum for CNC. It’s a general CNC aluminum alloy, with good strength-to-weight ratio and excellent machinability.
- Aluminum 6082 alloy has a similar composition and material properties to Aluminum 6061. Furthermore, it is more commonly used in Europe, as it is compliant with British Standards.
- Aluminum 7075 alloy is the most commonly used in aviation applications where lightweight is a critical requirement, as it has excellent fatigue properties and can be heat treated to high strength and hardness, comparable to steels.
- Aluminum 5052 alloy is considered as the most common block of aluminum for CNC. It’s an exceptional CNC aluminum alloy, with good strength-to-weight ratio and fine machinability. This alloys also has higher strength than most other aluminum alloys.
Why choose Aluminum material for CNC Machining?
Aluminum is incredibly regular in CNC milling Aluminum processes because of its functionality and flexibility. Furthermore, it contains a subtle amount of strength-to-weight ratio.
Aluminum is what they used to make airplanes of (until carbon fiber tagged along). Aluminum is a lot stiffer than plastic. Working with Aluminum has its difficulties; however, makes way for reliable, innovative parts coming right off your Aluminum CNC machine.
Aluminum is the third most regular component in the Earth’s crust after oxygen and silicon. This metal is exceptional for its low density and capacity to resist corrosion. It is significant in the aerospace, transportation, electrical, and building industries.
It is additionally used to make a variety of industrial parts. Aluminum is quite often alloyed to improve its mechanical properties. About 25% of Aluminum is die-cast, and the rest is created or alloy aluminum.
As a fact, lighter and stiffer designs can be accomplished with Aluminum than steel. Aluminum’s capacity to conduct heat and electricity well is regularly valuable. Aluminum has remarkable corrosion resistance, and Aluminum is entirely recyclable.
Possibly the most used CNC milling material, Aluminum, is a sound decision for mechanical parts. Moreover, contrasted with various metals, Aluminum is usually fit to be machined rapidly than others, making it the most monetarily achievable of the pack.
Aluminum CNC parts manufacturing structure a protective layer when exposed to nature (environment), which prompts new quality, strength, and resistance to corrosion.
Given these first-rate metal qualities, CNC Aluminum is ideal for use in the auto, aviation, and medical industry.